What Makes an Automatic Copper Coil Strapping Machine Indispensable for Modern Packaging?
I have seen how small packaging oversights cripple shipping schedules. That presses me to find a reliable way to protect copper coils. An advanced strapping system answers that need today.
The machine eliminates guesswork by regulating strap tension. It prevents coil deformation, lowers labor needs, and guards products against shock during transport. Robust materials and smart sensors provide secure bundling. This advanced technology speeds throughput, reduces packaging waste, and strengthens supply chain reliability, making it indispensable for modern operations today.
I notice that many facilities still rely on outdated methods. That slows production, raises safety risks, and leads to inconsistent results. Automated strapping offers a clear alternative. It standardizes coil handling, frees up labor, and keeps operations on schedule. I want to explain how each part of the process works, so you can judge whether this technology fits your needs. Let me share three important angles that show why this machine stands out.
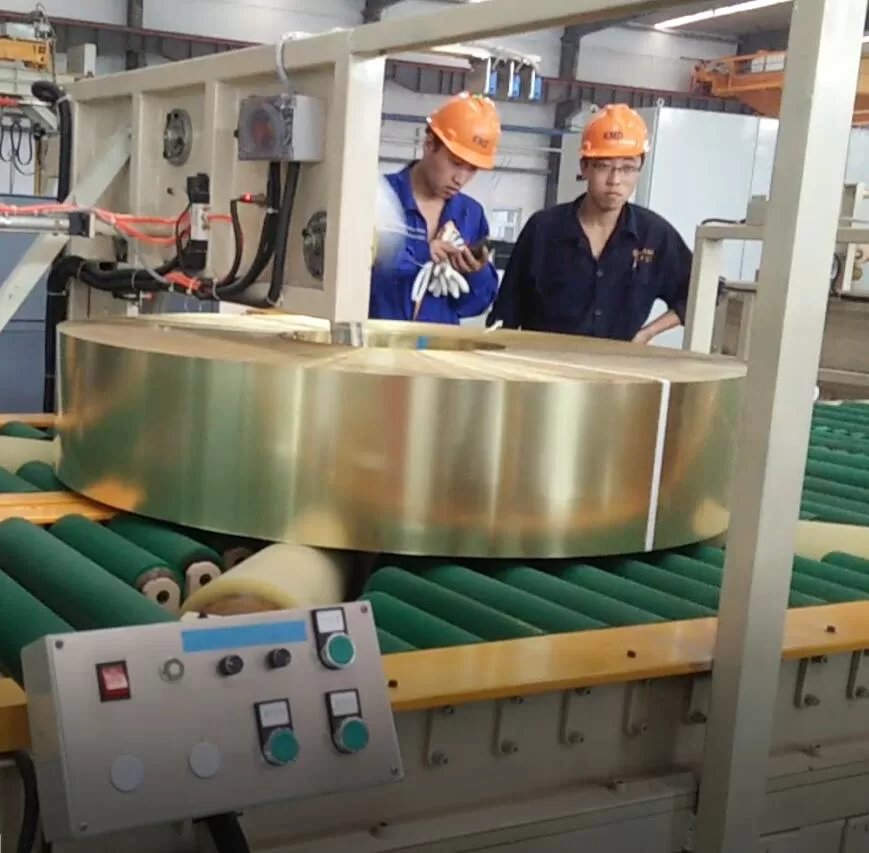
How Does Automated Strapping Safeguard Copper Coils from Damage?
I have watched coils shift or suffer scrapes when strapped by hand. That leads to dissatisfied clients, wasted time, and costly product returns. An automated machine avoids these pitfalls.
It applies the correct tension every time. It locks coils in place and removes the risk of loose or inconsistent straps. That lowers friction and prevents metal surfaces from rubbing. I think it is the safest way to bundle copper coils for transport and storage.
Automated strapping offers a stable wrap that cushions the coil edges. It also cuts down the chance of worker injuries that come from manual bundling. It ensures a uniform tension that standard practices rarely achieve.
Dive Deeper: Preventing Handling Errors and Minimizing Surface Flaws
I recall seeing how fragile copper coils can be. Small scratches or bends change their function. In my time at FHOPEPACK, I learned that uniform tension is key to safeguarding the product. When a manual process overlooks tension consistency, coils can shift inside their packaging. That leads to metal-on-metal contact or repeated vibration during transport, which may cause blemishes. An automated strapping machine solves this by measuring tension with precise sensors. This process guarantees that each strap has the same hold, cycle after cycle.
The Need for Gentle Yet Secure Fastening
Copper may appear tough, but it marks easily if handled poorly. Automated systems address this by allowing operators to set tension levels within safe limits. If the tension is too high, straps dig into the edges. If the tension is too low, the coil may slip or loosen. These machines fine-tune strap force through adjustable parameters, ensuring a snug but non-damaging grip.
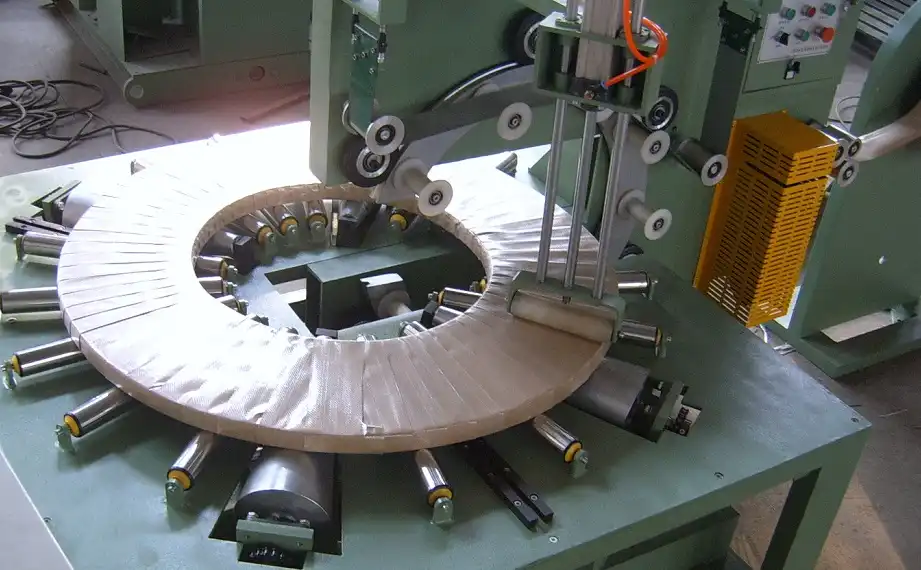
Avoiding Worker-Related Errors
Manual strapping often relies on human judgment. Workers might hurry because of deadlines. They might apply extra force to ensure the coil does not shift. That can lead to bent edges. Or they might not apply enough force, leaving the coil vulnerable. Automated systems replace guesswork with a measured approach. This consistent approach prevents the small mistakes that become big problems later. In addition, an automated system removes repetitive strain from workers, which reduces injuries. That makes the overall operation safer.
Protecting Surface Finish and Roundness
Copper coils may develop surface flaws if they move too much in their packaging. If the straps are uneven, the coil can flatten or warp at certain points. An automated strapping line sets each strap at the correct angle and tension. Some machines can also rotate or tilt coils to ensure every critical area is secured. This helps the coil maintain its roundness or its original shape through shipping. That is especially helpful for clients with strict tolerances, like those in electronics or specialized manufacturing.
Using Protective Materials
Many automated systems include options for plastic or edge protectors. These small inserts safeguard corners and surfaces when the strap tightens. I have found that combining a well-calibrated tension system with simple edge guards significantly reduces scuffs. An integrated approach that merges the strapping tool and protective measures can remove the chance of friction or localized pressure. This design keeps the coil free from damage even when traveling long distances.
Key Factor | Action Taken by Automated System | Result |
---|---|---|
Tension Control | Precisely sets force for each strap | Uniform grip, no coil shifting |
Protective Materials | Inserts edge guards before tension is set | Prevents scuffs, preserves shape |
Positioning Mechanisms | Repositions or rotates coil as needed | Even coverage and stable bundling |
Sensor Monitoring | Detects misalignments or strap irregularities | Reduces errors and rework |
Monitoring and Feedback
Some automated strapping setups record data for every strap cycle. They log tension values, coil sizes, and strap counts. That allows management to review packaging consistency. If a strap was applied incorrectly, the machine might stop or alert an operator. This real-time feedback helps keep coil protection high. It also ensures any problem is caught early, before a whole batch gets compromised.
Integration with Lifting Equipment
Copper coils can be heavy. It is risky to move them by hand. Automated lines pair strapping with lifts or conveyors that place the coil in the correct position. The strapping head then tightens the band around the coil without needing an operator to hold or guide it. This approach lowers the risk of dropping or scratching the coil. It also speeds up the packaging cycle. The coil remains stable, and the machine completes each strap with minimal human intervention.

Overall Benefits to Product Quality
By preventing manual tension misjudgments and ensuring consistent application, automated strapping protects coils from dents and scuffs. With careful use of protective materials, the packaging remains secure through transit. This reliability builds trust with customers, who value products that arrive in the same condition they left the facility. That trust often translates to repeat business and fewer disputes over damage claims.
I see that thorough coil protection relies on a machine that balances power with precision. The shift from manual to automated strapping has saved many companies time and money. It also reduces workplace injuries and returns due to product flaws. When each coil is strapped methodically, the final package can handle rough roads, stacking, or loading into containers without trouble. That leads to predictable outcomes in a field where unpredictability used to cause frustration.
What Core Features Ensure High Efficiency and Reliability?
I have studied many strapping systems, and some appear promising but fail to deliver. They skip critical elements like sturdy construction or sensor-based tension checks.
An advanced machine must offer programmable tension control, user-friendly interfaces, durable strapping heads, and quick strap feeding. It also needs real-time monitoring for coil misalignment. These features give stable performance and require fewer manual adjustments.
I learned that a machine with a rugged frame and modular parts is easier to maintain. A strong design supports continuous output while sensors prevent errors. That leads to uninterrupted production.
Dive Deeper: Key Components and Their Impact on Operational Stability
I have experienced how seemingly minor details can make or break a strapping machine. In a high-output environment, even one breakdown can set back shipping by hours or days. That is why understanding core features is vital. If these features are carefully chosen, the machine can run longer, produce consistent results, and require fewer unexpected repairs.
Sturdy Frame and Engineering
I recall a case where a flimsy frame led to constant vibrations, which caused the strapping head to fall out of alignment. A well-built machine uses thick-gauge steel and stable mounting points. That rigid platform does not shift or rattle as the strap is tensioned. It also prevents external bumps or forklift movements from nudging the machine off calibration. When the base is strong, the rest of the system can function well.

Tension Controllers
Some machines rely on a fixed tension setting, but that ignores differences between coil sizes or strap materials. A modern system uses adjustable tension controllers. Operators pick an ideal range, and the machine stays within it. This is especially important for copper coils with specific hardness or thickness. If the tension is too high, edges might bend. If it is too low, the strap might slide around. Automated controllers read sensor data and keep tension consistent.
Rapid Strap Feeding Mechanism
Efficiency often depends on how fast the machine can feed and cut straps. If the feed is slow or jams frequently, downtime adds up. A good system uses guides that align the strap, pinch rollers that feed it smoothly, and a cutting blade that can slice through the strap material without dulling quickly. High-quality feed components also let you use a variety of strap types, from steel to polyester. Flexibility matters when you change coil sizes or adapt to new packaging rules.
Automated Coil Sensing
I find that some advanced machines have sensors that detect coil dimensions or orientation. That data is fed into the tension controller, which adjusts in real time. This reduces the chance of accidental misalignment. If the coil is not placed properly, the machine can halt or alert an operator. That prevents wasted strapping material or potential coil damage. An automated sensing routine also speeds up line changeovers when coil sizes vary.
User-Friendly Interface
A machine can have top-tier hardware, but if the interface confuses operators, problems arise. I look for clear touchscreen panels that show tension settings, strap counts, and error codes. Operators can quickly switch between presets or run diagnostic checks. Multi-language support can help in factories with diverse teams. A straightforward interface makes training simpler, which reduces mistakes.
Feature | Purpose | Benefit |
---|---|---|
Rigid Frame | Minimizes vibration and misalignment | Stable operation, lower maintenance |
Adjustable Tension | Matches strap force to coil requirements | Prevents coil damage, ensures firm hold |
Quick Strap Feeding | Speeds up cycle times | Reduces downtime, raises throughput |
Sensor Integration | Detects coil position and size | Cuts errors, automates tension adjustment |
Intuitive Interface | Simplifies operator training and control | Lowers error rates, speeds troubleshooting |
Speed and Cycle Times
In high-volume operations, speed is king. A machine that can strap many coils per hour has a direct impact on shipping schedules. But speed must not compromise accuracy. Strapping heads that accelerate the tensioning process need advanced servo motors or precise pneumatics. These motors deliver consistent force without skipping. Coupled with fast strap feeding, they cut cycle times significantly. Yet they must not jerk the coil or overshoot tension. Balancing speed with safety is crucial.
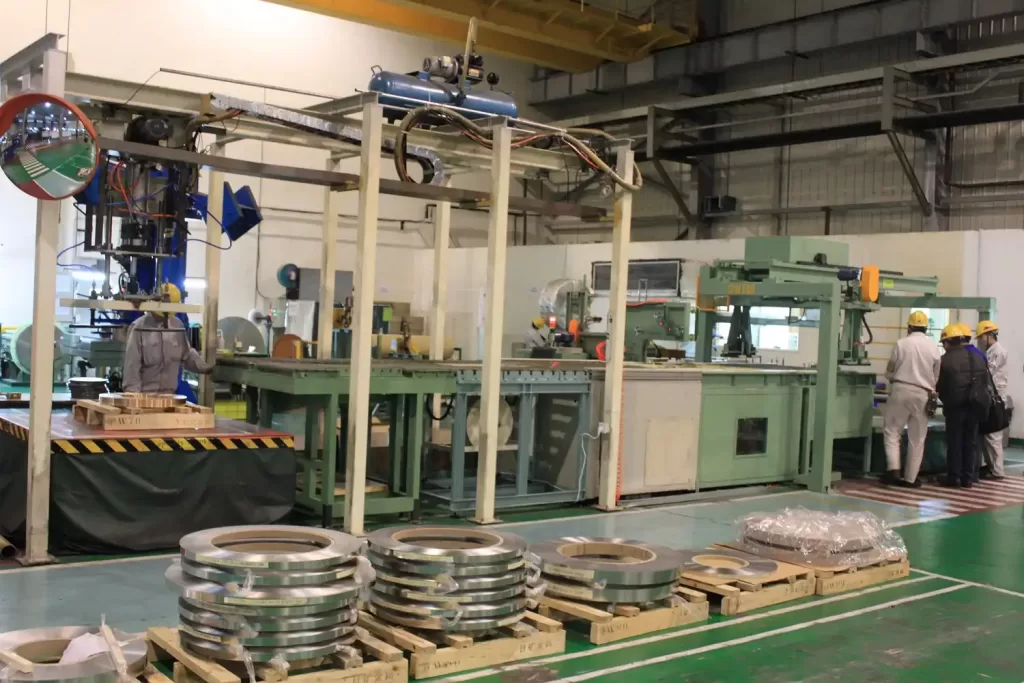
Maintenance Requirements
No machine is perfect, so it helps if components are modular. This design choice means if one roller or sensor fails, the operator can quickly replace that part without disassembling the entire system. Some strapping machines have easy-access doors or hinged panels. That makes routine checks simpler. A well-organized interior, with labeled cables and color-coded tubing, also helps maintenance crews identify parts. This approach reduces the mean time to repair (MTTR). It also lowers frustration when time is short.
Reliability in Varying Environments
Copper coils may be stored in areas with dust, humidity, or temperature swings. A reliable machine must handle these conditions without frequent malfunctions. Electronics and sensors should have protective enclosures. Bearings or gears should be lubricated or sealed to keep out debris. I have seen how a poorly sealed sensor can cause repeated false readings, bringing the line to a halt. Weather-resistant or sealed components help keep the system stable, which keeps productivity high.
Data Collection and Diagnostics
I notice that modern strapping machines often connect to a plant’s network. They record data about coil sizes, strap usage, cycle times, or errors. Managers can review that information for production planning. They can also predict when to order new strap stock. In some systems, remote diagnostics allow technicians to troubleshoot issues from afar. That means faster solutions and less downtime. Over time, analyzing the machine’s data can reveal patterns that help you optimize coil handling further.
When these features come together in one package, the strapping machine performs reliably day after day. It does not waste resources, and it does not require constant baby-sitting. That is what I mean by high efficiency. It accomplishes the task with minimal input, minimal downtime, and minimal chance of error. The best systems strike a balance between advanced technology and user-friendliness. They are built to handle real-world conditions in a busy factory. That is why I see them as essential tools, rather than optional luxuries.
How Do You Optimize Your Investment with the Right Machine Setup?
I believe that choosing an automated strapping machine is not just about speed. It also involves checking your plant layout, product mix, and future growth.
You can extend the machine’s lifespan by scheduling maintenance and training staff thoroughly. A well-integrated system can meet expanding demands. This stops the need for frequent replacements.
I realize that a balanced approach to cost, throughput, and long-term flexibility is what ensures a solid return on investment. That approach covers installation, operator preparation, and future expansions.
Dive Deeper: Making Smart Decisions for a Lasting Packaging Solution
I have encountered many clients who want to jump straight into buying the biggest, fastest strapping machine available. Then they find their facility layout cannot accommodate it, or their staff is unprepared for the complexity. A well-planned investment strategy looks at the machine’s technical specs, matches it with existing infrastructure, and leaves room for growth. That ensures the system pays for itself over time.
Assessing Your Production Needs
Start by looking at daily and monthly coil output. If you handle large volumes, you need a high-capacity machine. If volume is moderate, a mid-range model might suffice. Think about product variety. Do you process only one coil size or multiple diameters and thicknesses? If there is variation, the machine should support quick changeovers. Also check if you plan to add more coil types soon. Buying a machine that barely meets your current demand might lead to problems if you experience a sudden surge in orders.
Matching Machine Capabilities to Layout
A strapping machine needs space for loading coils, strapping, and unloading. Operators also need room to move around for maintenance or spool changes. If your layout is cramped, consider if a vertical or horizontal strapping orientation is better. Some machines can be embedded in an existing conveyor line. Others are standalone with integrated coil feeding. Draw a diagram of your floor plan to see how the machine fits with forklift routes and other equipment. A smooth material flow from coil storage to packaging to shipping is ideal.
Training and Staff Engagement
I think staff buy-in is essential. If operators do not understand how to set tension levels or run diagnostics, the machine will not perform well. Provide hands-on training when the machine is installed. Walk operators through routine checks, spool replacement, and minor troubleshooting. Encourage them to watch for any unusual sounds or error codes. A well-trained team can keep the machine running at peak efficiency. They can also help identify small issues before they become major breakdowns.

Maintenance Scheduling
Every machine has wear items, such as belts, blades, or sensor components. Plan a regular schedule to inspect these parts and replace them as needed. Try to keep a small stock of critical spares on hand. Downtime while waiting for parts can be costly. Document each service event. Note the replaced parts and any symptoms leading up to the failure. Over time, you will see patterns that let you do preventive maintenance instead of reactive fixes. That approach extends the machine’s life.
Optimization Step | Action | Benefit |
---|---|---|
Measure Production Volume | Forecast daily and monthly output | Right machine size, no over- or under-buy |
Evaluate Layout | Plan space for loading and feeding | Smooth flow, fewer collisions or stops |
Train Operators | Provide detailed instruction | Fewer errors, faster troubleshooting |
Schedule Maintenance | Replace wear parts on a regular timetable | Less downtime, better reliability |
Plan for Expansion | Choose a flexible design | Easier upgrades, meets future needs |
Budget and Return on Investment
Cost is always a factor. However, a cheaper system that breaks frequently can cost more in lost productivity. On the other hand, an overly advanced system might be underutilized if you do not really need its features. I suggest calculating a payback period based on labor savings, less rework, and faster throughput. If you currently spend a lot on manual strapping or on re-packaging damaged coils, you might recoup the cost quickly. Also consider intangible benefits, like better client satisfaction and fewer returns.
Future-Proofing the Setup
Copper coil demand can shift. If you plan to add bigger coils or new product lines, pick a machine that can handle a range of dimensions. Some solutions are modular and let you add expansions later. For instance, you might start with manual feeding, then add an automated conveyor if throughput grows. This staged approach helps spread out costs. It also stops the disruption of replacing the entire system when your needs change. Look at the supplier’s track record. Do they offer upgrades or trade-in programs?
Integration with Other Equipment
Think about linking your strapping machine with automated wrapping, labeling, or palletizing. If each piece works together, you create a unified packaging line. That leads to less downtime transferring products from station to station. Also, integrated lines often share data, letting you track coil status from strapping to shipping. You can see real-time stats, which help with scheduling. This synergy can reduce labor further and refine the overall process.
Safety Considerations
Heavy coils can injure workers if they slip or tip. Automated strapping systems often come with guards, safety interlocks, and emergency stops. Confirm that these features meet regulatory standards in your region. Also confirm that the machine is easy to power down in case of jammed straps or coil misalignment. By planning for safety from the start, you protect employees and limit the risk of accidents.
Ongoing Support
A reliable supplier does more than sell a machine. They help with setup, training, and ongoing support. Ask about service contracts or extended warranties. Find out if there is a local service center that can assist quickly. If remote diagnostics are available, the technician might be able to log into the machine and solve issues. That approach can save hours of downtime. Also, keep in touch with your supplier about software updates or hardware upgrades.
When you optimize your investment in an automatic copper coil strapping machine, you set up a process that can run with minimal hiccups. You adapt the system to your space, your product mix, and your workforce. The result is a packaging line that consistently delivers secure coils, day after day. This stable performance fosters trust among clients who rely on timely shipments of undamaged products. It also brings peace of mind internally, knowing the line can scale if demand jumps. From what I have seen, a well-chosen machine repays your time and money many times over, especially when you integrate it with thoughtful planning and thorough training.
Conclusion
I observed that an automatic copper coil strapping machine can transform packaging operations by uniting speed, consistent tension, and long-term durability. It minimizes worker strain, prevents coil damage, and provides a firm base for growth. When you combine it with clear training, flexible design, and timely maintenance, the machine stands as a reliable pillar of modern coil handling. I trust this exploration sheds light on why it has become indispensable. I hope my experience at FHOPEPACK demonstrates how thoughtful choices lead to a stable, efficient packaging environment that meets the demands of today’s market.