Optimizing Slitting Coil Handling: Automated Packing and Palletizing Solutions
Slit coils, narrower rolls cut from a master coil of metal (often steel or aluminum), are fundamental materials in numerous manufacturing processes. However, handling these coils efficiently and safely presents significant challenges due to their weight, potentially sharp edges, and susceptibility to damage. Automating the handling, packing, and palletizing processes offers a robust solution to enhance productivity, improve worker safety, and ensure product integrity.
Key Challenges in Manual Slit Coil Handling
- Safety Risks: Lifting heavy coils manually poses ergonomic hazards and risks of injury.
- Product Damage: Improper handling can easily lead to scratches, dents, edge damage, or telescoped coils, impacting final product quality.
- Inefficiency: Manual processes are often slow, labor-intensive, and can become bottlenecks in production flow.
- Inconsistent Packaging: Manual wrapping or strapping can vary in tension and quality, potentially leading to load instability or insufficient protection.
The Automated Slitting Coil Packing and Palletizing Process
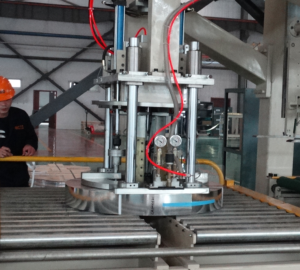
Automated systems are designed to streamline the entire workflow immediately following the slitting line. A typical integrated process includes several key stages:
- Coil Reception & Separation: Receiving individual slit coils from the slitter's turnstile or recoiler, often involving separation mechanisms.
- Conveying & Handling: Transporting coils safely via conveyors (belt, chain, or roller). This stage may include weighing and labeling.
- Orientation Control: Utilizing equipment like downenders, tilters, or upenders to position coils correctly (e.g., changing from eye-to-horizon to eye-to-sky) for subsequent packaging or stacking.
- Packaging:
- Wrapping: Applying protective stretch film around the coil's circumference for containment and protection against environmental factors.
- Strapping: Securing the coil using steel or PET straps. This can be done radially (through the eye) or circumferentially (around the outside diameter).
- Stacking: Carefully placing processed coils onto each other to form a stable stack. This is often performed by robotic arms or dedicated stacking units, sometimes incorporating separators (wood blocks or plastic spacers) between coils.
- Palletizing: Transferring the completed stack of coils onto a pallet, ready for storage or shipment. This may involve automated pallet dispensers and robotic palletizers.
Core Components of Automated Systems
A comprehensive automated line integrates various specialized machines:
- Coil Cars / Turnstiles: Receiving coils from the slitting line.
- Conveyors: Robust systems designed for heavy coil transport.
- Downenders / Tilters / Upenders: Machines for precise coil orientation changes.
- Circumferential Strapping Machines: Apply straps around the coil's outer diameter.
- Through-the-Eye Strapping Machines: Apply straps through the coil's inner diameter.
- Orbital Stretch Wrappers: Apply stretch film efficiently around the coil.
- Stacking Units / Robotic Arms: Automate the vertical stacking process.
- Pallet Dispensers: Automatically supply empty pallets.
- Robotic Palletizers: Place finished coil stacks onto pallets.
- Control Systems (PLC & HMI): Programmable Logic Controllers and Human-Machine Interfaces for system integration, operation, and monitoring.
Advantages of Automation in Coil Handling
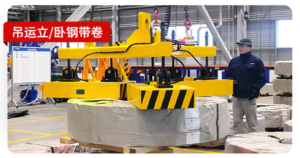
Implementing automated solutions provides significant benefits:
- Enhanced Throughput: Significantly faster processing speeds compared to manual operations.
- Improved Worker Safety: Minimizes manual lifting and reduces operator exposure to potential hazards associated with heavy, sharp-edged coils.
- Consistent Quality: Ensures uniform packaging (wrap tension, strap placement) and stable stacking, protecting product integrity.
- Reduced Labor Costs: Automates repetitive and physically demanding tasks, allowing personnel reallocation.
- Minimized Product Damage: Gentle and precise automated handling reduces the risk of scratches, dents, and deformation.
- Optimized Floor Space: Efficient layouts and vertical stacking capabilities can save valuable plant floor area.
- Data Integration: Systems can often integrate with plant-level ERP/MES for tracking and inventory management.
System Demonstrations: Testing and Operation
The following videos illustrate automated slitting coil handling and packing systems in different phases:
A. Slitting Coil Packing Line Testing and Checking
This video showcases a system undergoing pre-delivery testing and checks, verifying the functionality, sequence, and integration of components.
B. On-Site Running in Daily Operation
Observe a slitting coil packing line functioning within a production facility during routine daily operations, demonstrating real-world application and workflow.
Implementation Considerations
When planning for or evaluating automated slitting coil solutions, key factors include:
- Coil Specifications: Minimum and maximum coil Outer Diameter (OD), Inner Diameter (ID), width, and weight.
- Material Type: Steel, aluminum, copper, etc., as material properties can affect handling.
- Throughput Requirements: The number of coils needing processing per hour or per shift.
- Packaging Needs: Specific requirements for wrapping materials, strap types, number of straps, and placement.
- Stacking Configuration: Desired stack height, use of separators, and pallet type.
- Available Facility Space: Floor area, ceiling height, and layout constraints.
- Integration Points: Connection requirements with upstream slitting lines and downstream warehousing or shipping processes.
- Budget and ROI: Initial investment versus long-term savings in labor, efficiency gains, and reduced damage.
packaging solutions for steel and aluminum coils Conclusion
Automated slitting coil handling, packing, and palletizing systems represent a vital investment for modern metal service centers and manufacturing facilities focused on achieving higher levels of efficiency, safety, and product quality. By carefully analyzing specific operational needs and understanding the capabilities of available automation technology, companies can implement tailored solutions that significantly optimize their downstream coil processing operations.
For related machinery information, see: Automatic Coil Packing Machinery