Okay, here is the updated content in Markdown format, incorporating the requested enhancements, technical details, SEO considerations, and formatting, while retaining the original media elements (with the video updated to iframe format and moved).
Handling large, heavy panels like steel sheets, wooden boards, or glass plates in a production environment presents significant challenges, both in terms of operational efficiency and worker safety. Manual rotation and stacking are often slow, labor-intensive, and carry inherent risks of injury and product damage. The automatic panel rotating and stacking machine offers a robust, automated solution to streamline these processes.
1. Understanding the Automatic Panel Rotating and Stacking Machine
This type of equipment is engineered to automatically perform two primary functions: rotating large flat panels, typically by 180 degrees, and then stacking them precisely. It's designed for integration into production lines where panels need to be flipped for processing, inspection, or packaging on both sides. Compared to manual turning, utilizing a dedicated rotating inverter significantly enhances operational safety and throughput.
2. Key Applications and Industries
Automatic panel rotators and stackers find applications across various sectors:
- Metal Fabrication: Flipping steel sheets for inspection, coating, or further processing.
- Woodworking: Handling large wooden boards or panels for sanding, finishing, or assembly.
- Glass Manufacturing: Rotating delicate glass panels safely.
- Building Materials: Managing drywall, composite boards, or other construction panels.
- Automotive & Aerospace: Handling large sheet metal components during manufacturing.
3. Design, Structure, and Key Components
The effectiveness of these machines lies in their robust design and carefully integrated components:
- Heavy-Duty Frame: Constructed typically from welded structural steel to handle significant loads and ensure stability during rotation.
- Rotating Mechanism: Often employs a powerful electromechanical or hydraulic drive system coupled with precision bearings. Secure clamping systems (hydraulic, pneumatic, or mechanical) grip the panel firmly during the 180-degree rotation to prevent slippage or damage.
- Lifting and Positioning System: Integrated lifters (e.g., hydraulic scissor lifts, chain conveyors) position the panel or stack correctly for rotation and stacking.
- Stacking Unit: Features alignment guides and sensors to ensure panels are stacked neatly and accurately. This may include powered conveyors for transferring completed stacks.
- Control System: Governed by a Programmable Logic Controller (PLC) providing reliable AUTOMATION. A Human-Machine Interface (HMI), often a touchscreen panel, allows for easy operation, parameter setting (e.g., panel size, rotation speed), and diagnostics.
- Safety Features: Essential components include safety interlocks, light curtains or area scanners, physical guarding, and emergency stop buttons to protect operators.
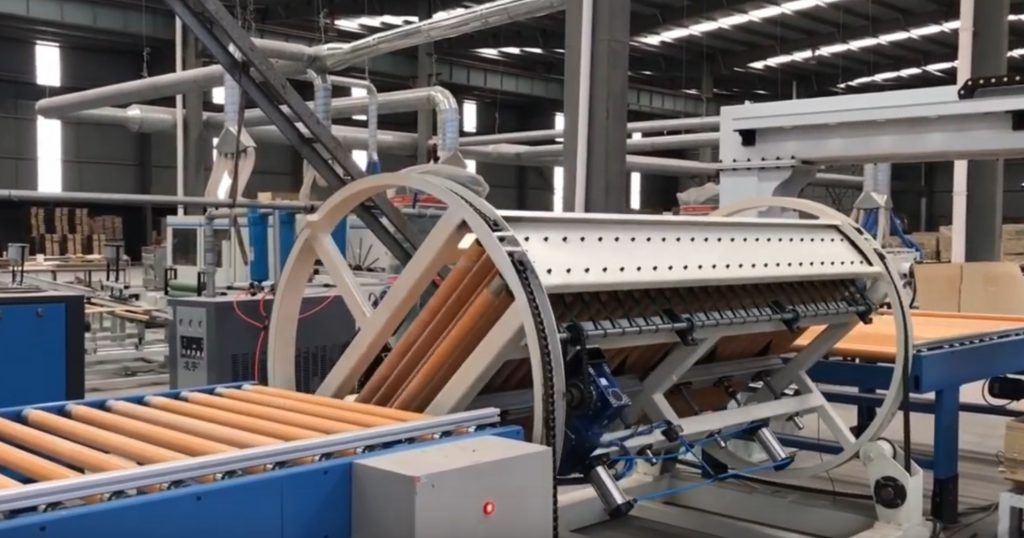
4. Technical Specifications Overview
While specific parameters vary by model and customization, typical technical data includes:
Parameter | Typical Range / Specification | Notes |
---|---|---|
Load Capacity | 1,000 kg - 5,000 kg (2,200 - 11,000 lbs) | Dependent on panel weight and dimensions |
Panel Size (L x W) | Customisable, e.g., up to 6m x 2.5m | Min/Max dimensions accommodated |
Panel Thickness | Customisable, e.g., 5mm - 100mm | Clamping system adjusted accordingly |
Rotation Angle | 180 degrees (standard); 90° optional | Precision controlled rotation |
Cycle Time | 30 - 90 seconds (rotation + handling) | Varies with panel size and machine design |
Stacking Height | Up to 1,500 mm (approx. 60 inches) | Sensor controlled for precise stacking |
Control System | PLC (e.g., Siemens, Allen-Bradley) + HMI | Provides automated control and monitoring |
Power Requirement | 480V/3Ph/60Hz or 380V/3Ph/50Hz | Based on regional standards |
Drive System | Electromechanical or Hydraulic | Choice depends on load and speed needs |
Safety Compliance | CE / OSHA standards | Includes light curtains, E-stops, guarding |
5. Operational Workflow Example
A typical automated sequence involves:
- Infeed: Panel arrives via conveyor or is placed manually/by crane onto the machine's infeed section.
- Lifting & Positioning: The panel is lifted or centered into the rotation position.
- Clamping: Secure clamps engage the panel edges or surface.
- Rotation: The machine rotates the panel 180 degrees.
- Unclamping: Clamps release the panel in its new orientation.
- Lowering/Stacking: The panel is lowered onto a stacking platform or an outfeed conveyor. Sensors detect stack height.
- Discharge (Optional): Completed stack is moved out via conveyor.
- Cycle Repeat: The machine returns to the start position for the next panel.
6. Benefits of Automation in Panel Handling
Investing in an automatic panel rotating and stacking machine yields significant advantages:
- Vastly Improved Safety: Eliminates dangerous manual lifting and flipping, drastically reducing the risk of musculoskeletal injuries and accidents.
- Increased Productivity: Faster cycle times compared to manual methods lead to higher throughput.
- Consistent Quality: Automated handling minimizes scratches, dents, or other damage often associated with manual handling.
- Reduced Labor Costs: Frees up personnel for less strenuous, higher-value tasks.
- Optimized Workflow: Creates a smoother, more predictable production flow.
- Space Efficiency: Can be designed to integrate compactly within existing line layouts.
7. Personal Experience and Selection Considerations
From experience, integrating such machinery requires careful planning. Key factors to consider when selecting or implementing a system include:
- Panel Characteristics: Accurately define the range of panel sizes, weights, materials, and surface sensitivity the machine must handle.
- Throughput Requirements: Match the machine's cycle time to your production line speed.
- Integration: How will the machine interface with upstream and downstream equipment (conveyors, processing stations)? Consider communication protocols.
- Footprint and Layout: Ensure sufficient space and proper positioning within your facility.
- Maintenance Access: Look for designs that allow easy access for routine maintenance and repairs.
- Vendor Support: Evaluate the manufacturer's technical support, training, and spare parts availability.
- Return on Investment (ROI): Calculate the payback period based on savings in labor, improved efficiency, reduced damage, and enhanced safety.
8. Conclusion
Automatic panel rotating and stacking machines are essential technology for modern manufacturing facilities dealing with large panels. By automating this critical handling step, companies can achieve substantial improvements in safety, efficiency, product quality, and overall operational consistency. As demonstrated in the video, these systems provide a reliable and robust solution for demanding industrial environments.