Optimizing Steel Coil Packing Lines: A Deep Dive into Speed, Precision, and Efficiency
In the demanding environment of steel manufacturing and processing, the final packaging stage is crucial for protecting valuable coils during handling, storage, and transportation. An optimized steel coil packing line must perform reliably, balancing three critical factors: speed, precision, and overall efficiency. Understanding how these elements interact, especially when comparing traditional methods with modern automated solutions, is key to improving throughput, maintaining product quality, and reducing operational costs.
Caption: A modern wire coil wrapping machine exemplifies automation in packing lines.
Advances in automation and packaging technology have significantly transformed steel coil packing lines. As facilities strive for leaner operations and higher output, evaluating the performance gains offered by automation in terms of speed, consistency, and resource utilization becomes essential for strategic investment and process improvement.
This article explores these three performance pillars, contrasting manual or semi-automated approaches with fully automated systems to illustrate how manufacturers can achieve substantial gains in productivity, packaging quality, and return on investment.
1. Speed: Maximizing Throughput in Coil Packaging
Speed, measured in cycle time per coil or coils processed per hour, directly impacts a facility's overall throughput capacity. Faster packaging allows the line to keep pace with upstream production processes, preventing bottlenecks and enabling quicker order fulfillment.
- Traditional Methods: Manual or semi-automated lines often involve significant human intervention for wrapping, strapping, and handling. Cycle times can range from several minutes per coil, limited by operator speed, fatigue, and the sequential nature of tasks. This can hinder operations, especially during peak demand periods.
- Automated Solutions: Modern automated coil packaging lines leverage integrated conveyors, high-speed wrapping machines (often utilizing stretch film or VCI paper), and automated strapping systems (both radial and axial) to drastically reduce cycle times. Fully automated lines can often process a coil in under a minute, with some high-performance systems achieving cycle times as low as 30-40 seconds, depending on coil size and wrapping requirements.
Key Impacts of Increased Speed:
- Higher Throughput: Enables processing more coils per shift, directly increasing production capacity.
- Reduced Bottlenecks: Ensures the packing line does not impede upstream production or downstream logistics.
- Improved Responsiveness: Allows manufacturers to handle larger orders and meet tighter delivery schedules.
- Labor Optimization: Frees up personnel from repetitive manual tasks for other value-added activities.
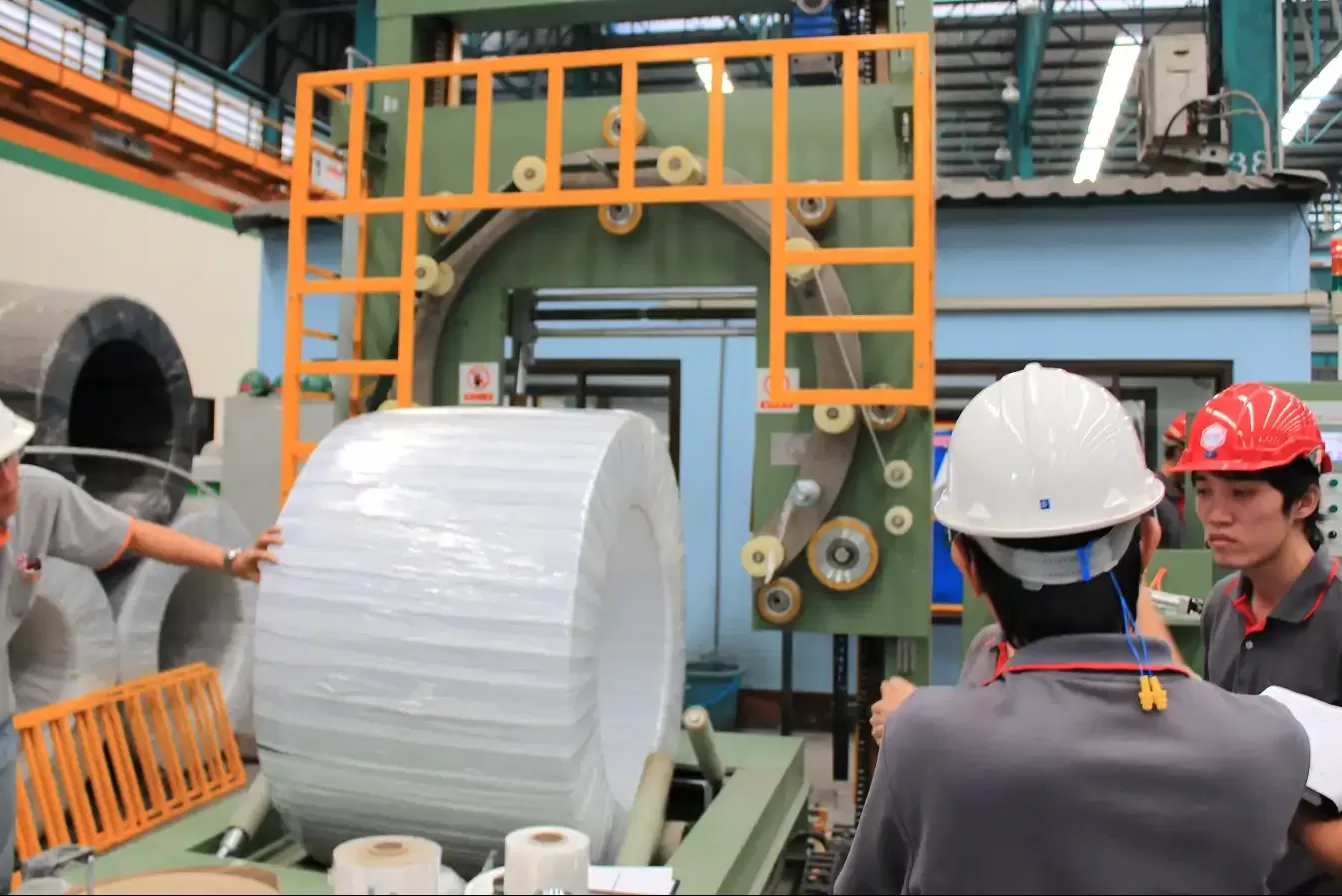
2. Precision: Ensuring Consistent and Protective Packaging
Precision refers to the consistency and accuracy of the packaging application. Proper packaging is vital to protect steel coils from physical damage (dents, scratches), environmental factors (moisture, corrosion), and shifting during transit. Imprecise packaging can lead to costly product damage, customer dissatisfaction, and safety hazards.
- Manual Challenges: Achieving consistent results manually is difficult. Factors like operator variability, fatigue, and subjective judgment can lead to:
- Inconsistent wrapping overlap or tension.
- Uneven strap placement or tension (too loose or too tight, potentially damaging edges).
- Incomplete coverage, leaving coil surfaces exposed.
- Automation Advantages: Automated systems excel at repetitive tasks with high accuracy.
- Robotic Wrapping: Applies stretch film or other materials with precisely controlled overlap, tension, and positioning, ensuring uniform coverage for every coil, regardless of size variations (within programmed limits).
- Automated Strapping: Applies straps at predetermined locations with consistent, calibrated tension, securing the coil effectively without causing damage. Sensors often verify strap placement and tension.
- Sensor Integration: Vision systems and sensors ensure correct coil positioning before and during packaging steps, minimizing errors.
Benefits of High Precision:
- Enhanced Product Protection: Reduces the risk of damage during handling and shipping.
- Material Optimization: Applies the exact amount of packaging material needed, minimizing waste and cost (e.g., optimizing stretch film usage).
- Improved Load Stability: Ensures coils are securely bundled for safe transport.
- Consistent Quality: Guarantees a uniform packaging standard for all products, enhancing brand perception.
3. Efficiency: Optimizing Resources and Minimizing Waste
Efficiency in a packaging line is a broader measure encompassing resource utilization, operational uptime, and overall cost-effectiveness. An efficient line maximizes output while minimizing inputs like energy, materials, labor, and time.
- Traditional Inefficiencies: Manual lines often suffer from lower efficiency due to:
- Higher labor requirements per coil.
- Increased potential for human error leading to rework.
- Inconsistent material usage (often over-application to be safe).
- Greater downtime associated with breaks, shift changes, and manual handling limitations.
- Automated Efficiency Gains: Automation enhances efficiency across multiple dimensions:
- Energy Consumption: Modern systems often incorporate energy-saving features like variable frequency drives (VFDs) on motors and sleep modes during idle periods.
- Material Usage: Precise application minimizes waste of stretch film, VCI paper, and strapping. Optimized wrapping patterns can significantly reduce consumption per coil.
- Labor Utilization: Automation reduces the need for direct manual labor in the packaging process, allowing staff to oversee multiple lines or perform other tasks.
- Reduced Downtime: Automated systems are designed for continuous operation. Integration with monitoring systems allows for quick fault identification.
- Process Integration: Seamless connection with plant-level control systems like Manufacturing Execution Systems (MES) or Enterprise Resource Planning (ERP) software enables real-time data tracking, performance analysis, and streamlined workflows. Data on throughput, material consumption, and uptime can drive continuous improvement efforts.

4. The Interplay Between Speed and Precision
Historically, increasing packaging speed sometimes came at the cost of precision. Rushing manual processes often leads to errors. However, modern automated steel coil packing lines are engineered to maintain high precision even at high speeds.
- Integrated Control Systems: Programmable Logic Controllers (PLCs) orchestrate the entire sequence, ensuring each step (conveying, lifting, rotating, wrapping, strapping) is performed accurately and in sync.
- Servo Motors and Actuators: Provide precise control over movement, speed, and tension for wrapping heads and strapping tools.
- Sensor Feedback Loops: Sensors constantly monitor parameters like coil position, film tension, and strap application, allowing the system to make micro-adjustments in real-time to maintain accuracy during high-speed operation.
Operators can typically adjust parameters via an HMI (Human-Machine Interface) to fine-tune the balance based on specific coil types or packaging requirements, ensuring that increased speed does not compromise the integrity of the final package.
5. The Role of Robotics in Enhancing Performance
Robotics plays an increasingly significant role in steel coil packing lines, further boosting speed, precision, and safety.
- Automated Handling: Robots can accurately pick up coils from production lines or storage areas and place them precisely onto the packing line conveyor or turntable. They handle heavy loads consistently without fatigue.
- Complex Strapping: Robotic arms can perform intricate strapping patterns, including placing straps through the inner diameter (ID) and around the outer diameter (OD), which can be challenging or time-consuming manually.
- Labeling and Marking: Robots can apply labels, tags, or ink-jet markings with high precision and consistency.
- Flexibility: Robots can often be reprogrammed to handle different coil sizes or packaging configurations, adding flexibility to the line.
- Safety: Automating heavy lifting and repetitive tasks reduces ergonomic risks and improves overall workplace safety.
6. Maximizing Uptime: Reliability and Maintenance Strategies
Downtime, whether planned or unplanned, directly impacts efficiency and throughput. Modern automated lines are designed for high reliability, but effective maintenance strategies are crucial for maximizing uptime.
- Robust Design: Equipment designed for heavy-duty industrial environments withstands wear and tear better.
- Predictive Maintenance: Utilizing sensors (e.g., vibration, temperature) and data analysis to predict potential component failures before they occur allows maintenance to be scheduled proactively during non-productive times.
- Real-time Diagnostics: Integrated monitoring systems provide immediate alerts for issues like material depletion (low film/straps), sensor faults, or mechanical problems, enabling faster troubleshooting and resolution.
- Modular Design: Components designed for quick replacement can significantly reduce repair times (Mean Time To Repair - MTTR).
Minimizing downtime is essential for achieving the full potential of a high-speed, high-precision packaging line.
7. Leveraging Smart Technology and Data Analytics
The integration of smart technology (IIoT - Industrial Internet of Things) provides unprecedented visibility and control over steel coil packaging operations.

- Data Collection: Sensors throughout the line gather real-time data on numerous parameters:
- Cycle times per station
- Material consumption (film weight, strap length)
- Energy usage
- Machine status and fault codes
- Coil identification and tracking
- Data Analysis: Analyzing this data helps identify bottlenecks, inefficiencies, and opportunities for optimization. For instance, tracking film usage per coil can reveal if tension settings need adjustment.
- Remote Monitoring: Allows managers and maintenance teams to monitor line performance and status remotely, facilitating quicker responses to issues.
- Process Optimization: Data insights enable fine-tuning of machine settings ("recipes") for different coil types, optimizing the balance between speed, precision, and material usage.
Smart technology transforms the packaging line from a standalone unit into an integrated, data-driven part of the manufacturing ecosystem.
8. Key Considerations for Optimizing Your Packing Line
Achieving the optimal balance of speed, precision, and efficiency requires careful consideration of specific operational needs when selecting or upgrading a steel coil packing line. Key factors include:
- Coil Specifications:
- Range of dimensions (ID, OD, width)
- Maximum weight
- Surface sensitivity (e.g., painted, galvanized, oily)
- Throughput Requirements:
- Target coils per hour or shift
- Peak vs. average production rates
- Packaging Requirements:
- Types of wrapping materials (stretch film, VCI, paper, poly)
- Strapping needs (material type, number/location of straps - radial/axial)
- Need for edge protectors, ID/OD protectors, labels
- Integration Needs:
- Connectivity with MES/ERP systems
- Integration with upstream/downstream conveyors and safety systems
- Operational Factors:
- Available floorspace
- Maintenance accessibility and required skill level
- Energy efficiency targets
- Economic Evaluation:
- Initial investment cost
- Ongoing operational costs (materials, energy, labor, maintenance)
- Return on Investment (ROI) based on increased throughput, reduced waste, and improved quality.
Consulting with experienced equipment manufacturers is crucial to designing a system tailored to specific requirements. For industry standards and best practices, resources like the Association for Iron & Steel Technology (AIST) can provide valuable information.
Caption: Precision wrapping is crucial for various coil types, including copper.
9. Conclusion: Investing in Optimized Steel Coil Packaging
In the competitive steel industry, an efficient, precise, and high-speed packaging line is no longer a luxury but a necessity. While traditional methods face inherent limitations, automated steel coil packaging systems offer significant advantages in maximizing throughput, ensuring consistent product protection, and optimizing resource utilization.
By leveraging technologies like robotics, advanced sensor systems, smart controls, and data analytics, manufacturers can achieve a superior balance of speed, precision, and efficiency. These systems streamline operations, reduce waste, enhance safety, and provide valuable data for continuous improvement.
Investing in modern automated packaging solutions represents a strategic move towards greater productivity, improved quality control, lower operational costs, and enhanced competitiveness in the global steel market. Evaluating current processes against the capabilities of modern automation is the first step toward unlocking significant performance gains in steel coil packaging.