Guide to Choosing the Right Mold Upender for Heavy Load Handling
Introduction: The Role of Mold Upenders in Heavy Load Handling
Mold upenders, also known as mold flippers or mold rotators, are indispensable pieces of equipment in industries dealing with large, heavy molds, such as plastics manufacturing, die casting, and automotive production. They provide a safe, controlled, and efficient method for rotating or tilting heavy molds for maintenance, inspection, or production purposes. Selecting the appropriate mold upender is critical for optimizing operational workflow, enhancing workplace safety, and protecting valuable tooling assets. This guide provides comprehensive insights into the key considerations for choosing the right machine, ensuring it meets your specific heavy load handling requirements.
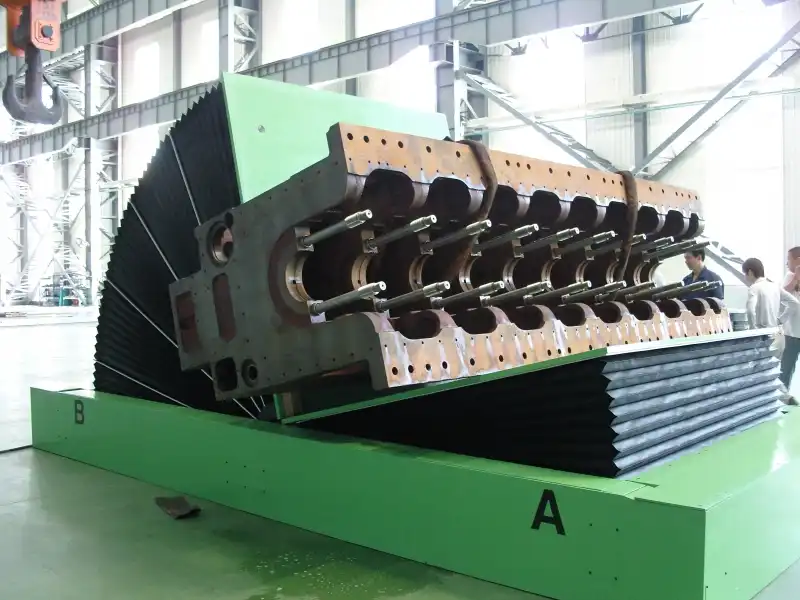
Essential Factors for Selecting a Mold Upender
Choosing the most suitable mold upender involves careful consideration of several critical factors related to your specific operational needs and the characteristics of the molds being handled.
1. Determining Load Capacity Requirements
The primary factor is the weight capacity. Accurately determine the maximum weight of the molds you need to handle. It's crucial to select a mold upender with a rated capacity that comfortably exceeds your heaviest mold, providing a safety margin. For heavy load handling, capacities often exceed 20 tons.
- Calculation: Include the weight of the mold itself plus any attached components (e.g., runners, cooling lines).
- Safety Margin: Opting for a capacity slightly higher than your maximum calculated weight accounts for potential future needs and reduces strain on the equipment.
- Consequences of Undersizing: Choosing an under-capacity machine poses significant safety risks, including equipment failure, mold damage, and potential injury to personnel.
2. Assessing Facility Space and Layout
Evaluate the physical space available in your facility where the mold upender will operate. Consider not only the footprint of the machine itself but also the necessary clearance for safe operation, loading, and unloading.
- Operating Footprint: Ensure sufficient room for the machine's full range of motion, including rotation or tilting.
- Loading/Unloading Zones: Allocate adequate space for forklifts, cranes, or other equipment used to place molds onto and remove them from the upender.
- Ceiling Height: Verify that there is enough vertical clearance, especially for upenders that tilt molds significantly.
- Compact Designs: If space is limited, inquire about compact mold upender models designed for tighter operational areas without compromising capacity or safety.
3. Prioritizing Critical Safety Features
Safety is paramount when handling heavy loads. Modern mold upenders incorporate various features designed to protect both the operator and the equipment. Look for machines equipped with:
- Robust Clamping Systems: Automatic or manual clamps that securely hold the mold in place during rotation, preventing slippage.
- Anti-Slip Surfaces: Platforms designed to provide high friction, ensuring the mold base remains stable.
- Emergency Stop Buttons: Easily accessible controls to immediately halt operation in case of an emergency.
- Limit Switches: Devices that prevent over-rotation or movement beyond safe operational limits.
- Safety Interlocks: Systems that prevent operation if safety guards are open or if the load is not properly secured.
- Warning Systems: Audible alarms or visual indicators during operation.
4. Evaluating Rotation Control and Precision
The ability to control the rotation speed and angle precisely is vital, especially when handling delicate, complex, or unbalanced molds.
- Variable Speed Control: Allows operators to slow down rotation for sensitive molds or speed up for robust ones, optimizing cycle times safely.
- Precise Angle Positioning: Ensures molds can be stopped accurately at specific angles (e.g., 90 degrees or 180 degrees) required for maintenance or setup.
- Smooth Operation: Hydraulic or electromechanical systems should provide smooth, jerk-free movement to prevent shock loads on the mold and the machine.
Understanding Mold Upender Innovations

Technological advancements continue to improve the efficiency, safety, and usability of mold handling equipment. Key innovations include:
- Automatic Load Balancing: Some advanced systems can detect and compensate for uneven weight distribution within the mold during rotation. This enhances stability, reduces stress on the machine components, and ensures a smoother, safer rotation cycle.
- Remote Control Interfaces: Wireless or pendant remote controls allow operators to manage the upending process from a safe distance, providing better visibility of the operation and keeping personnel away from the immediate vicinity of the heavy moving load.
- Integrated Sensor Technology: Sensors monitor various parameters during operation, such as mold position, clamping pressure, and rotation angle. This data can be used for automated adjustments, fault detection, and ensuring the process stays within safe operating parameters.
Ensuring Durability and Ease of Maintenance
A mold upender represents a significant investment, and its long-term reliability depends on robust construction and regular maintenance.
- Materials and Construction: Look for upenders built from high-strength materials like hardened steel or reinforced alloys, particularly in load-bearing components. Quality welding and construction techniques are essential for durability under continuous heavy use.
- Maintenance Access: Choose a design that provides easy access to key maintenance points, such as lubrication fittings, hydraulic components (if applicable), electrical panels, and drive mechanisms. This simplifies routine inspections and servicing, minimizing downtime.
- Maintenance Schedule: Adhere strictly to the manufacturer's recommended maintenance schedule. Regular lubrication, inspection of structural integrity, checking hydraulic fluid levels and filters, and inspecting electrical connections are crucial for longevity and safe operation.
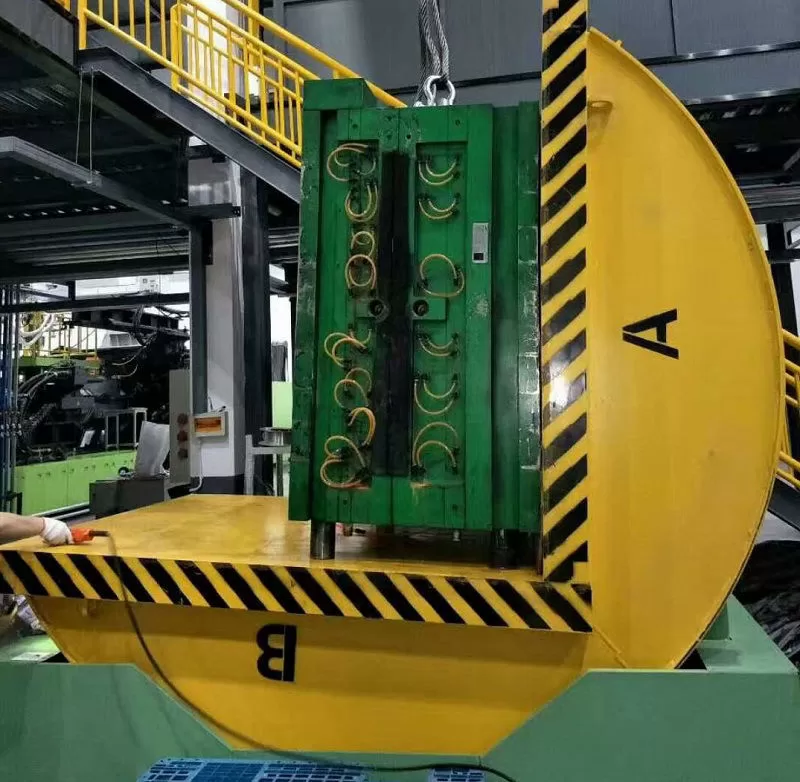
Adhering to Safety Standards and Compliance
Ensuring the mold upender complies with recognized safety standards is non-negotiable. Compliance protects your workforce, reduces liability, and ensures the equipment meets industry best practices.
- Key Standards: Verify compliance with relevant national and international standards. Depending on your location and industry, these might include:
- OSHA (Occupational Safety and Health Administration) regulations regarding general machine guarding and material handling (External Link: OSHA Machine Guarding Overview).
- ISO (International Organization for Standardization) standards related to machinery safety (e.g., ISO 12100).
- ANSI/ASME standards, particularly those related to material handling equipment and conveyors).
- Certification and Testing: Look for manufacturer certifications or third-party verification confirming the equipment has been tested to meet its rated capacity and complies with applicable safety standards. Request documentation detailing load testing and safety feature validation.
Conclusion: Making an Informed Mold Upender Choice
Selecting the right mold upender is a critical decision for any operation involving heavy mold handling. By carefully evaluating factors such as load capacity, operational space, safety features, rotation control, durability, and compliance with safety standards, you can choose a machine that enhances safety, improves efficiency, and provides reliable service for years to come.
Investing in a well-designed, appropriately sized mold upender equipped with modern safety and control features is essential for protecting your personnel, preserving valuable mold assets, and maintaining a productive manufacturing environment. Prioritize safety, consult with reputable manufacturers, and ensure the chosen equipment aligns perfectly with your operational demands.