Enhancing Production: A Guide to Automatic Coiling Machines for Pipe and Hose
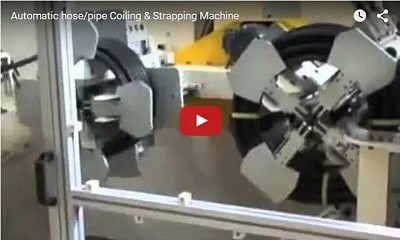
In modern manufacturing and fabrication environments, efficiency, consistency, and safety are paramount. For operations dealing with extensive lengths of pipe, hose, or tubing, manual coiling methods can be time-consuming, inconsistent, and pose ergonomic risks. Automatic coiling machines offer a robust solution, streamlining the process of winding these materials into neat, manageable coils for storage, transport, or further processing.
This guide explores the functionality, key components, and benefits of utilizing automatic coiling machines in industrial settings.
Understanding the Coiling Process: A Visual Example
Observing these machines in action provides the clearest understanding of their capabilities. The following video demonstrates a typical automatic coiling operation:
Automatic coiling machine for cable is at fhopepack

Core Components and Functionality of Automatic Coiling Machines
Automatic coiling machines integrate several sophisticated systems to achieve precise and efficient coiling. Key features typically include:
Coil Forming Arms and Mandrels
These are the primary mechanisms that physically shape the pipe or hose into a coil. The design allows for adjustments to accommodate various material diameters and flexibility characteristics. Advanced systems can automatically set the required coil inner diameter (ID), outer diameter (OD), and wrap spacing based on pre-programmed specifications, ensuring consistent coil dimensions.
Securing the Coil: Clamping and Strapping Systems
Once the desired length of material is coiled, integrated clamping mechanisms hold the coil securely in place. Often, these machines also incorporate automatic strapping or banding units that apply bands (typically plastic or metal) through the eye or around the circumference of the coil. This maintains the coil's integrity during subsequent handling, storage, and shipping, preventing unwinding.
Ensuring Quality: Tension Control Systems
Maintaining consistent tension as the material feeds into the coiling arms is critical for producing tight, uniform coils without damaging the product. Sophisticated tension control systems regulate the feeding speed and resistance, preventing buckling, kinking, or excessive stretching of the pipe or hose. This is crucial for maintaining the material's structural integrity and ensuring a high-quality end product.
Precision Handling: Pipe Guiding Systems
To ensure the material wraps evenly and concentrically onto the forming mandrel, specialized guiding systems are employed. These guides keep the pipe or hose properly aligned as it enters the coiling zone, contributing significantly to the final coil's neatness and stability.
Automation and Control: Programmable Logic Controllers (PLCs)
Modern automatic coiling machines are typically governed by Programmable Logic Controllers (PLCs). These industrial computers allow operators to input specific parameters (like coil length, diameter, number of straps) via a human-machine interface (HMI). PLCs enable automated adjustments for different product runs, store recipes for various pipe/hose types, and integrate the coiling machine with upstream and downstream equipment, enhancing overall line automation and flexibility.
Integrated Material Handling
Efficiency is boosted through automated handling features. This can include gripper arms to manage the leading end of the material, drive systems like sprockets or powered rollers to feed the material consistently, and conveyors or robotic arms to automatically discharge finished coils from the machine.

Post-Coiling Operations: Counting and Stacking
For high-volume production, some advanced coiling lines incorporate automated systems downstream. These can count the finished coils, stack them according to pre-set patterns, and even palletize them, minimizing manual labor requirements and preparing the products efficiently for warehousing or shipping.
Operational Safety Features
Safety is a primary design consideration. Automatic coiling machines are equipped with essential safety features such as emergency stop buttons, physical guarding around moving parts, safety interlocks on access doors, and often light curtains or area scanners to detect personnel presence and halt operation if necessary, ensuring operator protection.
Key Benefits of Automated Coiling
Implementing automatic pipe and hose coiling machines yields significant operational advantages:
- Increased Throughput: Automation drastically reduces cycle times compared to manual coiling, significantly boosting production output.
- Consistent Coil Quality: Machines produce uniform coils with precise dimensions and secure strapping, improving product presentation and handling.
- Reduced Material Waste: Accurate length measurement and controlled tension minimize scrap generated from inconsistent coiling or material damage.
- Improved Safety and Ergonomics: Automating the repetitive and physically demanding task of coiling reduces the risk of musculoskeletal injuries for operators.
- Lower Labor Costs: Reduced need for manual intervention allows personnel to be reallocated to more value-added tasks.
- Enhanced Integration: PLC controls allow seamless integration into larger automated production lines.
By investing in automatic coiling technology, manufacturers handling pipes, hoses, and similar materials can achieve greater efficiency, higher product quality, and a safer working environment, ultimately strengthening their competitive position.