Horizontal Orbital Wrapper and Strapping Machine for Panel and Board: Solution Evaluation and Comparisons
In today's fast-paced manufacturing world, efficient and reliable packaging solutions are critical to maintaining high levels of productivity and ensuring product integrity, especially for industries handling large or long items like panels and boards. The drive for automation in packaging has led to innovations such as the horizontal orbital wrapper and the automatic strapping machine—two key technologies designed to ensure products like wood panels, engineered boards, metal sheets, or even drywall are securely packaged for transport and storage, enhancing load security and packaging efficiency.
This article provides a detailed evaluation and comparison of horizontal orbital wrappers and strapping machines. We will explore their core functionalities, key features, benefits, and how they address various industrial packaging requirements. By understanding the strengths and applications of each system, you can determine the optimal packaging solution for your operation's unique needs.
1. Understanding the Horizontal Orbital Wrapper
A horizontal orbital wrapper (also known as a horizontal stretch wrapper) is specialized machinery designed to wrap elongated or flat products, such as panels, boards, lumber, extrusions, or pipes, in protective stretch film. The wrapping mechanism, typically a ring carrying the film roll, moves around the product as it passes horizontally through the machine. This orbital motion encases the product in a secure, continuous layer of stretch film, effectively shielding it from moisture, dust, contamination, and surface damage during handling and transport.
Key Benefits of Horizontal Orbital Wrappers:
- Versatility: Capable of handling a wide range of product lengths, shapes, and sizes.
- Superior Product Protection: Fully wraps products, offering excellent protection against environmental elements and abrasions.
- Operational Efficiency: Automates the wrapping process, significantly reducing the time and labor required compared to manual wrapping.
- Material Savings: Modern machines offer precise film tension and pre-stretch control, optimizing film usage.
One of the primary advantages of implementing a horizontal orbital wrapper is the substantial reduction in manual labor. In medium-to-high volume operations, this automation boosts productivity, improves wrapping consistency, and allows personnel to focus on higher-value tasks while the machine ensures precise and secure packaging.
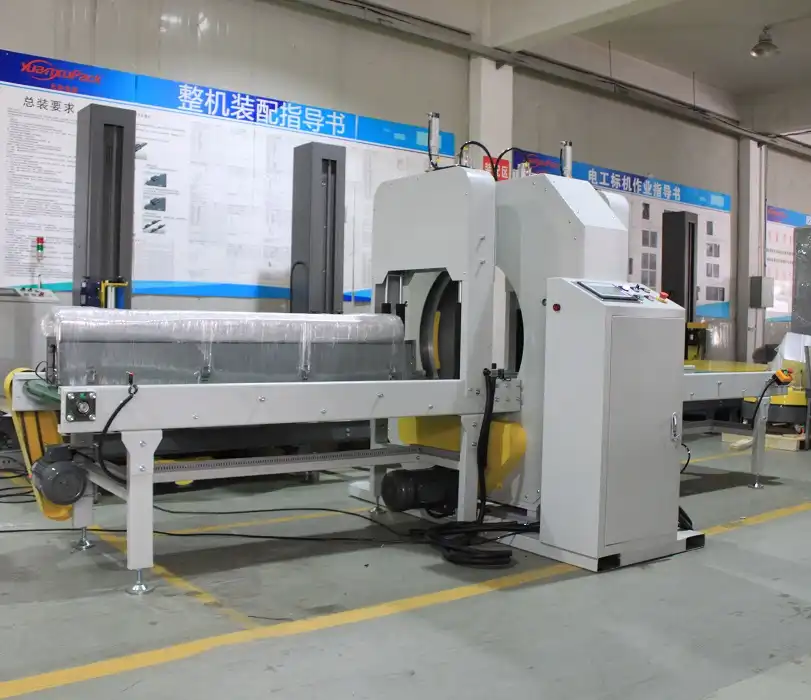
2. The Role of Strapping Machines for Load Security
While orbital wrapping provides excellent surface protection and containment, strapping machines focus on load unitization and stabilization. These machines apply strong plastic (typically Polypropylene - PP or Polyester - PET) or metal straps around individual products or bundled stacks, preventing shifting, separation, or collapse during transit.
For heavy, bulky, or potentially unstable items like stacks of boards or panels, strapping is often crucial for maintaining package integrity and ensuring safe handling. Automated strapping machines can operate standalone or be integrated seamlessly with orbital wrappers or other conveyor systems, creating a comprehensive automated packaging solution.
Key Benefits of Strapping Machines:
- Enhanced Stability & Load Security: Securely bundles products or reinforces packages, reducing movement and ensuring safer transportation and stacking.
- Time Savings: Automated strapping cycles are significantly faster and more consistent than manual strapping methods.
- Consistent Tension: Provides uniform strap tension across all packages, crucial for load integrity without damaging the product.
- Versatile Application: Can be used for bundling, carton closing, or reinforcing large pallet loads.
3. Evaluating Key Features of Horizontal Orbital Wrappers
When selecting the right horizontal orbital wrapper, consider these critical features:
- Ring Diameter/Wrapping Zone Size: Must accommodate the maximum cross-section dimensions of your products.
- Wrapping Speed: Look for machines with adjustable rotation speeds (RPM) and conveyor speeds to match production rates.
- Film Pre-Stretch System: Powered pre-stretch significantly reduces film consumption (up to 300% or more) and provides better load containment.
- Film Tension Control: Precise, adjustable tension control is vital to securely wrap the load without crushing or damaging the product.
- Automatic Film Cut and Clamp: Automates the start and end of the wrap cycle, improving efficiency and safety.
- Customization Options: Programmable wrap cycles (e.g., number of wraps, banding) cater to specific product protection needs.
Horizontal orbital wrappers are particularly indispensable for industries packaging long or large flat items, such as wood panels, metal sheets, profiles, lumber, pipes, and doors. Their ability to automate the wrapping process delivers faster turnaround times, reduced labor costs, and improved package quality.
4. Evaluating Key Features of Strapping Machines
When comparing strapping machines, key factors include:
- Strap Type Compatibility: Ensure the machine can reliably run the required strap type (PP, PET, or steel) and size (width, thickness) for your load requirements.
- Tensioning Range and Control: Must provide sufficient tension for load security, with consistent and adjustable control to prevent product damage. Automatic tension control is highly desirable.
- Sealing Method: Common methods include heat sealing (for PP) and friction-weld sealing (for PET), known for their reliability and strength. Steel strapping uses mechanical seals (notch or crimp).
- Arch Size: The arch must accommodate the largest package dimensions that need strapping.
- Cycle Speed: Measured in straps per minute, a faster cycle speed is crucial for high-volume operations.
- Automation Level: Ranges from semi-automatic (operator feeds strap) to fully automatic (integrated into conveyor lines).
Both horizontal orbital wrappers and strapping machines provide vital protective functions, but the optimal choice—or combination—depends heavily on your specific products, handling processes, and operational goals.

5. Solution Comparison: Orbital Wrapper vs. Strapping Machine
Evaluating these two machine types requires understanding their distinct primary functions:
- Orbital Wrappers: Excel at containment and surface protection. They fully enclose the product in stretch film, guarding against dirt, moisture, scratches, and minor impacts. The film also provides a degree of unitization.
- Strapping Machines: Excel at unitization and stabilization. They apply high-tensile bands to hold items together securely, preventing shifting and ensuring the structural integrity of the bundle or package, especially under the stresses of transport.
Here’s a simple comparison based on product type:
- For Lightweight or Surface-Sensitive Products: If your primary concern is protecting surfaces from scratches, dust, or moisture, and the items are relatively stable, an orbital wrapper might suffice. Examples include finished wood profiles or plastic extrusions.
- For Heavy, Bulky, or Unstable Products: For heavy loads (like stacks of timber or large panels) or items prone to shifting, strapping is essential for stability. Often, the best solution involves both wrapping and strapping: the wrapper provides surface protection, and the strapper ensures the load remains secure and unitized.
- For Bundling Multiple Items: Strapping is generally the preferred method for tightly bundling multiple units (like pipes or lumber) together. Wrapping can then be applied over the strapped bundle for added protection.
In many panel and board applications, a combination of orbital wrapping followed by strapping provides the most robust packaging solution, addressing both protection and stability requirements.
6. Industries Benefiting from Automated Panel and Board Packaging
While woodworking (lumber, panels, flooring) and construction materials (drywall, insulation boards, metal studs) are major users, several other industries benefit significantly from these automated packaging systems:
- Furniture Manufacturing (large components, flat-pack items)
- Metal Fabrication (sheet metal, extrusions, profiles)
- Plastics Industry (pipes, profiles, sheets)
- Textiles (rolls of fabric, carpet)
- Glass and Window/Door Production
- Automotive Parts (exhaust pipes, long components)
By adopting automated horizontal wrappers and strapping machines, companies in these sectors can achieve substantial improvements in material handling efficiency, reduce labor costs, enhance worker safety, minimize product damage, and increase overall throughput.
7. Cost Considerations: Investment vs. Long-Term ROI
The initial investment for a horizontal orbital wrapper or an automatic strapping machine can be significant. However, analyzing the long-term return on investment (ROI) reveals compelling financial benefits:
Key Cost Benefits & ROI Drivers:
- Reduced Labor Costs: Automation drastically decreases the manual labor required for wrapping and strapping, freeing up employees for other tasks and lowering direct labor expenses.
- Lower Product Damage Rates: Consistent, secure packaging minimizes damage during shipping and handling, reducing costs associated with returns, rework, and replacements.
- Increased Productivity/Throughput: Automated systems operate much faster than manual methods, allowing more products to be packaged per shift, thus increasing overall output capacity.
- Optimized Material Usage: Features like powered film pre-stretch and precise strap tension control reduce consumption of packaging materials (film, strap), leading to direct cost savings.
- Improved Safety: Automating these often physically demanding tasks reduces the risk of repetitive strain injuries and accidents associated with manual handling.
When evaluating the cost, consider the total cost of ownership (TCO), including maintenance, consumables, and potential downtime, against these significant long-term gains.

8. Customization Options for Optimal Performance
Modern horizontal orbital wrappers and strapping machines are rarely one-size-fits-all. Leading manufacturers offer various customization options to tailor the equipment precisely to specific operational needs:
Customizable Features to Look For:
- Variable Speed Controls: Independent adjustment of conveyor speed, ring/arch speed, and wrapping/strapping cycle parameters allows fine-tuning for different products and line speeds.
- Size Adjustability: Machines designed to handle a wide range of product dimensions (length, width, height) provide flexibility for diverse product lines. Options might include larger rings/arches or adjustable guides.
- Film/Strap Delivery Systems: Choices in pre-stretch ratios, tensioning systems, and strap feeding mechanisms ensure optimal performance for specific materials and load requirements.
- Integration Capabilities: Options for seamless integration into existing conveyor systems, including communication protocols for upstream and downstream equipment (e.g., sensors, interlocks, PLC integration).
- Specialized Options: Features like top sheet dispensers (for added weather protection), corner protection applicators, or multi-strap patterns can be incorporated.
Tailoring the machinery through these customization options ensures maximum operational efficiency, consistent packaging quality, and adaptability to future needs.
9. Essential Safety Features in Packaging Machinery
Operating machinery, especially with large or heavy products like panels and boards, necessitates robust safety features. Reputable manufacturers equip their horizontal wrappers and strapping machines with multiple safety mechanisms:
Essential Safety Features Include:
- Emergency Stop Buttons (E-Stops): Strategically placed for quick access, allowing immediate shutdown of the machine in an emergency.
- Safety Interlocks: Sensors on access doors and guards prevent machine operation if safety barriers are open.
- Guarding: Physical barriers around moving parts (like the wrapping ring or strapping head) prevent accidental contact.
- Photo-Eye Sensors: Detect product presence and position, ensuring proper cycle start/stop and preventing collisions or misfeeds.
- Automatic Fault Detection: Systems often include diagnostics that detect issues like film breaks, strap misfeeds, or jams, stopping the machine and alerting operators.
- Compliance with Standards: Machines should ideally comply with relevant safety standards (e.g., CE marking in Europe, OSHA guidelines in the US).
Incorporating these safety features is crucial for protecting operators, reducing the risk of workplace accidents, and ensuring compliance with safety regulations.
10. Integrating Wrappers and Strappers into Production Lines
A key advantage of modern packaging machinery is its ability to be integrated into broader production or packaging lines. Both horizontal orbital wrappers and strapping machines are often designed with modular architecture, facilitating connection with:
- Infeed and outfeed conveyors
- Stacking or accumulating systems
- Labeling or marking equipment
- Palletizing systems
Benefits of Integration:
- Seamless Workflow Automation: Creates a continuous flow from production to final packaging, minimizing manual handling and bottlenecks.
- Higher Overall Throughput: Synchronized operation of integrated components maximizes the efficiency of the entire line.
- Improved Process Control: Centralized control systems can manage multiple machines, providing better oversight and data collection.
- Reduced Footprint: Thoughtful integration can optimize the layout and space utilization within the facility.
Successful integration transforms disparate packaging steps into a cohesive, efficient, and fully automated system, delivering significant productivity gains.
11. Real-World Example: Transforming Furniture Panel Packaging
Consider a mid-sized furniture manufacturer specializing in flat-pack cabinets. They were manually wrapping large laminated panels using handheld stretch wrap dispensers and manually applying PP straps. This process was slow, labor-intensive, inconsistent, and resulted in occasional shipping damage due to loose wrapping or inadequate strapping.
After analyzing their bottleneck, they invested in an integrated line featuring a horizontal orbital wrapper followed immediately by an automatic strapping machine. The results were transformative:
- Packaging Speed Increased by 150%: The automated line significantly outpaced the manual team, clearing the packaging backlog.
- Labor Reallocation: Two workers previously dedicated to wrapping/strapping were reassigned to quality control and assembly tasks.
- Damage Reduction: Shipping damage claims related to packaging failure dropped by over 80% due to the consistent, secure wrapping and strapping.
- Material Savings: The wrapper's pre-stretch unit reduced film usage by 40% compared to manual wrapping.
This example highlights how strategic investment in appropriate automated packaging technology can yield substantial operational and financial improvements.
12. Environmental Considerations and Sustainability
Environmental impact is an increasingly important factor in packaging decisions. Modern horizontal wrappers and strapping machines can contribute to sustainability goals:
Sustainable Features and Practices:
- Film Optimization/Source Reduction: High-efficiency pre-stretch systems on orbital wrappers minimize the amount of plastic film required per load, reducing waste at the source.
- Recyclable Consumables: Compatibility with stretch films and plastic straps (PP, PET) that are recyclable helps improve the end-of-life profile of the packaging. Encouraging the use of materials with recycled content is also beneficial.
- Energy Efficiency: Newer machine designs often incorporate energy-saving motors, drives, and control systems, reducing the overall carbon footprint of the packaging operation.
- Durability and Longevity: Well-maintained, high-quality machinery lasts longer, reducing the environmental impact associated with manufacturing and disposing of equipment.
By choosing machines with these features and opting for recyclable or reduced-source materials, companies can align their packaging operations with environmental stewardship goals while often achieving cost savings.

Conclusion: Selecting the Right Panel and Board Packaging Solution
In the specialized world of panel and board packaging, the choice between a horizontal orbital wrapper and a strapping machine—or implementing both—hinges on a thorough analysis of your specific products, production volume, handling requirements, and protection needs. Both technologies offer significant advantages, driving productivity, ensuring consistency, lowering labor costs, and reducing product damage.
However, for many applications involving large, heavy, or high-value panels and boards, the most effective and reliable packaging line often involves the synergistic combination of both machines. The orbital wrapper provides comprehensive surface protection and containment, while the strapping machine delivers crucial load stability and unitization.
By carefully evaluating machine features, customization options, integration potential, safety aspects, and long-term ROI, businesses can make informed decisions that optimize their packaging processes. Implementing the right automated wrapping and strapping solutions can transform your operation, leading to faster, safer, more consistent, and cost-effective results that directly benefit your bottom line. For further insights into packaging machinery standards and industry trends, resources from organizations like PMMI, The Association for Packaging and Processing Technologies, can be valuable.