Top 6 Automated Steel Coil Packing Lines Compared
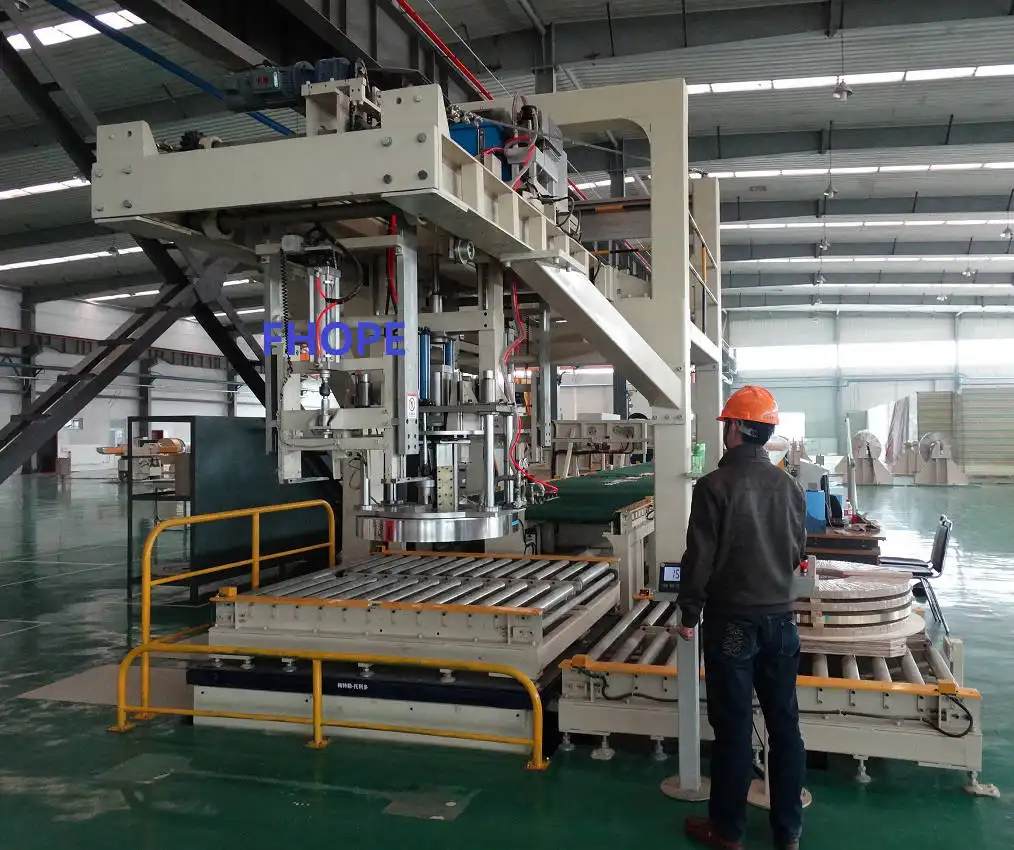
For industries handling steel coils, efficient, reliable, and safe packaging is crucial. Automated steel coil packing lines provide significant advantages over manual methods, enhancing speed, precision, consistency, and worker safety. However, with various systems available, selecting the right one requires careful consideration of your specific operational needs.
This guide compares six prominent automated steel coil packing lines, examining their key features, capabilities, and suitability for different applications. Understanding these differences will help you identify the optimal system for your facility.
1. Understanding Automated Steel Coil Packing Lines
The increasing demands from sectors like automotive, construction, and appliance manufacturing necessitate efficient and robust coil packaging solutions. Steel coil packing has evolved significantly from labor-intensive manual processes to sophisticated automated systems capable of handling heavy loads with precision and speed.
Implementing the right automated packing line impacts productivity, labor costs, safety, and product protection during transit. Key components typically include coil loading/unloading, conveying, wrapping stations (using materials like stretch film, VCI paper, or HDPE), strapping stations (using steel or PET strapping), labeling, and stacking systems.
2. Benefits of Automating Steel Coil Packaging
Transitioning from manual to automated steel coil packaging offers substantial operational advantages:
a. Increased Productivity and Throughput
Automated lines operate continuously at speeds significantly higher than manual methods. Systems can process anywhere from 25 to over 40 coils per hour, enabling facilities to meet demanding production schedules and reduce bottlenecks.
b. Enhanced Worker Safety
Handling heavy steel coils manually poses significant risks of injury. Automation minimizes direct human interaction with coils during the packaging process, drastically reducing the potential for accidents related to lifting, maneuvering, and securing heavy loads.
c. Improved Packaging Quality and Consistency
Automated systems apply packaging materials (film, straps) with precise tension and placement every time. This consistency ensures optimal protection against environmental factors and handling damage during storage and transportation, reducing product loss and customer claims.
d. Long-Term Cost Savings
While requiring an initial investment, automation reduces long-term operating costs by lowering labor requirements, minimizing material waste through efficient application, increasing throughput, and reducing product damage.
3. Key Criteria for Comparing Packing Lines
To effectively compare different automated steel coil packing lines, consider these critical factors:
- Throughput Speed: How many coils can the system reliably process per hour?
- Coil Size & Weight Capacity: What is the range of coil diameters, widths, and weights the system can handle?
- Packaging Flexibility: Can the system accommodate different packaging materials (e.g., stretch film, VCI paper, different strap types) and specifications?
- Level of Automation: Does the system offer fully integrated automation from coil entry to exit, or are some manual steps required?
- Footprint & Layout: How much floor space does the system require, and can it be configured to fit the available area?
- Safety Features: What integrated safety mechanisms (e.g., light curtains, safety fencing, emergency stops, sensors) are included?
- Maintenance & Reliability: How robust is the system, and what are the expected maintenance requirements?
- Integration Capability: Can the system easily integrate with existing plant management systems (MES, ERP) or other upstream/downstream equipment?
Evaluating systems based on these criteria will help determine the best fit for your specific operational context.
4. Fhopepack Coil Packing Line
The Fhopepack Coil Packing Line is recognized for its versatility and comprehensive automation, handling a broad spectrum of coil sizes and packaging requirements.
Key Features:
- Versatile Wrapping: Employs advanced wrapping technology compatible with various materials like stretch film, VCI paper, and woven fabrics for tailored protection.
- High Throughput: Capable of processing 30-40 coils per hour, suitable for medium to high-volume operations.
- Integrated Safety: Features comprehensive safety measures including sensors, light curtains, and emergency stops.
- User-Friendly Controls: Utilizes PLC controls with an intuitive interface for ease of operation and parameter adjustments.
Pros:
- Highly customizable to specific coil dimensions and packaging material needs.
- Offers a good balance of speed and flexibility.
- Strong emphasis on operator safety.
Cons:
- May have a higher initial investment compared to less flexible systems.
- Advanced automation might require specialized maintenance personnel.
5. Signode CoilMaster System
The Signode CoilMaster System is engineered for durability and robust performance, particularly favored in industries requiring heavy-duty coil packaging solutions.
Key Features:
- Heavy-Duty Construction: Built to withstand demanding industrial environments and handle large, heavy steel coils reliably.
- High-Tension Strapping: Specializes in applying steel strapping with high tension for maximum coil securement during transport.
- Size Flexibility: Accommodates a wide range of coil sizes, with adjustable settings for strapping patterns and tension.
Pros:
- Extremely durable design suitable for heavy industrial use.
- Provides excellent coil securement with high-tension strapping.
- Known for reliability and requiring minimal maintenance in harsh conditions.
Cons:
- Typically operates at a slightly lower speed, around 25-30 coils per hour.
- Primarily focused on strapping; wrapping may require separate or integrated modules.
6. PESMEL Coil Packaging Line
The PESMEL Coil Packaging Line is noted for its high efficiency and often compact, space-saving designs, making it suitable for facilities where floor space is a constraint.
Key Features:
- Efficient Footprint: Often designed to minimize floor space requirements while maintaining high throughput.
- Full Automation: Offers highly automated solutions, often integrating wrapping, strapping, and logistics for minimal manual intervention.
- Rapid Changeovers: Engineered for quick adjustments between different coil sizes and packaging recipes, enhancing operational flexibility.
Pros:
- Space-efficient designs are advantageous for plants with limited area.
- High degree of automation reduces labor needs and potential errors.
- Fast changeover capabilities maximize uptime and productivity.
Cons:
- May have limitations on the maximum coil size or weight compared to some heavy-duty systems.
- Compact integration might limit accessibility for certain maintenance tasks.
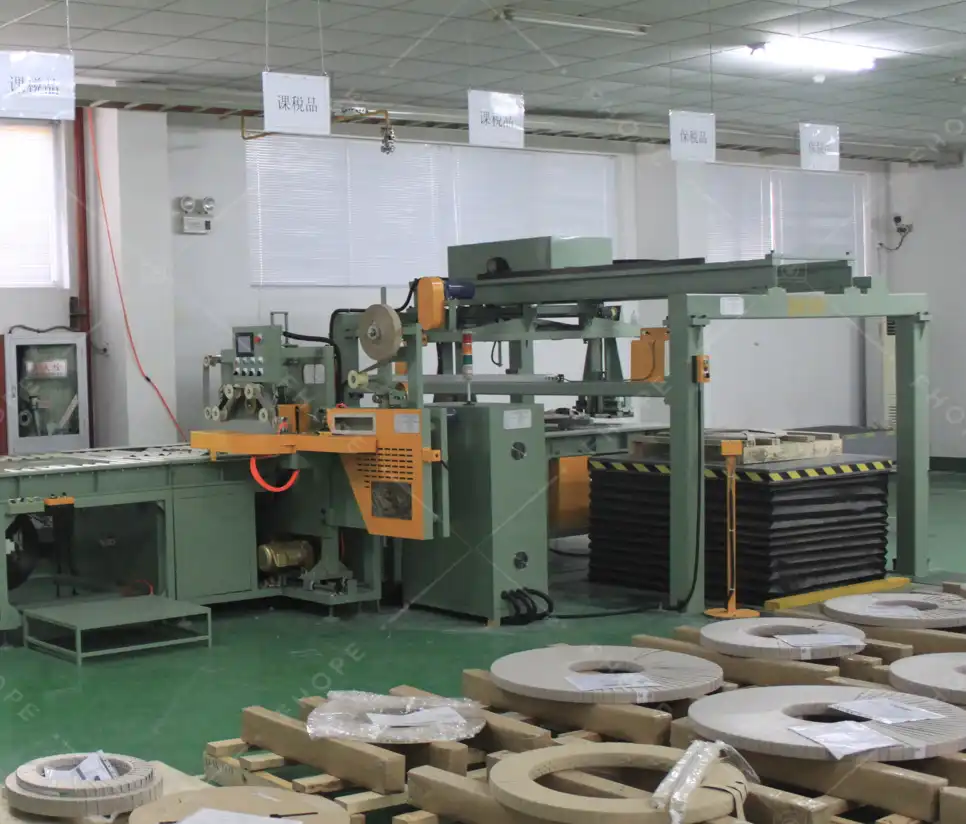
7. Lachenmeier Coil Wrapping Machine
Lachenmeier (now part of Signode) systems are renowned for innovative stretch hood and stretch wrapping technology, focusing on load stability and film efficiency. While often part of a larger line, their wrapping technology is a key component.
Key Features:
- Film Efficiency: Utilizes advanced stretch film application techniques (like Power Stretch) to maximize film yield and reduce material consumption while ensuring secure wrapping.
- Load Integrity: Focuses on creating highly stable and protected loads suitable for transport and outdoor storage.
- Customizable Wrapping: Allows precise control over wrapping patterns, tension, and film overlap for optimal protection based on coil specifics.
Pros:
- Excellent film efficiency leading to lower consumable costs.
- Produces highly stable and consistently wrapped coils.
- Technology integrates well with conveying and strapping systems.
Cons:
- Primarily focused on wrapping; a complete line requires integration with other components (strapping, conveying).
- Advanced film technology may represent a higher initial cost module.
8. Signode Multistrap System
Distinct from the CoilMaster, the Signode Multistrap System emphasizes high-speed strapping, often used for securing coils quickly in high-throughput environments.
Key Features:
- Multiple Strapping Heads: Capable of applying several straps (steel or PET) simultaneously or in rapid succession, significantly speeding up the strapping cycle.
- High-Speed Operation: Designed for maximum throughput, potentially exceeding 40 coils per hour depending on the configuration and coil size.
- Flexible Strapping: Accommodates various strap types and sizes, with adjustable tension settings for different coil requirements.
Pros:
- Very high strapping speed, ideal for large-scale, fast-paced operations.
- Customizable strapping patterns and tensions.
- Compatible with both steel and PET strapping.
Cons:
- Requires consistent maintenance to keep multiple strapping heads operating optimally.
- Primarily a strapping solution; needs integration with wrapping and handling systems for a full line.
9. SHJLPACK Steel Coil Packing Line
The SHJLPACK Steel Coil Packing Line is another robust option, providing integrated solutions often tailored for heavy coils and demanding industrial applications.
Key Features:
- Integrated Solutions: Often provides a complete line including conveying, wrapping, strapping, and sometimes stacking/upending functions.
- Heavy Coil Handling: Designed with robust structures and components capable of handling large and heavy steel coils common in mills and service centers.
- Safety Integration: Incorporates standard safety features like guarding, interlocks, and sensors to ensure safe operation.
Pros:
- Offers complete, integrated packaging lines from a single source.
- Durable construction suitable for heavy-duty environments.
- Can be customized to specific layout and process requirements.
Cons:
- Throughput might be moderate (approx. 25-30 coils per hour) depending on the complexity of the integrated functions.
- As a comprehensive system, it represents a significant capital investment.
10. Comparative Overview
Here’s a summary comparing the key aspects of the discussed systems:
System | Typical Speed (Coils/Hour) | Primary Focus / Strength | Automation Level | Flexibility | Key Consideration |
---|---|---|---|---|---|
Fhopepack | 30-40 | Versatile Wrapping & Handling | High | High (Size & Materials) | Balanced Speed & Flexibility |
Signode CoilMaster | 25-30 | Heavy-Duty Steel Strapping | Moderate to High | Good (Heavy Coils) | Durability, Steel Strapping |
PESMEL | 30-35+ | Efficiency, Compact Design, Integration | High to Full | Good (Fast Changeover) | Space Efficiency, Automation |
Lachenmeier (Wrapping) | 30-40 (Wrapping Cycle) | Film Efficiency, Load Stability | High (Module) | High (Wrapping Patterns) | Consumable Savings |
Signode Multistrap | 40+ (Strapping Cycle) | High-Speed Strapping | High (Module) | High (Strap Types/Patterns) | Maximum Strapping Speed |
SHJLPACK | 25-30 | Integrated Heavy-Duty Solutions | High | Good (System Customization) | Complete Line, Heavy Coils |
Note: Speeds are estimates and depend heavily on coil size, packaging recipe, and specific line configuration.
Key Takeaways:
- For Maximum Throughput (Strapping Focused): The Signode Multistrap excels in high-speed strapping environments.
- For Overall Flexibility: Fhopepack offers high adaptability for various coil sizes and packaging materials.
- For Heavy-Duty Applications: Signode CoilMaster (strapping) and SHJLPACK (integrated lines) are built for durability with heavy coils.
- For Space-Constrained Facilities: PESMEL lines often feature space-efficient designs with high automation.
- For Optimizing Film Costs: Lachenmeier's wrapping technology minimizes stretch film consumption.
Conclusion
Automating the steel coil packaging process is a strategic investment that yields significant returns in productivity, safety, consistency, and cost-efficiency. The best system depends entirely on your specific operational needs, including coil characteristics (size, weight), required throughput, packaging material preferences, available floor space, and budget.
Whether prioritizing speed (Signode Multistrap), flexibility (Fhopepack), heavy-duty reliability (Signode CoilMaster, SHJLPACK), space efficiency (PESMEL), or material savings (Lachenmeier), a suitable automated solution exists. Carefully evaluating your requirements against the capabilities of these leading systems will guide you toward the most effective automated steel coil packing line for your business, ensuring your products are protected and your operations run smoothly.