Investing in a Steel Coil Packing Line: A Guide to Future-Proofing Your Operations
Table of contents block placeholder (handled by WordPress plugin)
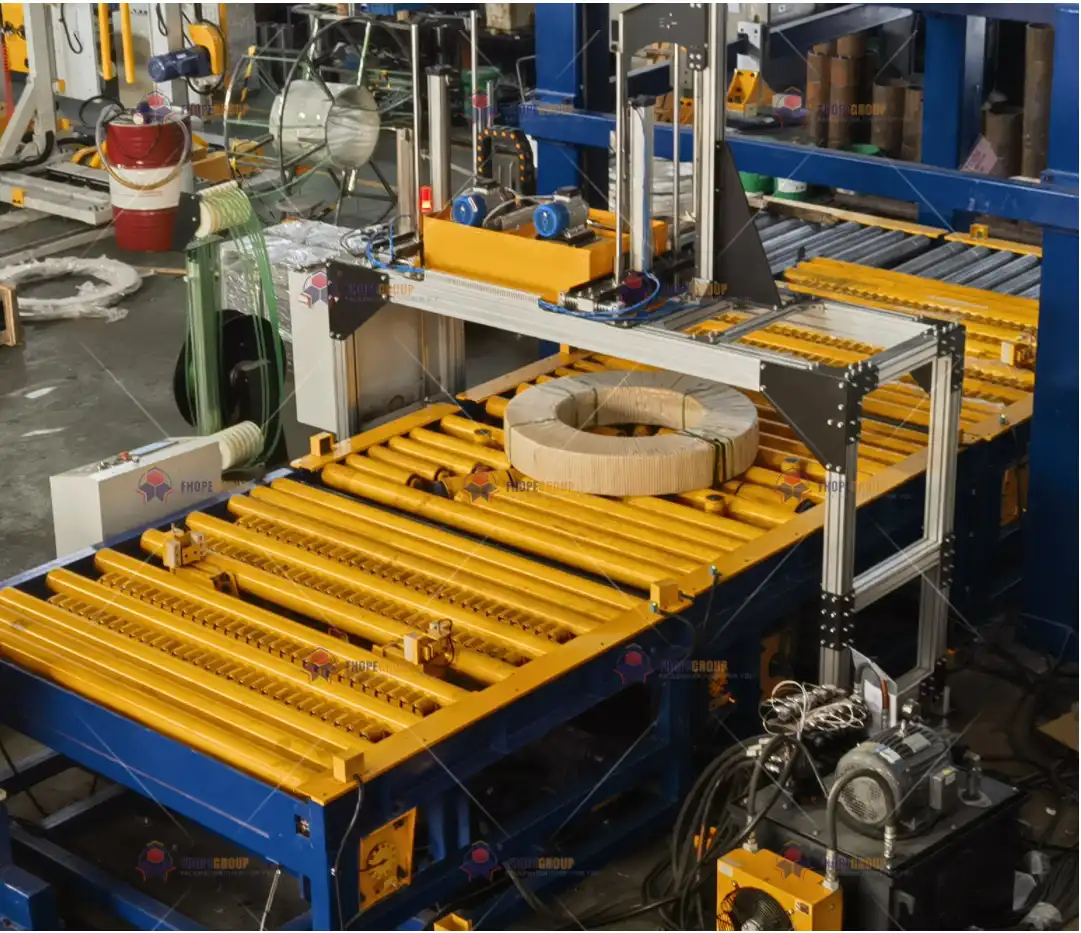
In today’s highly competitive manufacturing and metal processing landscape, staying efficient and competitive is paramount. One strategic move to future-proof your business is investing in advanced automation, specifically a steel coil packing line. This guide explores why automated steel coil packaging systems are becoming indispensable, how they can revolutionize your production flow, and the long-term benefits of this critical investment.
1. The Growing Importance of Automation in Steel Coil Handling
Automation in manufacturing, particularly in steel processing, is transitioning from a competitive advantage to an operational necessity. Businesses relying solely on manual packaging methods face significant challenges in speed, consistency, and safety. Embracing automation technologies like integrated packing lines is key to streamlining operations, reducing operational costs, and enhancing workplace safety.
Automated steel coil packing lines address the complex and often hazardous task of packaging heavy steel coils. By integrating such a system, businesses can significantly minimize manual labor requirements, dramatically increase packaging throughput, and guarantee consistent packaging quality. Furthermore, a well-designed automated line helps eliminate common issues like product damage during handling and transit, production bottlenecks, and worker fatigue—all factors that directly impact profitability.
2. Understanding Steel Coil Packaging Lines: Core Functions
A steel coil packing line is an integrated, often fully automated system engineered to wrap, strap, and protect steel coils efficiently as they move from production or slitting to storage or shipping. These systems perform tasks that traditionally required multiple personnel, thereby reducing manual intervention while boosting the speed and precision of the entire packaging process.
Key components and functions typically include:
- Coil Loading & Centering: Safely receiving coils from cranes or turnstiles and positioning them accurately for processing.
- Automatic Coil Wrapping: Applying protective materials like stretch film, VCI paper, or plastic sheeting uniformly around the coil.
- Strapping Systems: Applying radial (through-the-eye) or circumferential straps (steel or PET) to secure the coil and packaging materials.
- Weighing & Labeling: Integrated scales and automated label applicators for tracking and identification.
- Stacking & Palletizing: Automated systems for stacking smaller coils or placing finished coils onto pallets.
- Conveyor Systems: Transporting coils smoothly between stations within the packing line.
steel coil palletizing1 3. Key Benefits of Investing in an Automated Steel Coil Packing Line
From an ROI (Return on Investment) perspective, implementing an automated steel coil packing line offers substantial advantages. Here are the primary benefits:
- Enhanced Efficiency and Throughput: Automation significantly accelerates the packaging cycle time compared to manual methods, allowing facilities to process more coils per shift and increase overall production output.
- Improved Workplace Safety: Handling heavy steel coils manually poses significant risks of musculoskeletal injuries. Automation minimizes direct human contact with heavy loads and repetitive motions, drastically reducing injury risks and associated costs.
- Significant Cost Savings: While requiring an initial investment, automation delivers long-term savings by reducing direct labor costs, minimizing material waste through precise application, and lowering expenses related to workplace injuries and product damage.
- Consistent Packaging Quality: Automated systems apply wrapping materials and straps with consistent tension and placement every time, ensuring uniform protection and load stability, reducing the likelihood of damage during handling and shipping.
- Reduced Product Damage: Proper, consistent packaging protects coils from moisture, contamination, and physical impacts, preserving material quality and reducing costly rejects or rework.
4. Common Challenges Overcome by Automated Coil Packaging
Businesses still relying heavily on manual or semi-manual coil packaging often encounter persistent challenges that impact efficiency, cost, and quality:
- Worker Fatigue and Injury Risk: The physically demanding nature of manually manipulating coils and packaging materials leads to fatigue, increasing the likelihood of errors and serious injuries.
- Inconsistent Packaging Quality: Manual application of wrap and straps can result in uneven tension, loose wraps, or improper strap placement, leaving coils vulnerable to damage or corrosion.
- Process Bottlenecks: Manual packaging is inherently slower than automated solutions, often creating bottlenecks that limit overall production capacity and lead to delays in shipping.
- High Labor Costs: Manual packaging requires significant labor resources, contributing substantially to operational expenses, especially in regions with high labor costs or during labor shortages.
These issues can be effectively mitigated or entirely eliminated by transitioning to a well-designed automated steel coil packing line.
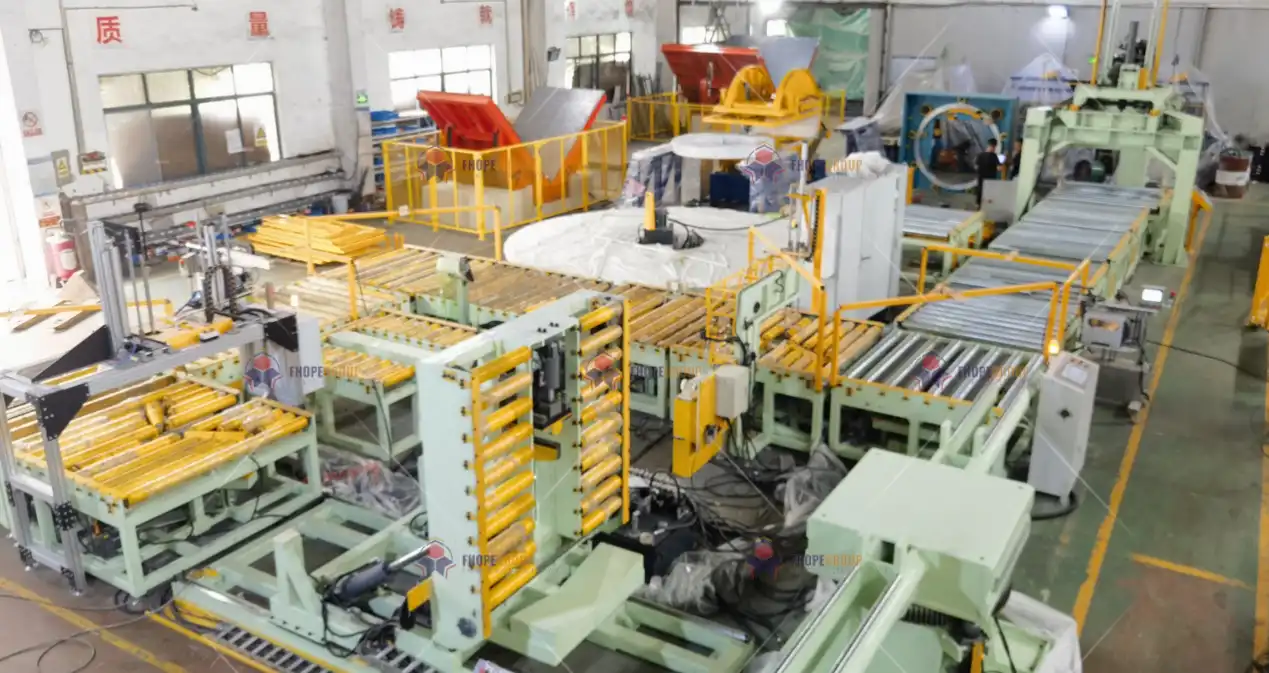
5. Essential Features to Look for in a Steel Coil Packing Line
To maximize the return on your investment, selecting a system that aligns with your specific operational needs is crucial. Consider these key features when evaluating potential steel coil packing lines:
- Coil Size and Weight Capacity: Ensure the system can handle the full range of coil dimensions (ID, OD, width) and weights processed in your facility.
- Customizable Packaging Programs: Look for flexibility in programming different wrapping patterns, strap placements, and material types (e.g., stretch film, VCI paper, plastic wrap) to suit various product requirements and customer specifications.
- Throughput Rate: Evaluate the machine's cycle time (coils per hour) to ensure it meets or exceeds your production targets.
- Durability and Reliability: Opt for robustly constructed equipment designed for industrial environments, minimizing downtime and maintenance requirements. Look for reputable manufacturers with strong track records.
- Advanced Safety Features: Essential features include safety interlocks, light curtains, emergency stops, and physical guarding compliant with relevant safety standards (e.g., ISO, ANSI).
- Integration Capabilities: Ensure the line can seamlessly integrate with existing upstream (e.g., slitting lines, cranes) and downstream (e.g., warehouse management systems, conveyors) processes.
6. The Role of Coil Packing Lines in Supply Chain Optimization
Effective supply chain optimization is critical in today's competitive market. An automated steel coil packing line plays a vital role by ensuring:
- Faster Order Fulfillment: Reduced packaging time translates directly to quicker preparation for shipment, helping meet tight delivery schedules.
- Reduced Transit Damage: Consistent, high-quality packaging minimizes the risk of coils arriving damaged, preventing costly returns and customer dissatisfaction.
- Improved Inventory Management: Automated weighing and labeling provide accurate data for inventory tracking and logistics planning.
This operational efficiency enhances the overall flow of materials, improves customer satisfaction through reliable delivery and quality, and strengthens your company's reputation—all essential elements for long-term business success.
7. How Automation Reduces Overall Packaging Costs
A primary driver for investing in a steel coil packing line is the significant potential for reducing operational costs. While the initial capital expenditure is a factor, the long-term savings generated by automation often provide a compelling ROI. Key areas of cost reduction include:
- Lower Labor Costs: Automated lines require fewer operators for tasks like wrapping and strapping, freeing up personnel for higher-value activities or reducing overall labor expenditure.
- Minimized Material Waste: Automated systems apply wrapping film and straps precisely, using optimized amounts based on coil size and requirements. This contrasts with manual application, which often leads to inconsistent material usage and higher waste.
- Decreased Downtime: Automated systems operate consistently without fatigue. While maintenance is required, overall uptime is typically higher compared to manual processes prone to variability and stoppages related to personnel availability or injury.
- Reduced Product Damage Costs: Preventing damage through superior packaging directly saves costs associated with scrap, rework, return logistics, and potential customer claims.
The cumulative savings from increased efficiency, reduced errors, optimized material use, and improved safety can quickly justify the initial investment, contributing positively to the bottom line.
8. Environmental Considerations and Sustainability Benefits
Increasingly, companies are focusing on sustainability and minimizing their environmental footprint. An automated steel coil packing line can contribute to greener operations:
- Efficient Resource Use: Optimized systems often consume less energy per coil packaged compared to less efficient or manual methods. Precise material application also reduces the consumption of packaging consumables.
- Less Packaging Waste: Consistent and optimized material usage directly translates to less plastic film, paper, or strapping ending up as industrial waste.
- Product Preservation: Effective packaging prevents corrosion and damage, reducing the likelihood that the steel itself becomes scrap due to inadequate protection during storage or transport, thus conserving valuable resources.
Adopting efficient automation aligns with growing customer and regulatory demands for environmentally responsible practices, potentially enhancing your company's image as a sustainability-conscious supplier.
9. Key Considerations Before Investing
Making the transition to an automated packing line requires careful planning. Evaluate these factors before committing to an investment:
- Scalability and Future Needs: Can the system accommodate potential future increases in production volume or changes in coil sizes/types? Choose a system with inherent flexibility or clear upgrade paths.
- Integration with Existing Infrastructure: How will the new line interface with your current material handling equipment (cranes, AGVs, conveyors) and data systems (MES, ERP)? Ensure compatibility to avoid operational disruptions.
- Total Cost of Ownership (TCO): Look beyond the initial purchase price. Factor in installation, commissioning, training, ongoing maintenance, spare parts, and energy consumption costs.
- Operator Training and Technical Support: Ensure the supplier provides comprehensive training for operators and maintenance staff. Verify the availability and responsiveness of technical support and spare parts.
- Facility Layout and Space: Confirm you have adequate floor space, ceiling height, and utility access (power, compressed air) for the proposed line configuration.
Thorough evaluation of these points will help mitigate risks and ensure your investment delivers the expected long-term value.
10. Real-World Impact: Success Stories with Automated Coil Packing
Numerous businesses across the steel industry and related sectors have successfully leveraged automated coil packaging:
- Steel Service Centers: Many service centers have reported significant increases (e.g., 30-50%) in packaging throughput after installing automated lines, allowing them to handle more orders and reduce lead times. They also benefit from improved package appearance and consistency requested by end-users.
- Metal Coil Producers: Large mills utilize high-speed automated lines to keep pace with production output, ensuring coils are protected immediately after production and prepared efficiently for shipment or storage. Reduced labor dependency in demanding environments is a major plus.
- Automotive and Appliance Suppliers: Companies supplying steel coils to industries with stringent quality requirements rely on automated packaging to prevent surface damage and corrosion, ensuring materials arrive in pristine condition for critical manufacturing processes.
These examples highlight how investing in steel coil packing automation provides tangible competitive advantages and measurable improvements in operational performance.
11. Future Trends in Steel Coil Packaging Technology
Steel coil packaging technology continues to evolve, driven by broader trends in manufacturing automation and data integration:
- AI and Machine Vision: Artificial intelligence (AI) and vision systems are being integrated for tasks like automatic coil identification, surface defect detection before wrapping, and adaptive control of packaging parameters based on real-time conditions.
- IIoT Integration and Data Analytics: The Industrial Internet of Things (IIoT) enables packing lines to connect to plant-wide monitoring systems. This allows for real-time performance tracking, predictive maintenance alerts, remote diagnostics, and data analysis for continuous process optimization.
- Advanced Robotics: Increased use of robotics for tasks like strap feeding, label application, and palletizing offers greater flexibility and automation potential, especially for complex packaging requirements.
- Sustainable Packaging Solutions: Ongoing development focuses on incorporating more recyclable or biodegradable packaging materials and optimizing systems to use minimal material while maintaining protective integrity.
Staying aware of these innovations can help ensure that current investments are forward-looking and adaptable to future industry standards.
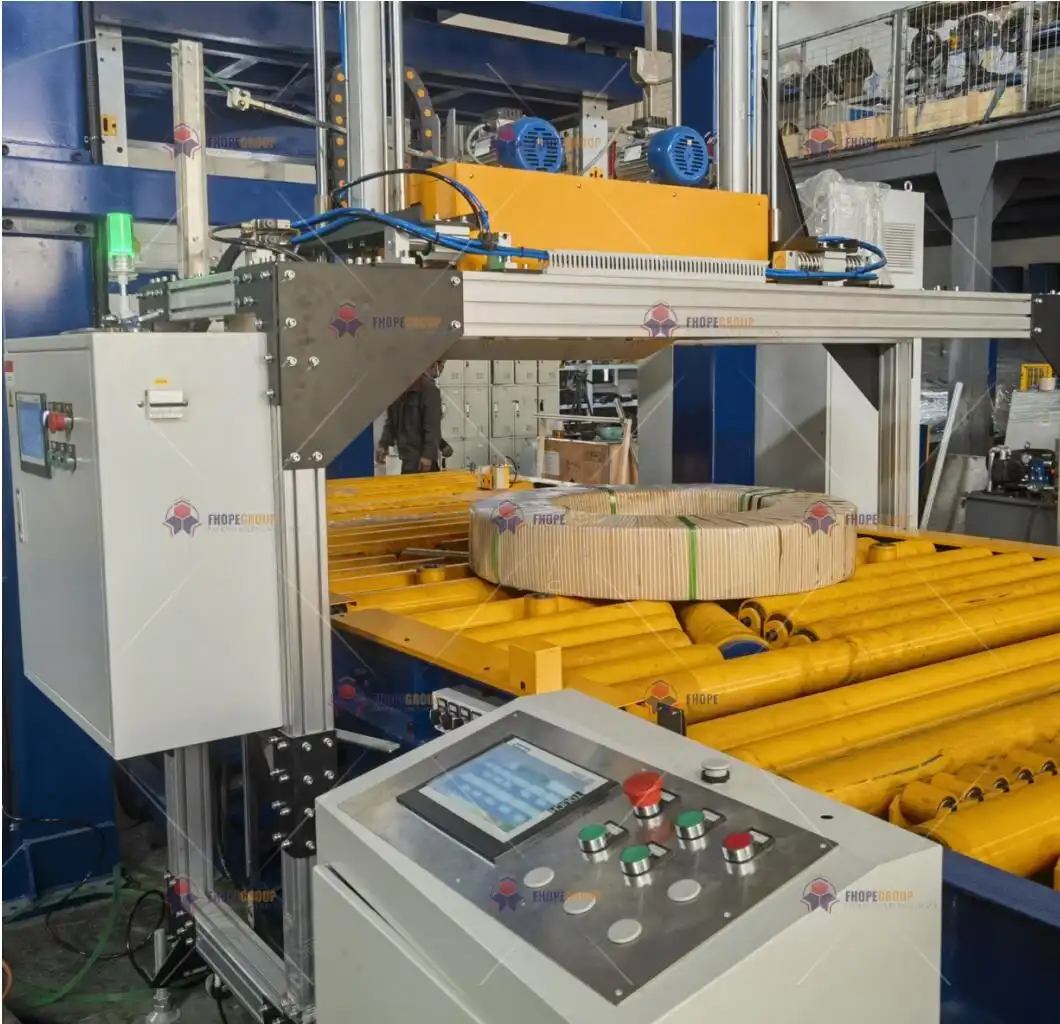
12. Conclusion: Secure Your Future with Strategic Automation
In summary, investing in an automated steel coil packing line is a strategic decision that addresses immediate operational challenges while preparing your business for future demands. In an era where efficiency, safety, and quality are non-negotiable, relying on outdated manual processes puts companies at a competitive disadvantage.
By automating your steel coil packaging, you can achieve significant improvements in:
- Productivity and Throughput
- Operational Cost Reduction
- Workplace Safety
- Packaging Consistency and Product Protection
Moreover, embracing advanced automation technologies positions your business as an adaptable, forward-thinking industry player. Future-proofing your operations with a modern packing line safeguards not only your current competitiveness but also your capacity to grow and thrive in a dynamic global market. It's an investment in efficiency, reliability, and long-term success.