Optimizing Coil and Mold Handling: A Technical Look at Upenders and Tilters
Handling heavy, bulky items like industrial coils and large molds presents significant challenges in manufacturing and fabrication environments. Improper handling can lead to safety hazards, product damage, and operational inefficiencies. Upenders and tilters are specialized material handling equipment designed specifically to address these challenges by safely and efficiently rotating or tilting heavy loads.
1. Understanding Upenders and Tilters
At their core, upenders (often called coil positioners or up-enders) are machines designed to rotate a load, typically 90 degrees, to change its orientation from horizontal to vertical (eye-to-sky) or vice versa. Tilters, while sometimes used interchangeably, often refer to equipment that can tilt a load to a specific angle, which might be 90 degrees but could also be other angles required for maintenance, inspection, or processing. Both serve the crucial function of repositioning heavy objects that are difficult or dangerous to manipulate manually or with conventional lifting equipment like forklifts or cranes alone.
Watch a typical upender/tilter in operation handling a coil.
2. Key Applications in Industry
The utility of upenders and tilters spans across various industrial sectors:
- Metal Coil Processing: In steel mills, service centers, and stamping plants, coils are often shipped and stored horizontally (eye-to-the-wall) but need to be oriented vertically (eye-to-sky) for feeding into slitting lines, presses, or other processing equipment. Upenders facilitate this transition smoothly and safely.
- Mold and Die Handling: Large injection molds, casting dies, and stamping dies require regular maintenance, cleaning, inspection, and setup. Tilters allow maintenance crews safe access to different sides of the mold or die by tilting it to a required angle, often 90 degrees, eliminating the risks associated with trying to manually prop or turn these heavy components.
- Roll Handling: Similar to coils, large rolls of paper, plastic film, or textiles may need reorientation for storage, shipping, or processing.
- Engine/Transmission Assembly: In automotive or heavy equipment manufacturing, tilters can be used to position large components for easier access during assembly or maintenance.
upender23 3. Essential Technical Specifications and Design Features
When evaluating or specifying an upender or tilter, several technical parameters are critical:
- Load Capacity: Ranging from a few hundred kilograms to over 50 tons, matching the machine's capacity to the maximum weight of the load is paramount.
- Platform Size and Configuration: The dimensions of the loading platform must accommodate the size of the coil, mold, or other workpiece. Platforms can be flat, feature a V-saddle to cradle coils, or include adjustable clamps or fixtures.
- Rotation/Tilt Angle: Typically 90 degrees for standard upenders. Tilters may offer variable angles or specific fixed angles based on application needs.
- Drive Mechanism:
- Electro-mechanical: Utilizes electric motors, gearboxes, and often screw jacks or chain drives. Generally provides precise control and requires less maintenance related to fluid leaks.
- Hydraulic: Employs hydraulic cylinders powered by a hydraulic power unit (HPU). Known for high power density, making them suitable for very heavy loads, but require routine checks for leaks and fluid levels.
- Control System: Options range from simple pendant controls (handheld push-button controllers) to programmable logic controllers (PLCs) for automated sequences or integration into larger manufacturing systems. Remote control options are also common for enhanced operator safety and visibility.
- Cycle Time: The time required to complete a full tilt or rotation cycle, impacting overall throughput.
- Safety Features: Essential elements include:
- Limit switches to control the extent of rotation/tilt.
- Safety barriers or light curtains to prevent personnel entry during operation.
- Emergency stop buttons.
- Mechanical locking mechanisms or velocity fuses (for hydraulic systems) to prevent uncontrolled movement in case of power or component failure.
- Audible alarms and visual beacons during operation.
4. Operational Benefits and Experience Sharing
Integrating the right upender or tilter yields tangible advantages:
- Enhanced Safety: Significantly reduces the risks associated with manual handling or less stable lifting methods, minimizing potential crush injuries or load drops.
- Improved Efficiency: Automating the reorientation process is much faster than manual methods, reducing downtime between processes or during loading/unloading.
- Product Protection: Smooth, controlled movement prevents damage to sensitive coils (e.g., edge damage) or expensive molds and dies.
- Ergonomic Improvement: Reduces physical strain on workers tasked with handling heavy items.
- Process Integration: Can be integrated with conveyors, automated guided vehicles (AGVs), or overhead crane systems for seamless material flow.
Experience shows that selecting a machine slightly above the maximum anticipated load capacity provides a safety margin and can extend equipment life. Furthermore, considering the specific shape and fragility of the load (e.g., requiring special platform padding for pre-painted coils) is crucial during specification.
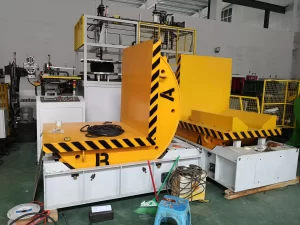
5. Selecting the Right Equipment
Choosing the appropriate upender or tilter involves considering:
- The type, weight, and dimensions of the load(s).
- The required orientation change (90°, 180°, specific angle).
- Frequency of use (duty cycle).
- Available power source (electrical, hydraulic).
- Operating environment (indoor/outdoor, hazardous area).
- Level of automation required.
- Safety requirements and plant standards.
A thorough analysis of these factors ensures the selected equipment meets the application's demands effectively and safely. For specific examples of coil upender configurations, see further details here:
https://www.fhopepack.com/Coil_upender.html
6. Maintenance Considerations
Like any industrial machinery, upenders and tilters require regular maintenance for safe and reliable operation. This typically includes:
- Lubrication of moving parts (gears, bearings, chains).
- Inspection of structural components for wear or fatigue.
- Checking hydraulic fluid levels and inspecting hoses/fittings for leaks (if applicable).
- Testing safety features (limit switches, E-stops).
- Verifying electrical connections and controls.
Adhering to the manufacturer's recommended maintenance schedule is vital.
Conclusion
Upenders and tilters are indispensable tools in modern manufacturing and material handling, providing a safe, efficient, and controlled method for reorienting heavy coils, molds, dies, and other large workpieces. By understanding their technical specifications, applications, and operational benefits, facilities can effectively leverage this equipment to enhance safety, protect valuable assets, and streamline production processes. Careful selection based on specific operational needs and diligent maintenance ensures long-term reliability and performance.
For further information or specific inquiries:
info@fhopepack.com