Modern Packaging Solutions for the Steel Industry: The Advantages of Automation
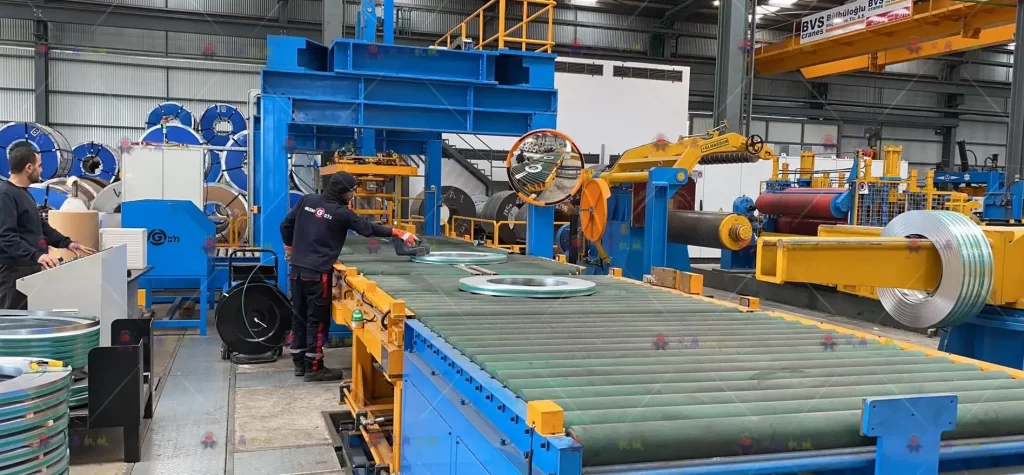
In the demanding environment of steel manufacturing, efficient and safe packaging is crucial. The industry frequently handles large, heavy, and irregularly shaped products like coils, sheets, pipes, and rods, presenting unique packaging challenges. While manual processes were once standard, the drive for greater efficiency, precision, and workplace safety has spurred the adoption of automated packaging systems. These modern solutions offer streamlined workflows and significant advantages, reshaping steel packaging operations.
This article examines how contemporary automated packaging solutions are enhancing the steel industry. We will delve into the specific benefits related to operational efficiency, cost reduction, improved safety protocols, and consistent quality control. Whether evaluating an upgrade to your current packaging lines or exploring the potential of automation, this guide offers key insights into leveraging technology for better performance.
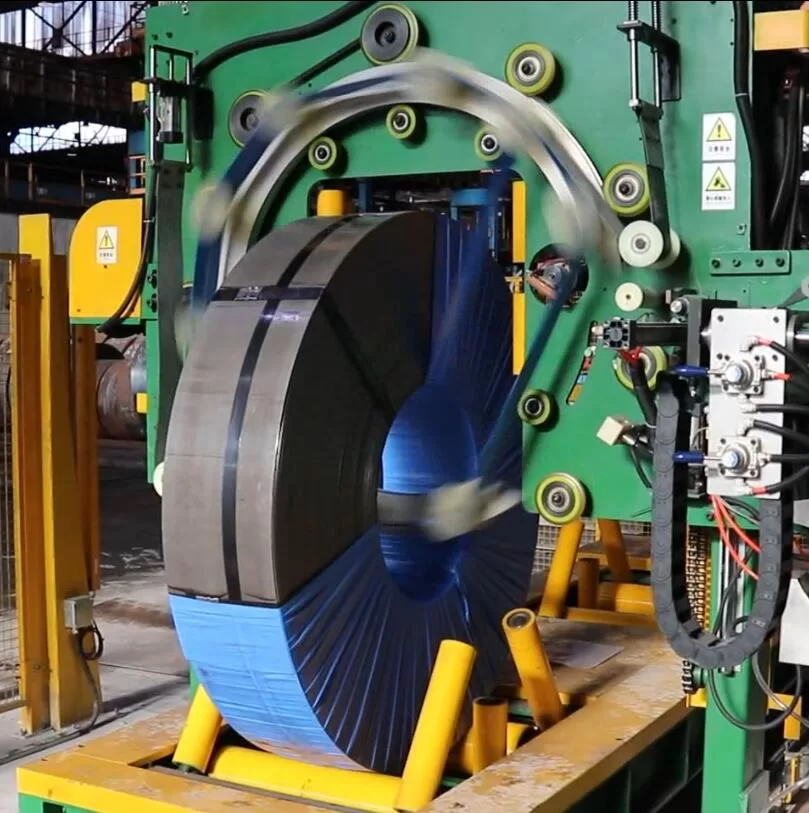
1. The Imperative for Automation in Steel Packaging
The steel industry operates on a scale defined by large volumes and substantial weight, necessitating robust handling and packaging protocols. Traditional manual packaging methods involve multiple steps – lifting, wrapping, strapping, and securing products – often leading to several operational bottlenecks:
- High Labor Intensity: Manual packaging demands considerable workforce allocation, increasing labor costs and the likelihood of human error during repetitive tasks.
- Significant Safety Risks: Handling heavy steel products manually elevates the risk of serious workplace injuries, including strains, sprains, and crush incidents. Adherence to safety regulations (like those from OSHA or equivalent bodies) becomes more complex.
- Inconsistent Packaging Quality: Manual application can result in variations in wrap tension, strap placement, and overall package integrity, potentially leading to product damage during transit.
- Throughput Limitations: Manual processes inherently limit the speed and volume of products that can be packaged, hindering scalability.
As global steel demand fluctuates and competition intensifies, manufacturers seek methods to optimize operations while upholding stringent safety and quality standards. Automated packaging solutions provide a technologically advanced alternative, delivering speed, reliability, and consistency that manual labor cannot match.
2. Key Advantages of Steel Packaging Automation
Migrating to automated systems provides tangible operational benefits that extend beyond simply modernizing processes. Here are the primary advantages automation introduces to steel packaging:
2.1 Enhanced Operational Efficiency
A primary benefit of automated packaging systems lies in their speed and unwavering consistency. Unlike human workers, machines maintain performance levels over extended periods without fatigue. This translates to:
- Reduced Packaging Cycle Times: Automated equipment, such as wrapping or strapping machines, performs tasks significantly faster than manual methods.
- Increased Throughput Capacity: More steel products can be processed and prepared for shipment per shift, enabling facilities to meet higher production targets and customer demands effectively.
- Optimized Labor Deployment: Automating repetitive packaging tasks frees up personnel for more complex, value-added responsibilities like quality assurance, machine oversight, and process optimization.
For instance, an automated steel coil wrapping machine uses sensors and programmed logic to apply protective wrapping consistently and securely, minimizing material waste and ensuring optimal protection without manual intervention. This accelerates the entire packaging sequence.
2.2 Improved Workplace Safety
Safety is non-negotiable in heavy industries like steel. Manual handling of steel components poses substantial risks. Automation mitigates these hazards by:
- Eliminating Hazardous Manual Tasks: Machines take over high-risk activities like lifting multi-ton coils, applying high-tension straps, and manipulating heavy packages, drastically reducing worker exposure to potential injuries.
- Ensuring Precision and Control: Automated systems operate with programmed accuracy, minimizing accidents often caused by fatigue, distraction, or misjudgment in manual operations.
- Enhancing Ergonomics: By removing the need for physically strenuous tasks, automation helps prevent work-related musculoskeletal disorders (MSDs), contributing to a healthier workforce.
Integrating solutions such as automated coil upenders, tilters, and pallet strapping systems ensures that even the most challenging loads are managed safely and efficiently, aligning with stringent occupational health and safety standards.
2.3 Long-Term Cost-Effectiveness
While the initial capital expenditure for automated packaging machinery can be significant, the long-term financial benefits often yield a strong return on investment (ROI). Key areas of cost savings include:
- Reduced Labor Costs: Automation decreases the reliance on manual labor for packaging tasks, leading to direct savings in wages, benefits, and training.
- Minimized Product Damage and Waste: Precise and consistent automated packaging reduces the likelihood of errors that can damage valuable steel products. Optimized use of packaging materials (like stretch film or straps) also cuts down on waste.
- Lower Operational Costs: Many modern automated systems incorporate energy-efficient designs and predictive maintenance features (often enabled by IoT), reducing energy consumption and minimizing costly unplanned downtime.
- Scalability: Automated lines can often be scaled more easily to handle fluctuations in production volume compared to adjusting manual workforce levels.
3. Core Technologies in Modern Steel Packaging Automation
The field of steel packaging automation leverages several advanced technologies to meet the industry's specific needs:
3.1 Robotics and Conveyor Integration
Industrial robots, particularly heavy-payload robotic arms, are essential for tasks requiring strength, precision, and repeatability. They excel at:
- Lifting and placing heavy steel items (e.g., billets, plates).
- Stacking finished products onto pallets.
- Applying protective elements or labels.
Integrated with smart conveyor systems (including roller, chain, or belt conveyors), robots enable a seamless, automated flow of materials through the entire packaging process, from production output to the final shipping stage.
3.2 Automated Wrapping and Strapping Systems
Securing steel products for transport is critical. Key automated systems include:
- Stretch Wrapping Machines: Orbital wrappers for long products (pipes, bars) or turntable/rotary arm wrappers for palletized coils or sheets apply stretch film tightly and consistently.
- Strapping Machines: Automated systems apply steel or high-strength plastic straps horizontally or vertically around coils, bundles, or pallets, ensuring load stability and security during handling and shipping. These can be integrated directly into the production line.
3.3 IoT and Data Analytics Integration
The Internet of Things (IoT) connects machinery, sensors, and control systems, enabling:
- Real-Time Monitoring: Tracking machine performance, material consumption, and potential issues.
- Predictive Maintenance: Analyzing sensor data (e.g., vibration, temperature) to anticipate potential failures and schedule maintenance proactively, reducing downtime.
- Process Optimization: Using operational data to fine-tune packaging parameters for maximum efficiency and minimal waste.
3.4 Machine Vision for Quality Control
Vision systems, often powered by Artificial Intelligence (AI), provide automated inspection capabilities:
- Verifying correct label placement and readability.
- Inspecting strap placement and tension.
- Detecting defects in wrapping or product positioning.
- Ensuring overall package integrity meets required standards before shipment.
These systems offer consistent, high-speed quality checks that surpass manual inspection capabilities.

4. Addressing Implementation Challenges
Despite the compelling benefits, transitioning to automation involves potential hurdles:
- Initial Investment: Automated systems require significant capital outlay. A thorough cost-benefit analysis, considering long-term savings and ROI, is essential. Financing options or phased implementation might be viable strategies.
- Workforce Adaptation: Employees may have concerns about job security. Effective change management, including transparent communication and robust retraining programs to develop skills for operating and maintaining automated systems, is crucial. Automation often shifts roles towards more technical and supervisory functions.
- System Integration: Integrating new automated equipment with existing production lines and IT systems (like ERP or MES) can be complex. Partnering with experienced automation providers is vital for smooth integration.
- Maintenance Requirements: Automated systems require specialized maintenance expertise. Companies need to invest in training internal staff or securing reliable external technical support.
5. Case Studies: Automation Success in Steel Packaging
(Note: The following are illustrative examples based on common industry outcomes. Specific results vary based on application and implementation.)
Case Study Example 1: Steel Coil Processing Center
- Challenge: A steel service center faced bottlenecks in its coil packaging line, relying heavily on manual wrapping and strapping, leading to inconsistent package quality and safety concerns.
- Solution: Implemented a fully automated packaging line including conveyors, an automated through-eye wrapping machine, and a radial strapping machine.
- Results: Achieved a 50% reduction in packaging cycle time per coil, improved package consistency significantly reducing transit damage claims by over 70%, and eliminated manual handling risks associated with strapping large coils.
Case Study Example 2: Steel Tube Manufacturer
- Challenge: A manufacturer of steel tubes struggled with efficiently bundling and strapping various product lengths and bundle sizes, leading to shipping delays.
- Solution: Integrated a robotic stacking system coupled with an automated horizontal strapping machine capable of adjusting to different bundle configurations.
- Results: Increased packaging throughput by 35%, reduced labor requirements for packaging by two personnel per shift (reallocated to quality control), and improved load security, enhancing customer satisfaction.
6. The Future Trajectory of Steel Packaging Automation
Automation in steel packaging continues to evolve. Future developments are expected to emphasize:
- Greater AI Integration: AI algorithms will enable smarter, self-optimizing packaging lines that can automatically adjust to variations in product dimensions, material types, and throughput demands, further enhancing efficiency and adaptability.
- Advanced Robotics: More sophisticated robots with enhanced sensing capabilities (vision, force-torque) will handle increasingly complex tasks and collaborate more safely alongside human workers (cobots).
- Sustainability Focus: Automation will play a key role in optimizing material usage (e.g., thinner gauge films, precisely applied straps) and energy consumption, supporting corporate sustainability goals and potentially reducing packaging costs. Data analytics will help track and minimize environmental footprint.
- Enhanced Connectivity: Deeper integration with supply chain management systems (using technologies like RFID or advanced tracking) will provide end-to-end visibility and traceability of packaged steel products.
Conclusion
Automation is no longer an optional upgrade but a strategic necessity for steel producers and processors seeking to thrive in a competitive global market. The benefits—improved operational efficiency, enhanced workplace safety, consistent quality, and long-term cost-effectiveness—are compelling. While implementation requires careful planning and investment, the adoption of automated packaging solutions enables steel companies to streamline critical operations, protect their workforce, reduce waste, and strengthen their market position.
Investing in modern steel packaging automation is an investment in resilience, productivity, and future growth.

Get Your Best Solution !