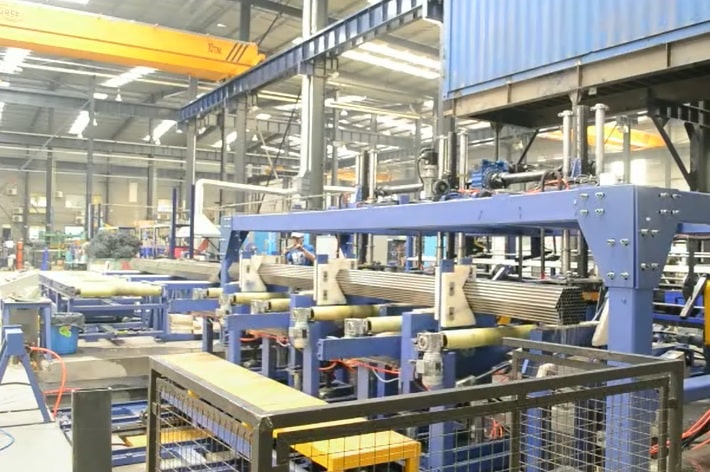
Evaluating Automated Steel Tube Packing Lines: Costs, Benefits, and Key Considerations
In modern steel tube and pipe fabrication and processing facilities, optimizing workflow for efficiency and product protection is paramount. An automated steel tube packing line represents a significant operational upgrade, streamlining the final stages before storage or shipment. However, understanding the investment involved versus the operational advantages gained is critical for informed decision-making. This guide examines the essential aspects of steel tube packing systems to help evaluate their suitability for your operation.
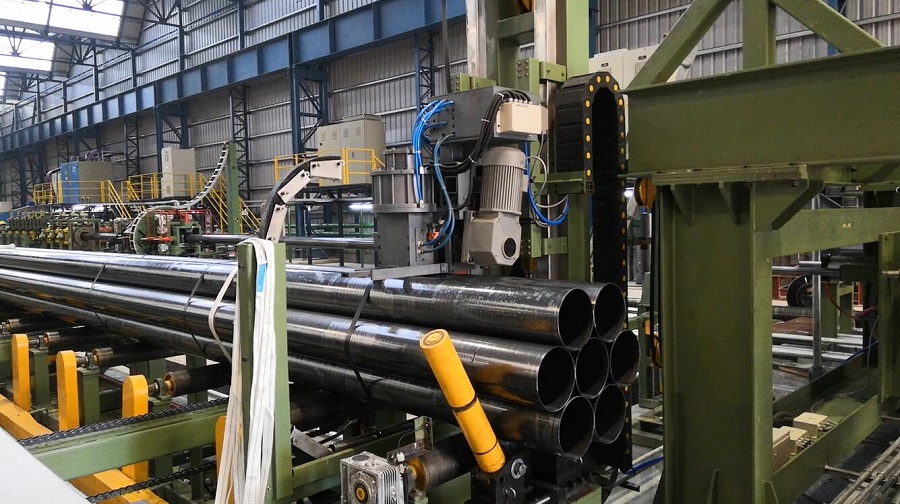
Understanding Steel Tube Packing Lines
What Comprises a Steel Tube Packing Line?
An automated steel tube packing line is an integrated system designed to prepare steel tubes or pipes for transport and storage with minimal manual intervention. These systems typically combine several functional modules, including:
- Conveying Systems: Transport tubes through the different stages.
- Counting and Arrangement: Accurately count tubes and arrange them into predetermined bundle shapes (e.g., hexagonal, square).
- Bundling/Strapping Stations: Securely apply steel or PET strapping around the bundle.
- Wrapping Systems (Optional): Apply stretch film or other protective wraps around the bundle for environmental protection.
- Weighing and Marking: Record bundle weight and apply necessary identification marks or labels.
- Discharge/Stacking: Move finished bundles to a storage or loading area.
Why Are Automated Packing Lines Important?
Manual packing of steel tubes is labor-intensive, time-consuming, and carries inherent safety risks. Automated systems address these challenges directly:
- Product Integrity: Consistent, secure packaging minimizes scratches, dents, and other damage during handling, transit, and storage.
- Operational Efficiency: Automation significantly increases throughput compared to manual methods, reducing bottlenecks between production and shipping.
- Labor Optimization: Frees up personnel from repetitive packing tasks to focus on higher-value activities.
- Enhanced Safety: Reduces manual handling of heavy tubes, lowering the risk of musculoskeletal injuries.
- Consistency: Ensures every bundle meets predefined packaging standards.
wrapper for steel tube Analyzing the Investment Considerations
Initial Capital Expenditure
The primary cost is the acquisition of the packing line machinery itself. This cost varies widely based on the line's complexity, speed, level of automation, and customization. Additional upfront costs include:
- Installation and Commissioning: Integrating the line into the existing facility layout.
- Operator Training: Ensuring personnel can operate and maintain the equipment effectively.
- Potential Facility Modifications: Ensuring adequate space, power, and compressed air supply.
Operational Costs
Ongoing expenses are a crucial part of the total cost of ownership:
- Energy Consumption: Power required to run motors, controls, and auxiliary systems.
- Consumables: Strapping materials, wrapping film, labels, etc.
- Maintenance: Routine servicing, spare parts, and potential technician costs. Well-maintained lines minimize costly unplanned downtime.
- Labor: While reduced compared to manual packing, skilled operators and maintenance staff are still required.
steel tube packing line2 Calculating Return on Investment (ROI)
A thorough ROI analysis should factor in projected savings from reduced labor, increased throughput, decreased product damage, lower consumable waste, and improved safety records against the total initial and operational costs. Many facilities find that the long-term benefits justify the initial investment, often realizing payback within a few years.
Evaluating the Operational Advantages
Increased Throughput and Efficiency
Automated lines operate continuously at speeds often unachievable manually, directly translating to higher output and the ability to meet demanding production schedules.
Improved Packaging Quality and Consistency
Automation eliminates human variability, ensuring each bundle is strapped or wrapped with consistent tension and placement, leading to better load stability and protection.
Significant Labor Savings
Reducing the number of workers required for packing duties leads to direct cost savings and allows for reallocation of labor resources.
Enhanced Workplace Safety
Minimizing manual lifting and handling of heavy or awkward steel tubes drastically reduces the potential for workplace injuries, contributing to a safer environment and lower insurance premiums.
Reduced Material Waste
Precise application of strapping and wrapping materials minimizes overuse and waste compared to manual methods.
Essential Features of Modern Tube Packing Lines
Customization and Flexibility
Lines should be adaptable to handle various tube diameters, lengths, wall thicknesses, profiles (round, square, rectangular), and bundle configurations required by the operation. Quick changeover capabilities are valuable for facilities processing diverse product ranges.
Advanced Technology Integration
Modern systems often incorporate:
- PLC Controls: Programmable Logic Controllers for reliable automation and process sequencing.
- HMI Interfaces: Human-Machine Interfaces for intuitive operation, monitoring, and diagnostics.
- Sensors and Vision Systems: For accurate tube detection, counting, and quality checks.
- Data Logging and Connectivity: Options for tracking production data (OEE, throughput) and integrating with plant-level Manufacturing Execution Systems (MES) or Enterprise Resource Planning (ERP) systems.
Durability and Reliability
Constructed for demanding industrial environments, high-performance packing lines utilize robust components designed for longevity and minimal downtime. Look for proven designs and quality manufacturing.
Integration Capabilities
The ability to seamlessly integrate the packing line with upstream processes (e.g., cutting, threading, coating) and downstream logistics (e.g., automated storage and retrieval systems) is crucial for maximizing overall plant efficiency.
Industry-Specific Considerations
Manufacturing and Processing Plants
Focus on matching packing line speed to production output to prevent bottlenecks. Integration with quality control checks can also be incorporated.
Service Centers and Distribution Hubs
Prioritize flexibility to handle a wide variety of tube sizes and bundle types efficiently. Packaging must ensure product protection during frequent handling and multi-modal transport.
Construction Material Suppliers
Need robust systems capable of handling large volumes and potentially heavier, longer tube bundles securely for transport to job sites.
Sustainability Considerations
Energy Efficiency
Look for systems designed with energy-efficient motors, drives, and operating modes (e.g., sleep modes during idle periods) to reduce operating costs and environmental footprint.

Sustainable Packaging Materials
Consider compatibility with recyclable strapping (e.g., PET) and explore options for minimizing wrap usage or using materials with recycled content. Efficient automation itself reduces material waste.
System Configurations: Manual, Semi-Automated, and Fully Automated
- Manual Packing: Lowest initial cost but highest labor requirement, lowest speed, and potential for inconsistency and injury. Suitable only for very low volume operations.
- Semi-Automated Systems: Combine automated modules (e.g., strapping) with manual steps (e.g., bundle forming). Offers a balance for medium-volume operations or budget constraints.
- Fully Automated Lines: Highest initial investment but delivers maximum efficiency, consistency, safety, and labor savings. Ideal for high-volume, continuous operations.
Key Factors When Choosing a Packing Line
- Throughput Requirements: Match the line's capacity to your current and projected production volumes.
- Tube Specifications: Define the full range of tube sizes, shapes, lengths, and weights to be processed.
- Bundle Specifications: Determine required bundle sizes, shapes, and strapping/wrapping needs.
- Budget and ROI Analysis: Align the investment with expected returns based on operational improvements.
- Available Facility Space and Layout: Ensure the line fits physically and integrates logically with material flow.
- Supplier Reputation and Support: Choose experienced suppliers with proven technology, installation expertise, training programs, and reliable after-sales service and parts availability.
steel tube packing line4 Conclusion
Implementing an automated steel tube packing line is a strategic investment that can yield substantial returns through increased efficiency, improved product protection, enhanced safety, and optimized labor utilization. While the initial cost requires careful consideration, the long-term operational advantages often provide a clear justification. By thoroughly analyzing specific operational needs, evaluating available technologies, and considering factors like ROI, space, and supplier support, manufacturers and processors can select a packing system that effectively supports their production goals and strengthens their competitive position.