Advanced 180-Degree Rotation Pallet Inverter: Enhancing Load Transfer with Double-Clamp Technology
Efficiently handling and transferring palletized loads is a critical aspect of modern logistics and manufacturing operations. The 180-degree rotation pallet inverter, particularly models equipped with double-clamp (or "double clapper") technology, offers a robust solution for inverting loads quickly, safely, and without manual handling. This system addresses common challenges such as exchanging pallets (e.g., wood to plastic/hygienic), recovering damaged goods at the bottom of a stack, or simply accessing the underside of a load.
Operational Mechanism and Engineering Principles
The core function involves rotating a full pallet load through 180 degrees. Unlike simpler tippers, the inverter securely grips the load before rotation begins. The "double-clamp" design, often employing hydraulic or electro-mechanical actuation, features two opposing pressure plates or "clappers."
- Loading: A palletized load is placed onto the inverter's loading platform, typically via forklift or conveyor.
- Clamping: The dual clamps engage simultaneously from the top and bottom (relative to the machine's orientation), applying controlled pressure to stabilize the load and the pallet together. This synchronized action is crucial for maintaining load integrity, a principle highlighted in various material handling equipment patents focusing on load stability during manipulation (e.g., concepts related to USPTO Class B65G - Conveying; Packing; Storing).
- Inversion: The secured load is then rotated 180 degrees around a central pivot point. The robust frame and powerful drive mechanism ensure a smooth, controlled rotation, minimizing G-forces exerted on the product.
- Release & Unloading: Once inverted, the clamps release, allowing the original pallet (now on top) to be removed. A new pallet can be placed before the load is rotated back or, more commonly, the inverted load is removed directly onto its new base pallet.
The double-clamp system provides superior load stabilization compared to single-clamp or side-support methods, particularly for unevenly stacked or sensitive goods. Research published in material handling journals often emphasizes the correlation between secure clamping methods and reduced product damage rates during automated handling processes.
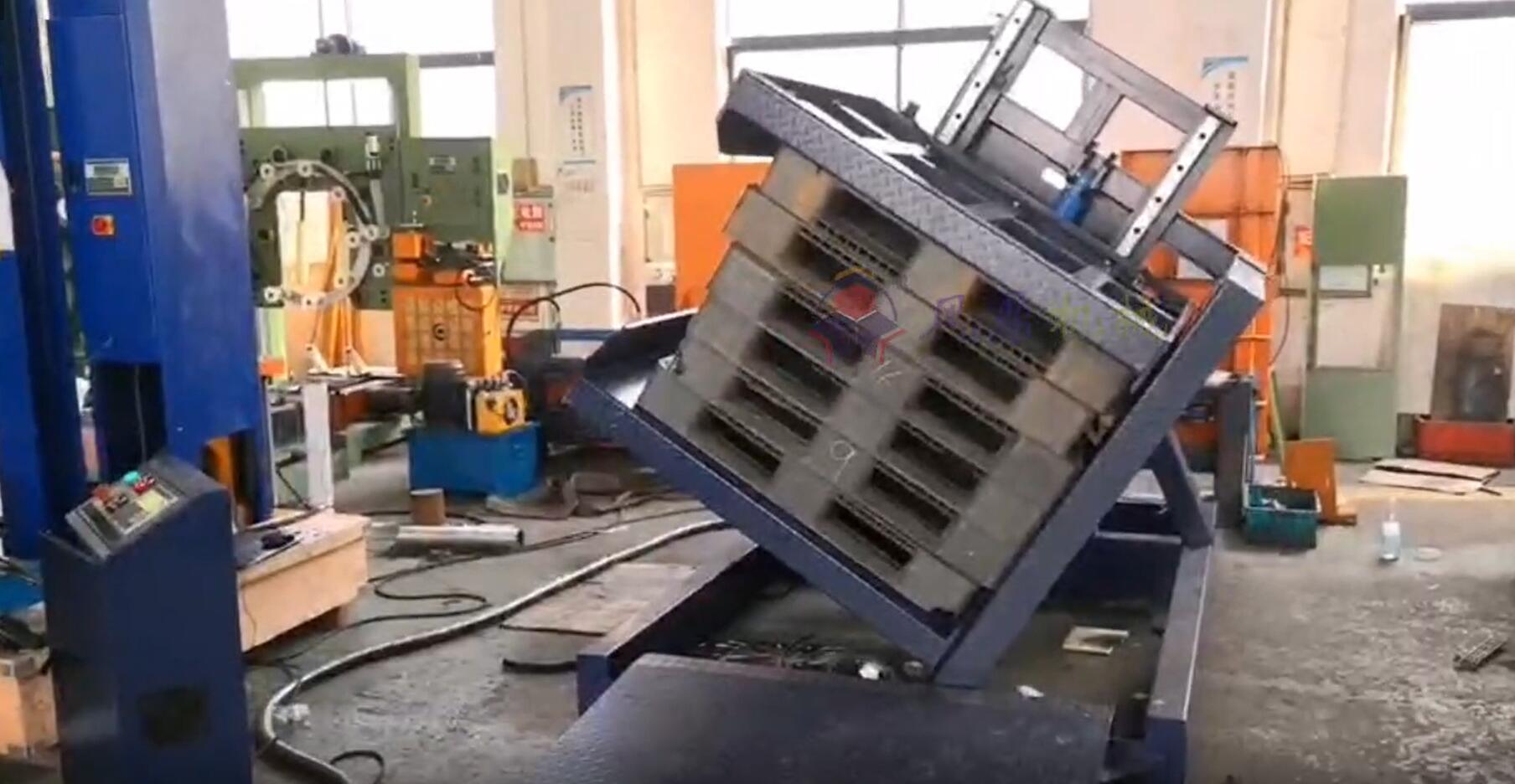
Key Features and Technical Specifications
Modern 180-degree double-clamp pallet inverters typically incorporate features designed for performance, safety, and durability:
- Dual Clamping System: Provides balanced pressure and secure load holding from opposite sides.
- Heavy-Duty Steel Construction: Ensures structural integrity and long service life under demanding industrial conditions.
- Hydraulic or Electric Drive: Offers reliable power for clamping and rotation. Hydraulic systems often provide higher clamping forces, while electric systems can offer cleaner operation.
- Adjustable Clamping Pressure: Allows operators to fine-tune the pressure based on load weight and fragility, preventing product damage.
- Control System: Options range from simple push-button controls to programmable logic controllers (PLCs) with touch-screen interfaces (HMIs) for integration into automated lines.
- Safety Features: Includes pressure relief valves, velocity fuses on hydraulic cylinders, safety guarding or light curtains, emergency stops, and potentially interlocked access doors, aligning with occupational safety standards (e.g., OSHA guidelines, ANSI/ITSDF B56 standards).
Typical Specification Ranges:
- Load Capacity: 1000 kg to 2500 kg (2200 lbs to 5500 lbs)
- Pallet Size Compatibility: Standard pallets (e.g., 1200x1000mm, 48"x40"), often with adjustable features for non-standard sizes.
- Rotation Speed / Cycle Time: Typically 40-60 seconds per 180-degree cycle (excluding loading/unloading).
- Clamping Range: Accommodates various load heights.
- Power Requirements: e.g., 480V/3Ph/60Hz or configured to local standards.
Advantages and Industrial Applications
The adoption of 180-degree double-clamp pallet inverters yields significant operational benefits:
- Enhanced Product Protection: Minimizes damage by securely holding the load during inversion, eliminating manual handling risks and issues associated with dragging or pushing loads.
- Increased Operational Efficiency: Automates the inversion process, significantly reducing the time and labor required compared to manual methods. Cycle times are predictable and consistent.
- Improved Worker Safety: Reduces manual lifting and awkward postures, mitigating risks of musculoskeletal injuries. Integrated safety features further protect operators.
- Versatility: Enables seamless pallet exchange (wood to plastic/aluminum, rental to in-house), handling of bagged goods (e.g., cement, seeds, flour where bags need flipping), inversion of loads for quality inspection, and recovery of damaged goods/pallets.
- Hygiene Compliance: Crucial in industries like food & beverage and pharmaceuticals, allowing transfer from external/wood pallets to sanitized internal pallets without direct product contact.
Common Industry Applications:
- Food and Beverage Processing
- Pharmaceutical Manufacturing
- Chemical Handling
- Printing and Paper Industries
- Automotive Parts Distribution
- General Warehousing and Logistics
Conclusion
The 180-degree rotation pallet inverter with double-clamp technology represents a sophisticated material handling solution engineered for efficiency and safety. Its ability to securely invert full pallet loads addresses critical operational needs across various industries, from maintaining hygiene standards to improving logistical throughput and protecting valuable goods. As highlighted in industry publications like Industrial Equipment News (IEN), advancements in automated handling equipment continue to drive productivity and safety improvements in manufacturing and distribution environments. For businesses seeking to optimize their pallet handling processes, exploring different types of pallet inverters is essential to identify the most suitable technology for their specific requirements.