Optimizing Hose Handling: The Role of Automated Rubber Tube Coiling and Banding Machines
Manual handling of rubber tubes and hoses in manufacturing and fabrication environments can be labor-intensive, pose safety risks, and lead to inconsistencies in product packaging. Automating the coiling and banding process offers a significant improvement, enhancing efficiency, safety, and product quality. This article explores the functionalities and benefits of automated rubber tube coiling and banding systems.
Why Automate Rubber Tube Coiling and Banding?
Transitioning from manual to automated processes provides several key advantages for fabricators and manufacturers:
Enhanced Worker Safety
Manual coiling of heavy or lengthy tubes can lead to musculoskeletal injuries from repetitive strain, awkward postures, and heavy lifting. Sharp edges or pinch points during manual banding also present hazards. Automation removes operators from these high-risk tasks, significantly reducing the potential for workplace injuries, associated costs, and downtime. Implementing automated systems aligns with modern ergonomic principles in manufacturing (external authoritative link example).
Improved Operational Efficiency
Automated coiling and banding machines operate continuously at high speeds, dramatically increasing throughput compared to manual methods. Consistent cycle times lead to predictable output and better production planning. This allows skilled labor to be reassigned to more complex, value-added tasks within the facility.
Ensuring Consistent Coil Quality
Automation guarantees uniformity in coil diameter, winding tightness, and overall appearance. Precise control systems prevent damage such as kinks, creases, or excessive flattening that can occur with inconsistent manual handling. Properly formed and secured coils improve product presentation and ensure integrity during storage and transit.
Optimizing Material Usage
Automated systems are designed for precision. They apply the optimal amount of tension during coiling and use precisely measured lengths of banding material, minimizing waste. This leads to direct cost savings on strapping materials and reduces scrap generated from improperly coiled tubes, contributing to more sustainable operations.
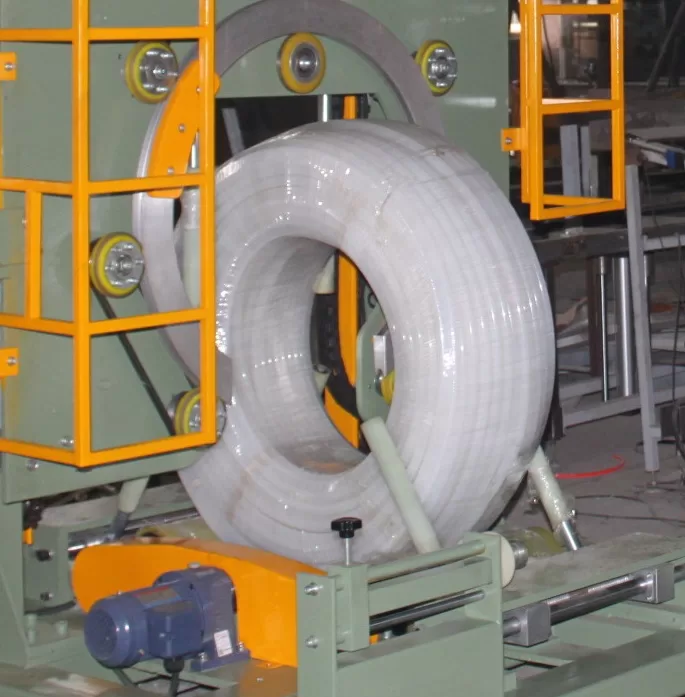
Key Features and Considerations for Automated Systems
When evaluating automated tube coiling and banding solutions, several features are crucial for performance and reliability:
Precise Tension Control Mechanisms
Maintaining the correct tension throughout the coiling process is critical. Insufficient tension leads to loose, unstable coils, while excessive tension can damage the tube or deform the coil shape. Advanced systems often utilize servo motors or other feedback mechanisms to dynamically adjust tension, accommodating variations in tube materials and dimensions.
Robust Banding and Securing
The banding unit must apply strapping material securely without damaging the product. Systems should offer adjustable tension for the banding process and ensure a reliable seal or joint (e.g., heat seal, friction weld for plastic straps). The goal is a tightly bundled coil that remains stable during handling, stacking, and shipping.
Durable Construction for Industrial Environments
These machines operate in demanding industrial settings and must be built to last. Look for heavy-duty frame construction, high-quality components (motors, bearings, sensors), and guarding that meets relevant safety standards. Reliability and minimal downtime are paramount for maintaining production schedules.
Footprint and Integration
While offering high capacity, modern machines often feature a relatively compact footprint to conserve valuable floor space. Consider how the machine will integrate into the existing production flow – options may include standalone units or systems designed for in-line automation with extruders or other processing equipment.
Control Systems and Ease of Use
Modern coiling and banding machines typically feature Programmable Logic Controllers (PLCs) and Human-Machine Interfaces (HMIs). These provide user-friendly controls for setting parameters (coil size, banding locations, tension), monitoring operation, and performing diagnostics, simplifying operation and maintenance.
Applications in Fabrication and Manufacturing
Automated rubber tube coiling and banding machines are essential in various sectors, including:
- Automotive hose manufacturing
- Industrial hydraulic and pneumatic hose production
- Garden hose and irrigation tubing manufacturing
- Medical tubing production
- Any facility requiring efficient processing and packaging of flexible tubes or hoses.
pipe coil wrap machine2 Conclusion
Automated rubber tube coiling and banding machines represent a valuable investment for manufacturers seeking to improve safety, efficiency, and consistency in their hose handling operations. By eliminating manual labor risks, increasing throughput, ensuring uniform coil quality, and optimizing material usage, these systems contribute directly to a more productive, safer, and cost-effective production environment. Careful consideration of features like tension control, durable construction, and integration capabilities will ensure the selected system meets specific operational needs.