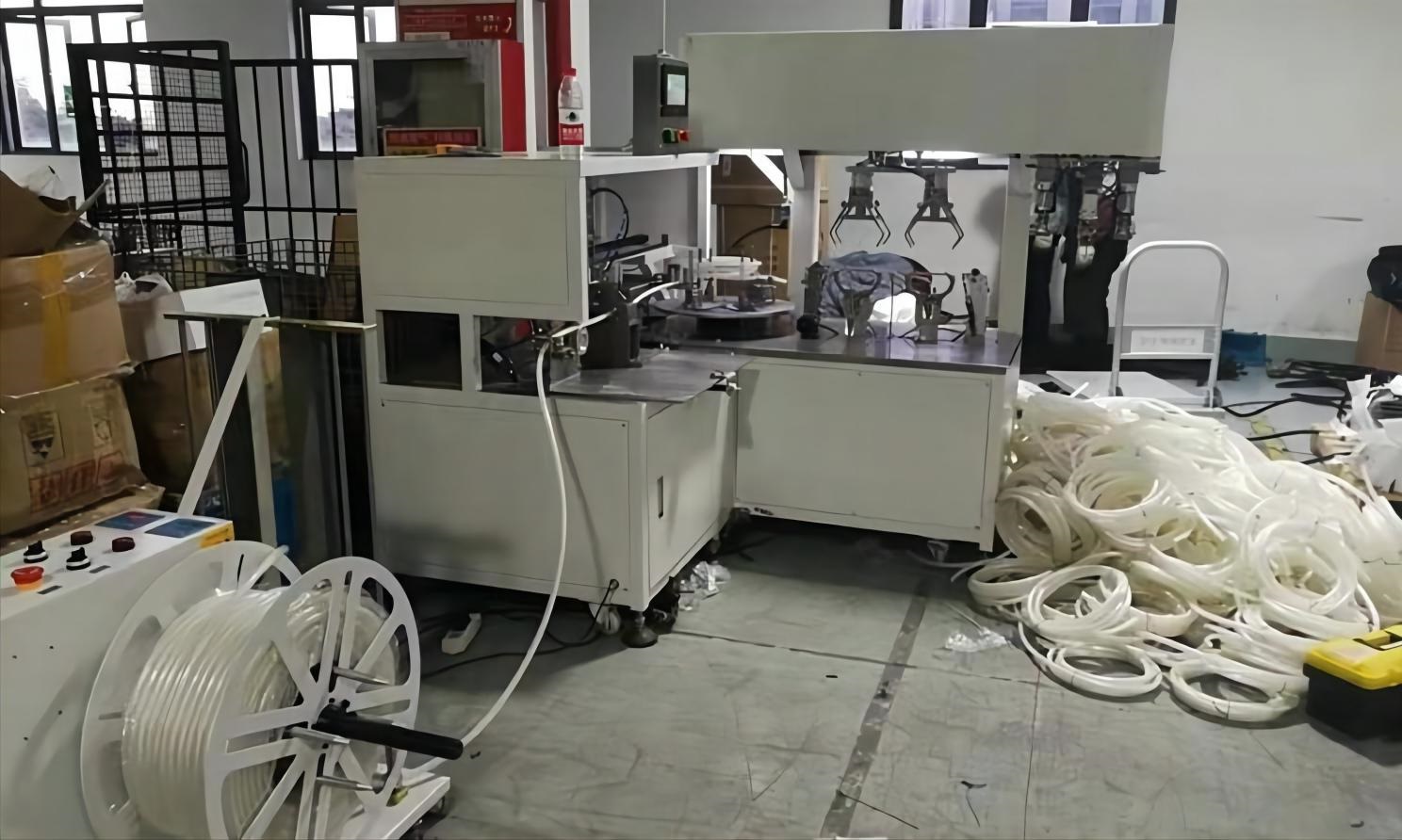
Enhancing Production Efficiency: The Engineering Behind Automated Winding and Binding for Tubes, Cables, and Hoses
The efficient management, storage, and transportation of long, flexible materials such as industrial tubing, electrical cables, and hydraulic hoses present significant logistical challenges. Manual handling is often labor-intensive, prone to inconsistencies, and can lead to product damage or unsafe working conditions. Automated winding and binding machines address these issues directly, offering a robust engineering solution designed to optimize packaging processes. This technology, underpinned by principles often explored in patents related to automated material handling (e.g., those focusing on tension control or coil formation mechanisms), provides quantifiable improvements in throughput, package integrity, and operational safety.
Core Functionality: Precision Winding and Secure Binding
At its heart, this automated system performs two critical functions: precisely coiling materials to specified lengths and diameters, and subsequently securing these coils with appropriate binding materials. It is engineered to handle a diverse range of products, typically accommodating diameters up to 50mm and lengths reaching 10 meters or more, depending on configuration.
The system integrates several key electromechanical subsystems:
- Variable Speed Drive (VSD) System: Powers the rotation of winding cores or reels, allowing for precise control over winding speed adaptable to different material characteristics and coil sizes. Research in motor control algorithms ensures smooth acceleration and deceleration, minimizing stress on the product.
- Material Guidance and Traverse System: Employs rollers, guides, and often a servo-driven traverse mechanism to ensure the tube, cable, or hose is laid onto the core in an orderly manner. This prevents overlapping and ensures a stable, dense coil structure, crucial for efficient storage and downstream processing.
- Tension Control System: Maintaining consistent, optimal tension is paramount during winding. Sophisticated tensioners, potentially utilizing feedback loops from sensors or dancer arms, prevent material stretching, kinking, or slack, preserving product integrity. The physics of material elasticity and friction are key considerations in tension system design, as documented in various engineering papers on web handling and winding.
- Automated Binding Unit: Applies binding materials such as polypropylene (PP) strapping, polyester (PET) strapping, stretch film, or specialized ties. The choice of binding material and application method (e.g., heat sealing, friction welding) depends on factors like coil weight, storage environment, and required tensile strength, drawing on material science principles.
Advanced Control and Operational Parameters
Modern winding and binding machines leverage Programmable Logic Controllers (PLCs) for coordinating the complex sequence of operations. This ensures repeatability and allows for easy adjustment of parameters via a Human-Machine Interface (HMI).
Key adjustable parameters often include:
- Winding Tension: Digitally set and dynamically adjusted.
- Winding Speed: Optimized for material type and desired throughput.
- Coil Length/Diameter: Precise measurement using encoders or sensors ensures specification adherence.
- Traverse Pitch/Winding Pattern: Configurable for level winding or specific patterns like drop-stitch or spiral, impacting coil density and stability.
- Binding Strategy: Number of straps, strap placement, and tension.
Integrated sensors (proximity, optical, limit switches) monitor the process, detect anomalies like material run-out or tangling, and contribute to the overall safety architecture, which typically includes emergency stops and physical guarding compliant with relevant industry safety standards (e.g., ISO 13849).
Technical Specifications Overview
While specific configurations vary, typical performance characteristics include:
- Product Diameter Handling: Up to 50 mm (or as specified)
- Maximum Winding Length: 10 m (or as specified, configurable)
- Winding Core Compatibility: Adaptable to various core sizes or coreless operation.
- Binding Materials: PP Straps, PET Straps, Stretch Film, Ties
- Control System: PLC with Touchscreen HMI
- Power: Typically 3-Phase Industrial Supply (e.g., 380V/50Hz, 480V/60Hz)
- Safety: Integrated E-stops, Interlocked Guarding, Sensor Fault Detection
Benefits and Return on Investment (ROI)
The implementation of automated winding and binding technology yields significant operational advantages, echoing findings in industrial automation research:
- Increased Productivity: Continuous, automated operation significantly outpaces manual methods.
- Enhanced Safety: Reduces manual handling of potentially heavy or unwieldy coils.
- Improved Package Quality: Consistent winding tension and secure binding protect product integrity during transit and storage, reducing damage claims.
- Labor Cost Reduction: Frees up personnel for higher-value tasks.
- Material Optimization: Precise length measurement minimizes waste.
- Space Efficiency: Uniformly wound and bound coils allow for denser, more stable storage.
This machine represents a strategic investment for manufacturers and distributors dealing with bulk quantities of tubes, cables, or hoses. Its rugged, industrial-grade construction ensures durability and reliability in demanding production environments. By automating a critical packaging step, it streamlines the workflow, reduces operational costs, and delivers consistently professional results, ready for efficient storage or economical shipment.
Explore further options for automated hose packaging solutions just here.
For dedicated automatic steel wire winding and packing machinery, see: https://www.fhopepack.com/Automatic-Wire-Winder/