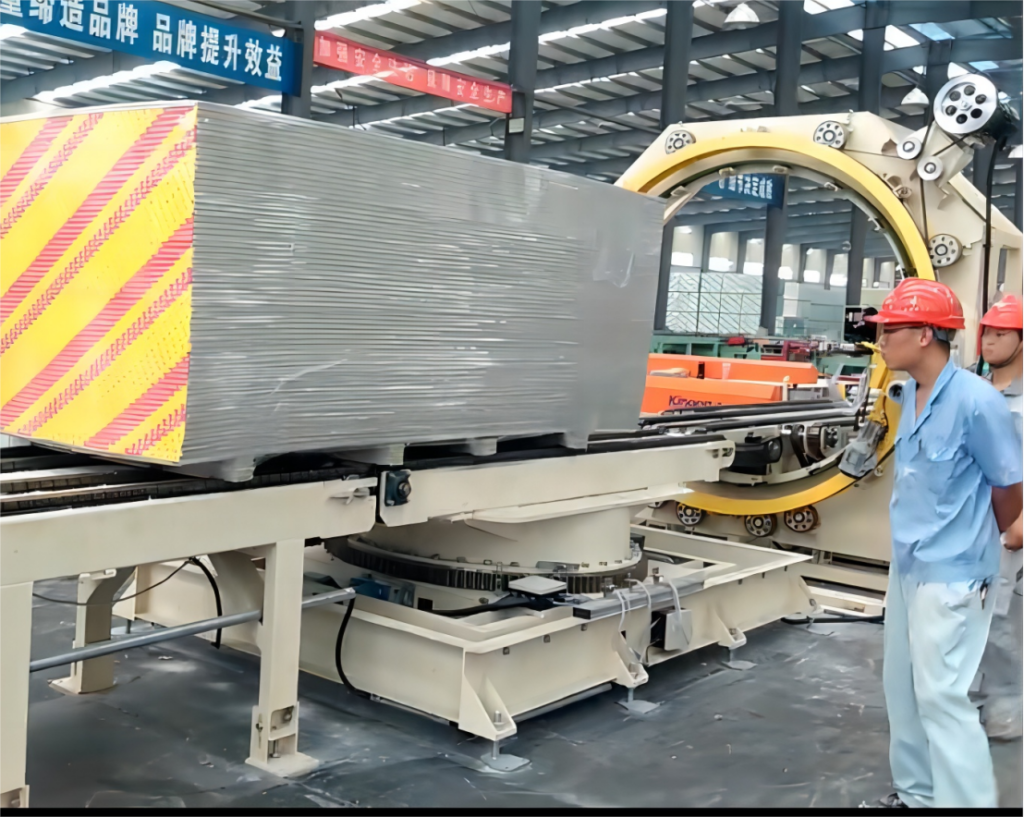
Handling and packaging long, often cumbersome items like panel timber and profiles presents unique challenges in manufacturing and logistics. Ensuring these materials are securely bundled and protected during storage and transit is crucial for maintaining quality and preventing costly damage. Automated packaging solutions, specifically horizontal orbital stretch wrappers, offer an effective method to address these challenges.
Understanding Horizontal Orbital Stretch Wrappers
A horizontal orbital stretch wrapper is specifically designed for packaging elongated products. Unlike traditional turntable or rotary arm wrappers where the load rotates, an orbital wrapper features a rotating ring carrying the stretch film roll. The product is fed horizontally through this rotating ring, allowing the film to be applied around its length in a continuous spiral. This method is ideal for items like:
- Timber panels
- Lumber
- Aluminum or plastic profiles and extrusions
- Pipes and tubing
- Doors and windows
Key Advantages for Wrapping Panel Timber and Profiles
Utilizing an orbital stretch wrapper provides several operational benefits for fabricators and manufacturers working with panel timber and profiles:
1. Enhanced Product Protection
The primary function is to secure and protect. Orbital wrapping tightly cocoons the product bundle in stretch film, providing significant protection against:
- Moisture and Dirt: Creates a barrier against environmental contaminants during storage or shipping.
- Scratches and Abrasions: Prevents surface damage caused by handling or friction between pieces.
- Load Shifting: Keeps bundles intact, reducing the risk of damage during transit.
horizontal orbital stretch wrapper52 2. Improved Handling Efficiency and Load Stability
Tightly wrapped bundles are inherently more stable and easier to handle than loose items.
- Unitization: Groups individual pieces into a single, manageable unit.
- Streamlined Logistics: Facilitates easier loading, unloading, and storage using forklifts or other handling equipment.
- Reduced Labor: Automation significantly decreases the manual effort required for packaging.
3. Increased Packaging Speed and Throughput
Automated orbital wrappers operate significantly faster than manual wrapping methods.
- Consistent Wrapping: Ensures uniform application of film and tension for every bundle.
- High Volume Capacity: Machines can be configured for various throughput requirements, matching production line speeds (typical speeds range from 5-20 meters per minute).
4. Optimized Material Usage
Modern orbital wrappers often feature powered pre-stretch systems. This technology stretches the film before application, maximizing its yield and holding force while minimizing material consumption compared to manual or less advanced methods.
Core Components and Operation
While designs vary, typical horizontal orbital wrappers include:
- Infeed and Outfeed Conveyors: Transport the product into and away from the wrapping ring. Conveyor length can often be customized based on product dimensions.
- Wrapping Ring: The core component that rotates around the product, carrying the film roll dispenser.
- Film Carriage: Holds the stretch film roll and often includes the pre-stretch mechanism.
- Press Devices: Vertical or side rollers that stabilize the product as it passes through the ring, ensuring a tight wrap, especially for stacked items.
- Automatic Film Clamp and Cutter: Mechanizes the start and end of the wrapping cycle, allowing for continuous operation.
- Control System (PLC): Manages machine functions, wrap parameters (e.g., rotation speed, film overlap), and integration with other line equipment.
These machines can handle significant load weights, often ranging from 10kg up to 1000kg or more, depending on the model specification. They are compatible with various packaging materials like LLDPE stretch film, HDPE, or PVC films.

Customization and Integration
Orbital stretch wrappers can often be tailored to specific needs:
- Variable Speed: Adjust wrapping speed based on product type and line requirements.
- Customizable Programs: Set different wrapping patterns or tension levels for various products.
- Integration: Can be integrated into fully automated production lines, receiving products directly from upstream processes and feeding them to downstream systems.
By investing in appropriate orbital stretch wrapping technology, manufacturers handling panel timber, profiles, and other long products can significantly improve packaging efficiency, enhance product protection, and reduce overall operational costs.