Operational Analysis: Automatic & Multipurpose Tilter for Box Handling
Automated material handling systems are essential components in modern logistics, manufacturing, and warehousing operations. Among these systems, automatic box tilters (also commonly referred to as box dumpers or tippers) provide a specialized function for efficiently and safely reorienting or emptying containers. This post delves into the operational principles, design considerations, and applications of such equipment, as demonstrated in the accompanying video.
1. Core Functionality and Mechanism
Automatic box tilters are designed to securely hold and rotate boxes, crates, or bins to a predetermined angle. The primary mechanism typically involves:
- Drive System: Often employing hydraulic cylinders or electro-mechanical actuators (like screw jacks or geared motors) to provide the necessary torque for lifting and tilting the load platform. Hydraulic systems offer high power density, while electro-mechanical systems can provide precise control and eliminate potential fluid leaks.
- Load Platform: The structure where the box or container is placed. It may include clamping mechanisms or specific shaping to secure the load during rotation.
- Frame and Pivot: The main structural base providing stability and the pivot point around which the tilting motion occurs.
- Control System: Usually managed by a Programmable Logic Controller (PLC) or dedicated control circuitry, allowing for automated cycles, adjustable tilt angles, speed control, and integration with other automation systems. Operator interfaces often include push buttons or touch screens.
The operational cycle typically involves loading the container onto the platform, initiating the tilt sequence via the control system, holding at the desired angle (for emptying or repositioning), and returning to the home position.
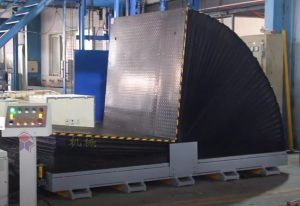
2. Key Design Considerations
Engineers designing or selecting an automatic box tilter must evaluate several critical factors:
- Load Capacity and Center of Gravity (CG): The machine must safely handle the maximum weight and dimensions of the intended load. Understanding the load's CG is vital for stability throughout the tilt cycle.
- Tilt Angle and Speed: Required angle (e.g., 90°, 120°, 180°) depends on the application (dumping vs. repositioning). Cycle time requirements dictate the necessary tilting speed, balancing throughput with smooth, controlled motion.
- Duty Cycle and Reliability: The expected frequency and duration of operation influence component selection (e.g., motor rating, bearing types) to ensure longevity and minimize downtime.
- Material Compatibility and Footprint: The materials being handled (e.g., powders, parts, liquids) may influence platform design (e.g., stainless steel, specific coatings). Physical space constraints dictate the maximum allowable machine footprint.
- Safety Features: Essential elements include physical guarding, emergency stop buttons, hydraulic velocity fuses (to prevent sudden drops), load sensors, and potential interlocks with upstream/downstream equipment. Compliance with relevant safety standards (e.g., ISO, ANSI, OSHA) is paramount.
- Maintenance Access: Designing for straightforward access to motors, hydraulics, bearings, and control panels simplifies routine maintenance and troubleshooting.
3. Technical Specifications (Example Parameters)
While specifications vary widely based on application, typical parameters for an automatic box tilter might include:
- Nominal Load Capacity: 500 kg - 2000 kg (1100 lbs - 4400 lbs)
- Maximum Tilt Angle: 90° to 180°
- Platform Size (L x W): Customizable, e.g., 1200 mm x 1000 mm (47" x 39")
- Tilting Time (90°): 15 - 40 seconds (adjustable)
- Control System: PLC with HMI or push-button controls
- Power Unit: Hydraulic Power Pack or Electric Motor/Gearbox
- Operating Voltage: e.g., 480V/3Ph/60Hz, 380V/3Ph/50Hz, or other industrial standards
- Control Voltage: Typically 24V DC
4. Applications and Use Cases
Automatic box tilters find application across various industries:
- Manufacturing: Tilting bins of components onto assembly lines or feeding parts into machinery at an ergonomic height.
- Warehousing & Logistics: Emptying received goods from containers, transferring bulk materials between bins, or preparing orders for shipment.
- Food Processing: Dumping ingredients into mixers or hoppers. Requires specific materials and cleaning considerations.
- Waste Management & Recycling: Emptying collection bins into larger receptacles or sorting lines.
- Agriculture: Handling crates of produce or tilting bins of feed.
These machines handle various cargo types, including standard cardboard boxes, plastic crates, metal bins, drums, and custom containers.
5. Operational Best Practices and Safety
Safe and efficient operation relies on proper procedures and maintenance:
- Thorough Operator Training: Ensure operators understand load limits, safe operating procedures, control functions, and emergency protocols.
- Pre-Use Inspections: Regularly check hydraulic fluid levels/leaks, structural integrity, fastener tightness, sensor function, and E-stop buttons.
- Correct Load Placement: Position the load centrally on the platform as intended by the design to maintain stability. Never exceed the rated capacity.
- Maintain Clear Operating Zone: Ensure the area around the tilter is free of personnel and obstructions during operation. Utilize safety guarding and light curtains where appropriate.
- Adhere to Maintenance Schedule: Follow manufacturer recommendations for lubrication, hydraulic filter changes, component checks, and electrical inspections.
- Compliance Checks: Regularly verify that safety features are functional and that operation complies with local and industry safety regulations.
mold maintain rotator and flipping table 6. Integration with Automated Systems
In automated facilities, box tilters are often integrated into larger material flow systems. This involves:
- Conveyor Interfaces: Automatic loading onto and unloading from the tilter platform via conveyor belts or rollers.
- PLC Communication: Handshaking signals between the tilter's controller and the main line control system to ensure synchronized operation (e.g., confirming position, load presence, cycle completion).
- Sensor Integration: Utilizing sensors (photoelectric, proximity, vision) to detect container presence/position, confirm tilting angle, or ensure safety interlocks are met.
Conclusion
Automatic box tilters offer significant advantages in material handling by improving operational efficiency, reducing the risk of musculoskeletal injuries associated with manual tilting, ensuring consistent process flow, and enabling integration into automated workflows. Understanding their design principles, application scope, and safety requirements is key to leveraging their full potential in industrial environments.
For information on related material handling equipment, such as coil upenders, visit: https://www.fhopepack.com/Coil_upender.html