Automating the handling and packaging of steel pipes post-production is crucial for improving efficiency, safety, and throughput in modern manufacturing facilities. Manual processes are often labor-intensive, slow, and pose significant safety risks. This article explores an automated solution designed specifically for steel pipe counting, stacking, bundle forming (typically hexagonal), and strapping, as demonstrated in the video above. Understanding the technical specifications, design considerations, and operational benefits of such systems is key for manufacturers looking to optimize their downstream processes.
1. The Challenge: Manual Steel Pipe Handling and Packaging
Traditionally, moving steel pipes from cutting or finishing lines to storage or shipping involved considerable manual effort. Key challenges include:
- Labor Costs: High manpower requirements for counting, lifting, arranging, and strapping pipes.
- Efficiency Bottlenecks: Manual handling limits the overall speed of the production line.
- Safety Hazards: Lifting heavy pipes carries risks of musculoskeletal injuries and accidents.
- Inconsistent Bundling: Manual bundling can lead to variations in bundle shape, density, and integrity, affecting storage and transport.
- Product Damage: Improper handling can cause scratches, dents, or deformation to the pipes.
Automated systems directly address these pain points, offering a streamlined and reliable alternative.
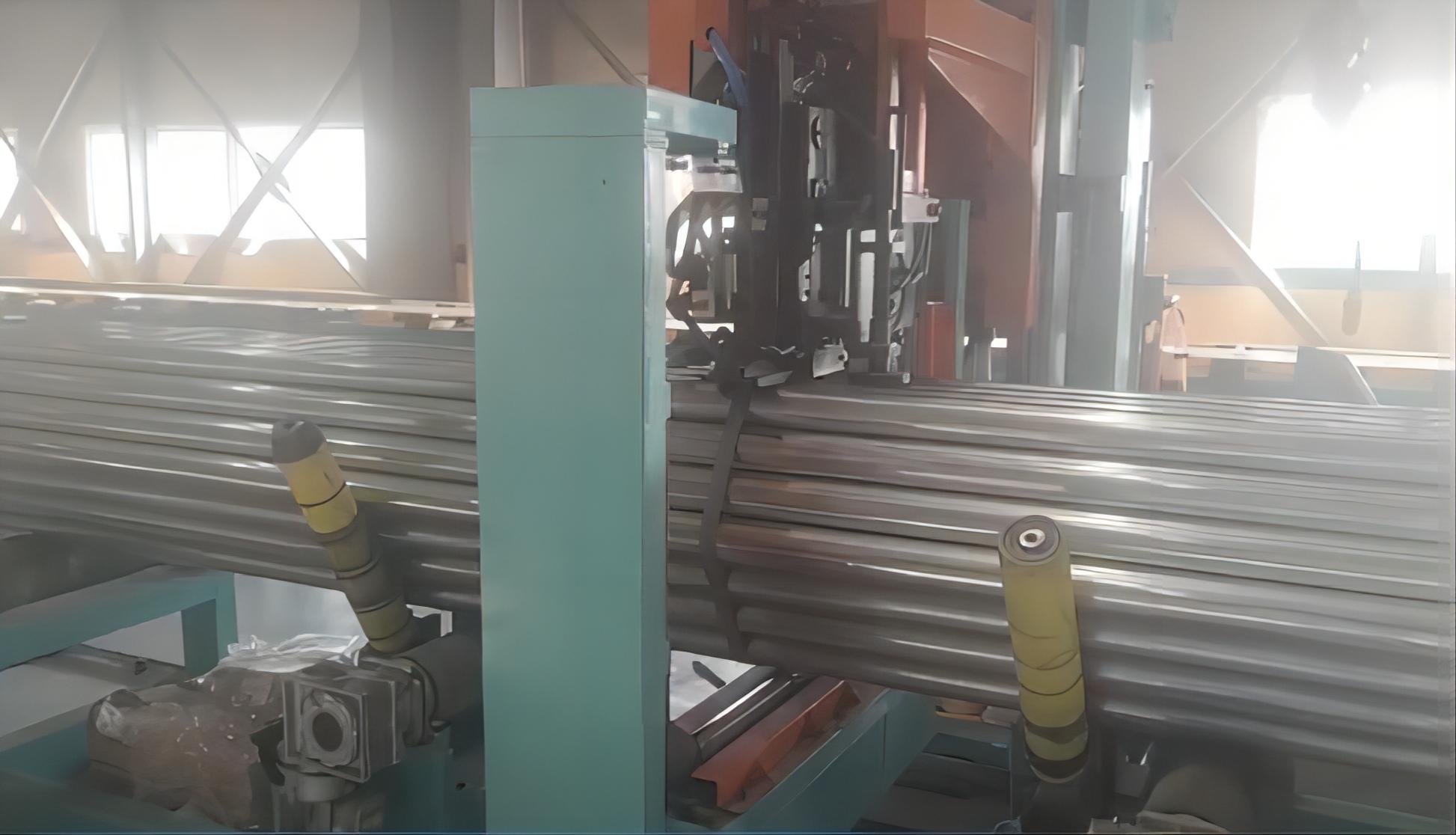
2. Solution Overview: Automatic Steel Pipe Bundling and Stacking Machine
The system showcased provides an end-to-end automated solution for preparing steel pipes for storage or shipment. Its core functions typically encompass:
- Pipe Reception: Receiving pipes individually or in layers from an upstream process (e.g., cutting machine, cooling bed).
- Counting and Collation: Accurately counting pipes and arranging them into predefined layer patterns.
- Hexagonal Bundle Formation: Systematically stacking layers to form a stable hexagonal bundle, maximizing packing density.
- Automatic Strapping: Securely strapping the formed bundle at multiple points using steel or PET straps.
- Bundle Discharge: Transferring the completed and strapped bundle to a storage area, roller conveyor, or crane pick-up station.
3. Key Design Features and System Components
A typical automatic steel pipe bundling system integrates several key components working in unison:
- Infeed Conveyor: Transports pipes from the production line to the bundling station. Often equipped with sensors for pipe detection and flow control.
- Pipe Counting & Alignment Mechanism: Uses sensors (photoelectric, laser, or vision systems) and mechanical actuators (stoppers, pushers) to count pipes accurately and align them for layer formation.
- Layer Forming Station: Collects the correct number of pipes and arranges them into a single layer, often using indexing forks or paddles.
- Bundle Forming Pocket/Cradle: A V-shaped or specially designed cradle where layers are deposited sequentially to build the hexagonal (or sometimes square/rectangular) bundle shape.
- Automatic Strapping Heads: Positioned strategically to apply, tension, seal, and cut strapping material (typically steel or high-strength PET) around the bundle. Multiple heads are common for long bundles.
- Bundle Ejection/Discharge Conveyor: Moves the finished bundle out of the machine, often incorporating weighing scales or labeling systems.
- Control System (PLC): A Programmable Logic Controller orchestrates the entire sequence, manages sensor inputs, controls motors and actuators, and interfaces with operators via an HMI (Human-Machine Interface). Safety interlocks and diagnostics are integral parts of the control logic.
4. Technical Specifications and Performance Data
While specific parameters vary based on application requirements, here's a typical range of technical data for such machines:
- Pipe Outside Diameter (OD) Range: 15 mm - 160 mm (customizable)
- Pipe Length Range: 3 m - 12 m (or specified range)
- Maximum Bundle Weight: 1000 kg - 5000 kg (dependent on design)
- Bundle Shape: Primarily Hexagonal (most common for round pipes), potentially Square/Rectangular
- Counting Accuracy: > 99.9%
- Cycle Time: 30 - 90 seconds per bundle (depending on pipe size, count, and strapping requirements)
- Strapping Material: Steel strap (e.g., 19mm, 32mm width) or PET strap
- Number of Straps per Bundle: 2 - 6 (adjustable positions)
- Control System: Siemens, Allen-Bradley, or equivalent PLC
- Power Requirements: 380V/50Hz/3Ph or customized
- Operating Air Pressure: 0.5 - 0.7 MPa
(Note: These are representative figures. Actual specifications are tailored to the customer's specific pipe dimensions, weight, and desired throughput.)
5. Operational Advantages and ROI
Implementing an automated pipe bundling system yields significant benefits:
- Increased Throughput: Drastically reduces bundling cycle times compared to manual methods, matching high-speed production lines.
- Reduced Labor Costs: Minimizes manual intervention, allowing personnel to be reassigned to higher-value tasks.
- Enhanced Safety: Eliminates heavy lifting and repetitive motions associated with manual bundling, reducing injury risks.
- Consistent Bundle Quality: Ensures uniform bundle shape, tightness, and strap placement, improving stability for handling and storage.
- Minimized Product Damage: Gentle, controlled handling reduces the likelihood of scratches or deformation.
- Improved Inventory Management: Accurate counting and potential integration with tracking systems enhance inventory control.
These advantages contribute to a tangible Return on Investment (ROI) through lower operating costs, higher productivity, and improved workplace safety.
6. Customization, Integration, and Operational Considerations
Flexibility is key in industrial equipment. These bundling systems are highly customizable:
- Size Adaptability: Designed to handle specific ranges of pipe ODs, lengths, and weights provided by the client.
- Layout Integration: Can be configured to fit existing plant layouts and integrate seamlessly with upstream (cutting, threading, coating) and downstream (storage, logistics) processes.
- Strapping Options: Choice of strapping material (steel/PET) and number/position of straps.
- Data Connectivity: Modern systems can offer data logging, remote diagnostics, and integration with plant-level Manufacturing Execution Systems (MES) for Industry 4.0 initiatives.
Operational Considerations:
- User Interface: HMIs typically provide intuitive controls for setting parameters (pipe count, bundle size), monitoring status, and troubleshooting alarms.
- Maintenance: Requires routine maintenance schedules for mechanical components, strapping heads, and sensors to ensure long-term reliability. Access points are usually designed for ease of maintenance.
- Reliability: Built for industrial environments, these machines are designed for continuous operation with high uptime, assuming proper maintenance protocols are followed.
7. Conclusion
Automatic steel pipe bundling and stacking machines represent a significant technological advancement over manual methods. By automating the counting, forming, and strapping processes, manufacturers can achieve substantial improvements in efficiency, safety, and bundle quality. The ability to customize these systems based on specific pipe dimensions and production requirements makes them a versatile solution for steel pipe mills and processing facilities aiming to optimize their end-of-line operations. The data clearly shows that investing in such automation leads to lower operational costs and a stronger competitive position.
For more detailed information on specific configurations and capabilities:
https://www.fhopepack.com/Automatic-pipe-bundle-packing-line.html