Optimizing Your Workflow: A Fabricator's Guide to PU/PE Tube Coiling and Strapping Systems
Efficiently handling and packaging polyurethane (PU) and polyethylene (PE) tubing is a critical step in many manufacturing and fabrication workflows. Selecting the right equipment – specifically tube coiling and strapping systems – directly impacts operational speed, product protection, labor costs, and overall throughput. Fabricators face a choice between budget-friendly, often simpler machines, and high-end, automated systems. This guide provides a practical comparison to help you determine the most suitable PU/PE tube packaging solution for your specific operational requirements.
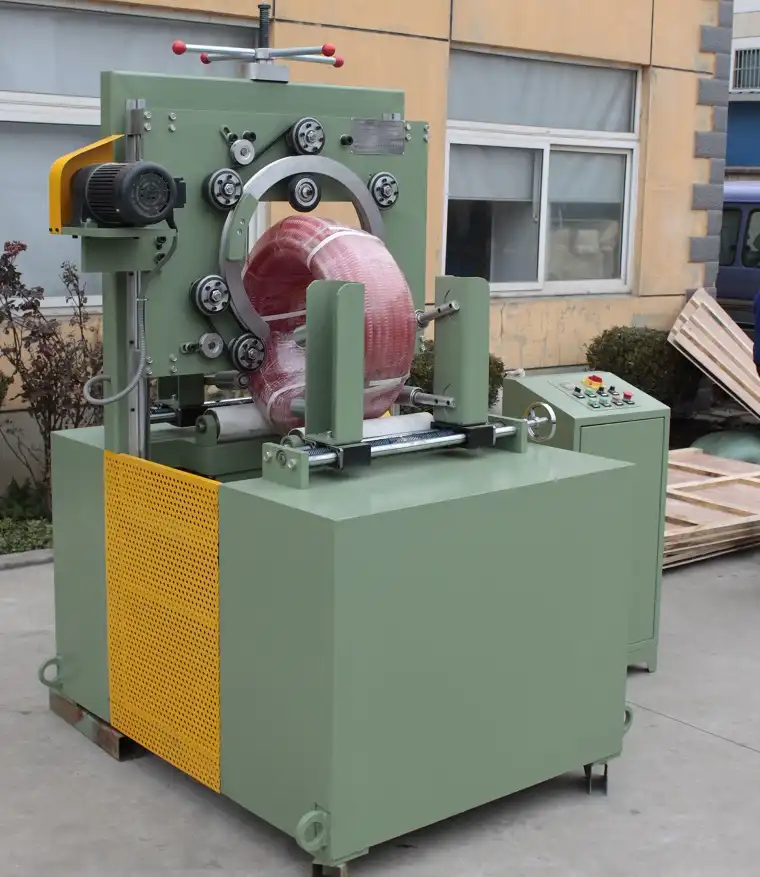
Understanding PU/PE Tube Coiling and Strapping Systems
At their core, PU/PE tube coiling and strapping systems automate the process of winding extruded or bulk tubing into neat coils and securing them with straps for handling, storage, and shipment. These systems are indispensable in industries ranging from automotive and pneumatics to beverage dispensing and irrigation, ensuring tube integrity and facilitating easier inventory management.
Key Components Breakdown
While designs vary, most tube coiling and strapping systems incorporate several essential functional units:
- Tube Infeed/Accumulator: Guides the tube smoothly into the machine, sometimes providing buffer capacity.
- Coiling Head/Winder: Forms the tube into a coil of a predetermined diameter and length. Precision and tension control are key here.
- Cutting Mechanism: Accurately cuts the tube once the desired coil length is reached. Cut quality is crucial to prevent tube damage.
- Strapping Unit(s): Applies and secures plastic straps around the finished coil. The number and position of straps can often be configured.
- Coil Ejection/Handling: Moves the finished, strapped coil out of the machine, often onto a conveyor or collection table.
- Control System (PLC/HMI): The brain of the operation, controlling sequence, parameters (coil size, strap tension), and diagnostics.
The sophistication, build quality, and integration capabilities of these components are the primary differentiators between budget and high-end systems. For a general overview of hose and tube packaging machinery, you can explore options for PU/PE Tube Packing.
Evaluating Budget-Friendly PU/PE Tube Packaging Systems
Budget-friendly systems are engineered to deliver core coiling and strapping functions at a lower initial capital expenditure. They are often a viable starting point for smaller operations, companies with lower production volumes, or those handling a limited range of tube sizes.
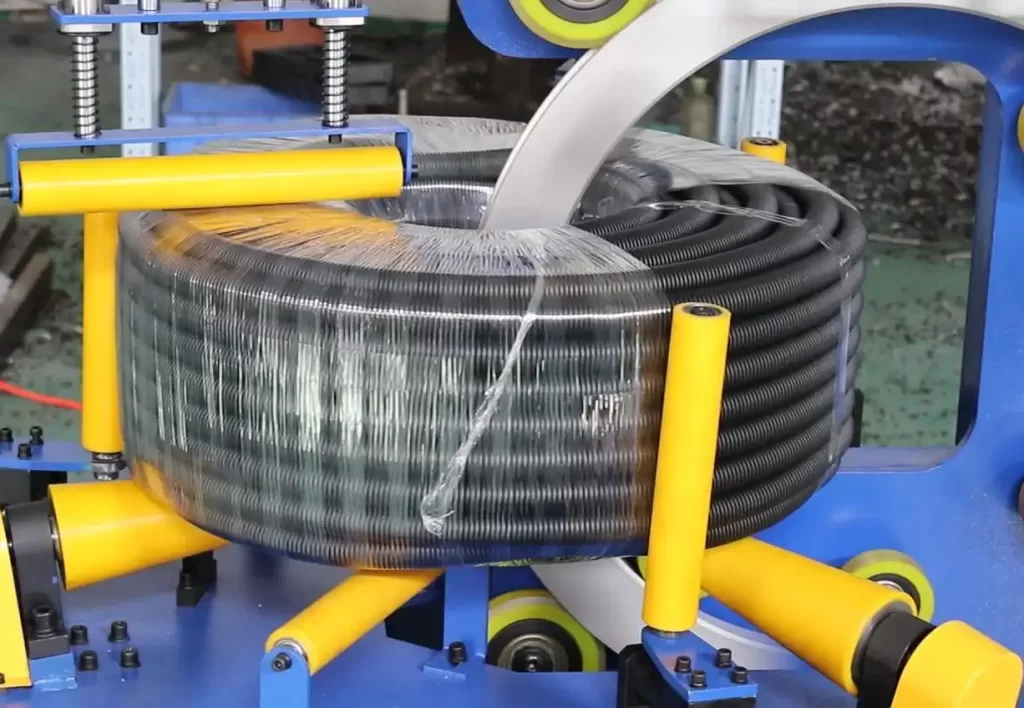
Typical Characteristics and Advantages
- Lower Initial Investment: The most significant benefit, making automation accessible.
- Simpler Operation: Often feature straightforward controls and require less extensive operator training.
- Smaller Footprint: Can be advantageous in facilities with limited floor space.
- Sufficient for Basic Needs: Effective for operations with moderate speed requirements and standard tolerances.
Potential Limitations
- Lower Throughput: Typically operate at slower speeds (coils per minute) compared to high-end counterparts.
- Limited Flexibility: May offer fewer adjustments for varying tube diameters, coil sizes, or material types without manual changeovers.
- Basic Control Features: Controls might lack advanced recipe management, detailed diagnostics, or extensive data logging.
- Durability Considerations: Components might utilize less robust materials, potentially leading to higher maintenance needs over time.
- Manual Intervention: May require more operator involvement for setup, adjustments, or fault recovery.
Exploring High-End Automated PU/PE Tube Coiling and Strapping Systems
High-end systems represent a more significant investment but are designed for demanding production environments, offering superior speed, precision, automation, and flexibility. They are typically chosen by fabricators with high-volume output, stringent quality requirements, or the need for integration into larger automated production lines.
Typical Characteristics and Advantages
- High Speed and Efficiency: Capable of significantly higher coiling and strapping rates, maximizing throughput.
- Enhanced Precision and Consistency: Utilize advanced sensors, servo motors, and controls for precise coil dimensions, cut lengths, and strap tension.
- Greater Flexibility and Automation: Often feature automatic changeovers for different tube/coil sizes, recipe storage via user-friendly HMIs, and sophisticated fault detection.
- Superior Durability and Reliability: Built with high-quality components designed for continuous operation and extended lifespan.
- Integration Capabilities: Designed for seamless connection with upstream (extruders) and downstream (palletizers, conveyors) equipment, supporting Industry 4.0 initiatives.
- Advanced Data & Diagnostics: Offer comprehensive production data logging, remote monitoring, and predictive maintenance alerts.
Potential Considerations
- Higher Initial Cost: Require a significantly larger capital outlay.
- Increased Complexity: May necessitate more specialized training for operation and maintenance personnel.
- Potential Overcapacity: Capabilities might exceed the needs of very small or low-volume operations.
Key Feature Deep Dive: Budget vs. High-End Comparison
Let's examine how specific functionalities differ:
1. Coiling Speed and Accuracy
- Budget: Often rely on simpler drive mechanisms. Coil dimensions might have wider tolerances. Speed might be limited (e.g., 1-3 coils/minute). Tension control can be basic.
- High-End: Employ servo-driven winding heads for precise speed, tension control, and layering. Achieve higher speeds (e.g., 4+ coils/minute) with tight dimensional accuracy. Offer programmable winding patterns.
2. Cutting Mechanism Precision
- Budget: May use basic pneumatic shear cutters. Cut quality might vary slightly.
- High-End: Utilize advanced cutting technologies (e.g., servo-driven blades, specialized shears) for clean, square cuts with minimal tube deformation, essential for subsequent fitting assembly.
3. Strapping System Reliability
- Budget: Standard strapping heads, potentially requiring more frequent adjustment or maintenance. Limited options for strap placement or number.
- High-End: Robust, high-speed strapping heads designed for high cycle rates. Precise, repeatable strap tensioning. Often offer programmable strap numbers and positions per coil.
4. Control Systems and Automation Level
- Budget: Basic PLC with limited HMI functionality. Manual parameter input is common. Diagnostics may be limited to simple error codes.
- High-End: Advanced PLC with intuitive touchscreen HMI. Features include recipe management, detailed diagnostics, production data logging, user access levels, and potential for remote access/support.
5. Integration and Material Handling
- Budget: Typically operate as standalone units. Integration might require custom interfacing. Basic exit conveyors or manual coil removal.
- High-End: Designed with standard communication protocols (e.g., OPC-UA, Ethernet/IP) for easy integration into plant-wide control systems (MES/SCADA). Offer automated coil handling options like transfer conveyors, accumulation tables, or robotic palletizing interfaces.
plastic pipe coil wrapping machine Crucial Selection Criteria for Your Operation
Beyond the budget vs. high-end distinction, consider these factors when choosing a system:
- Required Throughput: How many coils per hour/day do you need to produce?
- Tube Specifications: What are the diameter ranges, wall thicknesses, and materials (PU, PE, other) you handle?
- Coil Specifications: What are the required inside/outside diameters, traverse widths, and lengths of the finished coils?
- Strapping Needs: How many straps per coil? Specific placement or tension requirements?
- Automation Level: Do you need standalone operation or integration with other equipment?
- Labor Availability: Consider the ease of operation and maintenance requirements versus available skilled personnel.
- Floor Space: Ensure the machine's footprint fits your available area.
- Total Cost of Ownership (TCO): Factor in initial cost, energy consumption, maintenance, potential downtime, and expected lifespan.
Conclusion: Making the Informed Choice
Selecting the right PU/PE tube coiling and strapping system is a strategic decision. There is no single "best" answer; the optimal choice hinges on a thorough evaluation of your specific production needs, budget, and long-term goals.
- Budget-friendly systems provide an accessible entry into automated coiling and strapping, suitable for lower volumes or less complex requirements. They fulfill the basic need efficiently but may present limitations in speed, flexibility, and long-term durability under heavy use.
- High-end automated systems offer significant advantages in speed, precision, flexibility, and integration for demanding, high-volume environments. While the initial investment is higher, the potential gains in throughput, reduced labor, improved quality, and lower TCO over time can justify the cost for the right application.
Carefully analyze your current production data and future growth projections. Consider conducting a TCO analysis comparing potential options. Engaging with equipment manufacturers, discussing your specific application, and potentially requesting demonstrations or trial runs can provide valuable insights. By making an informed decision based on your unique operational context, you can implement a PU/PE tube packaging solution that enhances efficiency, protects your product, and supports your business objectives.