Enhancing Upender Safety: Why Worm Gear Drives Offer Superior Protection
Safety is paramount when handling heavy loads like coils, molds, or dies. In operations involving 90-degree tilting or turning, the upender's drive system plays a critical role. While various factors contribute to overall system safety – including design, construction, and maintenance – focusing solely on the drive mechanism reveals a key distinction: a worm gear motor configuration generally provides enhanced safety compared to a standard gear motor drive.
Let's explore why worm gear drives are often preferred for safety-critical upending applications.
1. The Safety Advantages of Worm Gear Motors in Upenders
Worm gear motors integrate a motor with a worm gear reducer. This combination offers distinct mechanical advantages that directly translate to increased operational safety, especially under heavy loads.
A typical worm gear motor assembly, illustrating the perpendicular arrangement of the worm (screw) and the worm wheel (gear).
1.1 High Reduction Ratio and Back-driving Prevention
Worm gear arrangements naturally provide a substantial gear reduction ratio. This means the motor's high speed and low torque are converted into low speed and high torque at the output shaft.
- Benefit: Less input force is needed to initiate and control the turning motion. Crucially, this high reduction makes it inherently difficult for the load's weight or inertia to drive the motor backward (a phenomenon known as back-driving). This resistance significantly reduces the risk of uncontrolled or unexpected load movement.
1.2 The Crucial Self-Locking Feature
Perhaps the most significant safety benefit is the inherent self-locking nature of most worm gears (especially those with low lead angles).
- Mechanism: The angle and friction between the worm (screw) and the worm wheel (gear) prevent the wheel from rotating the worm. In essence, the output shaft cannot easily turn the input shaft.
- Benefit: When the motor stops (either intentionally or due to power loss), the worm gear inherently holds its position, effectively braking the load. This prevents the upender from unintentionally continuing its rotation or reversing under gravity, even if the primary motor brake fails. The machine can reliably stop and hold the load steady at any angle during the tilting process.
1.3 Smoother, Quieter Operation
Compared to some other gear types, the sliding action between the worm and wheel threads often results in smoother and quieter operation. While not a direct safety feature like self-locking, reduced vibration and noise can contribute to a better and potentially safer working environment.
2. Potential Safety Concerns with Standard Gear Motors in Upenders
Standard gear motors, often using helical or spur gears, present a different operational dynamic.
A common configuration where the motor and helical gearbox output shaft are aligned.
2.1 Reliance on External Braking
In typical configurations, the motor shaft and the output shaft of a standard gearbox are essentially in-line. These gear types generally do not possess inherent self-locking properties.
- Implication: Stopping and holding the upender's load relies almost entirely on the motor's integrated brake.
2.2 Risk During Stoppage or Power Failure
While motor brakes are designed for stopping, relying solely on them for holding heavy, off-balance loads presents risks:
- Brake Wear/Failure: Brakes are subject to wear and tear and potential failure. Holding a heavy load mid-turn puts significant, continuous stress on the brake.
- Power Loss: If power is cut unexpectedly during a tilting operation, the motor brake engages, but without the inherent holding power of a worm gear, there's a higher risk (especially with very heavy or dynamically shifting loads) of the brake slipping or failing over time, potentially leading to the load drifting or falling. This poses a significant safety hazard.
3. FHOPEPACK's Commitment to Safety: Worm Gear Driven Upenders
Recognizing the superior safety characteristics, the mechanical upenders provided by FHOPEPACK utilize a robust worm gear + motor drive system. This design choice prioritizes operational safety and durability, allowing the equipment to withstand demanding industrial environments.
This approach offers double safety protection:
- Primary Motor Brake: Provides initial stopping force.
- Worm Gear Self-Locking: Offers inherent, failsafe load holding, independent of the motor brake or power status.
This combination ensures that loads remain secure during operation and, critically, in the event of a power interruption.
For more details on specific upender solutions incorporating this safer drive technology, please visit: https://www.fhopepack.com/Coil_upender.html
4. Visual Examples of Upenders and Tilters
Below are examples of equipment where drive system safety is crucial:
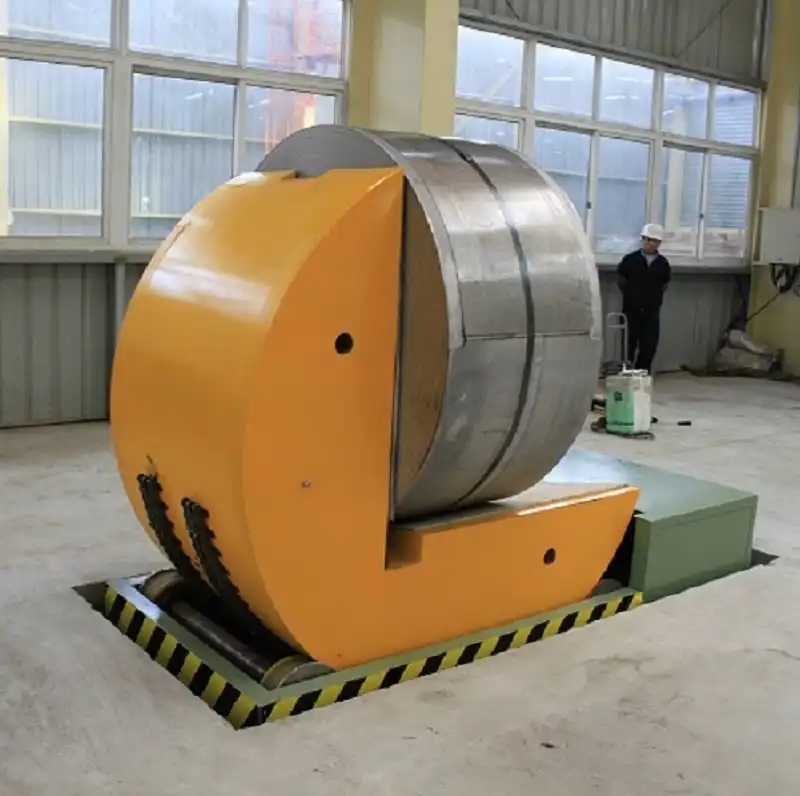
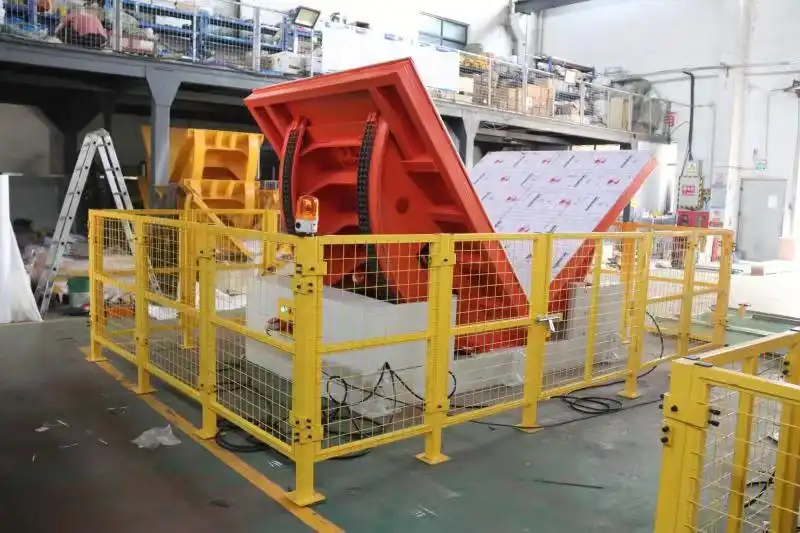
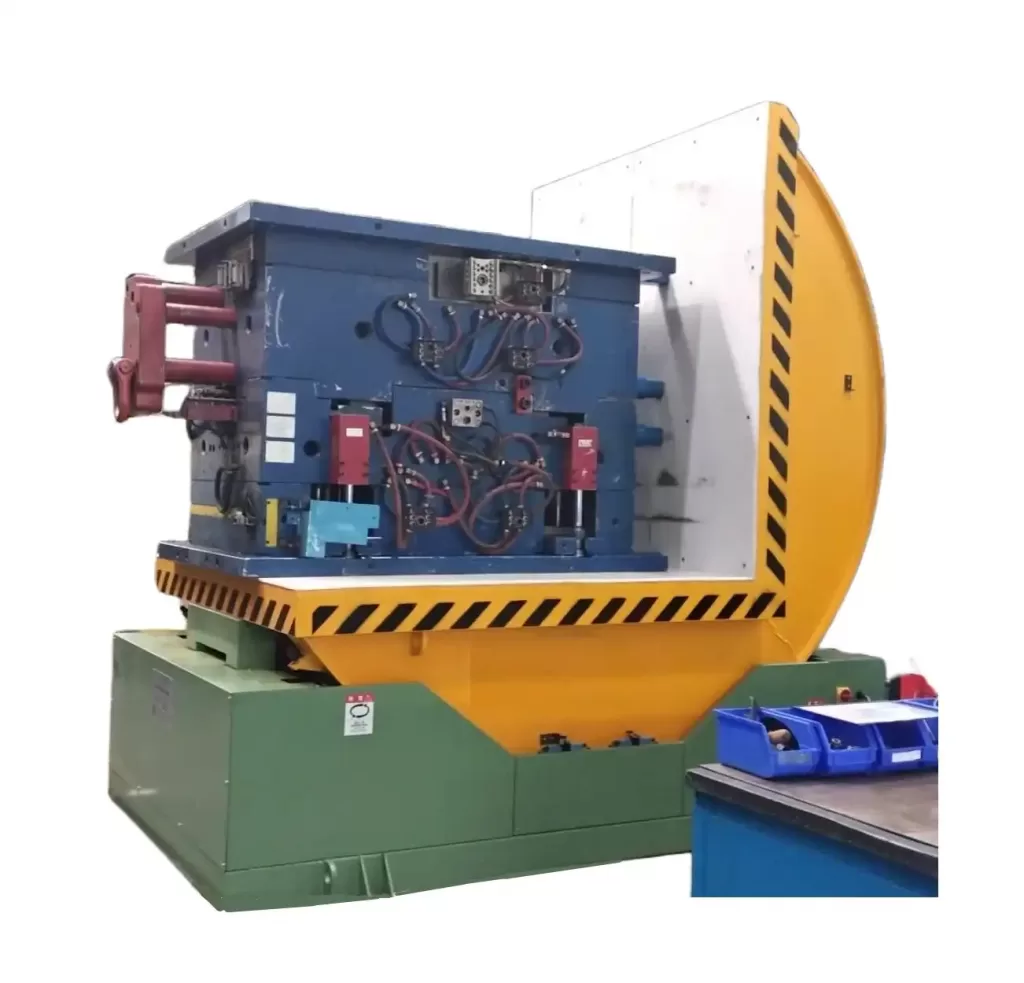
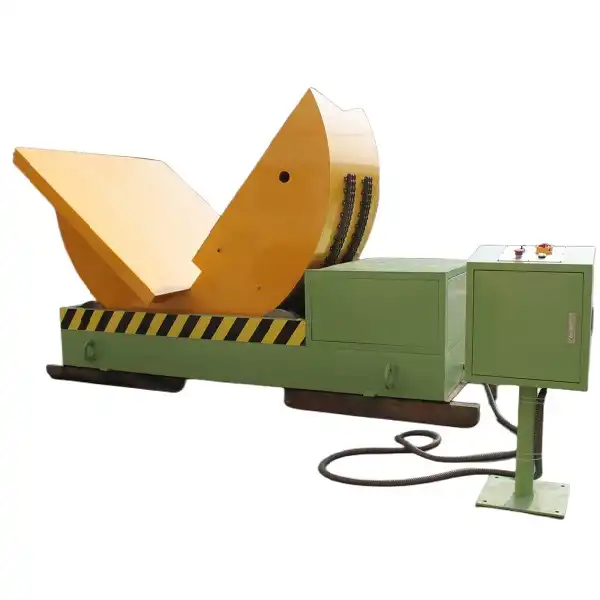