Horizontal wrapping machines, also known as orbital wrappers, represent a cornerstone technology in modern industrial packaging, particularly for long, bulky, or irregularly shaped products. Ensuring product integrity and load stability during transit and storage is paramount in the distribution chain. This article delves into the specifics of the Master horizontal wrapping machine provided by FHOPE, exploring its technical specifications, design features, operational benefits, and real-world applications, offering valuable insights for operations managers and packaging engineers.
1. Understanding the Master Horizontal Wrapping Machine
The FHOPE Master horizontal wrapping machine is specifically engineered to apply stretch film around the length of products as they pass horizontally through the wrapping ring. Unlike traditional turntable wrappers suited for palletized loads, this orbital wrapping method is ideal for items such as lumber, pipes, profiles (aluminum, PVC), doors, windows, and bundled materials. Its primary function is to provide a protective, unitizing layer of film, safeguarding products from environmental factors like dust, moisture, and scratching, while also securing them for handling and transport. FHOPE positions this machine for enterprises requiring robust solutions for large-specification product packaging.
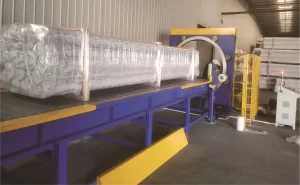
2. Key Technical Specifications and Performance Data
While exact specifications can be tailored to customer requirements, typical performance parameters for a machine in the Master series include:
- Maximum Product Cross-Section: Varies significantly based on model configuration (e.g., up to 1200mm x 1200mm or larger for custom builds).
- Maximum Product Length: Typically unlimited, constrained only by conveyor length and facility space.
- Wrapping Ring Speed (RPM): Adjustable, often ranging from 30 to 90 RPM, directly impacting throughput.
- Conveyor Speed: Variable, typically adjustable from 5 to 15 meters per minute, synchronized with ring speed for optimal wrap overlap.
- Stretch Film: Compatible with standard LLDPE stretch film rolls (e.g., 500mm width, 76mm core diameter).
- Film Pre-Stretch Ratio: Often includes powered pre-stretch systems, capable of stretching film up to 250-300%, maximizing film yield and load containment force.
- Control System: PLC (Programmable Logic Controller) with HMI (Human-Machine Interface) touch screen for parameter adjustment, diagnostics, and program storage.
- Power Requirements: Typically 480V, 3-Phase, 60Hz (or specified local standard).
- Pneumatic Requirements: Compressed air often required for cutting and clamping mechanisms (e.g., 6-8 bar).
Note: Data presented is indicative. Consult FHOPE for precise specifications based on the specific model and configuration.
3. Design and Structural Features
Built for demanding industrial environments, the Master horizontal wrapper emphasizes durability and operational efficiency:
- Heavy-Duty Steel Frame: Provides stability and longevity, minimizing vibration during high-speed operation.
- Rotating Ring Assembly: Precision-engineered ring housing the film carriage, ensuring smooth and consistent film application.
- Infeed and Outfeed Conveyors: Often feature driven rollers or belts, designed to handle heavy loads and provide smooth product transition through the wrapping zone. Side guides or pressure rollers may be included for product stability.
- Safety Features: Includes safety guarding, emergency stop buttons, and potentially light curtains to protect operators.
- Modular Design: Allows for easier integration into existing production lines and facilitates potential future upgrades or modifications.
4. Core Components Breakdown
Understanding the key components provides insight into the machine's operation:
- Wrapping Ring Assembly: The heart of the machine, carrying the film roll carriage and applying the film orbitally around the product.
- Film Carriage & Pre-Stretch Unit: Holds the stretch film roll and applies tension. Advanced models feature powered pre-stretch rollers to elongate the film before application, optimizing material usage and load security.
- Conveyor System: Transports the product horizontally through the wrapping ring at a controlled speed. Roller type (steel, PVC coated) and drive mechanism are chosen based on product characteristics.
- Control Panel (PLC/HMI): Allows operators to set wrapping parameters (ring speed, conveyor speed, number of wraps, wrap overlap, film tension), store recipes for different products, and monitor machine status and diagnostics.
- Automatic Film Cut and Clamp Unit: At the end of the wrapping cycle, this mechanism automatically cuts the film and clamps the tail, preparing the machine for the next product and ensuring a clean finish.
- Film Tail Treatment: Often includes a wipe or heat-seal mechanism to secure the film tail to the product, preventing unraveling.
board and cabinet horizontal wrapping machine testing video with two layers packing material 5. Operational Workflow and Automation
The Master horizontal wrapper streamlines the packaging process through automation:
- Product Entry: The product is placed onto the infeed conveyor, either manually or via an automated upstream process.
- Automatic Sensing: Sensors detect the leading edge of the product, initiating the wrapping cycle.
- Film Application Start: The machine may automatically cover the leading end of the product with film before orbital wrapping begins.
- Orbital Wrapping: The product moves through the rotating ring, which applies stretch film according to pre-set parameters (overlap, tension).
- Film Section Reinforcement: Specific sections (e.g., ends, middle) can receive additional wraps for enhanced protection or stability, programmed via the HMI.
- Film Cutting and Clamping: Once the trailing edge of the product is detected and wrapping is complete, the film is automatically cut and clamped.
- Product Exit: The fully wrapped product moves onto the outfeed conveyor for removal or downstream processing.
This level of automation significantly reduces manual labor requirements, improves consistency, and increases overall packaging throughput compared to manual methods.

6. Applications Across Industries
The versatility of the Master horizontal wrapping machine makes it suitable for a wide range of industries:
- Building Materials: Wrapping lumber, siding, insulation panels, PVC pipes, metal studs, doors, and windows.
- Metals Industry: Packaging aluminum extrusions, steel bars, copper pipes, and coiled products.
- Textiles: Securing rolls of fabric, carpet, or non-woven materials.
- Furniture: Protecting disassembled furniture components or long items like posts or frames.
- Plastics: Bundling plastic profiles, pipes, and sheets.
7. Benefits for Industrial Distribution & Manufacturing
Implementing a Master horizontal wrapper offers tangible advantages:
- Improved Load Stability: Securely unitizes long or bundled items, preventing shifting during handling and transport.
- Enhanced Product Protection: Creates a barrier against dust, dirt, moisture, and surface damage. Opaque film options can also provide UV protection or conceal contents.
- Increased Throughput: Automated wrapping cycles are significantly faster than manual methods, boosting packaging line efficiency.
- Reduced Labor Costs: Minimizes the need for manual wrapping labor, allowing personnel to be reallocated to other tasks.
- Material Savings: Powered pre-stretch systems maximize stretch film yield, reducing consumable costs per package.
- Professional Package Appearance: Consistent, tightly wrapped products present a more professional image.
8. User Experience Insights
From an operational standpoint, the Master wrapper is designed for usability and reliability:
- Ease of Operation: Intuitive HMI touch screens allow for quick setup and adjustment of wrapping parameters. Stored programs enable fast changeovers between different product types.
- Maintenance: Design considerations often include easy access to key components like the film carriage for roll changes and routine maintenance points for lubrication and inspection. Regular preventative maintenance is crucial for longevity.
- Integration: These machines can be integrated into fully automated packaging lines, receiving products from upstream processes and feeding them into downstream systems like labeling or palletizing.
9. Choosing the Right Configuration
Selecting the appropriate Master horizontal wrapping machine involves considering:
- Product Dimensions & Weight: Maximum and minimum size/weight dictates the required machine frame and ring size.
- Throughput Requirements: Desired packs per hour influences the necessary ring and conveyor speeds.
- Level of Automation: Options range from basic wrappers to fully automated systems integrated with conveyors and safety systems.
- Specific Product Needs: Requirements like end-covering, reinforcement wraps, or specific film types influence configuration.
Prospective buyers should engage with the manufacturer, FHOPE, to discuss specific application needs and determine the optimal machine configuration and features.
Conclusion
The FHOPE Master horizontal wrapping machine provides a robust and efficient automated solution for packaging long, bulky, or challenging product profiles. By incorporating advanced features like PLC controls, powered pre-stretch, and automatic cutting/clamping, it delivers significant benefits in terms of product protection, load stability, labor reduction, and material efficiency. For businesses in manufacturing and distribution dealing with such products, investing in this type of orbital wrapping technology can lead to substantial improvements in packaging operations and overall supply chain effectiveness.