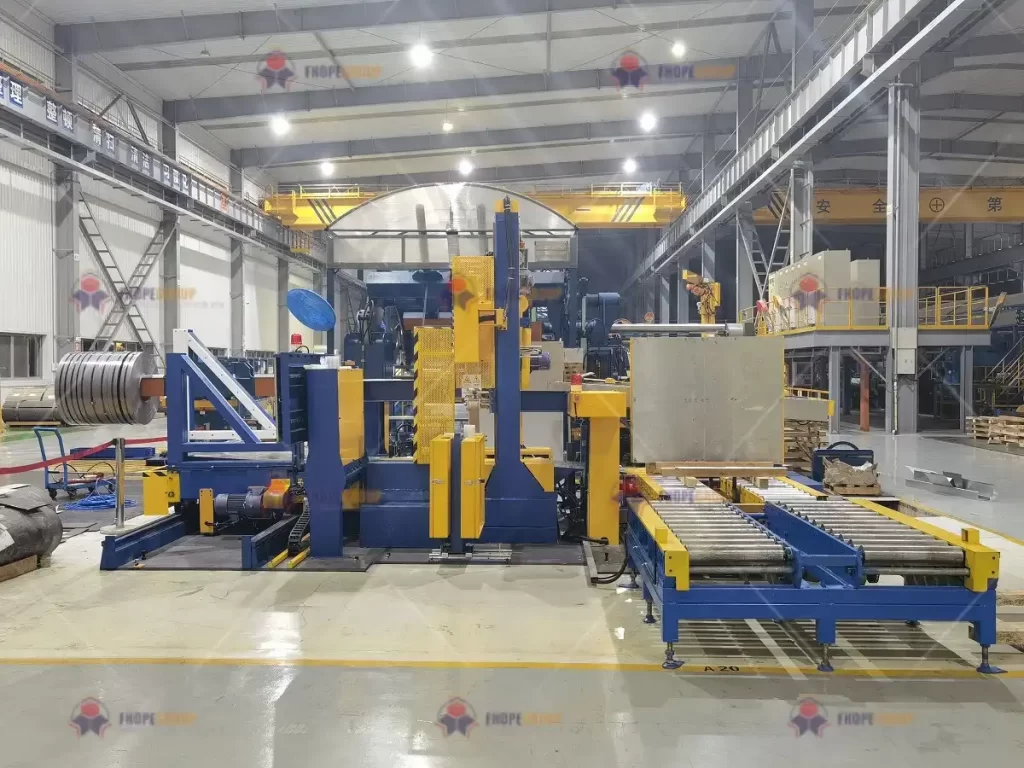
Steel coil packaging processes have significantly advanced over the past decade, driven by the need for greater efficiency, safety, and cost-effectiveness. Manufacturers increasingly rely on sophisticated automated systems and integrated solutions to remain competitive. This guide explores the latest technologies transforming steel coil packaging lines, focusing on automation, data analytics, and sustainability advancements that streamline operations and improve outcomes.
Modern steel coil packaging lines are complex systems integrating automated wrapping, material handling, quality control, and data management. Understanding these technological advancements is essential for manufacturers aiming to optimize their operations. Let's examine the key components and innovations shaping the industry today.
1. Key Components of Modern Steel Coil Packaging Lines
1.1 Advanced Material Handling Systems
Efficient material handling is fundamental to modern steel coil packaging. Current systems utilize sophisticated technologies for moving, positioning, and aligning heavy coils seamlessly. Key advancements include:
- Precision Control: Hydraulic and servo-controlled mechanisms provide precise, reliable movement and accurate orientation of coils, essential for consistent packaging.
- Automated Transport: Automated Guided Vehicles (AGVs) and multi-axis robotic arms are increasingly used for transporting coils between stations. This reduces reliance on manual labor, enhancing productivity and significantly lowering the risk of workplace injuries associated with handling heavy loads.
- Integrated Conveyors: Smart conveyor systems (discussed further below) ensure smooth transitions between different packaging stages.
1.2 Enhanced Wrapping and Strapping Technologies
The core wrapping and strapping processes have seen significant innovation. Modern systems offer greater control and efficiency:
- Customizable Wrapping: Advanced orbital stretch wrappers allow precise adjustments to wrapping parameters like film tension, overlap percentage, film thickness, and wrap speed. This ensures optimal coil protection using the minimum necessary material, reducing waste and cost.
- Intelligent Controls: Systems often feature sensors that detect coil dimensions (diameter, width) and weight, automatically adapting the wrapping or strapping cycle for optimal security and material usage.
- Durable Strapping: Automated strapping machines apply high-tensile steel or PET straps securely, essential for maintaining coil integrity during handling and transport. Integration ensures strapping occurs at the right point in the packaging sequence.
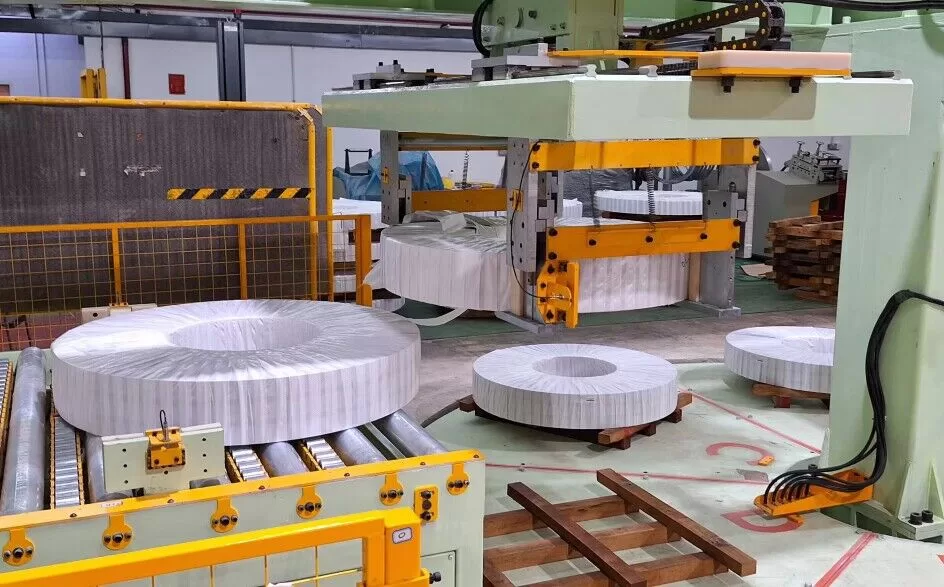
1.3 Integration of Automated Quality Control (QC)
Ensuring package integrity is crucial. Modern lines integrate automated QC systems:
- Vision Systems: High-resolution cameras and laser scanners inspect wrapped coils for defects such as incomplete coverage, tears in the wrapping material, improper strap placement, or misaligned labels.
- Sensor Integration: Sensors confirm proper positioning, wrapping tension, and strap application according to preset parameters.
- Real-Time Feedback: Detected issues trigger alerts, allowing operators to intervene immediately or enabling the system to automatically divert faulty packages. Data logged from QC checks contributes to process improvement analysis.
2. How Automation Enhances Efficiency in Packaging Lines
2.1 Advanced Robotics and Process Synchronization
Automation, particularly through robotics, dramatically streamlines steel coil packaging. Robots execute tasks like loading/unloading coils, applying protective materials, and palletizing with high speed and precision. Crucially, process synchronization ensures that each automated stage—material feeding, wrapping, strapping, labeling, inspection, and palletizing—operates cohesively. This coordinated workflow minimizes bottlenecks and idle time, maximizing throughput. Integration with Manufacturing Execution Systems (MES) or Enterprise Resource Planning (ERP) systems can further enhance synchronization across the entire production facility. Reduced human intervention leads to higher consistency, fewer errors, and improved workplace safety.
2.2 Intelligent Conveyor Systems
Modern conveyor systems are more than just transport belts; they are intelligent components of the automated line. Integrated sensors detect coil weight, dimensions, and position, allowing the system to automatically adjust conveyor speeds and spacing. This dynamic adaptation prevents collisions, ensures proper alignment for subsequent processes (like wrapping or labeling), and optimizes the flow based on real-time conditions. Variable speed controls help manage accumulation and prevent bottlenecks, ensuring smooth, continuous operation. IoT connectivity allows for remote monitoring of conveyor status and performance.
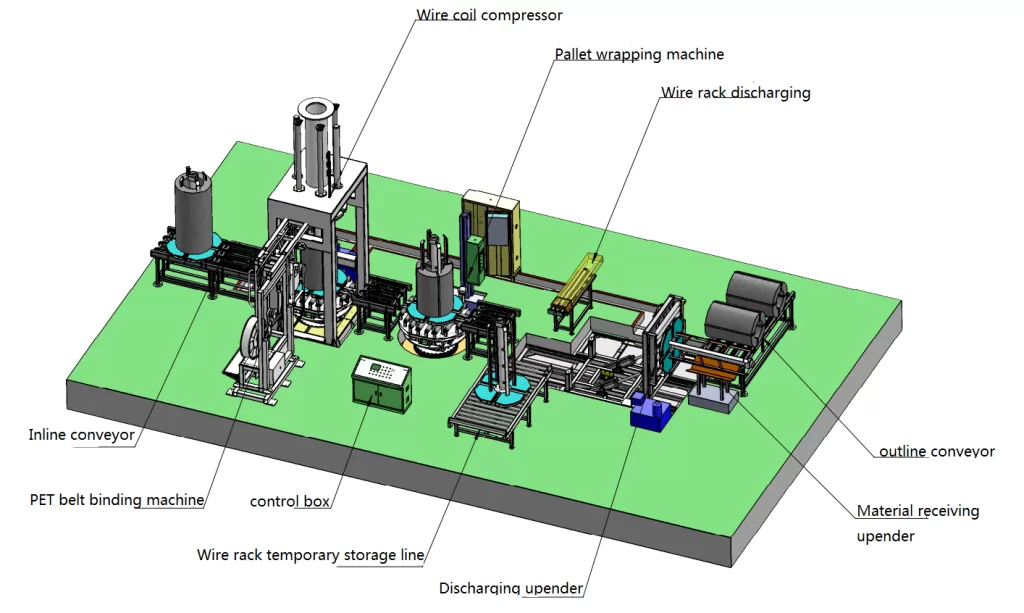
2.3 Predictive Maintenance through IoT
The Industrial Internet of Things (IIoT) enables predictive maintenance strategies, a significant improvement over reactive repairs. Sensors embedded in critical machinery components (e.g., motors, bearings, hydraulic systems, wrappers) continuously monitor operational parameters like temperature, vibration, pressure, and energy consumption. Advanced analytics process this data to detect subtle anomalies that often precede equipment failure. This allows maintenance teams to schedule repairs proactively, minimizing unplanned downtime, reducing repair costs, and extending the lifespan of valuable machinery. [*Optional: Add an external link here to a resource about IIoT in manufacturing or predictive maintenance.*]
3. Leveraging Data Analytics for Performance Improvement
3.1 Comprehensive Data Collection and Real-Time Monitoring
Integrated packaging lines generate vast amounts of data from sensors, machines, and control systems. This data includes:
- Production rates (coils per hour)
- Machine uptime and downtime duration/causes
- Material consumption (film, straps)
- Coil parameters (weight, dimensions)
- Quality control pass/fail rates and defect types
- Energy usage per machine or per coil
Real-time monitoring dashboards provide operators and managers with immediate visibility into line performance, enabling rapid identification and correction of inefficiencies or deviations from target KPIs.
3.2 Machine Learning for Predictive Insights
Machine learning (ML) algorithms analyze historical and real-time operational data to uncover patterns, predict future outcomes, and suggest optimizations. For example, ML models can:
- Predict potential equipment failures with higher accuracy (linking to predictive maintenance).
- Identify optimal machine settings (e.g., wrapping tension, conveyor speed) for different coil types or environmental conditions to maximize throughput and minimize material waste.
- Detect subtle process deviations that might lead to quality issues downstream.
- Forecast production throughput based on current conditions and upcoming schedules.
These data-driven insights empower manufacturers to make proactive adjustments, continuously improving efficiency, quality, and resource utilization.
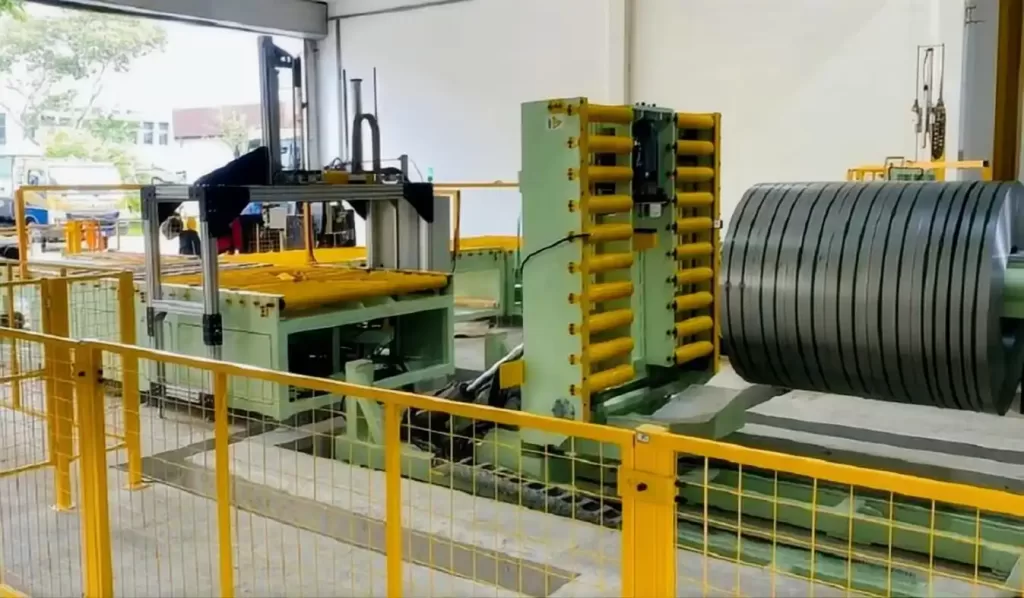
3.3 Enhancing Decision-Making with Data Visualization
Raw data becomes actionable intelligence through effective visualization. Dashboards displaying key performance indicators (KPIs) via charts, graphs, and alerts allow managers and operators to quickly grasp the operational status. Visual tools help in:
- Identifying trends in performance (e.g., gradual decrease in wrapping speed, increase in downtime).
- Pinpointing bottlenecks or underperforming equipment.
- Comparing performance across shifts, lines, or time periods.
- Facilitating data-backed discussions and collaborative problem-solving among different teams (operations, maintenance, quality).
Clear visualization supports faster, more informed decision-making for continuous improvement initiatives.
4. Sustainability Benefits of Integrated Packaging Solutions
4.1 Eco-Friendly Materials and Resource Optimization
Sustainability is increasingly important in manufacturing. Integrated packaging lines contribute through:
- Material Choice: Compatibility with eco-friendly packaging materials, such as thinner gauge stretch films with high puncture resistance, recyclable films, or biodegradable options, reducing environmental impact.
- Reduced Consumption: Precise control over wrapping tension and film pre-stretch capabilities significantly reduces the amount of film needed per coil without compromising protection. Automated strapping systems ensure optimal strap usage.
- Waste Minimization: Improved process control and quality checks reduce the number of improperly packaged coils that need rework or disposal, minimizing material waste.
4.2 Energy-Efficient Machinery Design
Modern packaging equipment is designed with energy efficiency in mind:
- Efficient Motors: Use of premium efficiency motors (e.g., IE3 or IE4 standards) and variable frequency drives (VFDs) on conveyors, wrappers, and robotic arms reduces electricity consumption.
- Smart Power Management: Features like automatic standby or sleep modes during periods of inactivity further conserve energy.
- Optimized Mechanics: Efficient designs in wrapping rings, conveyors, and hydraulic systems minimize energy loss.
Investing in energy-efficient machinery lowers operational costs and reduces the facility's carbon footprint, aligning with corporate sustainability goals. [*Optional: Add an external link here to a resource on energy efficiency standards for industrial machinery.*]

4.3 Sustainable Supply Chain Integration
Integrated packaging solutions extend sustainability benefits into the broader supply chain. Accurate tracking and data logging from the packaging line improve inventory management, reducing the risks of overproduction and associated waste. Digitized documentation (e.g., automated labeling and data transfer) minimizes paper usage. Furthermore, optimized packaging ensures better load stability and protection during transit, reducing product damage and the need for replacements, which carries its own environmental cost. Efficient logistics planning, aided by accurate packaging data, can also optimize transportation routes and fuel consumption.
Conclusion
The evolution of steel coil packaging lines centers on integration, automation, data intelligence, and sustainability. Innovations in material handling, wrapping technology, automated quality control, and robotics are driving significant improvements in efficiency, safety, and consistency. By leveraging IoT for predictive maintenance and data analytics for performance optimization, manufacturers can achieve substantial cost savings and operational excellence. Furthermore, the focus on energy-efficient machinery and resource optimization underscores the industry's move towards more sustainable practices. Adopting these advanced, integrated solutions is key for manufacturers seeking to maintain a competitive edge in the modern steel industry.

Get Your Best Solution !