Innovations in Automatic Vertical Slitting Coil Packaging Solutions: Enhancing Efficiency and Protection
The handling and packaging of slitting coils, particularly in industries like steel and aluminum processing, present unique challenges. Ensuring product integrity, preventing damage during transit and storage, and optimizing logistical efficiency are paramount. Traditional manual or semi-automated methods often fall short, leading to increased labor costs, potential safety hazards, and inconsistent packaging quality. Addressing these critical needs, innovations in automatic vertical slitting coil packaging systems represent a significant leap forward in manufacturing and supply chain operations.
The Core Technology: Automated Vertical Packaging Explained
Automatic vertical coil packaging lines are sophisticated systems designed to streamline the entire process, from coil reception to final dispatch-ready packaging. Unlike horizontal systems, the vertical orientation offers distinct advantages, particularly for narrow slit coils, minimizing the risk of coil collapse or edge damage during handling.
Key components and operational principles often include:
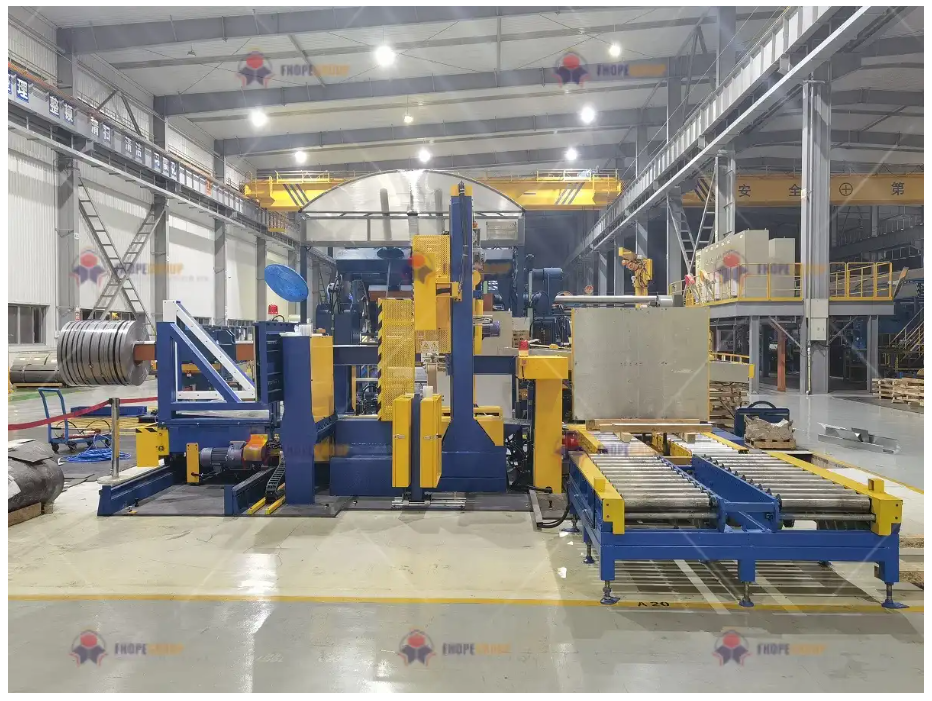
- Infeed Conveyor System: Robust conveyors engineered to safely transport coils of varying weights and dimensions to the packaging station. Advanced systems may incorporate sensors for precise coil positioning and sequencing.
- Central Positioning Unit: Crucial for accuracy, this mechanism ensures the coil is perfectly centered before wrapping begins. Technologies employed can range from mechanical guides to laser or optical sensors, enhancing packaging consistency and stability. This precision is vital, as highlighted in studies focusing on load stability in logistics (e.g., research published in Transportation Research Part E: Logistics and Transportation Review).
- Vertical Wrapping Mainframe: The heart of the system, utilizing materials like stretch film, VCI paper, or polypropylene woven fabric. The vertical rotation allows for comprehensive wrapping around the coil's circumference and through its eye, providing robust protection against environmental factors like moisture and dust – critical for preventing corrosion, a topic frequently addressed by organizations like NACE International (now AMPP).
- Automated Strapping Station: Applies radial or through-eye strapping (typically PET or steel straps) to secure the packaging material and enhance the structural integrity of the packed coil. Integration with the wrapping process ensures a seamless workflow.
- Control System & HMI: Sophisticated PLC (Programmable Logic Controller) systems coupled with intuitive Human-Machine Interfaces (HMIs) allow operators to monitor the process, adjust parameters, and manage different packaging recipes for various coil specifications. This level of automation aligns with Industry 4.0 principles, focusing on interconnectedness and data-driven operation.
Driving Efficiency: Performance and Economic Benefits
The adoption of automated vertical packaging lines yields substantial operational and financial advantages. Systems like the economic type slitting coil fully automatic packaging line developed by Fhope team exemplify how automation translates into tangible benefits.
- Reduced Labor Costs: Automation significantly minimizes the need for manual intervention in the wrapping and strapping processes, leading to direct savings on labor expenses.
- Increased Throughput: Continuous, automated operation allows for faster packaging cycles compared to manual methods, boosting overall production output. Industry benchmarks often show automation can increase packaging speeds by over 50%.
- Enhanced Packaging Quality: Consistent application of wrapping material and strapping ensures uniform, high-quality packaging for every coil, reducing the risk of damage claims and improving customer satisfaction. The precise control over wrapping tension and overlap is often a focus of packaging machinery patents (e.g., within classifications like B65B - Conveying; Packing; Storing).
- Improved Safety: Automating the handling and packaging of heavy coils reduces manual lifting and manipulation, significantly lowering the risk of workplace injuries.
Technical Superiority: Precision and Adaptability
Modern vertical coil packaging lines are engineered for precision and flexibility, catering to the diverse needs of the metal processing industry.
- Adjustable Parameters: Key settings such as wrapping tension, film overlap percentage, conveyor speed, and strapping positions can be easily adjusted via the HMI. This allows optimization for different coil dimensions (ID, OD, width), weights, and material types (e.g., sensitive aluminum surfaces vs. robust steel coils).
- Versatility: These systems are designed to handle a broad spectrum of coil sizes and weights, making them suitable for various slitting operations and end-use applications. This adaptability is crucial for job shops and service centers handling diverse customer orders.
- Material Compatibility: Engineered to work effectively with a range of packaging materials, allowing companies to choose the best option for corrosion protection, physical cushioning, and cost-effectiveness based on the specific coil material and transport requirements.
Reliability and Maintenance: Ensuring Long-Term Value
Beyond immediate performance gains, the long-term operational reliability of these systems is a key consideration.
- Robust Construction: Built with high-quality materials and components designed for industrial environments, ensuring durability and extended service life.
- Ease of Maintenance: Thoughtful design often incorporates features for easy access to key components, simplifying routine maintenance and cleaning. This minimizes downtime, contributing positively to the Overall Equipment Effectiveness (OEE).
- Minimized Downtime: The inherent reliability of automated systems, coupled with ease of maintenance, ensures maximum uptime and consistent productivity.
Conclusion: Investing in the Future of Coil Handling
Automatic vertical slitting coil packaging solutions offer a compelling combination of efficiency, protection, cost savings, and safety. By leveraging automation, precision engineering, and adaptable design, these systems address the core challenges of coil handling in demanding industrial settings. As highlighted in publications like Modern Metals or Metal Center News, investments in advanced automation are becoming increasingly critical for maintaining competitiveness in the global metals market. Choosing a well-designed, reliable system represents a strategic investment in operational excellence, product quality, and future growth.