The effective packaging of coiled products like paper rolls, hoses, and cables is crucial for protection against environmental factors and handling damage during storage and transit. Orbital wrapping machines offer an automated, efficient solution for applying stretch film securely around the circumference of these items. This article provides a technical overview of a typical orbital coil wrapping machine, similar to the one demonstrated in the video, focusing on its design, components, specifications, and operational benefits, adhering to the detailed analysis expected by Machine Design readers.
1. Operational Principle and Design Engineering
Orbital wrapping machines utilize a unique mechanism where a rotating ring carries the stretch film roll. This ring passes through the inner diameter (ID) of the coil while the coil itself is supported, often on driven rollers.
- Wrapping Cycle: The film dispensing unit, mounted on the rotating ring, orbits around and through the coil. Simultaneously, the support rollers may rotate the coil itself (depending on the specific machine configuration and product), ensuring complete 360-degree coverage of the coil's surface with overlapping layers of stretch film.
- Structural Design: The machine frame is typically constructed from welded steel for rigidity and durability, designed to withstand the dynamic forces of the rotating ring and support the weight of the coils. Key design considerations include minimizing vibration, ensuring precise alignment of the ring and rollers, and providing easy access for maintenance.
2. Key Component Breakdown
Understanding the core components is essential for appreciating the machine's functionality and performance:
- Rotating Ring Assembly: The heart of the machine, this component carries the film carriage and rotates at controlled speeds. Its diameter dictates the maximum coil OD the machine can handle.
- Film Carriage and Pre-Stretch Unit: This assembly holds the stretch film roll. Crucially, it incorporates a pre-stretch system. The referenced machine features up to 200% pre-stretch, meaning 1 meter of film is stretched to 3 meters as it's applied. This significantly reduces film consumption and increases load holding force. Pre-stretch mechanisms typically involve powered rollers running at different speeds.
- Coil Support System: Usually consists of powered or non-powered rollers (V-rollers or flat rollers) that support the coil's weight and may assist in rotating it during the wrapping cycle. The configuration depends on the coil's size, weight, and shape.
- Control System (PLC): A Programmable Logic Controller manages the machine's operations, including ring speed, roller speed (if applicable), number of wraps, film tension, and cycle start/stop. An HMI (Human Machine Interface) panel typically allows operators to set parameters and monitor status.
- Safety Features: Essential components include emergency stop buttons, safety interlocks on access doors or light curtains around the wrapping zone to protect operators.
3. Technical Specifications Overview
While specifications vary between models, a typical orbital wrapper for smaller coils like paper rolls, hoses, or cables might feature:
- Coil Outer Diameter (OD): 300mm - 1200mm
- Coil Inner Diameter (ID): >150mm (must allow ring passage)
- Coil Width/Height: 50mm - 500mm
- Maximum Coil Weight: 50kg - 200kg
- Wrapping Material: LLDPE Stretch Film (typically 50-100mm width)
- Film Pre-Stretch Ratio: Up to 200% (variable, electronically controlled)
- Ring Rotation Speed: 60 - 150 RPM (variable)
- Packing Efficiency: Dependent on coil size and wraps, e.g., 30-60 coils/hour
- Power Supply: 380V/50Hz/3Ph (or per regional standard)
- Control System: PLC with HMI Touch Screen
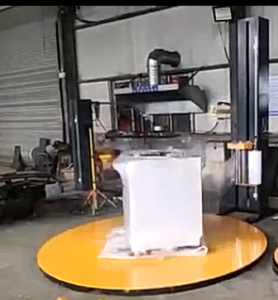
4. Application Focus: Wrapping Paper Rolls and Similar Coils
The embedded video demonstrates the machine effectively wrapping a paper roll, showcasing its suitability for protecting sensitive materials from dust, moisture, and scuffing.
The orbital wrapping method ensures complete coverage without gaps, crucial for maintaining product integrity. This type of coil wrapping machine is particularly well-suited for:
- Paper Rolls
- Hose Coils
- Wire and Cable Coils
- Small Tire Bundles
- Other ring-shaped or cylindrical products within its size/weight limits.
5. Performance Comparison: Orbital Wrapping vs. Manual Methods
Automated orbital wrapping offers significant advantages over manual stretch wrapping or other packaging methods:
- Speed & Throughput: Significantly faster than manual wrapping, increasing production line efficiency.
- Consistency: Ensures uniform film application and tension for every coil, improving package integrity and predictability.
- Material Savings: The pre-stretch function drastically reduces film consumption compared to manual wrapping (which typically achieves little to no pre-stretch). A 200% pre-stretch can cut film usage by 50-65%.
- Labor Reduction: Automates the wrapping process, freeing up personnel for other tasks and reducing labor costs.
- Improved Protection: Tightly applied stretch film provides better protection against environmental contaminants and handling damage.
- Load Security: Consistent tension and proper layering enhance the stability of the coiled product.
6. User Experience and Operational Considerations
From an operational standpoint, these machines are designed for industrial environments:
- Ease of Use: Modern machines feature intuitive HMI panels for setting parameters like wrap counts, tension, and overlap.
- Film Loading: Film carriages are typically designed for relatively quick and straightforward roll changes.
- Maintenance: Requires routine checks on rollers, bearings, drive belts/chains, and the film pre-stretch mechanism. Access points are usually integrated into the design.
- Integration: Can often be integrated into automated production lines with infeed and outfeed conveyors.
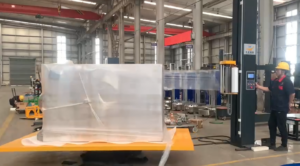
Conclusion
Orbital coil wrapping machines represent a significant advancement in packaging technology for coiled products. By utilizing a rotating ring mechanism and incorporating features like high pre-stretch film systems, they deliver enhanced efficiency, superior product protection, significant material savings, and reduced labor requirements compared to manual methods. The machine shown effectively packaging paper rolls highlights its capability for handling delicate materials, making it a valuable asset in industries dealing with hoses, cables, wires, and similar coiled goods.
Explore more packaging solutions on our https://www.fhopepack.com/