Enhancing Workshop Safety and Efficiency: A Guide to Mold Tilters
Handling heavy, cumbersome molds and dies is a significant challenge in many manufacturing and fabrication settings. These essential components often weigh several tons and require precise maneuvering for maintenance, repair, or setup. Manual or improper handling poses substantial risks to personnel safety and can lead to costly damage to the molds themselves. This is where specialized equipment like mold tilters becomes indispensable.
1. What is a Mold Tilter?
A mold tilter, sometimes referred to as a die flipper, mold turnover machine, or upender, is a piece of industrial equipment specifically designed to safely rotate heavy, bulky items like injection molds, stamping dies, and large castings. Typically, they provide a 90-degree rotation, allowing operators to easily access different sides of the workpiece for maintenance or positioning. Some heavy-duty models can offer 180-degree or even 360-degree rotation for more complex tasks.
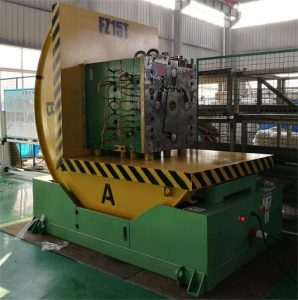
2. Key Benefits of Using a Mold Tilter
Integrating a mold tilter into your workflow offers several advantages over traditional handling methods (like cranes with chains or manual prying):
2.1. Enhanced Safety
Rotating multi-ton objects is inherently dangerous. Mold tilters provide a controlled, stable platform, significantly reducing the risk of accidents caused by slips, drops, or unstable loads. This minimizes potential injuries related to crushing or strenuous manual effort.
2.2. Increased Operational Efficiency
Tilting molds manually or with makeshift crane setups can be time-consuming and require multiple personnel. A dedicated mold tilter streamlines the process, allowing for faster rotation and turnaround times for maintenance or production changes, often requiring only a single operator.
2.3. Protection of Valuable Assets
Molds and dies represent significant capital investments. Improper handling can cause dents, scratches, or critical damage. Mold tilters provide smooth, controlled movement, preventing impacts and safeguarding the integrity and precision of these tools.
2.4. Improved Ergonomics
Eliminating the need for awkward manual pushing, pulling, or prying reduces physical strain on workers, contributing to a healthier and more productive workforce.
3. How Mold Tilters Work: Technical Insights
While designs vary, most mold tilters operate on a fundamental principle: securing the workpiece onto a table or platform and then rotating that platform using a powered mechanism.
3.1. Core Components:
- Base Frame: Provides stability and houses the drive mechanism.
- Rotating Table/Platform: The surface where the mold or die is placed. Often equipped with securing points or specialized surfaces (e.g., V-blocks, flat tables).
- Drive System: Typically electro-mechanical (using motors and gearboxes) or hydraulic (using cylinders and pumps) to provide the rotational force. Electro-mechanical systems often offer precise control and lower maintenance, while hydraulic systems can provide immense lifting/tilting power.
- Control System: Usually a pendant controller or remote control allows the operator to manage the tilting operation safely from a distance. Includes functions like start, stop, tilt forward/reverse, and emergency stop.
3.2. Typical Operational Sequence:
- Loading: The mold/die is placed onto the tilter's platform, often using an overhead crane or forklift.
- Securing: The workpiece may be secured using clamps, chains, or gravity, depending on the design and the load.
- Tilting: The operator initiates the tilting process via the control panel. The drive system smoothly rotates the platform to the desired angle (usually 90 degrees).
- Access/Work: Maintenance or other operations are performed on the now accessible side of the mold.
- Return Tilt: The platform is rotated back to its original position.
- Unloading: The workpiece is safely removed from the tilter.
4. Key Technical Specifications to Consider
When evaluating or specifying a mold tilter, several parameters are crucial:
- Load Capacity: The maximum weight the tilter can safely handle (e.g., ranges from 1 ton to over 100 tons).
- Tilting Angle: Typically 90 degrees, but other angles (180°, custom) may be available.
- Platform Size (L x W): Must accommodate the footprint of the molds/dies being handled.
- Tilting Speed: The time it takes to complete the rotation (can impact cycle times).
- Power Requirements: Voltage, phase, and power consumption (e.g., 220V/380V/480V, 3-phase).
- Control Type: Pendant, remote control, integrated panel.
- Safety Features: Limit switches (prevent over-rotation), emergency stop buttons, overload protection, potential locking mechanisms.
- Construction: Heavy-duty steel fabrication for durability and wear resistance.
mold tilter78 5. Operational Best Practices and Experience Sharing
To maximize the benefits and ensure the longevity of a mold tilter:
- Proper Loading: Always ensure the load is centered and stable on the platform before tilting. Adhere strictly to the rated load capacity.
- Operator Training: Only trained personnel should operate the equipment. Training should cover safe operating procedures, load limits, and emergency protocols.
- Regular Maintenance: Follow the manufacturer’s guidelines for inspection and maintenance. This typically includes checking hydraulic fluid levels (if applicable), lubricating moving parts, inspecting structural integrity, and testing control functions and safety features.
- Clear Operating Area: Keep the area around the tilter clear of obstructions and personnel during operation.
- Choosing the Right Model: Select a tilter with adequate capacity and platform size for your largest molds/dies, considering future needs. Over-specifying slightly is often better than under-specifying.
6. Mold Tilter in Action
Watch this video demonstration to see a typical mold tilter operating:
7. Integrating Tilters into the Workflow
Mold tilters are rarely standalone devices. They are typically integrated into a larger material handling workflow involving overhead cranes for loading/unloading onto the tilter and transport carts or forklifts for moving molds to/from storage or presses. Efficient plant layout considers the placement of the tilter to minimize travel distances and streamline the mold handling process.
8. Conclusion
Mold tilters are essential tools in modern manufacturing environments that handle heavy molds and dies. By providing a safe, controlled method for rotating these large components, they contribute significantly to workshop safety, operational efficiency, and the protection of valuable tooling assets. Careful selection based on technical requirements and adherence to operational best practices ensure these machines deliver maximum value.
Back to front page: https://cn.fhopepack.com/page/list.php?tid=132