Enhancing Packaging Efficiency: A Deep Dive into Horizontal Stretch Wrapping Machines for Bundles
In today's fast-paced logistics and manufacturing environments, optimizing packaging processes is paramount. The Horizontal Stretch Wrapping Machine for Bundles emerges as a critical asset, specifically engineered to consolidate and secure multiple items efficiently. This technology moves beyond basic packaging, offering enhanced load stability, product protection, and significant operational improvements. Whether dealing with timber, textiles, boxed goods, or extrusions, understanding the nuances of this equipment is key to leveraging its full potential.
1. Core Functionality: How Horizontal Bundle Wrapping Works
At its heart, a horizontal stretch wrapper automates the process of unitizing elongated or grouped products. Here’s a breakdown of the typical operational flow:
- Infeed: Bundles are placed onto or automatically fed onto the machine's conveyor system.
- Conveyance: The powered conveyor smoothly transports the bundle horizontally towards the wrapping zone.
- Wrapping Zone: As the bundle passes through a central opening, a rotating ring or orbiting arm dispenses stretch film, applying it circumferentially around the bundle. The bundle moves steadily while the film applicator revolves around it.
- Film Application: Sophisticated film carriage systems often pre-stretch the film (up to 300% or more), maximizing film yield and ensuring tight, secure wraps with optimal tension control.
- Cut and Seal: Upon cycle completion, an automated system typically clamps, cuts, and seals the film tail, preparing the machine for the next bundle.
- Outfeed: The fully wrapped bundle exits the machine via the outfeed conveyor, ready for storage or shipment.
This automated process ensures consistent wrap quality, improves throughput, and enhances the stability and protection of the bundled items during handling and transit.
2. Design and Structural Integrity
The performance and longevity of a horizontal wrapper heavily depend on its design and construction:
- Frame: Typically built with heavy-duty welded steel for rigidity and vibration damping, ensuring consistent wrapping even under continuous operation.
- Wrapping Mechanism:
- Rotating Ring: Often preferred for high-speed applications and smoother wrapping cycles, as the ring provides balanced rotation around the bundle.
- Orbiting Arm: Can sometimes offer more flexibility for highly irregular shapes or larger cross-sections, though potentially at lower maximum speeds.
- Conveyor System: Options include powered rollers (ideal for rigid items) or belt conveyors (better for softer or uneven bundles). Conveyor widths and heights are often customizable.
- Modularity: Modern designs often incorporate modular components, facilitating easier maintenance, upgrades, and integration with existing production lines (e.g., upstream bundling or downstream labeling systems).
horizontal oribital bubble film wrapper 3. Key Components Breakdown
Several critical components define the machine's capabilities and user experience:
- PLC (Programmable Logic Controller): The machine's central nervous system (often Siemens, Allen-Bradley, or similar), controlling all operational logic, timing, sequences, and safety interlocks.
- HMI (Human-Machine Interface): Typically a touchscreen panel providing intuitive operator control for setting wrap parameters (wrap counts, tension, overlap), selecting stored recipes, monitoring machine status, and accessing diagnostics.
- Film Carriage System: This is crucial for efficiency. Key features include:
- Powered Pre-Stretch: Stretches the film before application (e.g., 1 meter becomes 3 or 4 meters), significantly reducing film consumption and cost while increasing load holding force. Variable pre-stretch ratios are common.
- Tension Control: Electronic sensors and controls maintain consistent film tension regardless of bundle shape or size, preventing overtightening (damaging product) or undertightening (loose wrap).
- Sensors: Photo-eyes detect bundle presence, leading/trailing edges for accurate wrap start/stop, and safety sensors (like light curtains) protect operators.
- Safety Features: Essential for workplace safety, including emergency stop buttons, physical guarding around moving parts, and safety interlocks connected to the PLC.
4. Technical Specifications & Performance Data Comparison
Disclaimer: The parameters listed below are indicative and may not perfectly match the specific model shown in the video. Always consult us for precise specifications tailored to your application.
Indicative Machine Parameters:
- Machine Type: Horizontal Orbital Stretch Wrapper for Bundles
- Year of Manufacture Example: 2023 (Reflects current technology standards)
- Maximum Bundle Width: e.g., 1200mm
- Maximum Bundle Height: e.g., 1000mm
- Wrapping Speed: Up to 25 wraps (revolutions) per minute (Note: Actual throughput in bundles per minute/hour depends on bundle length, required overlap, and conveyor speed.)
- Film Type Compatibility: LLDPE Stretch Film (various thicknesses)
- Typical Pre-Stretch Ratio: 200-300% (Powered System)
- Power Requirements: e.g., 240V/415V, 50/60Hz, 3 Phase (Varies by region and configuration)
- Machine Footprint (Approx.): Length: 4000mm; Width: 2500mm; Height: 2200mm
- Machine Weight (Approx.): 1000kg - 2500kg+ (Depending on size and features)
- Control System: PLC with HMI Touchscreen
- Customizable Wrap Programs: Yes (Allows storing settings for different products)
Performance Comparison: Automated vs. Manual Wrapping
Feature | Automated Horizontal Wrapper | Manual Wrapping |
---|---|---|
Speed | High (e.g., 20-60+ bundles/hour) | Very Low (e.g., 2-10 bundles/hour) |
Consistency | Excellent (Uniform tension/overlap) | Poor (Highly variable) |
Film Usage | Optimized (Pre-stretch savings) | High (No pre-stretch) |
Labor Cost | Low (Minimal operator intervention) | High (Labor-intensive) |
Load Security | Superior | Often Inferior / Inconsistent |
Ergonomics | Good (Automated process) | Poor (Risk of strain/injury) |
Product Damage | Reduced (Controlled tension) | Higher Risk (Inconsistent tension) |
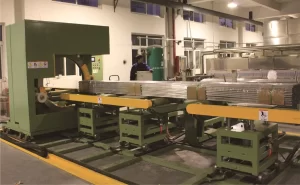
5. Real-World Applications & Quantifiable Benefits
The versatility of horizontal stretch wrappers translates into tangible benefits across industries:
- Logistics & Distribution: Securing bundles of grouped parcels or boxes ensures stability during automated sorting and transport, reducing damages and returns. Benefit: Faster processing, lower damage rates (potentially saving 1-3% of goods value), improved customer satisfaction.
- Building Materials: Wrapping bundles of timber, pipes, conduit, or extrusions protects them from weather damage and simplifies handling with forklifts. Benefit: Reduced material spoilage, safer and faster yard management, easier inventory counts.
- Textile Industry: Packaging large rolls of fabric, carpet, or nonwovens shields them from dust, moisture, and contaminants during storage and shipping. Benefit: Preserved product quality, reduced storage space requirements due to tight bundling, easier handling of bulky items.
- Manufacturing: Bundling metal rods, furniture components, or assembled sub-units streamlines internal logistics and prepares goods for secure shipping. Benefit: Improved workflow efficiency, reduced risk of scratches or damage during movement, professional package appearance.
6. Operational Insights: The User Experience
From an operator's standpoint, modern horizontal wrappers are designed for usability and efficiency:
- Ease of Operation: The HMI allows operators to easily select pre-programmed wrap recipes or adjust parameters like tension, wrap count at leading/trailing edges, and conveyor speed.
- Film Loading: Quick-load film carriages minimize downtime during roll changes. Standard film roll sizes are typically accommodated.
- Maintenance: Well-designed machines provide easy access to key components for routine maintenance like cleaning sensors, lubricating chains/bearings, and inspecting rollers. Diagnostic messages on the HMI assist in troubleshooting.
- Safety: Integrated safety features like light curtains at the infeed/outfeed and emergency stops provide a safer working environment compared to manual methods.
7. Choosing the Right Configuration
Selecting the appropriate horizontal stretch wrapper involves considering:
- Bundle Characteristics: Dimensions (Length, Width, Height), weight, shape (regular vs. irregular).
- Throughput Requirements: Required bundles per minute or hour.
- Level of Automation: Standalone machine vs. fully integrated into an automated production line.
- Film Specifications: Required film type, thickness, and pre-stretch capabilities.
- Operating Environment: Space constraints, temperature, cleanliness.
- Budget: Initial investment vs. long-term ROI through efficiency gains and material savings.
Conclusion: A Strategic Investment in Packaging Excellence
The Horizontal Stretch Wrapping Machine for Bundles is more than just packaging equipment; it's a strategic investment in operational efficiency, product integrity, and workplace safety. By automating the bundling process, businesses can achieve significant cost savings through reduced labor and optimized film consumption, while ensuring their products are securely wrapped and protected. The consistency and reliability offered by these machines are invaluable in meeting the demands of modern supply chains.
For detailed specifications or to discuss how a horizontal wrapper can be tailored to your unique application, please reach out to our specialists.