Optimizing Load Stability: A Technical Deep Dive into Semi-Automatic Stretch Wrappers with Top Press Fixtures
Stretch wrapping remains a cornerstone of modern logistics and warehousing, ensuring load stability and protection during transit and storage. While fully automatic systems offer maximum throughput, semi-automatic stretch wrappers provide a cost-effective and efficient solution for many operations. This article delves into the technical aspects, design features, and operational benefits of semi-automatic stretch wrapping machines, with a specific focus on models equipped with top press fixtures – crucial for handling challenging loads.
Let's observe a typical semi-automatic stretch wrapper with a top press fixture in action:
1. Core Functionality: Semi-Automatic Stretch Wrapping
Semi-automatic stretch wrappers bridge the gap between manual wrapping and fully automated lines. The core process involves:
- Load Placement: An operator places the palletized load onto the machine's turntable using a forklift or pallet jack.
- Film Attachment: The operator manually attaches the stretch film tail to the load.
- Cycle Initiation: The operator starts the pre-programmed wrapping cycle via the control panel.
- Automated Wrapping: The machine automatically rotates the load (turntable models) or moves a wrapping arm around the load, while a film carriage dispenses stretch film, typically moving vertically along a mast to cover the entire load height.
- Film Cut & Finalization: Once the cycle completes, the operator manually cuts the film tail and secures it to the load.
These machines are widely utilized in manufacturing facilities, distribution centers, and warehouses where packaging throughput requirements are moderate, but efficiency, consistency, and load security are paramount.
2. Critical Components and Design Considerations
Understanding the key components is essential for selecting the right machine:
-
Turntable:
- Construction: Typically heavy-duty steel for durability.
- Diameter: Standard sizes range from 1500mm (59") to 1800mm (71"), dictating maximum load footprint. Custom sizes are available.
- Capacity: Standard weight capacities often range from 1500kg (3300 lbs) to 2500kg (5500 lbs).
- Drive System: Chain-driven with variable speed control (e.g., 3-12 RPM) allows optimization for different load types. Soft start/stop features prevent load shifting.
-
Film Carriage System:
- Pre-Stretch: This is crucial for film economy and load containment force. Powered pre-stretch systems (PPS) electronically control film elongation, typically offering ratios from 150% up to 300% (meaning 1 meter of film is stretched to 2.5 - 4 meters). Mechanical pre-stretch offers lower, often fixed ratios.
- Film Delivery: Ensures consistent tension and smooth application. Look for easy film threading designs.
-
Mast/Tower:
- Height: Determines the maximum wrapping height, usually ranging from 2000mm (78") to 3000mm (118") or more.
- Structure: Robust construction prevents flexing during operation.
-
Control System:
- Interface: Options range from simple button controls to sophisticated PLC (Programmable Logic Controller) systems with touchscreens.
- Programmability: Allows customization of wrap patterns (e.g., number of top/bottom wraps, carriage ascent/descent speed, turntable speed, film tension). Multiple saved programs are beneficial for varied load types.
-
Top Press Fixture (Pneumatic/Electric):
- Function: A pneumatically or electrically actuated plate that descends onto the top of the load before the wrapping cycle begins.
- Purpose: Essential for stabilizing lightweight, tall, or unstable loads (e.g., stacks of empty boxes, light containers, irregularly shaped items) preventing them from shifting or toppling during the turntable's rotation.
- Control: Pressure/force is typically adjustable to suit different load sensitivities. The stroke distance must accommodate varying load heights.
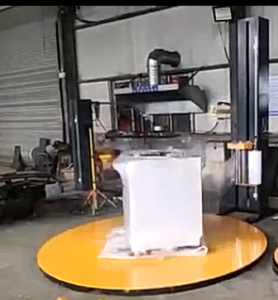
3. Technical Specifications & Performance Metrics Comparison
When evaluating machines, compare key technical data. Below is a representative comparison:
Parameter | Typical Standard Semi-Auto Wrapper | Fhopepack Model (Illustrative Example) | Unit | Notes |
---|---|---|---|---|
Max Load Size (L x W) | 1200 x 1200 | 1300 x 1300 | mm | Larger platforms available |
Max Wrapping Height | 2100 | 2400 | mm | Extended mast options exist |
Max Load Weight | 2000 | 2000 | kg | Higher capacity options available |
Turntable Diameter | 1650 | 1650 | mm | Common size, fits standard pallets |
Turntable Speed | 3 - 12 | 3 - 12 | RPM | Variable speed control is standard |
Film Pre-Stretch Ratio | Up to 250% | Up to 300% | % | Higher ratio means more film savings |
Top Press | Optional | Standard / Optional | - | Specify if needed; check pressure/stroke range |
Wrapping Efficiency | 15 - 30 | 20 - 35 | Pallets/Hour | Operator dependent; cycle time influences this |
Power Supply | 220V/1Ph/50-60Hz | 220V/1Ph/50-60Hz (or custom) | V/Ph/Hz | Check local requirements |
Control System | PLC | PLC with Touchscreen | - | User interface preference |
Note: Specific data varies greatly between models and manufacturers. Always refer to official specification sheets.
4. Operational Benefits and ROI
Investing in a semi-automatic wrapper, especially one with a top press, yields tangible benefits:
- Enhanced Load Security: Consistent wrap patterns and tension, combined with top press stabilization, significantly reduce product damage during handling and shipping.
- Increased Efficiency: Dramatically faster than manual wrapping, freeing up labor for other tasks. Expect wrapping times of 60-90 seconds per pallet depending on the cycle.
- Material Cost Savings: Powered pre-stretch systems can reduce film consumption by 50-75% compared to manual wrapping, leading to significant cost savings.
- Improved Ergonomics & Safety: Reduces physical strain and repetitive motion injuries associated with manual wrapping.
- Professional Package Appearance: Consistent wrapping provides a more professional look for outgoing shipments.
- Return on Investment (ROI): Calculated based on labor savings, film cost reduction, and decreased product damage costs. Payback periods can often be less than a year for operations wrapping a moderate volume of pallets.
5. User Experience and Practical Considerations
- Ease of Use: Modern machines with intuitive controls require minimal training. Pre-set programs simplify operation for different load types.
- Maintenance: Requires regular checks (film carriage rollers, turntable drive chain tension, sensor cleaning) and periodic lubrication as per the manufacturer's guidelines. Pneumatic systems require clean, dry air.
- Flexibility: Easily handles various load sizes and shapes within its specifications. Options like loading ramps (for pallet jack access) or integrated weigh scales add further functionality.
- Top Press Necessity: Indispensable when dealing with:
- Multiple layers of lightweight boxes.
- Tall, narrow loads prone to instability.
- Loads that cannot withstand high initial rotational force without stabilization.
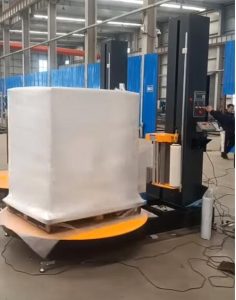
6. Fhopepack: Tailored Stretch Wrapping Solutions
Fhopepack emerges as a notable manufacturer offering robust semi-automatic carton and pallet wrapping machines, often at competitive price points. Key advantages include:
- User-Friendly Design: Their machines prioritize ease of operation and high operational efficiency.
- Customization: Fhopepack specializes in adapting machines to specific customer requirements, whether it involves non-standard load dimensions, specific control features, or integration needs like conveyors or specialized fixtures like the top press.
- Reliability: Built for industrial environments, focusing on durability and consistent performance.
By offering customization, Fhopepack ensures that businesses acquire a wrapping solution precisely matched to their unique packaging challenges, maximizing the benefits discussed above.
For more details on their range of stretch wrapping equipment, visit:
https://www.fhopepack.com/Stretch_wrapping_machine.html
Conclusion
Semi-automatic stretch wrapping machines represent a significant upgrade from manual methods, boosting efficiency, safety, and load integrity. The addition of a top press fixture extends these benefits to unstable or lightweight loads, ensuring they are wrapped securely without risk of toppling. By carefully considering technical specifications, component design, and features like the top press, businesses can select a machine that optimizes their packaging operations, reduces costs, and protects their products throughout the supply chain.