A Comprehensive Guide to Injection Mold Flippers: Enhancing Safety and Efficiency
Handling heavy and cumbersome injection molds is a critical task in manufacturing operations. Improper handling can lead to safety hazards, mold damage, and operational inefficiencies. An injection mold flipper, also known as a mold upender or tilter, is specialized equipment designed to safely and efficiently rotate these molds for maintenance, repair, or setup. This guide provides an in-depth look at injection mold flippers, their benefits, types, and key selection criteria.
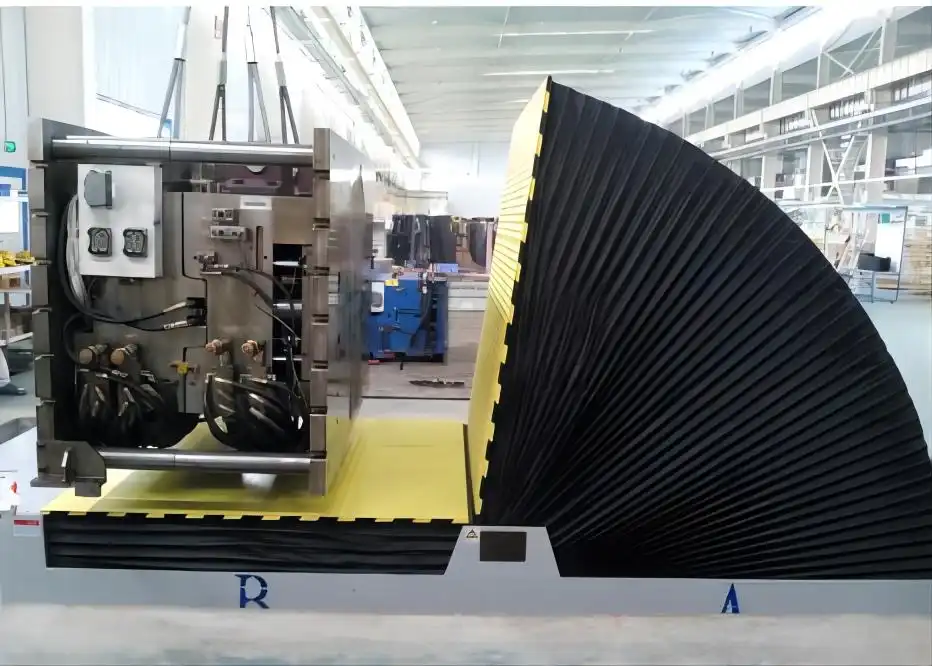
1. What is an Injection Mold Flipper?
An Injection Mold Flipper is robust mechanical or hydraulic equipment specifically engineered to grip and rotate heavy injection molds, typically by 90 or 180 degrees. Its primary purpose is to provide safe and easy access to different sides of the mold for essential tasks such as:
- Maintenance and Cleaning: Allowing technicians to reach internal components and cavities without manual strain or awkward positioning.
- Repair: Facilitating access for welding, polishing, or component replacement.
- Mold Setup and Changeover: Enabling efficient positioning and alignment during production changes.
By automating or assisting the rotation process, these machines mitigate the risks associated with manually handling heavy, unbalanced loads, which often require cranes or forklifts in less controlled maneuvers.
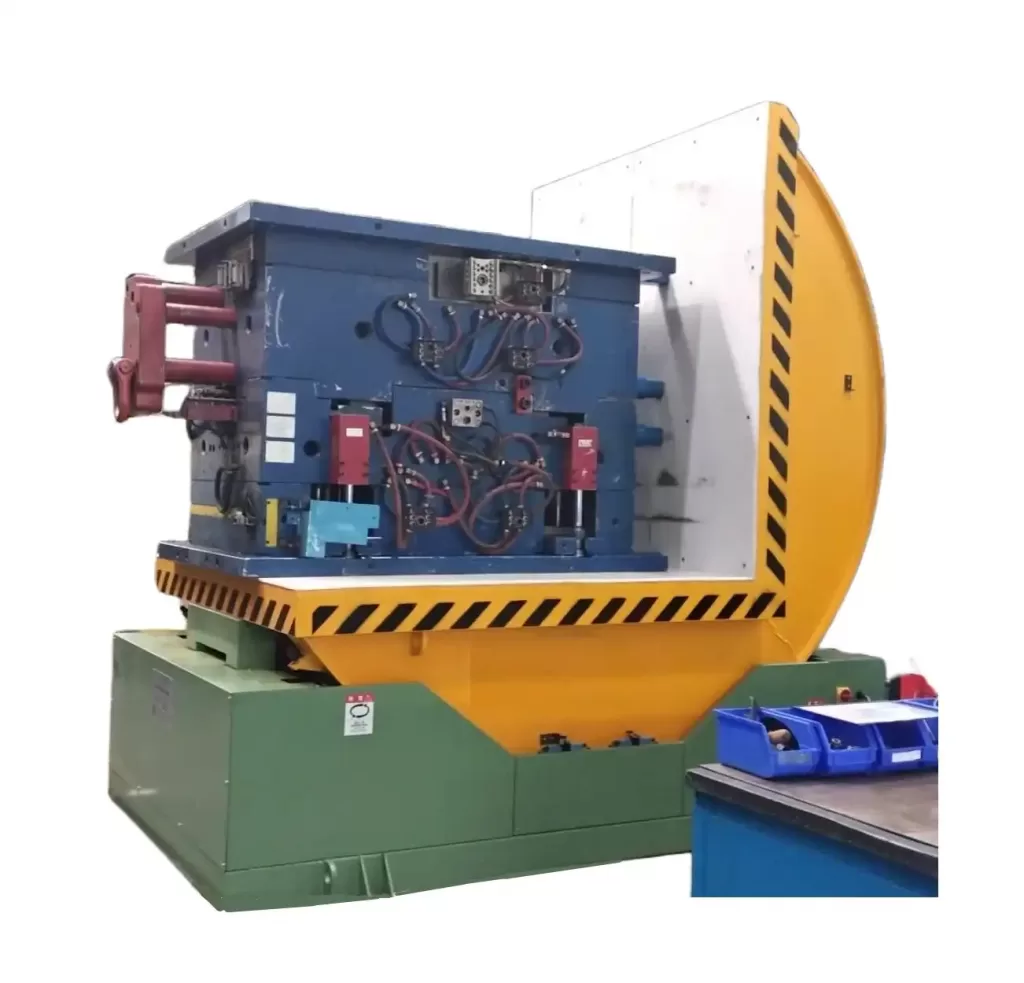
2. Types of Injection Mold Handling Equipment
While often referred to broadly as "flippers," several types of equipment serve this purpose, varying in operation and rotation angle:
- 90-Degree Mold Flipper/Upender: Rotates the mold by 90 degrees, typically from a horizontal to a vertical orientation or vice-versa. This is common for accessing mold halves or parting lines during maintenance.
- 180-Degree Mold Flipper: Rotates the mold a full 180 degrees, allowing access to the opposite side without needing to reposition the mold entirely.
- Mold Flipper Tables: Often feature a flat platform where the mold rests and is rotated. Some designs offer ergonomic height adjustments.
- Actuation Methods:
- Manual Flippers: Require operator effort, suitable for smaller molds or infrequent use.
- Hydraulic Flippers: Use hydraulic power for smooth, controlled rotation of heavy molds. They are the most common type for industrial applications.
- Electric Flippers: Utilize electric motors and gear systems for rotation, offering precise control.
- Chain-Driven Flippers: Employ robust chain mechanisms for rotation, known for durability in demanding environments.
The choice depends on mold size, weight, frequency of use, available power sources, and specific maintenance requirements.
3. How Does an Injection Mold Flipper Work?
Most powered injection mold flippers operate on a similar principle:
- Loading: The mold is placed onto the flipper's platform or table, often using a crane or forklift.
- Securing: Depending on the design, clamps or fixtures may be used to secure the mold, although gravity often suffices on well-designed platforms.
- Rotation: The operator initiates the rotation using a control panel (e.g., push buttons, pendant control). The hydraulic or electric system powers the mechanism (cylinders, motors, chains) to smoothly rotate the platform and mold to the desired angle (90 or 180 degrees).
- Safety Interlocks: Modern mold flippers incorporate safety features like limit switches to prevent over-rotation, emergency stops, and sometimes protective guarding or light curtains to ensure operator safety during operation.
- Access: Once rotated, the mold is held securely in position, allowing technicians safe access for their tasks.
4. Key Benefits of Using an Injection Mold Flipper
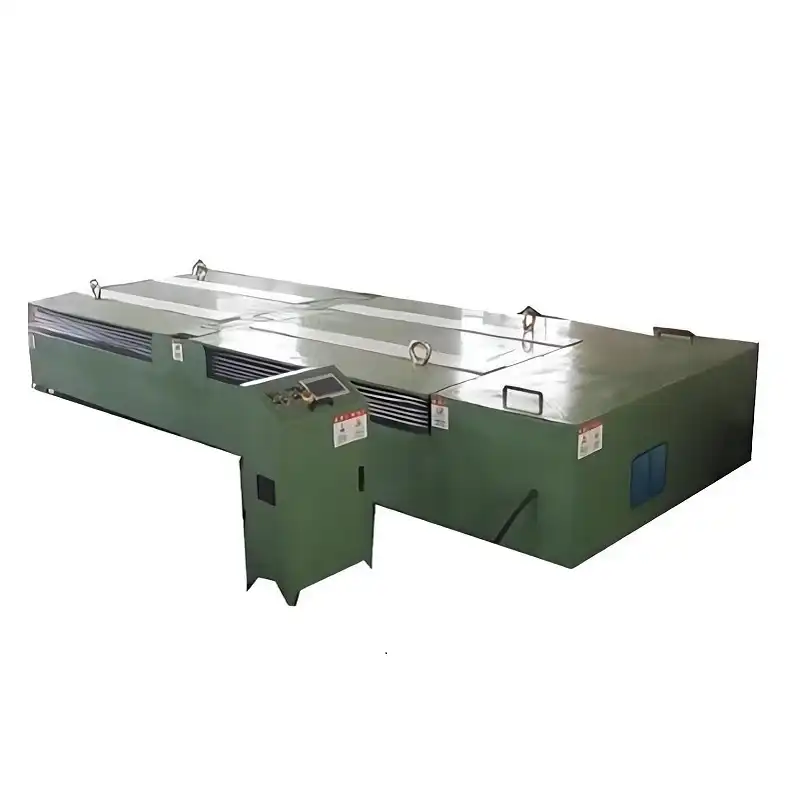
Integrating an injection mold flipper into your workflow offers significant advantages:
- Enhanced Safety: Dramatically reduces the risks associated with manual handling or less stable methods like flipping with chains and cranes. Minimizes potential crush injuries and strains.
- Increased Efficiency: Speeds up mold maintenance and changeover times by providing quick and easy access to all sides of the mold. Reduces reliance on crane availability.
- Mold Protection: Controlled, smooth rotation prevents accidental drops or impacts that can damage costly molds, especially parting line surfaces or delicate components.
- Improved Ergonomics: Reduces physical strain on technicians, allowing them to work in more comfortable and safer postures, leading to better quality work and reduced fatigue.
- Labor Optimization: Often allows mold handling and maintenance tasks to be performed safely by fewer personnel compared to traditional methods.
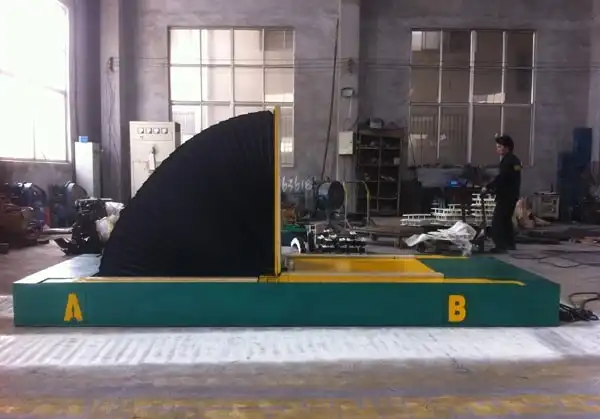
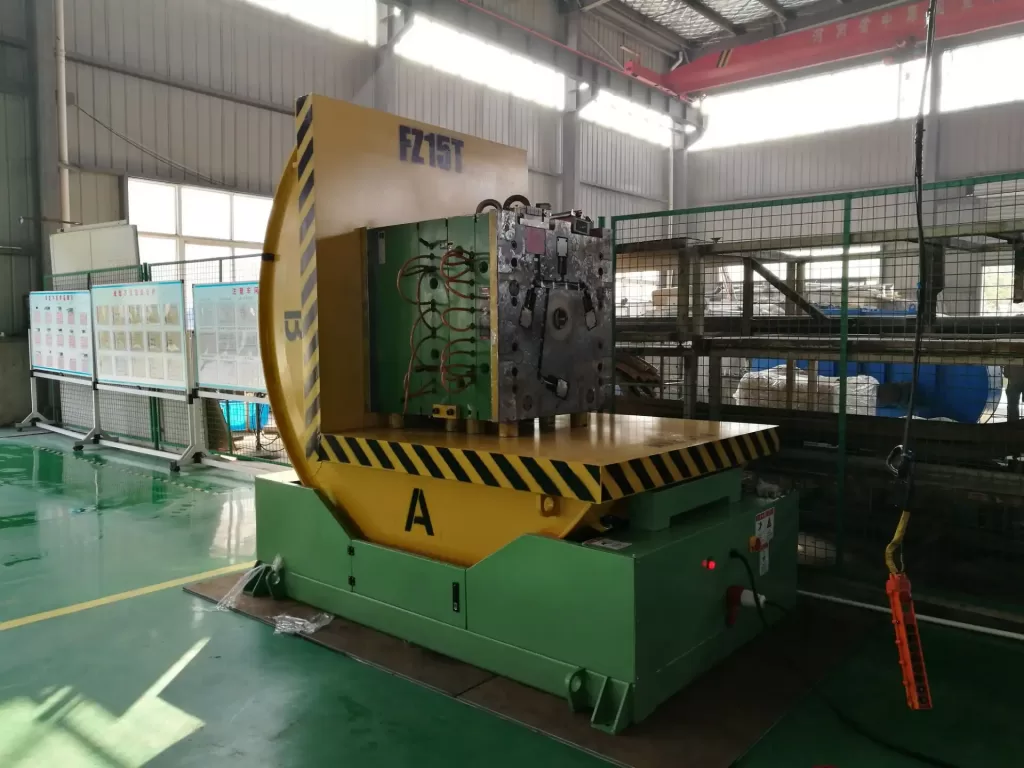
5. Essential Considerations When Choosing a Mold Flipper Manufacturer
Selecting the right injection mold flipper requires careful consideration of several factors beyond the initial cost. Partnering with a reliable manufacturer ensures you receive a safe, durable, and effective machine.
- Load Capacity and Size: Ensure the machine's rated capacity significantly exceeds the weight of your heaviest mold. Consider the physical dimensions (length, width, height) the flipper can accommodate.
- Rotation Angle and Type: Determine if you need 90-degree, 180-degree, or potentially custom rotation. Choose the actuation type (hydraulic, electric) that best suits your facility and maintenance capabilities.
- Safety Features: Verify the inclusion of essential safety components: emergency stops, limit switches, overload protection, robust construction, and potentially guarding or light curtains depending on your workplace safety assessment. Compliance with relevant safety standards (e.g., CE, ANSI) is crucial.
- Control System: Evaluate the ease of use and reliability of the control interface (pendant, push-button station). Consider options for variable speed control or automated cycles if needed.
- Construction Quality and Durability: Assess the materials used, weld quality, and overall robustness of the design. Look for features like heavy-duty bearings and structural reinforcements appropriate for the load capacity.
- Manufacturer Reputation and Experience: Research the manufacturer's history, industry experience, and customer feedback. Do they specialize in mold handling equipment? Can they provide references or case studies?
- Technical Support and Service: Inquire about installation support, operator training, availability of spare parts, warranty terms, and post-sales technical assistance. Responsive support is vital for minimizing downtime.
- Customization Options: If you have unique mold designs or specific handling requirements, check if the manufacturer offers customization (e.g., custom platform sizes, specific control integrations).
6. Conclusion: Investing in Safety and Productivity
An injection mold flipper is more than just a piece of equipment; it's an investment in workplace safety, operational efficiency, and the longevity of valuable tooling. By facilitating controlled, secure rotation of heavy molds, these machines significantly reduce manual handling risks, protect molds from damage, and streamline maintenance processes.
When choosing an injection mold flipper, carefully evaluate your specific requirements regarding load capacity, size, rotation, and safety features. Partnering with a reputable manufacturer who provides robust equipment and reliable support ensures you maximize the benefits of this essential technology, ultimately contributing to a safer and more productive manufacturing environment.
Explore various mold handling solutions, including mold upenders: https://www.fhopepack.com/mold-upender.html