Enhanced Rotary Arm Pallet Wrapping Machine: The R300 In-Depth
In demanding industrial environments where pallet wrapping speed, load stability, and automation are paramount, rotary arm pallet wrappers offer distinct advantages, especially for heavy or unstable loads. The Fhope R300 model exemplifies this technology, designed as a fully automatic system integrating robust engineering with sophisticated control for high-throughput packaging lines.
1. Operational Principle and Core Design
Unlike traditional turntable wrappers that rotate the pallet, the R300 utilizes a rotary arm design. The pallet load remains stationary – a critical advantage for unstable, very light, or extremely heavy loads that might shift or collapse during rotation.
- Mechanism: The wrapping arm, equipped with the stretch film carriage, rotates around the stationary pallet. This allows for higher rotation speeds compared to turntable models without compromising load integrity.
- Structure: Built on a heavy-duty steel frame, the R300 is engineered for durability and stability during high-speed operation. Its design typically requires dedicated floor space but eliminates the need for a heavy rotating platform integrated into the conveyor line.
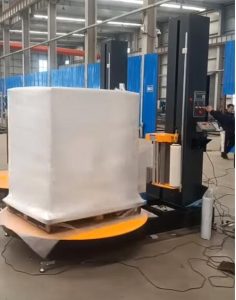
2. Key Components and Construction Details
The R300's performance relies on the synergy of several high-quality components:
- Rotary Arm Drive: Precision bearing slewing ring and a variable frequency drive (VFD) controlled motor ensure smooth, controlled rotation and speed adjustment.
- Film Delivery System: A powered pre-stretch film carriage is standard, stretching the film typically between 150% to 300% before application. This optimizes film usage (reducing costs) and enhances load containment force.
- Control System: A Programmable Logic Controller (PLC), often from reputable brands like Siemens or Allen-Bradley, serves as the brain, coordinating all machine functions.
- Human-Machine Interface (HMI): A touchscreen panel allows operators to easily set parameters, select wrap patterns, monitor status, and perform diagnostics.
- Sensors: Photo-eyes detect pallet height automatically, ensuring optimal film placement and preventing over-wrapping. Safety sensors (light curtains, fencing interlocks) protect personnel during operation.
- Film Management: Features often include automatic film clamping, cutting, and wiping/sealing mechanisms for a fully automated cycle start and finish.
3. R300 Technical Specifications Overview
While specific configurations can vary, typical R300 performance parameters include:
- Rotational Speed: Up to 25-35 Revolutions Per Minute (RPM), enabling high throughput.
- Maximum Load Dimensions (L x W x H): Commonly accommodates pallets up to 1200mm x 1200mm x 2400mm (approx. 48" x 48" x 94"), with options for larger sizes.
- Load Weight Capacity: Effectively unlimited as the load remains stationary on the conveyor or floor. Conveyor capacity is the limiting factor.
- Film Pre-Stretch Ratio: Standard 250%, adjustable electronically via HMI (options often range from 150% to 300%+).
- Film Type Compatibility: Designed for standard LLDPE machine stretch film rolls (e.g., 500mm/20” width, up to 23 microns).
- Throughput: Capable of wrapping 40-60+ pallets per hour, depending on load height, wrap pattern complexity, and conveyor integration speed.
- Power Requirements: Typically 480V/3Ph/60Hz or tailored to regional standards.
- Control: PLC system with intuitive touchscreen HMI.
4. Performance Advantages and Efficiency Gains
The R300 delivers tangible benefits in industrial packaging:
- Increased Throughput: The high rotation speed significantly boosts the number of pallets wrapped per hour compared to manual or semi-automatic methods.
- Labor Reduction: Fully automatic operation minimizes the need for manual intervention, freeing up personnel for other tasks and reducing labor costs.
- Optimized Film Consumption: Powered pre-stretch significantly reduces the amount of film used per pallet, leading to substantial material cost savings.
- Enhanced Load Protection & Stability: Consistent wrap patterns and adjustable tension ensure superior load containment, protecting goods from shifting, dust, and moisture during transit and storage.
- Improved Safety: Automating the wrapping process removes operators from the immediate vicinity of rotating machinery and heavy loads.
5. Control System Flexibility and Integration
The PLC control system is central to the R300's versatility:
- Programmable Parameters: Operators can easily define and save multiple wrap programs via the HMI, specifying parameters like top/bottom wrap counts, film tension, overlap percentage, and rotation speed for different load types.
- Automation Integration: The R300 is designed for seamless integration into automated packaging lines, communicating with upstream and downstream conveyors, palletizers, and warehouse management systems (WMS).
- Diagnostics and Monitoring: The HMI provides real-time operational status, fault diagnostics, and maintenance alerts, simplifying troubleshooting and minimizing downtime.
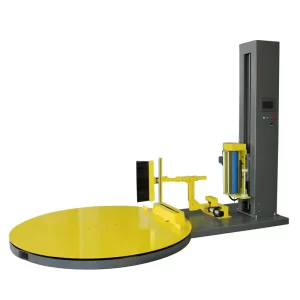
6. User Experience and Maintenance Considerations
From an operational standpoint, the R300 focuses on ease of use and reliability:
- Operator Interaction: The touchscreen HMI provides an intuitive interface for setup and daily operation. Film roll changes are typically designed for quick and easy execution.
- Reliability: Robust construction and high-quality components contribute to dependable performance in continuous operation environments.
- Maintenance: Routine maintenance usually involves sensor checks, lubrication of moving parts (like the slewing ring), and inspection of the film cutting and sealing mechanisms. The PLC diagnostics aid in identifying potential issues proactively.
7. Ideal Applications
The R300 rotary arm pallet wrapper is particularly well-suited for:
- High-volume distribution centers and warehouses.
- Manufacturing facilities with automated end-of-line packaging.
- Industries handling unstable loads (e.g., beverages, empty containers, tissue paper).
- Operations dealing with very heavy loads (e.g., building materials, metals).
- Applications where consistent load containment and presentation are critical.
8. Manufacturer Perspective: Fhope Packaging Machinery
Fhope, as a manufacturer of the R300 and similar automatic pallet wrapping systems, focuses on providing cost-effective and efficient packaging automation solutions. Their machines are engineered for ease of use and high productivity, aiming to help businesses optimize their packaging processes and reduce operational costs.
In conclusion, the R300 automatic rotary arm pallet wrapper represents a significant upgrade for high-demand packaging operations. Its PLC-controlled automation, combined with robust design and efficient film usage, delivers consistent, secure pallet wrapping while optimizing throughput and reducing labor requirements, making it a valuable asset for modern logistics and manufacturing.