Optimizing Bearing Protection: An Overview of Automated Wrapping Machinery
Proper packaging is crucial for protecting bearings during storage and transit. Bearings are precision components susceptible to damage from contamination, moisture, and physical impact. Automated bearing wrapping machinery offers a reliable and efficient solution to ensure these critical parts arrive at their destination in optimal condition.
Understanding the specific requirements of your bearings is the first step toward selecting the right packaging solution. Key factors include the bearing's dimensions, weight, and the necessary level of protection against environmental factors like corrosion.
Key Considerations for Bearing Wrapping Machines
When evaluating automated bearing wrapping solutions, several technical specifications are paramount:
- Size Capacity: Machines must accommodate the range of bearings being processed. Common adjustable parameters include:
- Outer Diameter (OD): Typical ranges might span from 250mm up to 550mm or more, depending on the model. For instance, some machines are designed for OD ranges like 300-500mm.
- Inner Diameter (ID): Corresponding ID capacity is critical, potentially ranging from 150mm to 400mm or larger.
- Width (Height): The machine must handle the bearing's width, often up to a maximum like 200mm.
- Machine Configuration: Depending on the application and space constraints, configurations can vary. While some models feature side cabinets for controls or material storage, others might be designed more compactly. Modifications to standard models are often possible to meet specific dimensional requirements, although this may involve engineering adjustments and potentially affect factors like usable film width or require multiple wrapping cycles for desired layering.
- Packaging Materials: The choice of wrapping material is vital for protection. Common options include:
- Stretch Film: Provides containment and some moisture resistance. Film widths (e.g., 50mm) and the number of layers applied impact the level of protection.
- VCI Paper/Film: Volatile Corrosion Inhibitor materials release compounds that prevent rust, essential for ferrous components during long-term storage or shipping in humid environments.
- Other Barrier Materials: Depending on the application, additional layers like crepe paper or specialized barrier films may be incorporated.
Referencing specific packaging material samples and requirements is crucial during the machine specification process.
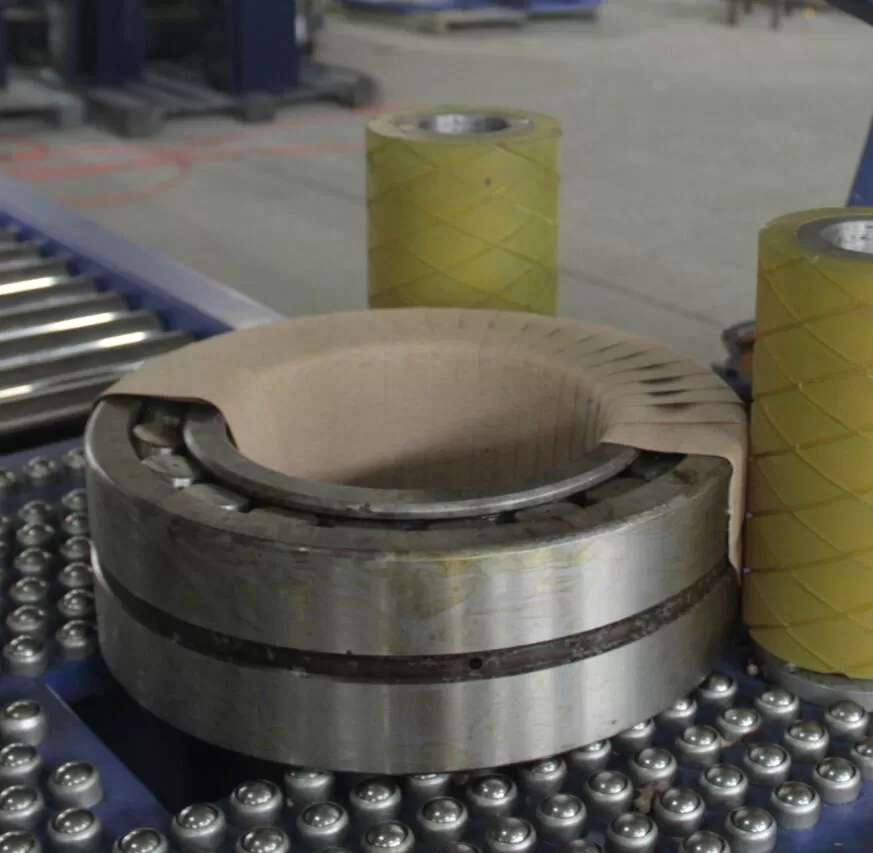
The Automated Wrapping Process
Automated bearing wrappers typically employ an orbital wrapping technique. The bearing is placed onto driven support rollers, which rotate the bearing. Simultaneously, a wrapping shuttle carrying the packaging material orbits through the center of the bearing, applying the film or paper circumferentially. This ensures consistent tension and overlap for a secure, protective wrap.
Benefits of Automation
Implementing an automated bearing packaging machine provides significant advantages:
- Consistency: Ensures uniform application of packaging materials every time.
- Efficiency: Increases throughput compared to manual wrapping methods.
- Protection: Provides a tightly sealed package, enhancing protection against contaminants and corrosion (especially when using VCI materials).
- Material Savings: Precise control over material usage and tension reduces waste.
- Labor Optimization: Frees up personnel for other value-added tasks.
Selecting the appropriate automated bearing wrapping machinery involves careful consideration of bearing dimensions, required protection levels, throughput needs, and integration with existing production lines. By automating this process, manufacturers can enhance product quality, improve operational efficiency, and ensure their bearings are adequately protected throughout the supply chain.