Automated Coiling and Strapping Systems: Boosting Efficiency for Pipe and Hose Manufacturers
Handling long lengths of pipe, hose, cable, and similar materials presents unique challenges in manufacturing and distribution. Manual coiling and strapping processes are often labor-intensive, slow, and can lead to inconsistent product packaging. Implementing an automatic coiling and strapping machine offers a robust solution to streamline these operations, enhance product quality, and improve overall productivity.
How Automatic Coiling and Strapping Machines Operate
These integrated systems automate the entire process from length measurement to the final strapped coil, ready for storage or shipment. The typical workflow involves several key stages:
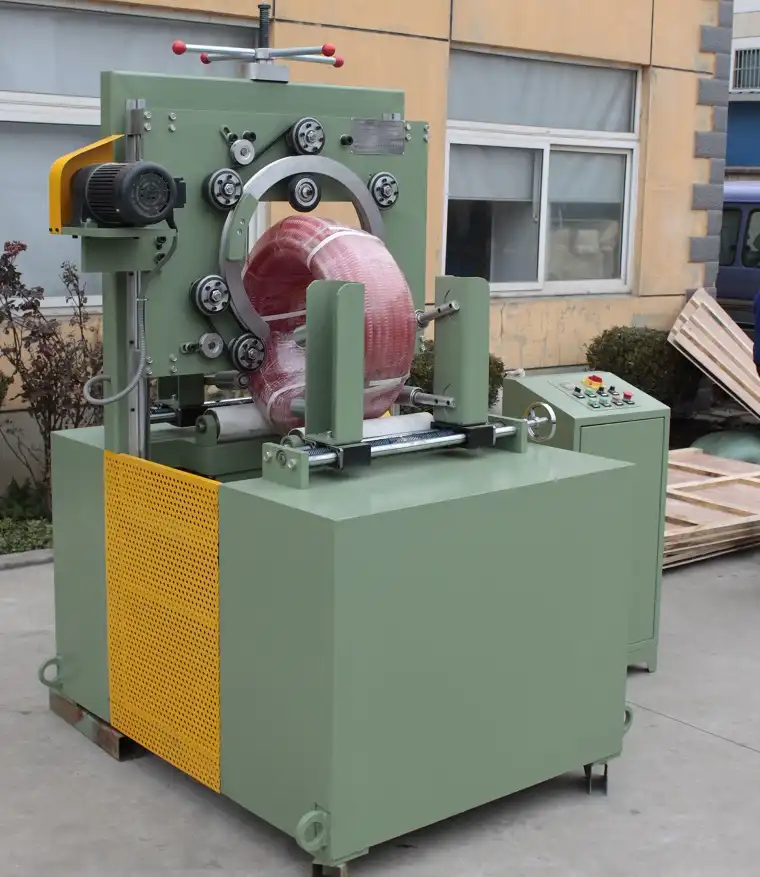
Optimizing the Coiling Process
- Length Measurement: The machine accurately measures the desired length of the pipe or hose fed into it, often using encoder wheels or laser sensors.
- Automated Winding: The material is precisely wound onto a coiling head or into a designated coiling basket. Advanced systems offer tight control over parameters like:
- Coil inside diameter (ID) and outside diameter (OD)
- Coil traverse width (layer thickness)
- Winding tension to ensure a stable, yet undamaged, coil.
- Material Handling: Systems are designed to handle a variety of materials, from flexible hoses to semi-rigid pipes, across a range of diameters.
Securing Coils with Automated Cutting and Strapping
- Automatic Cutting: Once the preset length is reached, an integrated cutting mechanism cleanly severs the material.
- Coil Transfer (if applicable): In some systems, the finished coil is automatically transferred to a strapping station.
- Strap Application: The machine feeds strapping material (typically robust polypropylene (PP) or sometimes steel strapping for heavier applications) around the coil circumference at designated points.
- Tensioning and Sealing: The strap is automatically tensioned to a predetermined level to secure the coil tightly without damaging the product. It is then sealed, usually through heat welding or friction welding for PP strap, creating a durable bond.
- Ejection: The finished, strapped coil is ejected from the machine, ready for downstream handling.
Key Benefits of Automated Coiling and Strapping Systems
Integrating automated coiling and strapping technology provides significant advantages for manufacturers:
- Enhanced Production Efficiency: These machines operate at high speeds, significantly increasing throughput compared to manual methods. Continuous operation minimizes downtime.
- Improved Product Consistency and Quality: Automation ensures every coil meets precise length specifications and diameter requirements. Consistent strap tension leads to uniform, stable, and professional-looking coils.
- Reduced Labor Costs: Automating these tasks frees up personnel for more value-added activities and reduces reliance on manual labor for repetitive coiling and strapping operations.
- Material Savings: Accurate length measurement minimizes material waste. Optimized strap usage reduces consumable costs.
- Enhanced Workplace Safety: Automating the handling, cutting, and strapping of potentially heavy or unwieldy materials reduces the risk of manual handling injuries.
- Improved Logistics and Storage: Neatly coiled and securely strapped products are easier to handle, stack, store, and transport, optimizing warehouse space and reducing shipping damage.
corrugated hose and pipe packing wrapping machine1 Considerations When Selecting a System
Choosing the right automatic coiling and strapping machine requires evaluating several factors:
- Material Type and Flexibility: Ensure the machine is compatible with the specific materials (e.g., PVC, PEX, rubber, braided hose) and their flexibility characteristics.
- Product Size Range: Verify the machine's capacity for the minimum and maximum diameters and lengths you process.
- Speed and Throughput Requirements: Match the machine's operational speed to your production targets.
- Coil Specifications: Consider required ID/OD, width, and weight capabilities.
- Strapping Needs: Determine the number of straps per coil, preferred strapping material (PP/Steel), and required tension levels.
- Integration: Assess how the machine will fit into your existing production line and any necessary upstream or downstream automation.
Conclusion
For manufacturers dealing with pipes, hoses, cables, or wires, automatic coiling and strapping machines represent a significant technological advancement. By automating these critical end-of-line processes, companies can achieve substantial improvements in speed, consistency, safety, and cost-effectiveness. Investing in such automation is a strategic move towards optimizing production and maintaining a competitive edge in today's demanding market.
(Note: When incorporating images into your post, always include descriptive alt text explaining the image content for accessibility and SEO purposes. For example: alt="Automatic coiling machine winding blue PEX pipe onto a spool"
)