Optimizing ROI for Steel Coil Packing Line Investments
Investing in a steel coil packing line represents a significant capital expenditure for steel producers, service centers, and distributors. Maximizing the Return on Investment (ROI) from this equipment is essential for long-term operational efficiency and financial health. As automation, data analytics, and sustainability reshape the manufacturing landscape, optimizing your packing line involves more than just the initial purchase; it requires a strategic approach to operation, maintenance, and continuous improvement. This guide outlines key strategies to enhance steel coil packaging efficiency and ensure your investment delivers maximum value.
*(Retain existing Table of Contents block functionality)*
1. Thoroughly Assess Operational Requirements
Before investing, conduct a detailed analysis of your current coil packing operations. Identify specific bottlenecks, inefficiencies, and challenges. Are you experiencing delays in coil movement? Is packaging quality inconsistent? Are labor costs excessively high? Pinpointing these issues helps define the objectives for a new or upgraded system.
Perform a comprehensive operational audit to quantify your needs:
- Coil Specifications: Document the range of coil dimensions (ID, OD, width) and weights handled.
- Material Types: List all materials processed (e.g., galvanized steel, stainless steel, aluminum, copper).
- Throughput Targets: Define required packaging speed (coils per hour/shift).
- Packaging Requirements: Specify necessary wrapping, strapping, labeling, and palletizing standards.
Tailoring the packing line specifications to your precise needs prevents overspending on unnecessary features while ensuring the system effectively addresses your core operational goals.

2. Implement Automation to Reduce Costs and Boost Consistency
Coil packaging automation is a primary driver for maximizing ROI. Automated systems significantly reduce reliance on manual labor, leading to:
- Lower Labor Costs: Reduced staffing requirements for repetitive packing tasks.
- Improved Consistency: Uniform application of wrapping and strapping enhances product protection.
- Increased Speed: Faster cycle times compared to manual processes.
- Enhanced Safety: Minimizes manual handling of heavy coils, reducing injury risks.
Consider integrating key automation components:
- Automated Coil Cars or AGVs: For efficient coil transport to and from the line.
- Coil Upenders/Downenders: To orient coils correctly for packing.
- Robotic Arms: For tasks like label application or palletizing.
- Automatic Wrapping Machines: Ensure tight, consistent film application.
- Automatic Strapping Machines: Apply straps securely at programmed intervals.
Look for systems with Programmable Logic Controllers (PLCs) and intuitive Human-Machine Interfaces (HMIs). These allow for precise control, quick adjustments for different coil types, and easier troubleshooting, directly impacting operational efficiency and uptime.
3. Establish a Robust Preventive Maintenance Program
Unplanned downtime is a major drain on ROI. Implementing a preventive maintenance (PM) program is critical for keeping your packing line running reliably. Regular inspections, lubrication, and component replacements minimize the risk of unexpected breakdowns that halt production, incur emergency repair costs, and delay shipments.
Modern packing lines often incorporate features that support proactive maintenance:
- Real-time Performance Monitoring: Tracking cycle times, motor loads, and other parameters.
- Diagnostic Tools: Onboard systems or software to identify potential issues.
- Predictive Maintenance Capabilities: Utilizing sensors (e.g., vibration, thermal) and IoT integration to anticipate failures before they occur, allowing maintenance to be scheduled during planned downtime.
Investing in equipment designed for maintainability and adhering to a strict PM schedule are crucial for maximizing availability and extending the lifespan of your packing line, directly contributing to a higher ROI.
4. Optimize Packaging Material Consumption
Expenditures on wrapping film and strapping materials represent a significant ongoing operational cost. Optimizing their usage is key to improving ROI. Advanced packing lines offer features to control material consumption precisely:
- Adjustable Film Pre-stretch: Maximizes film yield, reducing the amount used per coil.
- Customizable Wrapping Tension: Ensures secure wrapping without excessive material use.
- Variable Strap Tension and Placement: Applies strapping effectively with minimal waste.
- Accurate Material Monitoring: Tracking consumption per coil or shift via the control system.
Evaluate the use of sustainable packaging materials, such as thinner gauge high-performance films, films with recycled content, or recyclable strapping. While potentially having different costs, they can reduce environmental impact and potentially lower waste disposal fees. Automated tension controls ensure consistent application, preventing material overuse regardless of the material type chosen.
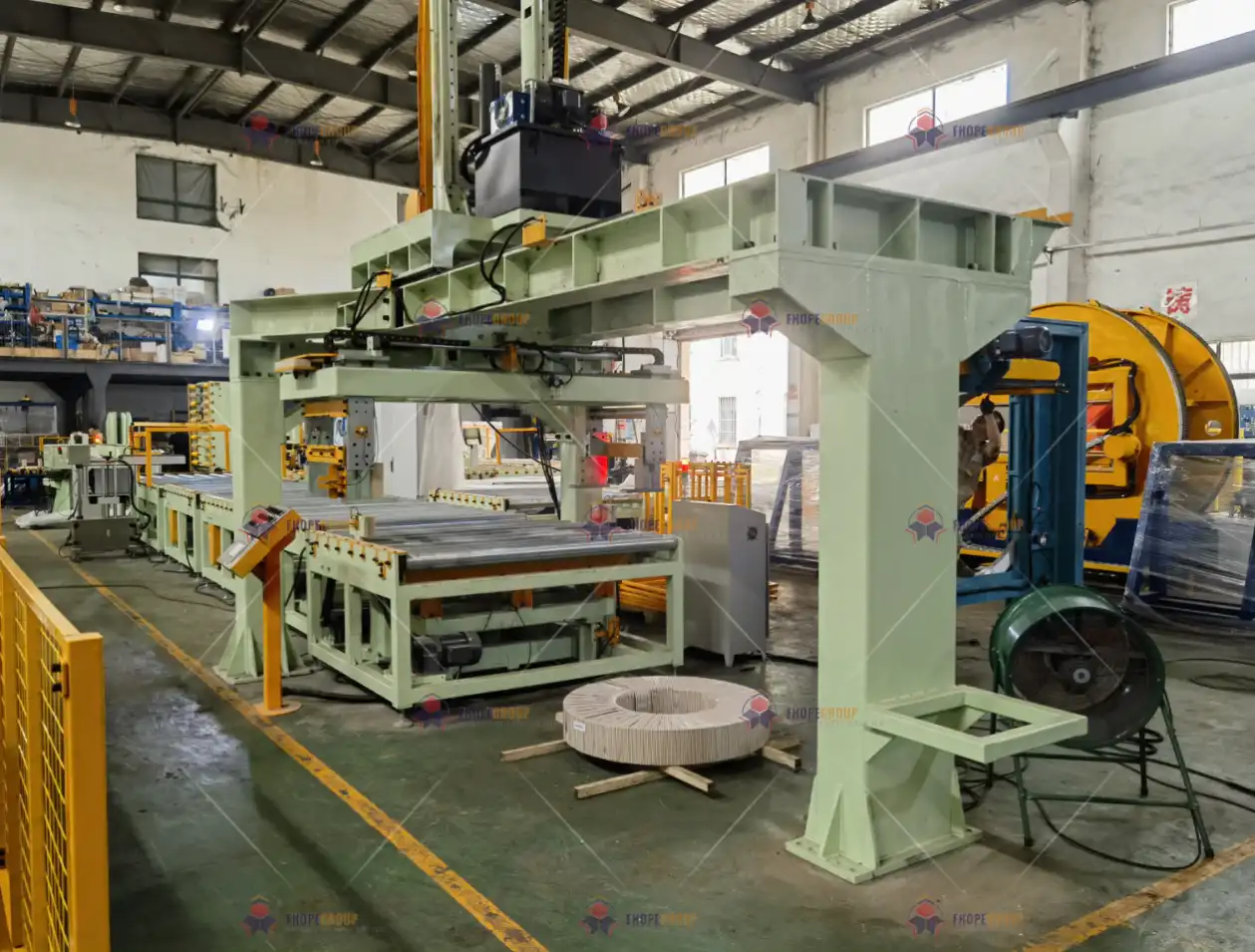
5. Enhance Speed and Throughput
In high-volume environments, packing line speed directly impacts profitability. Investing in equipment capable of high-speed operation increases the number of coils processed per shift, improving overall facility throughput. Key factors include:
- Fast Cycle Times: Automated wrapping and strapping cycles (often under 60 seconds per coil).
- Efficient Coil Handling: Minimizing delays between process steps (loading, wrapping, strapping, unloading).
- Parallel Processing: Systems designed to handle multiple functions simultaneously where possible.
Increased throughput leads to faster order fulfillment, reduced lead times, and potentially lower inventory levels, all contributing positively to ROI. Tracking metrics like Overall Equipment Effectiveness (OEE) can help identify opportunities to further optimize speed and efficiency.
6. Leverage Data and Analytics for Continuous Improvement
Modern steel coil packing lines generate valuable operational data. Utilizing data tracking and analytics provides insights for optimizing performance and reducing costs. Key data points include:
- Cycle times per coil/station
- Material consumption (film, straps)
- Downtime occurrences and reasons (error codes)
- Energy usage
Analyzing this data helps identify bottlenecks, sources of inefficiency, and patterns that might indicate maintenance needs. Integrating the packing line controls with plant-level Manufacturing Execution Systems (MES) or Enterprise Resource Planning (ERP) systems provides a holistic view of production efficiency, labor productivity, and cost per unit, enabling data-driven decision-making for continuous improvement and sustained ROI.
7. Customize the Packing Line for Maximum Flexibility
A packing line tailored to your specific needs offers better long-term value. Invest in a customizable packing line that can adapt to variations in:
- Coil Dimensions: Handling a wide range of ODs, IDs, and widths.
- Coil Types: Processing steel, aluminum, copper, slit coils, master coils, etc.
- Packaging Requirements: Different wrap patterns, strapping configurations, or labeling needs.
Consider modular designs that allow for future expansion or reconfiguration as your production requirements evolve. Features like automatic coil dimension sensing and programmable recipes enable quick changeovers between different product types without manual adjustments, maximizing uptime and flexibility. This adaptability ensures the packing line remains a valuable asset even as your business changes, safeguarding your initial investment.

8. Invest in Comprehensive Employee Training
Even highly automated systems require skilled personnel for operation, supervision, and maintenance. Providing thorough training programs is essential for maximizing equipment performance and ROI. Well-trained employees can:
- Operate the machinery efficiently and safely.
- Perform routine preventive maintenance tasks correctly.
- Troubleshoot minor issues quickly, reducing downtime.
- Utilize advanced features (e.g., recipe management, diagnostics) effectively.
Consider training as an ongoing investment, including initial onboarding for new equipment and regular refresher courses. Skilled operators minimize errors, reduce wear and tear through proper operation, and contribute significantly to maintaining high OEE levels.
9. Emphasize Sustainability for Environmental and Financial Benefits
Integrating sustainable practices into your coil packaging operation can yield both environmental and financial advantages. This includes:
- Energy Efficiency: Selecting machinery with energy-saving components like Variable Frequency Drives (VFDs) on motors and optimized pneumatic/hydraulic systems.
- Material Reduction: Utilizing features like film pre-stretch and optimized wrap patterns (as mentioned in point 4).
- Waste Minimization: Reducing packaging rejects through consistent automated processes.
- Sustainable Materials: Exploring options like biodegradable films, materials with recycled content, or easily recyclable strapping.
Beyond direct cost savings on energy and materials, sustainable operations can enhance brand reputation, meet customer expectations, and ensure compliance with evolving environmental regulations, indirectly supporting long-term ROI.
10. Regularly Monitor and Evaluate Performance
Maximizing ROI is a continuous process. Once operational, monitor and evaluate the packing line's performance against established Key Performance Indicators (KPIs). Important metrics include:
- OEE (Overall Equipment Effectiveness): Combines availability, performance, and quality.
- Throughput: Coils packed per hour/shift.
- Downtime: Frequency and duration of stops (planned vs. unplanned).
- MTBF (Mean Time Between Failures): Indicates reliability.
- MTTR (Mean Time To Repair): Measures maintenance efficiency.
- Material Cost per Coil: Tracks consumable usage efficiency.
- Energy Consumption: Monitors operational energy costs.
Conduct regular performance audits and review meetings to analyze KPI trends, identify areas for improvement, and ensure the packing line continues to meet financial and operational objectives. Many systems offer remote monitoring capabilities, allowing real-time performance tracking and faster response to potential issues.
11. Calculate the Total Cost of Ownership (TCO)
When evaluating packing line investments, look beyond the initial purchase price and consider the Total Cost of Ownership (TCO). TCO provides a more accurate picture of long-term value and includes:
- Initial Purchase Price: The cost of the equipment itself.
- Installation and Commissioning: Costs to set up and integrate the line.
- Operating Costs: Energy consumption, labor.
- Consumables: Wrapping film, strapping, labels.
- Maintenance and Repairs: PM costs, spare parts, technician labor.
- Training Costs: Initial and ongoing training for staff.
- Downtime Costs: Lost production value during outages.
- Potential Decommissioning Costs: End-of-life considerations.
A system with a higher upfront cost might offer lower TCO due to superior energy efficiency, greater reliability (lower maintenance/downtime), or more efficient material usage. Performing a TCO analysis during vendor selection helps ensure you choose the most economically advantageous solution over the equipment's lifespan, directly impacting overall ROI. Authoritative sources like financial publications or industry associations often provide frameworks for calculating TCO.
12. Plan for Future Scalability
Consider your facility's future growth trajectory when selecting a packing line. An investment made today should ideally accommodate potential increases in production volume or changes in product mix. Key aspects of scalability include:
- Modular Design: Allows for adding or upgrading specific functions (e.g., adding automated labeling, integrating AGVs) without replacing the entire line.
- Throughput Capacity: Choose a system with capacity slightly above current needs or one that can be easily upgraded for higher speeds.
- Software Updates: Ensure the control system (PLC/HMI) can be updated to incorporate new features, improve diagnostics, or enhance integration capabilities.
- Flexibility: The ability to handle a wider range of coil sizes or new packaging specifications in the future (as discussed in point 7).
Planning for scalability protects your investment by ensuring the packing line can adapt to future business needs, avoiding the premature need for costly replacements and contributing to sustained long-term ROI.
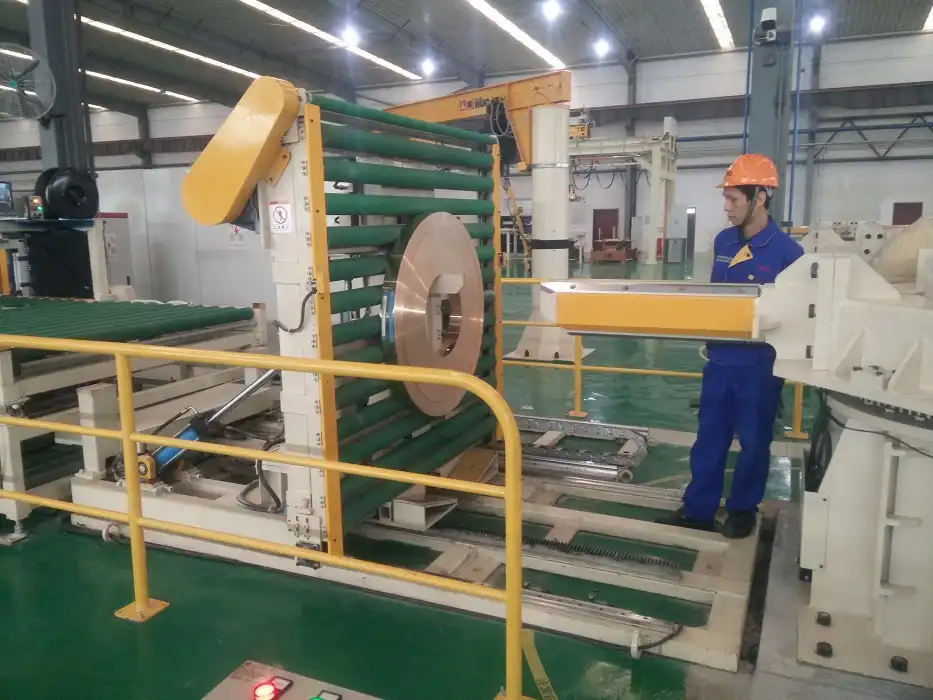
Conclusion
Maximizing the ROI on a steel coil packing line involves a multifaceted strategy encompassing careful planning, smart technology adoption, diligent maintenance, and continuous performance evaluation. By thoroughly understanding operational needs, strategically implementing coil packaging automation, optimizing material and energy usage, and investing in employee training, manufacturers can significantly enhance efficiency and reduce costs.
Furthermore, focusing on factors like TCO, flexibility, scalability, and sustainability ensures the investment delivers value throughout its operational life. A well-optimized packing line not only leads to faster production cycles and lower operational expenditures but also strengthens a company's competitive position through improved product protection, consistent quality, and enhanced responsiveness to market demands.