In today's precision-driven manufacturing landscape, the journey of a bearing doesn't end upon production. Ensuring its integrity until the point of installation is paramount. This introductory video showcases a bearing packing and wrapping machine designed to provide robust protection for these critical components. Proper packaging is not merely about aesthetics; it's a crucial step in maintaining performance, preventing corrosion, and avoiding costly damage during transit and storage. This article delves into the technical specifications, operational benefits, and strategic importance of utilizing advanced bearing wrapping solutions.
1. The Imperative of Specialized Bearing Protection
Bearings are highly sensitive components susceptible to various forms of damage:
- Corrosion: Exposure to moisture and contaminants can initiate rust and corrosion, severely compromising bearing surfaces and lifespan.
- Physical Damage: Impacts, vibrations, and improper handling during shipping can lead to dents, scratches, or brinelling.
- Contamination: Dust, dirt, and other particulates can infiltrate bearing internals, leading to premature wear and failure upon installation.
Effective packing, often utilizing materials like VCI (Volatile Corrosion Inhibitor) paper or barrier films, directly addresses these risks, ensuring the bearing arrives in pristine, ready-to-use condition.
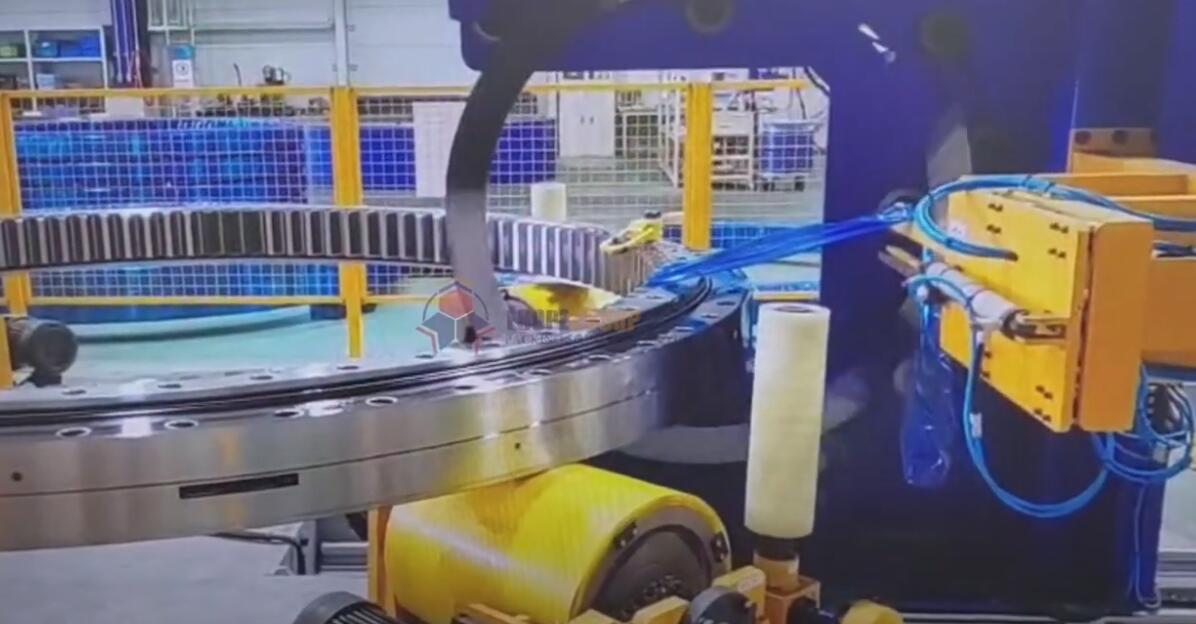
2. Anatomy of the Bearing Packing & Wrapping Machine
This type of machinery automates the application of protective materials around the bearing's circumference. The core principle involves securely wrapping the bearing, typically through the eye (bore), creating a tight, conformal layer of protection.
3. Technical Deep Dive: Design, Structure, and Components
Understanding the machine's construction reveals its capabilities:
- Frame and Structure: Built with robust steel for stability and longevity in industrial environments. Designed for minimal vibration during operation.
- Ring Wrapping Unit: The heart of the machine. A rotating ring holds the packing material dispenser (e.g., VCI paper roll, stretch film roll). As the bearing is positioned, the ring rotates, wrapping the material through the bearing's inner diameter and around the outer diameter.
- Material Feed & Tensioning System: Precisely controls the dispensing and tension of the packing material, ensuring a snug fit without damaging the bearing or wasting material. Often includes adjustable rollers and dancers.
- Conveyor/Feeding System (Optional): In automated lines, conveyors position the bearing correctly within the wrapping station and move it to the next stage. Manual loading is common for semi-automatic models.
- Control Panel (PLC): Typically features a user-friendly interface (HMI) for setting parameters like wrapping speed, overlap percentage, number of wraps, and cutting cycles. PLC (Programmable Logic Controller) ensures reliable and repeatable operation.
- Cutting Mechanism: Automatically cuts the packing material once the wrapping cycle is complete.
- Safety Features: Interlocked guards, emergency stop buttons, and sensors protect operators during operation.
4. Key Performance Specifications at a Glance
While specific models vary, typical technical parameters include:
Specification | Typical Range/Value | Significance |
---|---|---|
Bearing OD Range | 50mm - 1500mm+ | Determines the machine's size handling capability |
Bearing ID Range | 20mm - 1200mm+ | Affects the ring size and wrapping mechanism design |
Bearing Width Range | 10mm - 500mm+ | Influences material width and wrapping cycle |
Wrapping Speed | 10 - 60 seconds/piece (Adjustable) | Directly impacts throughput and line efficiency |
Packing Material | VCI Paper, PE Film, PP Woven Belt, Crepe Paper | Versatility to meet different protection needs |
Material Roll Width | 50mm - 200mm | Must match bearing size and protection strategy |
Material Roll OD | Up to 500mm | Determines how often material needs reloading |
Control System | PLC + HMI | Ensures precision, repeatability, ease of use |
Power Supply | 380V/50Hz/3Phase (or customized) | Standard industrial power requirements |
Air Supply | 0.5 - 0.7 MPa (if pneumatic components used) | For actuation of cutters, clamps etc. |
Note: These are representative values. Always refer to specific manufacturer datasheets for accurate information.
5. Material Versatility: Tailoring Protection
The ability to use different packing materials is a key advantage:
- VCI Paper/Film: Releases corrosion-inhibiting vapors within the package, actively protecting metal surfaces from rust. Ideal for long-term storage or shipping in humid environments.
- PE Stretch Film: Provides a moisture barrier, secures the bearing, and offers good puncture resistance. Cost-effective for general protection.
- PP Woven Belt: Offers high tensile strength for securing larger, heavier bearings or bundling multiple units.
- Crepe Paper: Provides cushioning and absorption, often used in conjunction with VCI or film.
The machine allows for easy switching between material types based on the specific bearing and its destination requirements.
6. Operational Workflow and User Experience
From an operator's perspective, the process is streamlined:
- Load Bearing: Place the bearing onto the designated support rollers or conveyor.
- Initiate Cycle: Start the wrapping process via the control panel.
- Automatic Wrapping: The ring rotates, feeding and wrapping the material through the bearing's eye. The machine controls overlap and tension. Some designs wrap simultaneously from two feed points ("two band feeding") for faster cycles.
- Automatic Cutting & Sealing: The material is cut, and often sealed (e.g., heat seal for film).
- Unload Bearing: Remove the securely wrapped bearing.
Personal User Experience Insights: Operators value machines with intuitive HMIs, quick material roll changeovers, and easily adjustable settings (like wrapping speed). Reliability and minimal downtime for maintenance are crucial in production settings. The automation significantly reduces manual labor and ensures consistent packaging quality compared to hand-wrapping.
7. Advantages in Modern Manufacturing & Logistics
Investing in a dedicated bearing packing machine yields significant benefits:
- Enhanced Product Protection: Minimizes damage and corrosion, reducing scrap rates and warranty claims.
- Increased Efficiency: Automates a labor-intensive process, boosting throughput.
- Consistent Quality: Ensures every bearing is packed to the same standard.
- Material Optimization: Precise control reduces material waste compared to manual methods.
- Improved Safety: Reduces manual handling risks associated with large or heavy bearings.
- Professional Presentation: Neatly wrapped bearings enhance brand perception.
8. Choosing the Right Bearing Wrapping Solution
Selecting the appropriate machine depends on factors like:
- The range of bearing sizes and weights you handle.
- Required throughput (pieces per hour).
- Desired level of automation (semi-auto vs. fully auto).
- Types of packing materials needed.
- Budget and available floor space.
Explore various bearing packing solution options, ranging from semi-automatic machines for lower volumes to fully integrated automatic lines for high-volume production. Consulting with packaging machinery experts, like the FHOPE team, can help identify the optimal configuration for your specific needs.