Optimizing Coil Packaging: A Guide to Semi-Automatic Wrapping Machines with Automatic Cutters
Efficiently packaging coils – whether steel, wire, cable, or hose – is crucial for protection during storage and transit. While manual wrapping is labor-intensive and fully automated systems require significant investment, semi-automatic coil wrapping machines offer a balanced solution. This guide explores the functionality, benefits, and key considerations of semi-automatic coil wrappers equipped with automatic film cutting systems.
1. Understanding the Semi-Automatic Coil Wrapping Process
Semi-automatic coil wrappers streamline the packaging process through an orbital wrapping mechanism. Here’s a breakdown of how they typically operate:
- Loading: An operator places the coil onto the machine's loading area, often equipped with support rollers or a turntable.
- Initiation: The operator secures the leading edge of the stretch film to the coil and initiates the wrapping cycle via the control panel.
- Wrapping: A wrapping ring or arm, holding the film roll carriage, rotates orbitally through the eye of the coil. Simultaneously, powered rollers may rotate the coil itself. This coordinated motion ensures stretch film is applied evenly around the coil's circumference and through its center, providing complete coverage.
- Cutting: Upon cycle completion (preset number of wraps), the integrated automatic cutter cleanly severs the stretch film.
- Unloading: The operator removes the securely wrapped coil.
The "semi-automatic" nature means an operator handles loading, unloading, and cycle initiation, while the machine performs the repetitive and physically demanding wrapping and cutting actions.
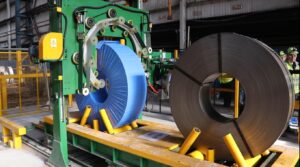
2. The Critical Role of the Automatic Cutter
The automatic cutter is a key feature distinguishing these machines from more basic models. Its primary functions and benefits include:
- Consistency: Ensures the film is cut at the same point and in the same manner every cycle, contributing to package integrity.
- Speed: Eliminates the need for the operator to manually cut the film, reducing overall cycle time and increasing throughput.
- Safety: Minimizes operator interaction with moving parts and cutting tools during the critical film-severing step.
- Film Economy: Often designed to leave a minimal, neat film tail, potentially reducing film waste compared to manual cutting.
- Operational Efficiency: Frees the operator to prepare the next coil while the current one finishes wrapping and cutting.
Cutter mechanisms can vary, commonly employing methods like heated wires or mechanical blades.
3. Key Technical Specifications and Parameters
When evaluating semi-automatic coil wrappers with auto-cutters, consider these typical specifications:
- Coil Dimensions:
- Inner Diameter (ID): Minimum and maximum capability (e.g., 300mm - 800mm)
- Outer Diameter (OD): Minimum and maximum capability (e.g., 500mm - 1500mm)
- Width/Height: Range the machine can accommodate (e.g., 100mm - 600mm)
- Maximum Weight: Coil weight capacity (e.g., up to 2000 kg)
- Performance:
- Wrapping Ring Speed: Rotational speed (e.g., 40-90 RPM, adjustable)
- Roller Speed: Coil rotation speed (e.g., 2-4 m/min, adjustable)
- Cycle Time: Varies based on coil size and wraps, but typically much faster than manual wrapping.
- Film Delivery System:
- Film Type: Usually LLDPE Stretch Film
- Film Roll Width: Standard compatible widths (e.g., 76mm, 125mm)
- Film Roll OD/ID: Specifies roll dimensions
- Film Tension Control: Mechanical or powered pre-stretch options for optimal film usage and load containment.
- Utilities:
- Power Supply: Voltage, phase, frequency (e.g., 480V, 3Ph, 60Hz)
- Compressed Air: Pressure and consumption (if required for certain functions)
- Control System:
- PLC (Programmable Logic Controller) based controls.
- HMI (Human Machine Interface) for parameter adjustments (wrap counts, overlap, tension) and diagnostics.
- Program storage for different coil recipes.
(Note: Specific values vary significantly between models and manufacturers. Always refer to specific machine documentation.)
4. Advantages Compared to Other Methods
Semi-automatic wrappers with cutters occupy a strategic middle ground:
- Versus Manual Wrapping:
- Speed & Throughput: Significantly faster, increasing packaging line output.
- Consistency: Uniform wrap tension and overlap ensure consistent package quality and load security.
- Ergonomics: Reduces physical strain and repetitive motion injuries for operators.
- Film Savings: Controlled tension and overlap often lead to more efficient film usage.
- Versus Fully Automatic Wrapping:
- Lower Initial Cost: More accessible capital investment compared to fully integrated systems.
- Simplicity: Often involves less complex mechanics and controls, potentially simplifying maintenance and troubleshooting.
- Flexibility: Can be easier to adapt to varying coil sizes or less frequent production runs without extensive reprogramming or conveyor integration.
The primary trade-off compared to fully automatic systems is the continued need for operator involvement in loading and unloading.
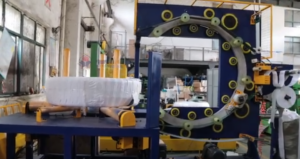
5. Application Considerations and Best Practices
Successfully implementing a semi-automatic coil wrapper involves careful planning:
- Industry Suitability: Widely used in industries producing or handling steel coils, aluminum coils, copper wire, electrical cable, plastic tubing, hoses, and other coiled products.
- Film Selection: Choose a stretch film with appropriate thickness (gauge), pre-stretch capability, and puncture resistance based on the coil's weight, shape, and handling requirements.
- Loading/Unloading: Ensure safe and efficient procedures are in place, potentially involving cranes, forklifts, or coil cars, depending on coil weight.
- Parameter Optimization: Experiment with wrap counts, film overlap percentages, and tension settings to achieve optimal load containment with minimal film consumption for each specific coil type.
- Workflow Integration: Position the wrapper logically within the production or warehousing workflow to minimize handling distances. Consider placing it near coil slitters, extruders, or storage areas.
6. Maintenance and Safety Protocols
Regular maintenance and adherence to safety procedures are vital for longevity and safe operation:
- Routine Checks: Regularly inspect film rollers, cutter mechanism (sharpness, heating element function), drive belts/chains, and safety sensors.
- Lubrication: Follow the manufacturer's recommended lubrication schedule for bearings, chains, and rotating components.
- Cleaning: Keep the machine free of film fragments, dust, and debris.
- Safety Features: Ensure emergency stops, safety guards, and interlocks are functional and never bypassed.
- Operator Training: Provide comprehensive training on proper operation, parameter adjustments, safety procedures, and basic troubleshooting.
Conclusion
Semi-automatic coil wrapping machines equipped with automatic cutters represent a significant upgrade over manual methods, offering enhanced efficiency, consistency, and operator ergonomics for businesses packaging coiled products. By carefully considering the technical specifications, optimizing operational parameters, and adhering to proper maintenance and safety protocols, these machines provide a reliable and cost-effective solution for improving coil packaging operations in various industrial distribution and manufacturing environments.
https://www.fhopepack.com/Tyre-packing-machine/
info@fhopepack.com