Understanding Pallet Wrapping Machines with Top Press Devices
In modern warehousing and logistics, ensuring load stability during transit is paramount. While standard stretch wrappers are effective for many applications, certain types of loads require additional stabilization during the wrapping process. This is where a specialized type of automated packaging equipment comes into play: the pallet wrapping machine with a press down device, also known as a stretch wrapper with a top platen.
What is a Pallet Wrapping Machine with a Top Press?
A pallet wrapping machine fundamentally automates the application of stretch film around a palletized load, securing it for storage or shipment. The defining feature of the model discussed here is the integrated top press device (often a platen or pressure plate).
While the core function remains wrapping the load with film dispensed from a moving film carriage as the pallet rotates on a turntable, the top press adds a crucial step:
- Top Press Engagement: Before or during the wrapping cycle, the press device descends onto the top of the load.
- Stabilization: It applies consistent downward pressure, compacting and stabilizing the load while the stretch film is applied.
This contrasts with standard pallet wrappers that rely solely on the film's tension to secure the load. The pallet wrapping machine with press down device offers a proactive solution for inherently unstable or lightweight goods.
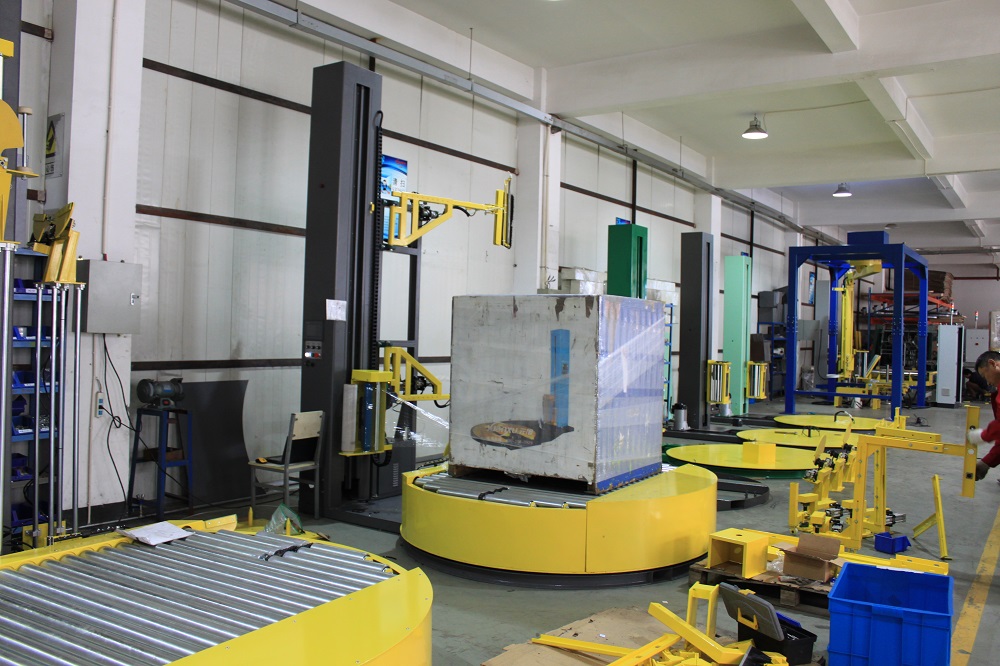
Key Applications and Benefits of Using a Top Press
The addition of a top press device provides significant advantages, particularly for challenging loads:
- Stabilizing Lightweight or Unstable Loads: Ideal for loads prone to shifting or collapsing under film tension alone, such as empty bottles, cans, light boxes, or stacked items with uneven tops.
- Preventing Load Shifting During Wrapping: Ensures the load remains stationary on the pallet as the turntable rotates and film is applied, leading to a more uniform and secure wrap.
- Improving Load Integrity: Creates a tighter, more contained final package, reducing the risk of product damage during handling and transportation.
- Enhanced Safety: Minimizes the potential for loads to topple during the wrapping process or later transit, improving warehouse safety.
- Consistent Wrap Quality: Helps achieve predictable wrap results even with variable load types within its designated category.
How It Works: The Wrapping Process Explained
While specific machine operations can vary, the typical sequence for a pallet wrapper with a top press involves these steps:
- Load Placement: The palletized load is placed onto the machine's turntable, typically via forklift or pallet jack.
- Cycle Start: An operator initiates the wrapping cycle via the control panel.
- Top Press Activation: The top press device lowers and makes contact with the top of the load, applying predetermined pressure.
- Turntable Rotation & Film Application: The turntable begins to rotate. Simultaneously, the film carriage, holding the roll of stretch film, moves vertically along the mast to dispense film around the load. The pre-stretch mechanism within the carriage elongates the film for optimal strength and economy.
- Wrapping Cycle: The carriage typically moves up and then down the mast, applying the desired number of film layers and overlap according to programmed settings. The top press remains engaged throughout this process.
- Film Cut and Seal: Once the wrapping is complete, the film is automatically cut and secured (e.g., wiped onto the load).
- Top Press Retraction: The top press device retracts upwards.
- Load Removal: The securely wrapped and stabilized pallet is ready to be removed from the turntable.
Key Components:
- Turntable: Rotates the palletized load.
- Mast: The vertical structure supporting the film carriage movement.
- Film Carriage: Houses the stretch film roll and pre-stretch system.
- Top Press Mechanism: The pneumatically or electrically actuated platen providing downward force.
- Control System: PLC-based interface for setting wrap parameters (rotation speed, carriage speed, film tension, top/bottom wraps, top press pressure).
Key Considerations When Selecting a Machine
Choosing the right pallet wrapping machine with a top press requires evaluating several factors:
- Load Characteristics: Maximum load weight, dimensions (L x W x H), and crucially, the nature of the instability (lightweight, shifting layers, compressible).
- Throughput Requirements: How many pallets per hour need to be wrapped? This dictates the necessary level of automation and cycle speed.
- Automation Level: Semi-automatic (requiring operator intervention for loading/unloading/start) vs. fully automatic (integrating with conveyors).
- Film Pre-Stretch: Higher pre-stretch percentages (e.g., 250% or 300%) maximize film efficiency and load holding force. Ensure the capability matches your film type.
- Top Press Specifications: Ensure the platen size is adequate for your largest load footprint and the pressure range is suitable for your products (enough to stabilize but not crush).
- Integration: Compatibility with existing conveyor systems or workflow if opting for a fully automatic solution.
- Safety Features: Emergency stops, safety fencing (for automatic models), and sensors are critical.
pallet stretch wrap 4 Conclusion
For operations handling lightweight, unstable, or easily shifted pallet loads, the pallet wrapping machine with a top press device offers a significant enhancement over standard stretch wrapping methods. By actively stabilizing the load during the wrapping cycle, these machines ensure greater load integrity, improve safety, and deliver consistently secure packages ready for the demands of storage and transportation. Evaluating your specific load types and throughput needs will guide the selection of the most appropriate model for your packaging operations.