Mastering Heavy Loads: A Technical Deep Dive into the Heavy-Duty Pallet Inverter for Oversized Pallets
Handling large, heavy, or unwieldy palletized loads presents significant logistical challenges in manufacturing, warehousing, and distribution. Manual rotation or transfer is often inefficient, labor-intensive, and carries inherent risks of worker injury and product damage. The specialized Heavy-Duty Pallet Inverter emerges as a critical engineering solution to address these operational bottlenecks.
1. The Operational Challenge: Beyond Standard Pallet Handling
Standard pallet handling equipment often falls short when dealing with non-standard dimensions or excessive weight. The manual or semi-automated methods employed can lead to:
- Increased Labor Costs: Requiring multiple personnel for safe manipulation.
- Safety Hazards: Potential for strains, sprains, and crush injuries during manual lifting and turning.
- Product Damage: Instability during rotation can cause shifting, breakage, or contamination.
- Process Inefficiency: Slow turnaround times impact overall throughput and productivity.
A customized, heavy-duty pallet inverter is specifically engineered to overcome these limitations for large-scale operations.
2. Defining the Heavy-Duty Pallet Inverter Solution
A customized heavy-duty pallet inverter is a robust piece of materials handling equipment designed explicitly for rotating or inverting pallets that exceed standard size and weight limits. Its core function is to provide a safe, automated, and efficient method for tasks such as:
- Switching loads from wooden pallets to more hygienic plastic or aluminum pallets (common in food and pharmaceutical industries).
- Replacing damaged pallets without destacking the load.
- Inverting products for layering, storage, or process requirements.
- Retrieving damaged goods from the bottom of a stack.
3. Engineering Deep Dive: Design, Structure, and Components
The reliability and performance of a heavy-duty pallet inverter hinge on its core engineering components:
- Structural Frame: Typically constructed from heavy-gauge, reinforced steel profiles (e.g., Q235 or equivalent structural steel) to withstand high torsional and compressive forces exerted by heavy loads during rotation. Finite Element Analysis (FEA) is often employed during the design phase to optimize strength and rigidity while minimizing material usage.
- Hydraulic System: The heart of the machine's power. This usually involves:
- High-Capacity Hydraulic Pump: Providing consistent fluid pressure.
- Dual Heavy-Duty Hydraulic Cylinders: Precisely engineered to ensure smooth, synchronized rotation and clamping pressure. Cylinder bore size and rod diameter are critical calculations based on maximum load capacity and desired speed.
- Hydraulic Power Unit (HPU): Containing the reservoir, motor, pump, filters, and control valves (solenoid or proportional) for managing fluid flow and pressure. Emphasis is placed on leak-free connections and efficient heat dissipation.
- Clamping Mechanism: Robust steel platforms (often with adjustable pressure settings) securely grip the pallet and load from top and bottom or sides. The design ensures even pressure distribution to prevent product damage. Surface options might include non-slip coatings or specialized materials for delicate loads.
- Drive System: Precision-engineered slew drives or robust chain-and-sprocket systems, coupled with geared hydraulic or electric motors, provide controlled rotational torque. Bearings must be rated for high radial and axial loads.
- Control System: Usually incorporates a Programmable Logic Controller (PLC) for managing the operational sequence, safety interlocks, and communication with optional peripherals. Operator interface is typically via a Human-Machine Interface (HMI) touchscreen panel or durable push-button controls. Remote control options enhance operator flexibility and safety by allowing operation from a distance.

4. Key Performance Metrics & Technical Specifications
When evaluating a heavy-duty pallet inverter, key technical data points are crucial:
- Load Capacity: Typically ranging from 1,500 kg (3,300 lbs) to 3,000 kg (6,600 lbs) or more for specialized applications.
- Maximum Pallet Dimensions: Accommodates oversized pallets (e.g., up to 1500mm x 1500mm or larger, specify L x W x H).
- Rotation Angle: Standard 180 degrees, though custom angles may be possible.
- Cycle Time: Typically 30-60 seconds for a full 180-degree rotation (load dependent). Faster speeds are achievable but may require more powerful hydraulic systems.
- Clamping Range: Minimum and maximum opening to accommodate various load heights.
- Noise Level: Engineered for reduced operational noise, often below 75 dBA, through optimized hydraulic design and component selection (e.g., low-noise pumps).
- Power Requirements: Dependent on motor size (e.g., 4-7.5 kW), typically 380V/50Hz or 480V/60Hz, 3-Phase.
- Control Voltage: Usually 24V DC for safety.
Technical Data Comparison (Illustrative Example):
Feature | Standard Inverter | Heavy-Duty Inverter (Fhope Model Example) |
---|---|---|
Max Load Capacity | ~1500 kg | 2000 kg - 3000+ kg |
Max Pallet Size (W x L) | ~1200 x 1200 mm | Up to 1500 x 1500 mm or custom |
Cycle Time | 45-75 sec | 30-60 sec |
Frame Construction | Standard Steel | Heavy-Gauge Reinforced Steel |
Control Options | Basic Panel | PLC + HMI, Optional Remote |
Noise Level | < 80 dBA | < 75 dBA (Low Noise Design) |
5. Enhancing Operational Efficiency and Workplace Safety
Integrating a heavy-duty pallet inverter yields tangible benefits:
- Productivity Boost: Automating the inversion process drastically reduces cycle times compared to manual methods.
- Labor Optimization: Frees up personnel from strenuous manual handling tasks, allowing reallocation to higher-value activities.
- Enhanced Safety: Eliminates direct manual lifting and rotation of heavy loads, significantly reducing the risk of musculoskeletal injuries. Safety features like light curtains, safety fencing, and emergency stops are standard.
- Reduced Product Damage: Controlled clamping and smooth rotation minimize the risk of load shifting, crushing, or dropping.
- Improved Ergonomics: Operators can manage the process via remote or panel controls from a safe and comfortable position.
6. Customization: Tailoring the Inverter to Specific Needs
Leading manufacturers like Fhope understand that one size rarely fits all in industrial applications. Customization options often include:
- Material Finishes: Stainless steel construction for food-grade or corrosive environments.
- Integration: Designed for seamless integration into automated conveyor lines.
- Safety Features: Enhanced guarding, area scanners, or specific interlocking requirements.
- Control Modifications: Custom PLC programming or integration with plant-wide SCADA systems.
- Load Handling: Specialized clamping jaws or platform surfaces for unique product types.
7. Real-World Application & User Experience
Operating a well-designed heavy-duty pallet inverter feels remarkably smooth and controlled, despite the immense forces involved. The low operational noise is immediately noticeable compared to older or less refined machinery. The intuitive controls, whether via HMI or remote, allow operators to confidently manage the entire cycle. From loading the pallet with a forklift to initiating the clamp and rotate sequence, the process is designed for efficiency. The stability during rotation instills confidence that the load is secure, translating directly to reduced damage and increased throughput. It becomes an indispensable tool rather than just a machine, fundamentally improving the workflow for handling bulky goods.
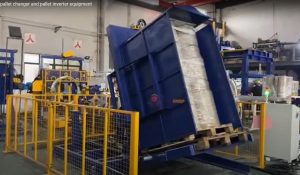
8. Exploring Different Pallet Inverter Technologies
While this article focuses on the robust 180-degree rotator, the pallet inverter family includes various designs suited for different needs, such as:
- Pallet Tippers/Exchangers: Often used for quickly switching pallets by tilting the load.
- Floor-Level Loaders: Allow pallet jack access, eliminating the need for a forklift in some scenarios.
- Inline Automated Systems: Fully integrated into production or packaging lines.
Fhope manufactures a range of these solutions, including pallet tippers and pallet changing machines, often available from stock or customizable at competitive price points, as demonstrated by recent projects for clients globally, including in Australia.
Back to front page: https://www.fhopepack.com/pallet-inverter/
Explore Our Pallet Inverter Video Gallery
9. Conclusion: A Strategic Investment in Efficiency and Safety
The customized heavy-duty pallet inverter is more than just machinery; it's a strategic investment in operational efficiency, worker safety, and product integrity. By automating the handling of large and heavy loads, businesses can achieve significant cost savings, enhance productivity, and maintain higher quality standards. With features like low noise operation, fast turning speeds, robust construction, and customization options offered by manufacturers like Fhope, these machines provide a reliable and indispensable solution for modern logistics and manufacturing challenges.