Optimizing Aluminum Handling: A Technical Overview of Automatic Profile Stacking Lines
Handling long, delicate aluminum profiles efficiently and without damage is a critical challenge in the aluminum extrusion and distribution industry. Manual stacking is labor-intensive, slow, and carries a significant risk of scratches, dents, and worker injury. Automatic aluminum profile stacking lines offer a robust, automated solution, dramatically enhancing throughput, safety, and product quality. This technical overview explores the design, components, operation, and benefits of these essential systems.
1. The Core Challenge: Manual vs. Automated Profile Handling
Manually handling aluminum extrusions, especially long or complex shapes, presents several difficulties:
- Damage Risk: Profiles are susceptible to surface damage (scratches, abrasions) and deformation during handling and stacking.
- Labor Intensity: Requires significant manpower, increasing operational costs and potential for ergonomic injuries.
- Inconsistency: Manual stacking can lead to unstable or poorly organized bundles, complicating storage and transport.
- Speed Limitation: Manual processes inherently limit the overall speed of the production or distribution line.
Automated stacking lines directly address these issues by providing a controlled, repeatable, and efficient handling process.
2. Anatomy of an Automatic Aluminum Profile Stacking Line
While designs vary based on specific application requirements, typical systems incorporate several key components:
- 2.1 Infeed Conveyor System: Transports individual or grouped profiles from the preceding process (e.g., extrusion cooling table, cutting station) to the stacking area. This often includes belt, roller, or chain conveyors designed for smooth profile movement.
- 2.2 Profile Alignment/Positioning Unit: Ensures profiles are correctly oriented and positioned before lifting. This may involve sensors, guides, pushers, or robotic arms for precise placement, critical for stable stack formation.
- 2.3 Lifting/Stacking Mechanism: The core of the system. Commonly utilizes robust lifting forks, vacuum lifters, or specialized grippers to pick up one or multiple profiles (a layer) and place them onto the growing stack or pallet. Fork-based systems are common for their durability and ability to handle various profile geometries.
- 2.4 Layer Separation (Optional): For sensitive profiles or specific packaging requirements, the system may incorporate mechanisms to automatically place protective separators (e.g., paper, plastic film, wooden spacers) between layers.
- 2.5 Pallet Dispenser/Outfeed System: Automatically dispenses empty pallets or dunnage into the stacking position and conveys the completed stack away for wrapping, strapping, or storage.
- 2.6 Control System (PLC): The brain of the operation, typically a Programmable Logic Controller (PLC) integrated with Human-Machine Interface (HMI) panels. It sequences all movements, monitors sensors, manages recipes for different profile types, and provides diagnostic feedback.

3. Operational Workflow: How It Works
The typical operational sequence follows these steps:
- Profile Arrival: Profiles arrive individually or in groups on the infeed conveyor.
- Positioning & Alignment: Sensors detect profile presence, and the alignment unit positions them correctly for lifting.
- Layer Formation: The system accumulates the required number of profiles to form a complete layer.
- Lifting: The lifting mechanism (e.g., forks) engages and lifts the formed layer.
- Stacking: The lifted layer is transported and carefully placed onto the pallet or the previous layer. Automatic positioning ensures precise placement.
- Separator Insertion (If equipped): A separator sheet or dunnage is placed on the newly stacked layer.
- Lowering & Retraction: The lifting mechanism retracts to pick up the next layer.
- Stack Completion: Steps 3-7 repeat until the desired stack height or count is reached.
- Outfeed: The completed stack is moved out of the stacking station via the outfeed conveyor.
- New Pallet (If applicable): An automatic pallet dispenser places a new empty pallet into position.
4. Key Technical Specifications & Considerations
When evaluating or specifying an automatic stacking line, consider these parameters:
- Load Capacity: The maximum weight the lifting mechanism can handle per cycle.
- Typical Range: 500 kg to 3,000 kg (1,100 lbs to 6,600 lbs), highly dependent on design.
- Cycle Time: The time required to pick, place, and return for one layer. Directly impacts overall throughput.
- Typical Range: 15 seconds to 60 seconds per layer, varying with travel distance and profile complexity.
- Profile Dimensions Handled: The minimum and maximum length, width, and height of profiles the system can accommodate.
- Length: Often up to 6m (20 ft) or 12m (40 ft), sometimes longer.
- Width/Height: Varies widely based on stack configuration.
- Maximum Stack Height/Weight: The limits for the completed stack, often dictated by pallet strength, downstream processes, or storage constraints.
- Positioning Accuracy: The precision with which layers are placed (+/- mm). Crucial for stack stability and appearance.
- Power Requirements: Electrical (Voltage, Phase, Amperage) and Pneumatic (Pressure, Flow) needs.
- Footprint: The physical space required for the machine, including safety zones and access for maintenance.
- Integration: Capability to communicate with upstream/downstream equipment and plant-level control systems (MES/ERP).
5. Benefits for Industrial Distribution & Manufacturing
Investing in automated profile stacking yields significant operational advantages:
- Increased Throughput & Efficiency: Faster cycle times compared to manual methods directly increase line output. Continuous operation minimizes bottlenecks.
- Reduced Labor Costs & Improved Safety: Automates repetitive and potentially hazardous manual lifting tasks, reducing direct labor requirements and minimizing risks of strains, sprains, and impact injuries.
- Enhanced Product Protection: Gentle, controlled handling with features like automatic positioning significantly reduces scratches, dents, and deformation, improving final product quality and reducing scrap. Lifting forks provide stable support during transfer.
- Consistency and Quality Control: Automated systems produce uniform, stable stacks every time, improving load stability for storage and transport and presenting a professional product appearance.
- Optimized Warehouse Space: Neatly stacked bundles allow for more efficient use of vertical storage space.
6. Operator Experience & Maintenance Considerations
Modern stacking lines are designed with usability and maintainability in mind:
- User Interface (HMI): Touch-screen interfaces allow operators to select recipes (pre-programmed settings for different profiles), monitor system status, adjust parameters, and access troubleshooting guides.
- Ease of Use: Systems are typically designed for straightforward operation after initial training.
- Maintenance: Requires regular preventative maintenance, including lubrication, inspection of wear parts (conveyor belts, bearings, fork tines, sensors), and calibration checks. Access points are usually designed for ease of service.
- Troubleshooting: Integrated diagnostics within the PLC/HMI help quickly identify and resolve issues like sensor faults or jams.
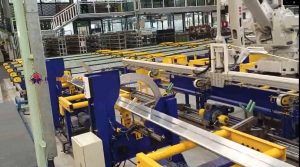
7. Supplier Spotlight: Fhopepack Solutions
Manufacturers like Fhope provide automatic aluminum profile stacking lines incorporating features discussed above. Their offerings often emphasize:
- Lifting Fork Design: Robust forks for secure handling of various profile shapes.
- Automatic Positioning: Integrated sensors and actuators for precise layer placement, enhancing stack quality and system efficiency.
- Capacity: Systems are available with varying capacities, such as models handling up to 1.5 tons (approx. 1500 kg) per lift, catering to different production needs.
- Efficiency Focus: Designs aimed at optimizing cycle times and minimizing manual intervention.
Fhope's solutions represent the type of automated equipment that can streamline the stacking process, reduce labor costs, improve safety, and ultimately enhance the quality and consistency of stacked aluminum profiles. For more details on their specific aluminum handling equipment, visit: https://www.fhopepack.com/Aluminum/
8. Conclusion: A Strategic Investment
Automatic aluminum profile stacking lines are no longer a luxury but a strategic necessity for competitive aluminum extruders and distributors. By replacing manual labor with precise, efficient automation, these systems deliver tangible benefits in productivity, cost reduction, safety, and product quality. Careful consideration of technical specifications, component design, and integration capabilities ensures the chosen system meets specific operational needs, providing a strong return on investment and optimizing a critical stage in the aluminum handling process. As automation technology continues to advance, expect further integration of robotics, advanced vision systems, and IIoT connectivity for even greater performance and predictive maintenance capabilities.
For further information on industry standards and best practices in aluminum extrusion, consider resources from the Aluminum Extruders Council (AEC) or broader material handling insights from MHI.