Adjustable Coil Tilter with Sliding Table: Technical Overview and Applications
Handling heavy coils, whether steel, aluminum, or other materials, presents significant challenges in industrial environments. Ensuring both operator safety and process efficiency requires specialized equipment. The adjustable, multipurpose coil tilter with a sliding table is one such solution designed to manipulate heavy cylindrical loads effectively. This overview details its operational principles, technical specifications, and application benefits, aligning with practical industry needs.
Video demonstrating the operation of an adjustable coil tilter with sliding table.
1. Operational Principle and Core Functionality
The primary function of a coil tilter is to safely change the orientation of a coil, typically from a horizontal (eye-to-sky) to a vertical (eye-to-wall) position, or vice versa. This specific model incorporates key features enhancing its utility:
- Adjustability: The equipment often allows for handling coils of varying diameters and widths within a specified range, offering flexibility for diverse production requirements.
- Tilting Mechanism: Utilizes robust hydraulic or electromechanical systems to achieve smooth and controlled tilting motion, typically up to 90 degrees.
- Sliding Table: This integrated feature allows for lateral movement of the coil after or before tilting. The sliding table facilitates precise positioning for subsequent processes, such as loading onto decoilers, transfer carts, or storage racks, minimizing the need for additional handling equipment.
upender and tilter with sliding table 2. Key Technical Specifications (Illustrative Data)
While specifications vary by manufacturer and model, typical parameters for such equipment include:
- Load Capacity: Ranging from 1 tonne to over 30 tonnes, depending on the application.
- Tilting Angle: Standard 90 degrees; custom angles may be available.
- Platform Dimensions (Coil Contact Surface): Designed to accommodate specific coil diameter and width ranges (e.g., V-saddle or flat platform).
- Sliding Table Travel Distance: Varies based on design, commonly ranging from 500 mm to 1500 mm or more.
- Tilting Speed / Cycle Time: Optimized for a balance between speed and safe operation (e.g., 30-90 seconds per 90-degree tilt).
- Power Unit: Typically electro-hydraulic (e.g., 400V/50Hz/3Ph or local standards).
- Control System: Push-button pendant or remote control, often with integrated safety interlocks.
- Construction Material: Heavy-duty steel structure for durability and stability.
3. The Advantage of the Integrated Sliding Table
The sliding table (or slid table) significantly enhances the machine's versatility:
- Precise Positioning: Allows operators to accurately align the coil with downstream equipment without needing complex crane manoeuvres or forklift repositioning.
- Reduced Handling Time: Streamlines the workflow by combining tilting and lateral positioning into a single sequence at one station.
- Improved Safety: Minimizes manual intervention and the risks associated with multiple handling steps.
- Space Efficiency: Can reduce the overall footprint required compared to separate tilting and transfer systems.
4. Common Industrial Applications
Adjustable coil tilters with sliding tables are employed across various sectors involved in coil processing and handling:
- Steel and Aluminum Service Centers: Preparing coils for slitting, cut-to-length lines, or storage.
- Stamping and Press Shops: Orienting coils correctly for feeding into stamping presses.
- Wire and Cable Manufacturing: Handling large reels or coils of raw material.
- Paper Mills: Managing large paper rolls.
- Automotive Manufacturing: Positioning coils within production lines.
5. Safety and Operational Considerations
Safe operation is paramount when dealing with heavy loads. These tilters typically incorporate multiple safety features:
- Stable Base Structure: Engineered to prevent tipping during operation.
- Limit Switches: Control the extent of tilt and slide movements.
- Hydraulic Safety Valves: Prevent sudden platform descent in case of hydraulic pressure loss.
- Emergency Stop Buttons: Located on the control panel for immediate shutdown.
- Operator Training: Crucial for understanding load limits, correct coil placement, and safe operating procedures.
From an efficiency perspective, integrating such a tilter can significantly reduce cycle times, lessen reliance on overhead cranes, and improve ergonomic conditions for operators by automating the reorientation task.
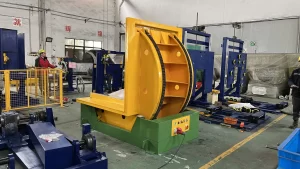
6. Maintenance and Longevity Insights
Regular maintenance ensures reliable performance and extends the equipment's lifespan. Key aspects include:
- Hydraulic System Checks: Monitoring fluid levels, checking for leaks, and filter changes.
- Lubrication: Regularly greasing pivot points, bearings, and sliding mechanisms as per manufacturer guidelines.
- Structural Inspection: Periodically checking welds, fasteners, and load-bearing surfaces for wear or damage.
- Electrical System Review: Inspecting wiring, limit switches, and control components.
Addressing minor issues proactively can prevent costly downtime and maintain operational safety.
Conclusion
The adjustable coil tilter with an integrated sliding table represents a valuable asset in modern material handling operations. By combining safe and controlled tilting with precise lateral positioning, it enhances productivity, improves workplace safety, and offers operational flexibility across various industries dealing with heavy coils. Understanding its technical capabilities and operational nuances allows for its effective integration into manufacturing and processing workflows.
For further details on different types of coil handling equipment, you can explore various coil upenders and tilters.
info@fhopepack.com