Understanding Mold Flipper Tables for Safe and Efficient Handling
Handling large, heavy molds and dies is a critical task in industries like plastic injection molding, die casting, and stamping. A mold flipper, also known as a mold upender or mold tipper, is specialized industrial equipment designed to safely and efficiently rotate these heavy tools, often between horizontal and vertical orientations for maintenance, inspection, or setup. This process minimizes manual handling risks and improves operational workflow.
The video above shows a mold flipper table undergoing testing before delivery, demonstrating its basic operation.
Key Benefits of Using a Mold Flipper
Integrating a mold flipper into your operations offers several significant advantages:
- Enhanced Safety: Dramatically reduces the risk of injuries associated with manually flipping or maneuvering heavy, awkward molds. This eliminates potential crushing hazards and strains.
- Increased Efficiency: Automating the flipping process significantly speeds up mold changeovers, maintenance tasks, and inspections compared to using cranes or manual methods.
- Preventing Damage: Provides controlled, smooth rotation, minimizing the risk of dropping or damaging expensive molds and dies.
- Improved Ergonomics: Reduces physical strain on operators, contributing to a healthier and more productive workforce.
mold flipper table manufacturer2 How Mold Flipper Tables Operate: Key Components
While designs vary, most mold flippers share common operational principles and components:
- Main Support Structure/Table: Provides a robust, stable base, often constructed from heavy-duty steel, designed to support the mold's weight during the entire rotation cycle. Tables can be stationary or mobile (with casters).
- Tilting Mechanism: This is the core of the machine. It typically uses powerful hydraulic cylinders to provide controlled tilting motion (often 90 degrees, but sometimes 180 degrees). Alternatives include electric motor drives with gearbox reducers or pneumatic systems for lighter loads.
- Mold Clamping/Support: Features designed to securely hold the mold or die onto the table during rotation. This might involve fixed stops, adjustable clamps, or specialized fixtures depending on the mold type.
- Control System: Operator controls range from simple push-button pendants or foot switches to more sophisticated PLC (Programmable Logic Controller) based systems with touchscreens for automated sequences or variable speed control.
- Drive System: The power source for the tilting mechanism – typically a hydraulic power unit (HPU) for hydraulic models, compressed air for pneumatic types, or electric motors and drives for electromechanical versions.
- Optional Features: Depending on the application, features like integrated conveyors, cushioned landing pads (airbags or bumpers), specific rotation angles, and custom guarding may be included.
Design Variations and Customization
Mold flippers are not one-size-fits-all. Key considerations for selection and design include:
- Load Capacity: Matching the machine's capacity to the maximum weight of the molds being handled.
- Mold Dimensions: Ensuring the table size and clamping mechanisms can accommodate the length, width, and height of the molds.
- Rotation Angle: Standard is 90 degrees, but 180-degree flippers are also common for complete inversion.
- Operating Environment: Considerations for space constraints, power availability (hydraulic, electric, pneumatic), and integration with other equipment.
Different mold flipper designs cater to these varied needs. For specific details on hydraulic mold flipper configurations and handling specifications, refer to manufacturer information or technical documentation:
https://www.fhopepack.com/Hydraulic/Mold-flipper.html
Essential Safety Features
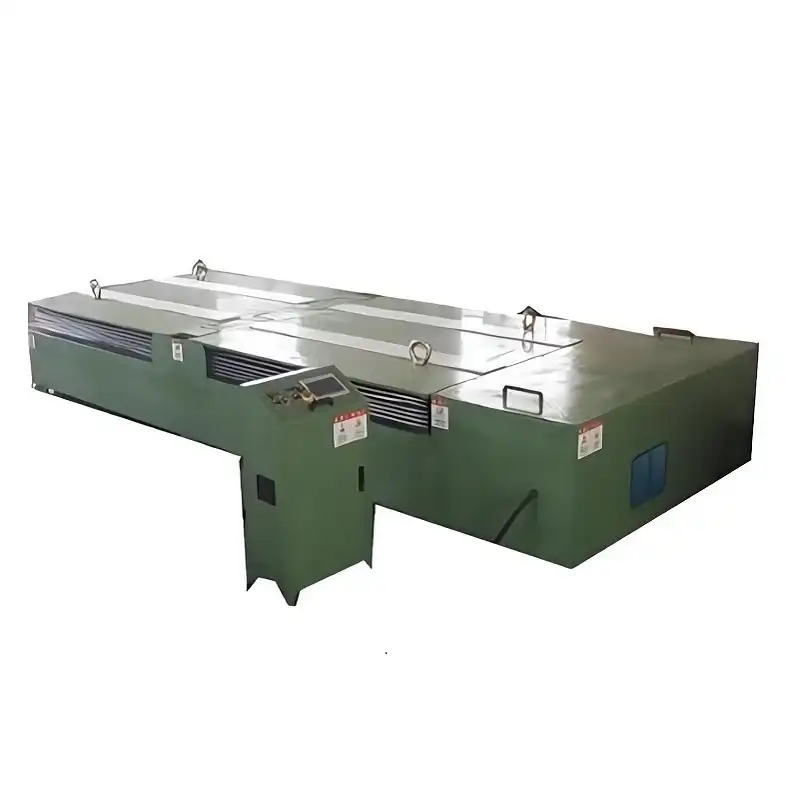
Safety is paramount when dealing with heavy rotating equipment. Common safety features include:
- Limit Switches: To control the start and end points of the rotation, preventing over-travel.
- Physical Guards/Barriers: Fencing or light curtains to prevent personnel from entering the operating zone during rotation.
- Emergency Stops (E-stops): Prominently placed buttons to immediately halt all motion in an emergency.
- Two-Hand Controls: Requiring the operator to use both hands to initiate rotation, ensuring they are clear of moving parts.
- Overload Protection: Systems (e.g., hydraulic pressure relief valves) to prevent the machine from attempting to lift loads beyond its rated capacity.
- Stable Base: Ensuring the machine is properly anchored or has a sufficiently wide base to remain stable during operation.
Common Applications
Mold flipper tables are essential in various manufacturing and maintenance settings:
- Mold Maintenance and Repair: Allowing easy access to all sides of a mold for cleaning, repair, or component replacement.
- Mold Setting and Removal: Facilitating the correct orientation of molds for installation into or removal from injection molding machines or presses.
- Inspection Processes: Enabling thorough visual or NDT inspection of all mold surfaces.
- Die Handling: Used similarly for large stamping dies or die-casting dies.
Conclusion
In conclusion, mold flipper tables (or mold upenders/tippers) are indispensable tools in modern manufacturing environments where heavy molds and dies are handled. By automating the rotation process, they significantly enhance operational safety, reduce the risk of damage to valuable tooling, and improve overall workflow efficiency. Selecting the right type and size of mold flipper, equipped with appropriate safety features, is crucial for optimizing production and maintenance processes involving large molds.