Efficiently rotating or tilting heavy loads is a fundamental challenge in numerous manufacturing, warehousing, and distribution operations. Safely and precisely changing the orientation of items like coils, barrels, pallets, or large components is crucial for various process steps, including assembly, machining, inspection, packaging, and pallet exchange. Industrial upenders and tilters are specialized material handling equipment designed specifically for these tasks, significantly enhancing both productivity and workplace safety. The videos above demonstrate two common types: a 90-degree tilter often used for barrels or pallet loads, and a 360-degree inverter capable of full load rotation.
1. Understanding Upenders and Tilters: Core Functionality and Types
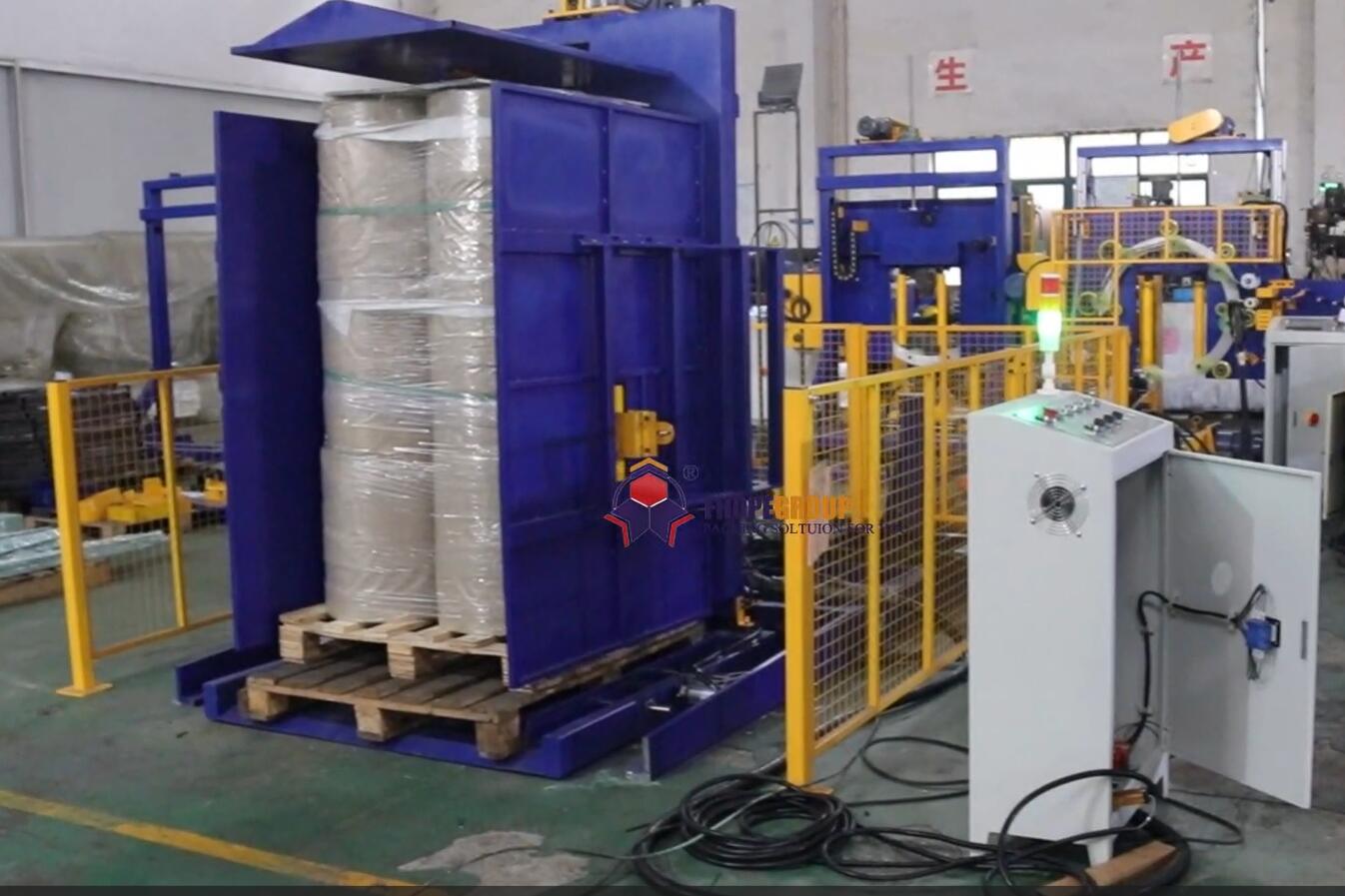
Upenders, tilters, and inverters are robust machines engineered to reorient loads around a horizontal axis. While often used interchangeably, subtle differences exist:
- Tilters: Typically rotate loads up to 90 degrees, sometimes 120 degrees. Ideal for tasks like tilting bins for parts access or positioning components for ergonomic assembly.
- Upenders/Downenders: Specifically designed to tilt loads (like steel coils or paper rolls) between horizontal and vertical orientations (90 degrees).
- Inverters: Capable of rotating loads 180 degrees or even a full 360 degrees. Commonly used for pallet exchange (replacing a broken pallet or switching to an in-house pallet), load squaring, or inverting products for processing on the opposite side.
The choice between these depends entirely on the application's required range of motion and the nature of the load.
2. Key Design and Structural Components
Understanding the construction of these machines is vital for selection and maintenance:
- Base Frame: Provides a stable foundation, typically constructed from heavy-gauge structural steel (e.g., ASTM A36) to withstand significant loads and operational forces. Must be anchored securely to the floor.
- Load Platform(s): The surface(s) that support the load. Can be flat steel plates, roller conveyors, V-saddles (for cylindrical loads like coils), or custom fixtures. Often includes adjustable clamping mechanisms (hydraulic or manual) to secure the load during rotation. Platform dimensions (e.g., 48"x48", 60"x60") must match load sizes.
- Drive System: The powerhouse for rotation. Common types include:
- Hydraulic: Utilizes hydraulic cylinders powered by an electro-hydraulic power unit (HPU). Offers high force density, smooth motion control, and durability. Typically involves pressures ranging from 1500 to 3000 PSI.
- Electro-Mechanical: Employs electric motors coupled with gear reducers (worm gear or planetary gear) and often heavy-duty chains or direct drives. Offers precise positioning and can be suitable for cleaner environments. Motor power typically ranges from 1 HP to 10 HP depending on capacity and speed.
- Control System: Manages operation. Can range from simple push-button pendants for manual control to sophisticated PLC (Programmable Logic Controller) systems integrated with sensors (proximity, limit switches, photo-eyes) for automated sequencing and integration into production lines. Variable Frequency Drives (VFDs) may be used for soft start/stop and speed control.
- Safety Features: Critical for protecting personnel and equipment. Standard features include:
- Velocity fuses on hydraulic cylinders to prevent uncontrolled descent in case of hose failure.
- Emergency stop buttons.
- Physical guarding or safety fencing around the operational area.
- Optional light curtains or safety scanners to detect intrusion into the work zone.
- Mechanical locking pins for maintenance.
3. Technical Specifications: A Comparative Overview

Selecting the right equipment requires careful consideration of technical parameters. Below is a representative comparison; actual specifications vary widely by manufacturer and model:
Feature | Light-Duty Tilter (90°) | Heavy-Duty Upender (90°) | Pallet Inverter (180°) | Heavy-Duty Rotator (360°) |
---|---|---|---|---|
Capacity (lbs) | 1,000 - 4,000 | 5,000 - 50,000+ | 2,000 - 6,000 | 10,000 - 100,000+ |
Capacity (kg) | 450 - 1,800 | 2,250 - 22,500+ | 900 - 2,700 | 4,500 - 45,000+ |
Tilt Angle (°) | 90 | 90 | 180 | 360 |
Platform Size (in) | 36x36 to 48x48 | 48x48 to 84x84+ (Coil) | 48x48 to 60x60 | Custom based on load |
Platform Size (mm) | 914x914 to 1219x1219 | 1219x1219 to 2134x2134+ | 1219x1219 to 1524x1524 | Custom based on load |
Typical Cycle Time (s) | 20 - 40 | 30 - 90 | 45 - 75 | 60 - 180+ |
Power Source | Hydraulic / Electric | Hydraulic / Electric | Hydraulic / Electric | Hydraulic / Electric |
Control Type | Push-button / PLC | Push-button / PLC | Push-button / PLC | PLC / Automated |
Primary Use | Parts bins, Ergonomics | Coils, Rolls, Molds | Pallet Exchange | Large Components, Molds |
Note: These are general ranges. Always consult manufacturer specifications for specific models.
4. Operational Benefits: Enhancing Efficiency and Safety
Integrating industrial tilters and upenders yields significant advantages:
- Improved Ergonomics & Safety: Dramatically reduces manual lifting, pushing, and pulling of heavy or awkward loads, minimizing risks of musculoskeletal disorders (MSDs) and complying with ergonomic guidelines (e.g., [OSHA guidelines on material handling]). Secure clamping prevents load slippage, reducing accident potential.
- Increased Productivity: Automating the tilting/rotating process is significantly faster and more consistent than manual methods or using general-purpose equipment like forklifts with attachments. Reduced cycle times directly translate to higher throughput.
- Reduced Product Damage: Gentle, controlled motion and secure clamping minimize the risk of dropping or damaging valuable products or components during orientation changes.
- Optimized Workflow: Allows loads to be presented at the ideal orientation for subsequent processes (machining, assembly, inspection, packaging), streamlining the overall production flow.
- Labor Savings: Reduces the number of personnel required for handling operations and minimizes worker fatigue.
5. Practical Applications Across Industries
The versatility of upenders and tilters makes them indispensable in various sectors:
- Metal Processing & Fabrication: Tilting heavy steel coils (up to 50 tons or more) from eye-to-sky (vertical) to eye-to-horizon (horizontal) for decoiling lines or storage. Rotating large fabrications or molds for welding or finishing access.
- Logistics & Warehousing: 180-degree pallet inverters are essential for transferring goods from wooden shipping pallets to plastic hygienic pallets, replacing damaged pallets without manual restacking, or recovering damaged goods at the bottom of a stack.
- Automotive Manufacturing: Positioning engine blocks, transmissions, or vehicle chassis components for assembly or robotic operations.
- Paper & Printing: Upending large paper rolls for feeding into printing presses or converting machinery.
- Chemical & Pharmaceutical: Tilting drums or Intermediate Bulk Containers (IBCs) for controlled dispensing or mixing.
- Food & Beverage: Inverting pallet loads for layer picking or transferring loads to sanitized pallets.
6. Personal Usage Experience & Selection Considerations
From an operational standpoint, using these machines effectively involves several factors:
- Load Assessment is Key: Before selecting a machine, thoroughly analyze the load: maximum weight, dimensions (L x W x H), center of gravity, stability, and any specific handling requirements (e.g., fragile surfaces). This dictates capacity, platform size, and clamping needs.
- Cycle Time vs. Control: Faster isn't always better. Consider the need for smooth acceleration/deceleration (using VFDs or proportional hydraulic valves) to prevent load shifting, especially with unstable or liquid loads.
- Operating Environment: Factor in space constraints (footprint), floor capacity, power availability (voltage/phase), and environmental conditions (dust, moisture, hazardous locations requiring explosion-proof components).
- Level of Automation: Decide between manual push-button control, semi-automatic cycles, or fully automated integration with conveyors, AGVs, or robotic cells.
- Maintenance Access: Ensure the design allows for safe and easy access to drive components, lubrication points, and electrical panels for preventative maintenance. Regular inspection of hydraulic hoses, chains, and structural welds is crucial.
- Operator Training: Proper training on safe operating procedures, load securing techniques, and emergency protocols is non-negotiable.
7. Integrating Tilters into Automated Workflows
Modern facilities increasingly integrate upenders and tilters into larger automated systems. This can involve:
- Conveyor Integration: Machines designed with through-conveyor platforms (roller or chain) allow seamless flow of loads into and out of the tilting station.
- PLC Handshaking: Interfacing the tilter's PLC with the main line control system ensures synchronized operation, preventing collisions and optimizing flow.
- Robotic Loading/Unloading: Robots can be used to place components onto the tilter or remove them after reorientation, enabling fully unmanned operations.
- Sensor Feedback: Sensors confirm load presence, correct positioning, and completion of the tilt cycle before signaling downstream equipment.
Conclusion
Industrial upenders, tilters, and inverters are far more than simple conveniences; they are essential tools for safe, efficient, and damage-free material handling in demanding environments. By carefully evaluating load characteristics, operational needs, and available technologies, facilities can implement the right rotating or tilting solution to significantly boost productivity, enhance worker safety, and protect valuable assets. Understanding the design, specifications, and application nuances allows for informed selection and optimal utilization of this critical equipment category.