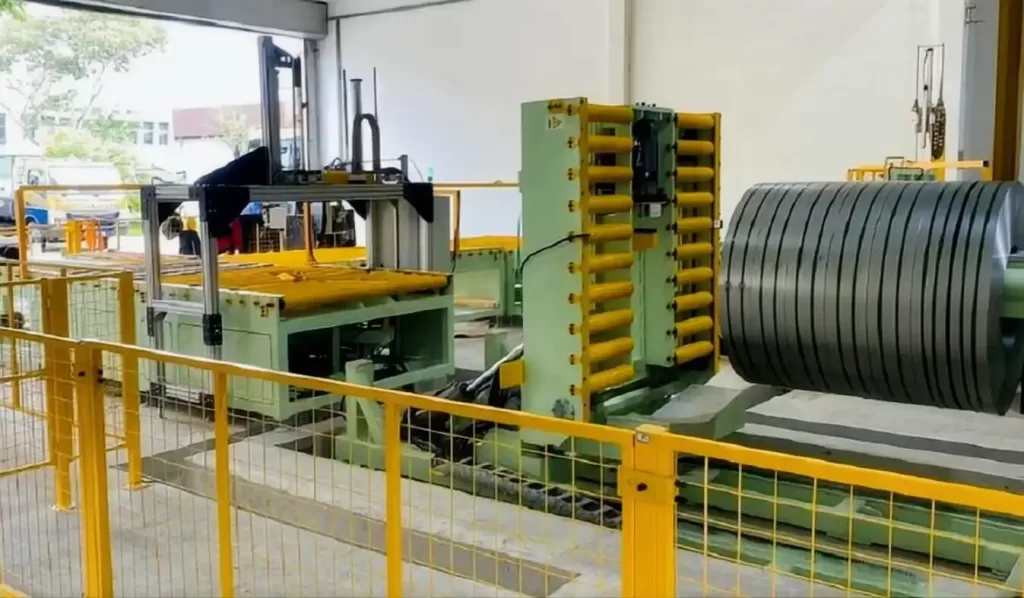
The landscape of steel wire packaging is rapidly transforming. Once dominated by manual bundling, the industry now relies on sophisticated, automated solutions engineered for unparalleled precision, speed, and efficiency. Today's cutting-edge technologies extend beyond mere packaging; they integrate advanced safety features, operational speed enhancements, and crucial sustainability practices, creating a comprehensive, modern process. This guide delves into the latest technological advancements and integrated solutions revolutionizing steel wire packaging, offering valuable insights into how these innovations are forging the industry's future.
For professionals involved in steel wire production and logistics, achieving high productivity, maintaining cost efficiency, and ensuring product integrity during transit are non-negotiable priorities. However, staying abreast of the rapid advancements in packaging machinery and integrated system solutions can be challenging. This guide simplifies these complexities, breaking down the most impactful technological developments in steel wire packaging lines and examining their potential impact on your operations.
Join us as we explore the innovations defining the next generation of steel wire packaging. We'll address key questions such as: What are the specific emerging technologies in this sector? How do advanced systems deliver both enhanced efficiency and operational cost savings? What crucial factors should guide your decision-making when considering an upgrade to a modern, integrated packaging system?
1. What is Automated Packaging, and How is it Revolutionizing Steel Wire Handling?
1.1 Understanding Automated Steel Wire Packaging Solutions
In steel wire manufacturing, automated packaging has transitioned from an operational luxury to a strategic necessity. Escalating global demand compels factories to boost throughput without compromising the quality and integrity of the wire products. Automated packaging systems utilize robotics, PLCs (Programmable Logic Controllers), and intelligent sensors to perform complex packaging sequences with minimal human intervention. These advanced solutions encompass a range of tasks:
- Automated coil handling and transport
- Precision orbital stretch wrapping
- Secure strapping (steel or PET)
- Accurate weighing and labeling
- Systematic palletizing and stacking
Automation significantly reduces errors inherent in repetitive manual tasks. With precisely calibrated movements and consistent operational parameters, automated systems handle more steel wire coils in less time, achieving uniform wrapping and strapping quality. However, a primary consideration is the significant upfront capital investment required for purchasing and integrating these systems. Implementation can also necessitate temporary workflow adjustments and operator retraining.
1.2 The Rise of Robotics in Steel Wire Packaging Lines
The integration of industrial robots has dramatically accelerated and refined steel wire packaging operations. Robotic arms are particularly adept at applying consistent tension during wrapping and strapping, crucial for protecting delicate wire surfaces from damage or deformation. These versatile robotic systems can automatically adjust to handle various coil dimensions (ID, OD, width) and weights, ensuring each package conforms to strict quality specifications and maintaining product integrity throughout the supply chain.
Despite the clear advantages, implementing robotics involves a learning curve. Operators require specialized training to manage, troubleshoot, and safely interact with robotic cells. Furthermore, retrofitting robotics into existing, older packaging lines might pose compatibility challenges. Nevertheless, the substantial gains in productivity, consistency, and reduction in manual handling errors often provide a strong return on investment.
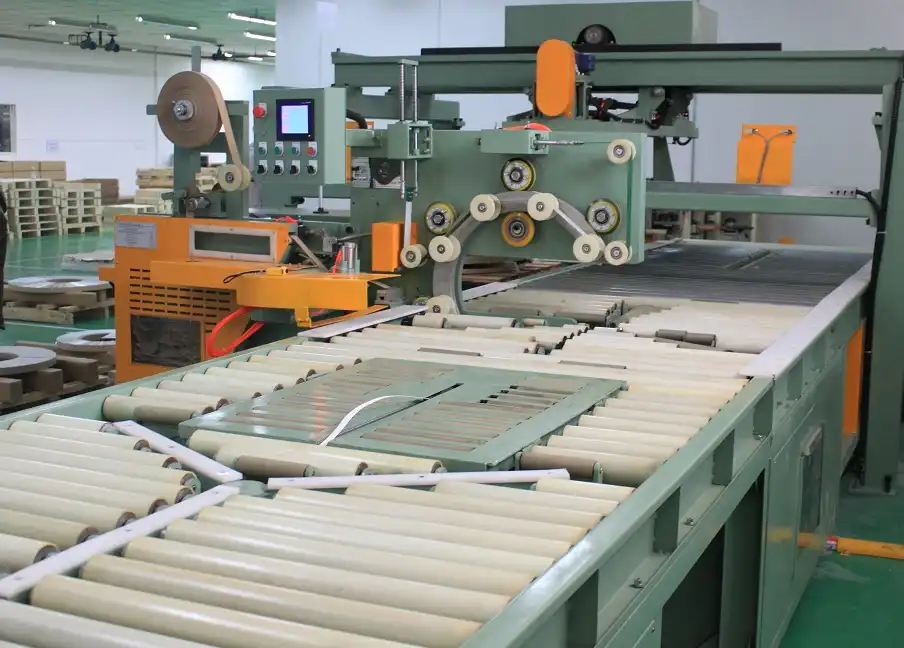
1.3 How Intelligent Sensors Enhance Process Efficiency and Quality
Intelligent sensors are indispensable components of modern automated steel wire packaging lines. These sensors continuously monitor critical parameters in real-time, including:
- Coil presence and position
- Coil dimensions (diameter, width) * Product weight verification * Wrapping film tension and usage * Strapping placement and tension * Machine operational status
This constant stream of data allows the control system to make instantaneous adjustments, optimizing packaging quality and material usage on the fly. For instance, sensors can detect coil misalignment or improper wrap tension and trigger corrective actions immediately, reducing the risk of defects that might be missed in manual inspections.
A key benefit of sensor integration is waste minimization. By precisely measuring coils and controlling material dispensing, systems ensure only the necessary amount of stretch film or strapping is applied, lowering material costs and reducing environmental impact. However, these sophisticated sensor networks rely on accurate calibration and robust software. They are also susceptible to environmental factors (dust, vibration) and require skilled technicians for maintenance and troubleshooting to ensure reliable performance.
2. How Are Advanced Safety Features Enhancing Modern Steel Wire Packaging Lines?
2.1 The Critical Importance of Safety Protocols in High-Speed Packaging
Safety is paramount in modern steel wire packaging environments, where heavy loads and automated machinery operate at high speeds. Manufacturers prioritize protecting employees while ensuring the integrity of the steel wire product. Today's packaging systems incorporate multiple layers of safety mechanisms, such as:
- Emergency stop buttons strategically placed around the line
- Physical guarding and safety fencing with interlocked access gates
- Light curtains and laser scanners creating safety zones
- Automated system shutdowns triggered by hazard detection (e.g., obstructions, overloads)
- Safety PLCs ensuring reliable control over safety functions
These integrated safety features are crucial for preventing accidents and minimizing risks associated with moving machinery, heavy coils, and potentially high-temperature processes (like certain wrapping techniques). They help ensure compliance with stringent occupational safety regulations like those from OSHA (Occupational Safety and Health Administration) or equivalent international standards.
A major advantage of robust safety protocols is the enhanced operator confidence and reduced risk exposure. Automated safety checks significantly decrease the likelihood of injuries resulting from machine malfunction or human error. However, the effectiveness of these systems hinges on regular inspection, testing, and maintenance. Neglecting safety system upkeep can lead to failures, resulting in potential injuries, costly equipment damage, and significant operational downtime.
2.2 Enhancing Worker Safety Through Automation and Ergonomics
Automation plays a pivotal role in improving worker safety by eliminating or reducing exposure to hazardous manual tasks. By automating physically demanding activities like lifting heavy steel wire coils, manually guiding wrapping materials, or positioning straps, modern packaging lines significantly reduce the risk of musculoskeletal injuries and accidents associated with manual handling.
- **Reduced Lifting Injuries:** Robotic arms, conveyors, and coil cars handle the transport and manipulation of heavy coils.
- **Minimized Repetitive Strain:** Automated wrapping and strapping cycles eliminate repetitive manual motions. * **Lower Exposure Risk:** Operators can supervise processes from safer distances, reducing exposure to moving parts or potential pinch points.
While automation drastically reduces physical strain and direct hazards, comprehensive training remains essential. Operators must be proficient in safely interacting with automated systems, understanding safety procedures, performing emergency stops correctly, and recognizing potential system malfunctions. Continuous training programs are vital to maximizing the safety benefits of automation.
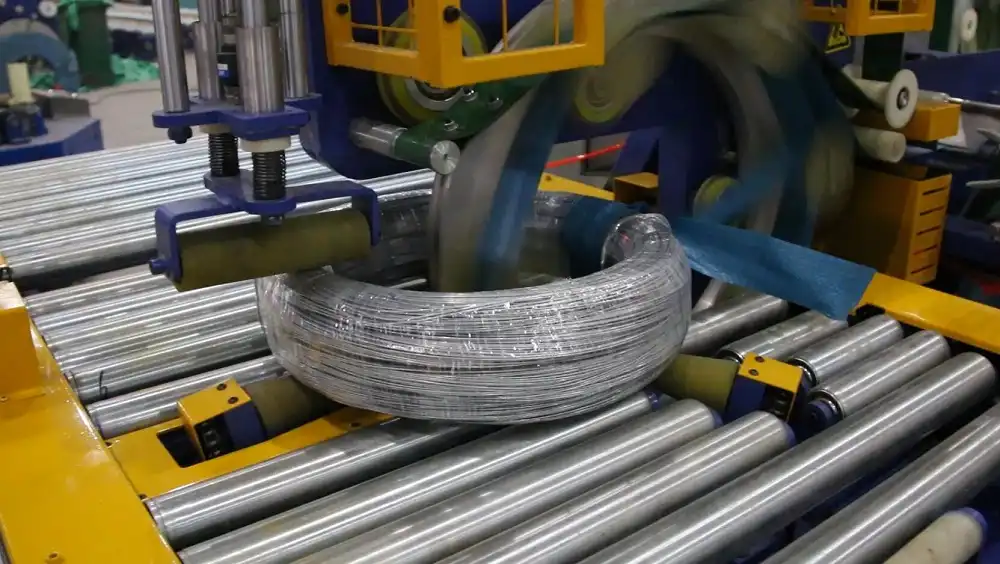
2.3 The Emerging Role of AI in Proactive Safety Monitoring
Artificial Intelligence (AI) and Machine Learning (ML) are beginning to offer powerful capabilities for proactive safety monitoring within steel wire packaging lines. AI-powered systems, often leveraging computer vision and sensor data analysis, can detect subtle anomalies that may indicate potential hazards:
- Identifying unusual vibrations or sounds from machinery that could precede a failure.
- Detecting unexpected objects or personnel entering restricted safety zones.
- Analyzing coil movement patterns for deviations that might signal instability.
- Predicting potential collision paths between robotic arms or automated guided vehicles (AGVs).
By analyzing vast amounts of historical and real-time operational data, AI algorithms can recognize patterns associated with potential failures or safety incidents. This allows for predictive warnings, enabling maintenance or intervention *before* a hazardous situation escalates. AI's ability to learn and adapt over time continuously refines its accuracy, potentially reducing false alarms while improving the detection of genuine threats. However, implementing AI for safety requires high-quality data, robust algorithms, and careful validation. Integration complexity and the need for ongoing updates are key considerations for adopting AI-driven safety systems.
3. What Role Does Data Analytics Play in Integrated Steel Wire Packaging Solutions?
3.1 How Data Analytics Drives Operational Efficiency and Throughput
Data analytics has become a cornerstone of optimizing steel wire packaging operations. By systematically collecting, processing, and analyzing real-time data from sensors, PLCs, and machine controllers across the packaging line, managers gain unprecedented visibility into operational performance. Key Performance Indicators (KPIs) that can be tracked and analyzed include:
- Overall Equipment Effectiveness (OEE)
- Cycle times per coil/package
- Material consumption (stretch film, straps)
- Machine uptime and downtime duration/causes
- Energy consumption
- Production rates versus targets
Interpreting these metrics allows companies to pinpoint bottlenecks (e.g., a slower strapping station), optimize resource allocation (e.g., adjusting film usage based on coil size), reduce waste, and ultimately enhance overall productivity and throughput. Data insights enable informed decision-making, moving from reactive adjustments to proactive optimization strategies.
The power to analyze operational data allows packaging lines to become more agile and responsive to changing production demands or material variations. This adaptability improves scheduling accuracy, reduces lead times, and minimizes waste generated from inefficient changeovers or suboptimal processing. However, unlocking the full potential of data analytics requires a robust data collection infrastructure (sensors, network connectivity), capable data storage and processing platforms (e.g., SCADA, MES), and potentially skilled personnel or analytics tools to interpret the data effectively.
3.2 Predictive Maintenance and Reducing Unplanned Downtime
One of the most valuable applications of data analytics in packaging lines is predictive maintenance (PdM). By analyzing data from sensors monitoring machine health parameters (e.g., vibration, temperature, motor current, cycle counts), advanced algorithms can detect patterns indicating potential component wear or impending failure. This allows maintenance teams to schedule interventions proactively *before* a breakdown occurs, rather than reacting after the line has stopped.
Key benefits of predictive maintenance include:
- **Significant Reduction in Unplanned Downtime:** Minimizing unexpected stoppages boosts productivity and schedule adherence.
- **Extended Equipment Lifespan:** Addressing minor issues early prevents catastrophic failures.
- **Optimized Maintenance Scheduling:** Maintenance is performed only when needed, reducing unnecessary interventions and costs.
- **Improved Safety:** Prevents failures that could create hazardous conditions.
Implementing predictive maintenance has enabled many manufacturers to achieve substantially higher levels of equipment uptime and operational reliability. However, effective PdM relies heavily on consistent, high-quality data streams and accurate predictive models. Failure to maintain sensors or update algorithms can compromise the system's accuracy, highlighting the need for ongoing system validation and refinement.
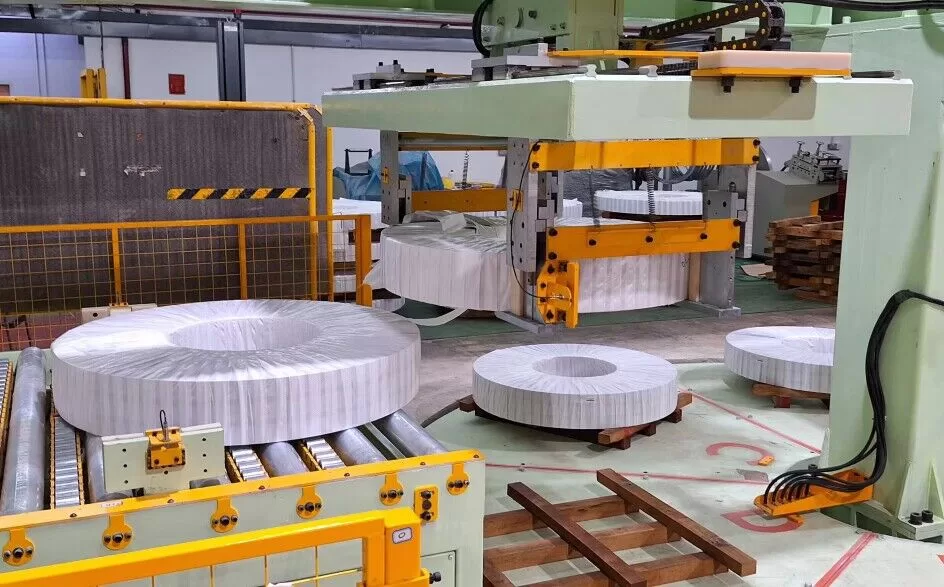
3.3 Real-Time Adjustments and Process Optimization via Data Feedback
Data analytics empowers packaging systems to make real-time adjustments, dynamically adapting to varying conditions or product requirements. For example, if sensors detect an incoming steel wire coil with slightly different dimensions or weight than the previous one, the system can automatically adjust parameters like:
- Conveyor speed
- Wrapping ring rotation speed
- Film overlap percentage
- Number of strap applications
- Label information
This capability for automatic, data-driven adjustments significantly reduces the time and potential errors associated with manual reconfigurations between different product runs, thereby increasing overall throughput and flexibility.
Furthermore, real-time data analytics enhances quality control. Continuous monitoring of parameters like wrap tension or strap placement ensures that each package consistently meets predefined specifications. Deviations can be flagged instantly, allowing operators or the system itself to take corrective action immediately. This closed-loop feedback mechanism minimizes defects and ensures high packaging quality. However, implementing effective real-time control systems requires robust communication networks (e.g., industrial Ethernet) and high processing power to handle the continuous data flow and execute adjustments without latency.
4. How Are Sustainability Initiatives Shaping the Future of Steel Wire Packaging?
4.1 The Shift Toward Eco-Friendly Packaging Materials
Driven by environmental regulations, corporate responsibility goals, and increasing customer demand for sustainable practices, the steel wire packaging industry is actively exploring and adopting eco-friendly materials. Key trends include:
- **Recycled Content:** Using stretch films and strapping materials containing higher percentages of post-consumer recycled (PCR) or post-industrial recycled (PIR) content.
- **Biodegradable/Compostable Options:** Investigating bio-based plastics or films designed to degrade under specific environmental conditions (though suitability for heavy industrial use is still under evaluation).
- **Paper-Based Alternatives:** Exploring the use of reinforced paper wraps or corner protectors as substitutes for plastic components where feasible.
- **Reduced Material Gauge:** Utilizing thinner yet stronger films and straps ("downgauging") to reduce overall plastic consumption without compromising package integrity.
- **Low-Emission Adhesives/Coatings:** Employing formulations with lower volatile organic compounds (VOCs).
Adopting sustainable materials helps companies meet environmental targets, reduce waste disposal costs, enhance brand image, and appeal to environmentally conscious customers. However, challenges remain. Eco-friendly materials can sometimes have higher initial costs, and their performance characteristics (e.g., strength, moisture resistance, durability) must be rigorously tested to ensure they provide adequate protection for heavy steel wire coils during handling and transport.
4.2 Energy-Efficient Machinery and Reducing Carbon Footprint
Modern steel wire packaging lines are increasingly designed with energy efficiency as a core principle. Manufacturers are incorporating technologies to minimize power consumption and reduce the overall carbon footprint of packaging operations:
- **Energy-Saving Motors:** Utilizing high-efficiency motors (e.g., IE3 or IE4 class) and variable frequency drives (VFDs) to match energy use to operational demand.
- **Optimized Machine Design:** Streamlining mechanical movements, using lighter-weight components where appropriate, and optimizing pneumatic/hydraulic systems to reduce energy loss.
- **Low-Voltage Controls:** Employing efficient control systems and LED lighting.
- **Sleep/Standby Modes:** Implementing automatic power-down sequences during idle periods. * **Energy Monitoring Systems:** Integrating sensors and software to track real-time energy consumption, enabling identification of high-usage areas and opportunities for further optimization.
Investing in energy-efficient machinery directly lowers operational electricity costs and contributes significantly to reducing a facility's environmental impact and greenhouse gas emissions. While these advanced machines often require a higher initial investment, the long-term savings in energy costs and potential eligibility for green incentives can provide a compelling financial justification.
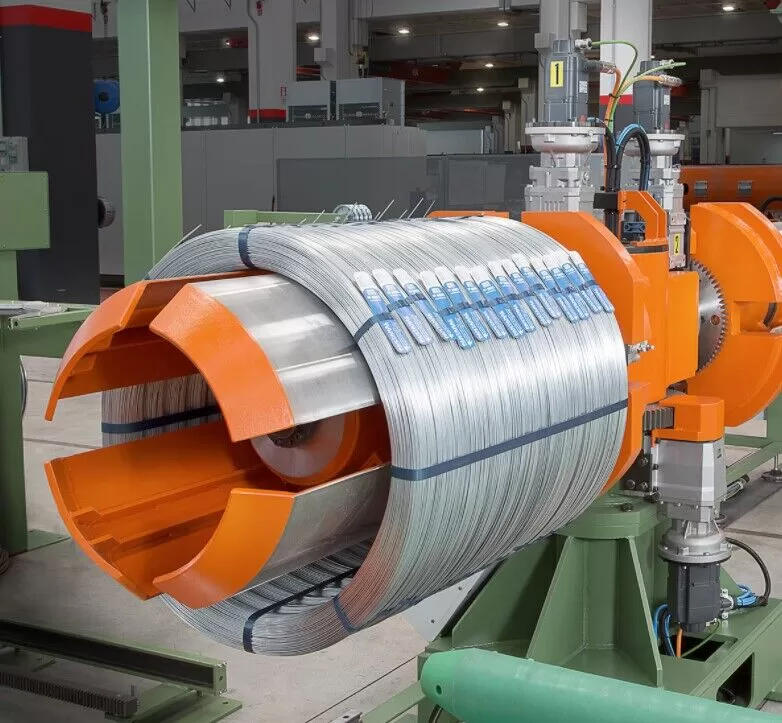
4.3 Waste Reduction Through Process Optimization and Circularity
Sustainability in steel wire packaging extends beyond materials and energy; it fundamentally involves minimizing waste throughout the entire process. Optimized operations, driven by automation and data analytics, play a crucial role:
- **Precision Material Usage:** Automated systems precisely measure coil dimensions and apply only the necessary amount of stretch film or strapping, eliminating overuse common in manual processes.
- **Reduced Product Damage:** Consistent, high-quality packaging minimizes damage during handling and transit, reducing the waste associated with rejected or scrapped wire products.
- **Minimized Changeover Waste:** Efficient setup and automatic adjustments between different coil sizes reduce material scrap generated during line changeovers.
- **Improved Recycling/Reuse:** Designing packaging for easier disassembly and using materials that are readily recyclable promotes circular economy principles. Some systems might facilitate the reuse of certain packaging components (e.g., pallets, frames).
Minimizing waste provides dual benefits: it lowers material procurement and disposal costs while significantly reducing the environmental footprint. Achieving optimal waste reduction often requires ongoing process audits, continuous monitoring via data analytics, and a commitment to identifying and implementing incremental improvements across the packaging line.
Conclusion: Embracing Innovation in Steel Wire Packaging for a Competitive Edge
The steel wire packaging industry is undergoing a significant technological evolution, profoundly shaped by advancements in automation, integrated safety systems, data analytics, and sustainable practices. Each of these pillars offers substantial advantages, ranging from dramatically enhanced operational efficiency and reduced costly downtime to vastly improved worker safety and environmentally responsible operations. Companies that strategically embrace these innovations not only optimize their current packaging performance but also position themselves as forward-thinking leaders equipped to thrive in an increasingly demanding and competitive global marketplace.
Successfully implementing these advanced technologies requires careful planning, strategic investment, and often, workforce development. While state-of-the-art automated and data-driven systems promise significant long-term savings and performance gains, they necessitate initial capital outlay and require personnel with the technical expertise to operate and maintain them effectively. Similarly, transitioning to more sustainable materials and energy-efficient machinery may involve upfront costs but can yield substantial returns through operational savings, enhanced brand reputation, regulatory compliance, and increased customer loyalty.
In summary, steel wire manufacturers and processors willing to invest in and adapt to modern packaging technologies—integrating automation, prioritizing safety, leveraging data insights, and committing to sustainability—will be best equipped to meet the rigorous demands of today's market, enhance their operational resilience, and build a strong foundation for future growth and success.

Get Your Best Solution !