Understanding Heavy-Duty Inverters and Upenders for Industrial Material Handling
Handling large, heavy, or unwieldy loads is a common challenge across numerous industrial sectors. Safely and efficiently rotating or tilting these items—such as steel coils, paper rolls, engine blocks, or molds—requires specialized equipment. Heavy-duty inverters and upenders are crucial engineered solutions designed specifically for these demanding tasks, enhancing both operational efficiency and workplace safety.
This article explores the function, design considerations, and applications of heavy-duty industrial inverters and upenders.
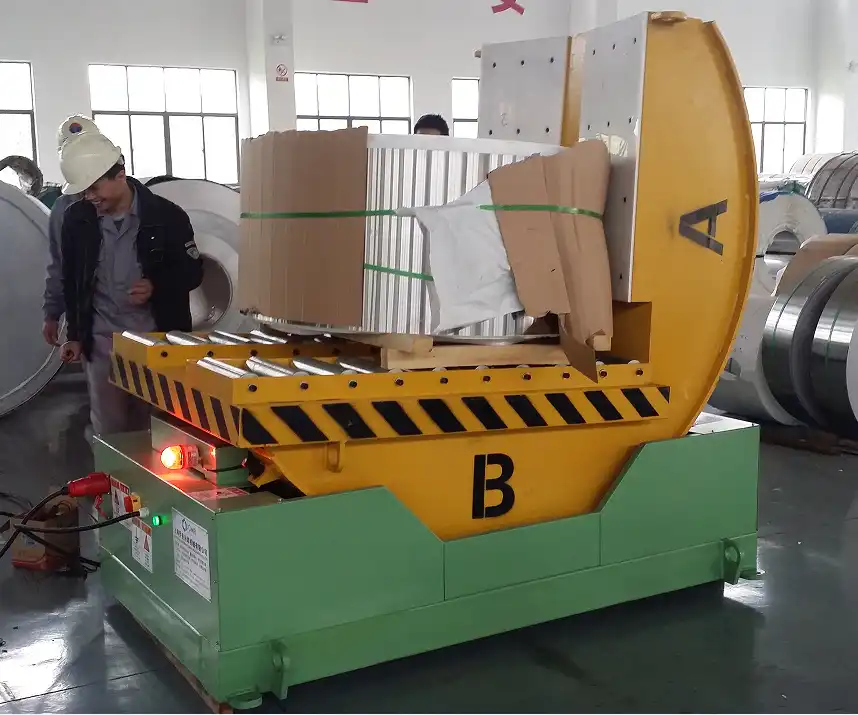
What Are Heavy-Duty Industrial Inverters?
A heavy-duty inverter, sometimes referred to as a load inverter or rotator, is designed to rotate a load, typically 180 degrees, around a horizontal axis. This capability is essential for tasks like:
- Inverting stacks of materials on pallets (pallet inverter).
- Turning over large molds or dies for maintenance or processing (mold inverter).
- Rotating large assemblies or components during manufacturing.
These machines must be built with robust components to handle significant weight and stress. Key design aspects focus on power, stability, and controlled movement to prevent load shifting or damage.
Watch this example demonstrating a heavy-duty inverter in action:
What Are Heavy-Duty Industrial Upenders?
Heavy-duty upenders, also known as tilters or downenders, are designed to tilt heavy loads, usually 90 degrees, changing their orientation from horizontal to vertical or vice versa. Common applications include:
- Tilting steel or paper coils from eye-to-sky to eye-to-the-wall orientation (coil upender).
- Positioning large fabrications or weldments for further processing or assembly.
- Handling heavy rolls or cylindrical objects safely.
Like inverters, upenders require robust construction and precise control systems to manage heavy, potentially unstable loads safely throughout the tilting cycle.
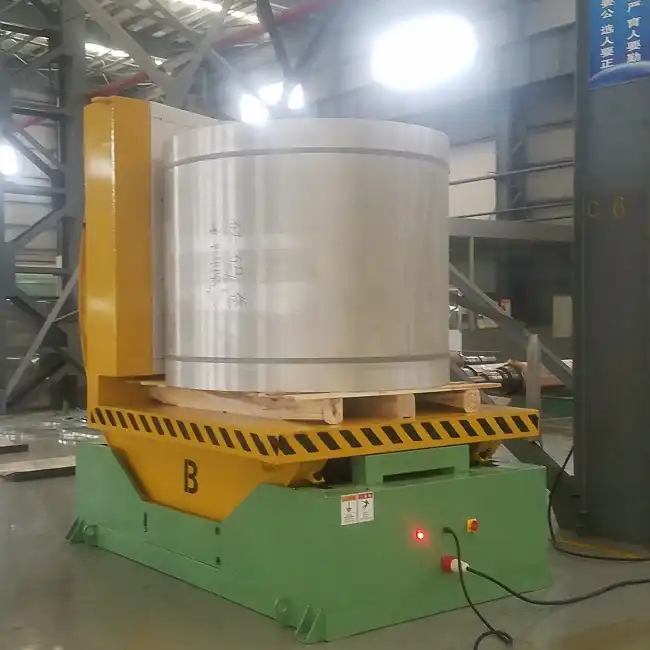
Key Design Considerations for Heavy-Duty Load Rotation Equipment
Building reliable and safe heavy-duty inverters and upenders requires careful engineering attention to several critical areas:
Structural Integrity
- Heavy-Grade Components: Utilize thick steel plates, reinforced frames, and oversized rollers, bearings, and shafts capable of withstanding high loads, impacts, and operational stresses without deformation or failure.
- Sturdy Base: Incorporate a wide, stable base or forklift pockets designed to properly distribute the weight of the machine and the maximum intended load, preventing tipping during operation.
Power and Drive Systems
- Hydraulic Systems: Often the preferred method for high-force applications. Heavy-duty hydraulic rams, pumps, valves, and cylinders provide the necessary power and control for smooth, consistent rotation or tilting of heavy loads.
- Electric Motors and Gearboxes: Oversized motors rated for continuous heavy-duty cycles, paired with robust gear reducers, provide the driving force for rotation or tilting mechanisms.
Safety Features
- Overload Protection: Integrate mechanisms (e.g., hydraulic pressure relief valves, motor current monitoring) to prevent operation if the load exceeds the machine's rated capacity.
- Locking Mechanisms: Positive locking systems are crucial to hold the load securely in position, especially during power loss or maintenance.
- Emergency Stops: Clearly marked and easily accessible emergency stop buttons are mandatory to halt machine operation immediately in hazardous situations.
- Sensors and Guarding: Proximity sensors, light curtains, and physical guarding can be incorporated to prevent personnel from entering hazardous zones during operation.
Durability and Maintenance
- Wear Resistance: Use abrasion-resistant materials, hardened bushings, wear pads, and durable coatings on surfaces that contact the load or experience friction.
- Sealing and Protection: Protect critical components, especially hydraulic systems and electrical enclosures, from environmental factors like dust, moisture, and contaminants.
- Maintenance Access: Design for reasonable access to lubrication points, inspection areas, and components requiring routine maintenance or repair.
Control Systems
- Operator Controls: Ranging from simple push-button pendants for manual operation to programmable logic controllers (PLCs) for automated cycles and integration with other factory systems.
- Optional Features: Consider features like variable speed control, automatic cycle initiation, load weighing systems, or data logging based on specific application requirements.
rotating coil upender Rigorous Testing
Before deployment, all heavy-duty load handling equipment must undergo thorough testing under simulated or actual maximum load conditions to verify its performance, safety features, and structural integrity. This ensures it can operate reliably and safely within its specified parameters in a production environment.
By understanding the functions and critical design elements of heavy-duty inverters and upenders, facilities can select and implement the right equipment to improve material handling processes, increase throughput, and significantly enhance operator safety when dealing with challenging loads.