6 Key Elements for an Effective Steel Wire Packing Strategy
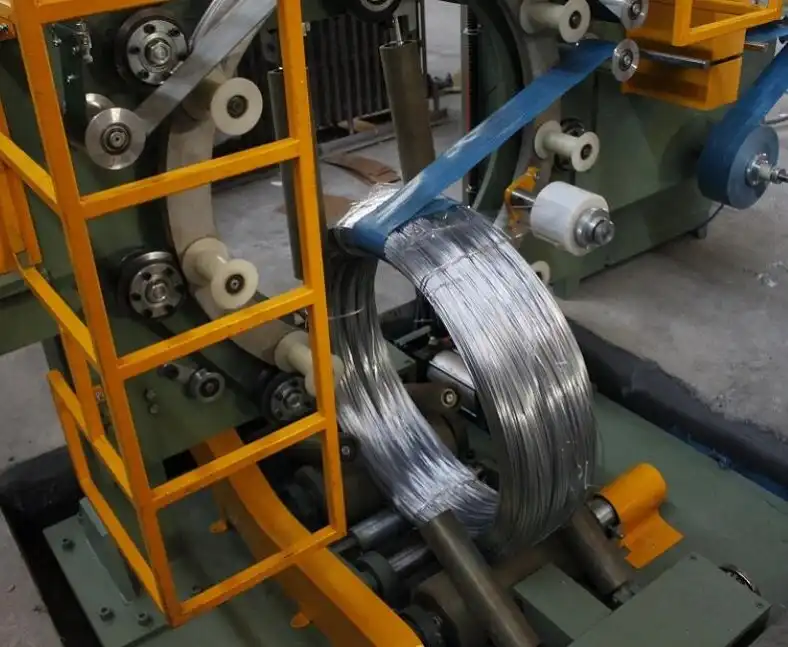
Introduction
Steel wire is a fundamental material in industries ranging from construction and automotive manufacturing to energy and agriculture. Protecting its integrity from the production line to the point of use is paramount. An effective steel wire packing and packaging strategy is crucial not only for preventing physical damage like scratches or deformation but also for guarding against environmental threats like corrosion. A well-designed strategy optimizes material use, enhances handling efficiency, ensures safe transportation, and ultimately delivers the steel wire in prime condition. This guide outlines six critical elements for developing a successful steel wire packaging plan, covering material selection, machinery, environmental considerations, and cost-efficiency.
1. Understand Steel Wire Characteristics
Developing an effective packing strategy begins with a thorough understanding of the specific steel wire product. Different types of wire have unique properties that dictate the required level of protection and handling methods.
- Wire Gauge and Diameter: Thicker, heavier wires demand robust packaging materials and structures capable of supporting significant weight without collapsing. Finer wires, conversely, are more susceptible to tangling, kinking, or breaking, requiring careful coiling and secure wrapping to maintain their form.
- Tensile Strength and Flexibility: High-tensile wire might exert outward pressure on packaging, necessitating strong containment like steel strapping. More flexible wires might require core support or specific coiling patterns to prevent collapsing or tangling.
- Surface Coating and Finish: Steel wires can be bare (black), galvanized, coated (e.g., PVC, epoxy), or stainless. Each finish has different vulnerabilities. Galvanized and coated wires need protection against abrasion that could compromise the protective layer, while bare carbon steel is highly susceptible to rust and requires moisture barriers or corrosion inhibitors. Stainless steel, while resistant, can still suffer from surface contamination or scratches.
- Coil Size and Weight: The dimensions and weight of the wire coil influence everything from the type of packaging materials needed (e.g., films, wraps, pallets) to the machinery required for handling and wrapping (e.g., lifters, automated wrappers with sufficient capacity).
Analyzing these characteristics allows for a tailored packaging approach that addresses the specific vulnerabilities and requirements of the steel wire.
2. Choose Appropriate Packing Materials
Selecting the right combination of packing materials is fundamental to protecting steel wire throughout storage and transit. The choice depends on the wire's characteristics, anticipated environmental exposure, transport method, and budget.

- Stretch Film: Highly versatile, stretch film provides excellent load containment and protection against dust and moisture when applied correctly. Available in various gauges (thicknesses), it can be applied manually or using automated wrapping machines for consistent tension and coverage. UV-inhibitor versions are available for outdoor storage.
- Shrink Film: Offering a tighter, more conforming fit than stretch film, shrink film provides a robust barrier against environmental factors. It requires heat application to shrink, creating a sealed unit. This is often used for long-term storage or when a high degree of weatherproofing is necessary.
- VCI (Vapor Corrosion Inhibitor) Paper and Film: Essential for ferrous metals like carbon steel wire, VCI materials release harmless chemical vapors that form a protective layer on the metal surface, preventing rust and corrosion. VCI paper or film can be used as an inner wrap or interleaving layer, especially crucial for sea freight or storage in humid conditions.
- Woven Fabric (Polypropylene/Polyester): For heavy-duty applications or wires with sensitive coatings, woven fabrics offer superior tear and puncture resistance compared to standard films. They provide a durable outer layer that withstands rough handling.
- Paper (Kraft Paper, Crepe Paper): Often used as a cost-effective inner wrap, paper provides a basic level of protection against scratches and absorbs minor amounts of condensation. Crepe paper offers more flexibility for wrapping coils.
- Edge Protectors: Cardboard, plastic, or metal edge protectors shield the coil edges from impact damage and prevent strapping from cutting into the wire or inner packaging layers.
- Strapping (Steel or Plastic): Used to unitize coils, secure them to pallets, or reinforce packaging. Steel strapping offers maximum tensile strength for heavy coils, while PET (polyester) strapping provides high strength with less risk of scratching and better resistance to environmental factors. PP (polypropylene) strapping is a lighter-duty option.
The optimal solution often involves a combination of these materials, layered strategically to provide comprehensive protection.
3. Select the Right Packing Machinery
Automation plays a key role in achieving consistent, efficient, and cost-effective steel wire packing, especially in medium- to high-volume operations. The choice of machinery depends on coil sizes, desired throughput, packaging materials, and integration needs.
- Automatic Wire Coil Wrapping Machines: These machines automate the application of stretch film, VCI film, or paper around the coil. Orbital wrappers pass the material through the eye of the coil, ensuring complete coverage. Horizontal wrappers are suitable for wrapping the outer diameter of coils stacked horizontally. Automation ensures consistent wrap tension and material usage, reducing waste and labor costs.
- Coil Strapping Machines: These machines automatically apply, tension, seal, and cut steel or plastic straps around the coil. They can be integrated into packing lines for securing individual coils or bundles. Different configurations handle various coil orientations and sizes.
- Shrink Tunnels/Heat Guns: Used in conjunction with shrink film, these apply controlled heat to shrink the film tightly around the coil, creating a sealed, weatherproof package. Tunnels are used for higher throughput, while heat guns are suitable for lower volumes or custom shapes.
- Coil Upenders/Tilters: These handling devices safely rotate coils between horizontal and vertical orientations, often necessary for different stages of the packing process (e.g., eye-to-sky wrapping vs. palletizing).
- Integrated Packing Lines: For maximum efficiency, custom-engineered lines can combine multiple processes, such as weighing, wrapping, strapping, labeling, and palletizing, into a single automated workflow.
Investing in the right machinery streamlines operations, improves package quality consistency, enhances worker safety, and optimizes material consumption.
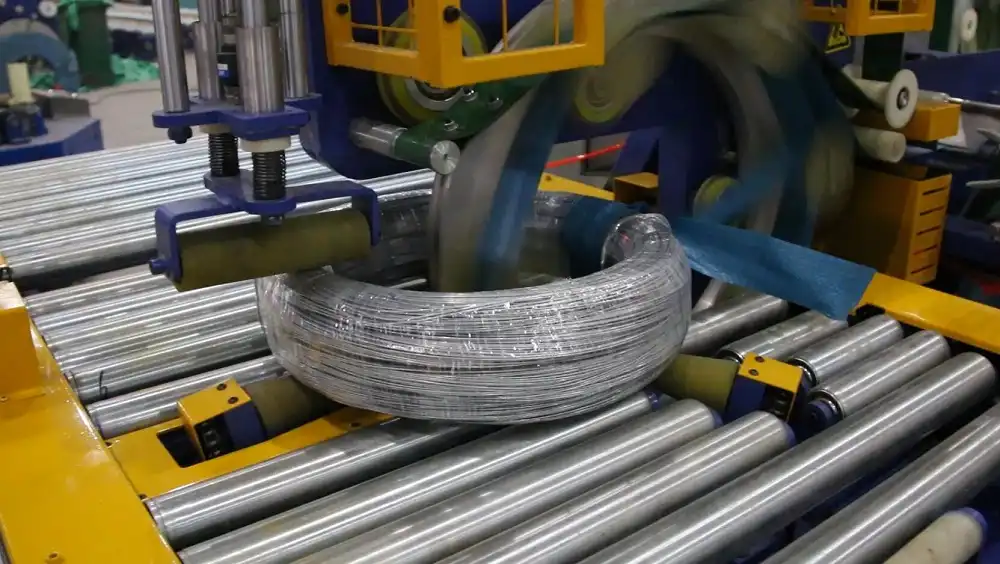
4. Adapt to Environmental Conditions
Steel wire is vulnerable to environmental factors during transit and storage. A robust packing strategy must anticipate and mitigate these risks.
- Moisture and Humidity: This is the primary cause of rust on carbon steel wire. Packaging must act as a moisture barrier. Using high-quality stretch film (properly overlapped), shrink film, or VCI materials is critical, especially for sea transport or storage in damp climates. Desiccants can sometimes be added inside packaging for extra moisture absorption.
- Temperature Fluctuations: Extreme heat or cold can affect both the wire and the packaging materials. Temperature changes can cause condensation to form inside improperly sealed packages. Materials should be selected to perform reliably across the expected temperature range without becoming brittle or losing tension.
- UV Exposure: Direct sunlight can degrade certain packing materials like standard stretch film over time, reducing their protective qualities. If outdoor storage or transport through sunny regions is expected, using UV-resistant films or adding an opaque outer layer is recommended.
- Saline Environments: Proximity to saltwater (sea freight, coastal storage) significantly accelerates corrosion. High-performance VCI materials and hermetically sealed packaging (where feasible) are essential in these conditions.
- Dust and Contaminants: Simple wrapping with stretch film or paper can prevent abrasive dust and dirt from contaminating the wire surface, which is important for wires requiring clean surfaces for subsequent processing (e.g., coating, welding).
Conducting a risk assessment based on the entire logistics chain—from factory to end-user—helps identify potential environmental hazards and select appropriate protective measures.
5. Secure Steel Wire for Safe Transportation
Properly securing steel wire coils is vital to prevent shifting, falling, or damage during handling and transportation. Unsecured or poorly secured loads pose significant safety risks and can lead to costly product loss.
- Coil Unitization: Wrapping individual coils tightly with stretch film or securing them with strapping helps maintain coil integrity and prevents unraveling.
- Palletizing: Securing coils onto pallets creates stable units that are easier and safer to handle with forklifts. Coils can be placed flat (eye-to-sky) or vertically (eye-to-wall) depending on size and stability. Strapping or stretch wrapping is used to secure the coils to the pallet. Dunnage (e.g., wood blocks, air bags) may be needed to fill voids and prevent movement.
- Load Bracing in Trucks/Containers: Within a truck trailer or shipping container, palletized or individual large coils must be properly blocked and braced to prevent shifting during transit. This can involve using lumber, airbags, or specialized load securing systems. Following established guidelines, such as those from the [Federal Motor Carrier Safety Administration (FMCSA)], is crucial for compliance and safety.
- Shock Absorption: For sensitive wires or rough transit conditions, incorporating cushioning materials like foam pads or heavy-duty cardboard between coils or layers can absorb impacts and vibrations.
- Proper Handling Equipment: Using appropriate lifting equipment (e.g., C-hooks, coil lifters, forklifts with coil rams) designed for handling wire coils prevents damage to both the product and the packaging during loading and unloading.
Effective load securement ensures the steel wire arrives undamaged and minimizes safety hazards throughout the supply chain.
6. Balance Cost and Efficiency
While robust protection is essential, the steel wire packing strategy must also be economically viable. Balancing packaging costs, material usage, labor efficiency, and the potential cost of damage is key to a sustainable operation.
- Material Optimization: Select materials that provide the necessary protection without over-packing. Using the correct gauge of stretch film, optimizing wrap patterns on automated machines, and choosing cost-effective VCI options where appropriate can significantly impact material costs.
- Process Efficiency: Automation through machinery reduces manual labor requirements, increases throughput speed, and ensures consistent application of materials, leading to lower labor costs and less material waste. Analyze bottlenecks in the current packing process to identify areas for improvement.
- Total Cost of Ownership (TCO): When evaluating machinery, consider not just the purchase price but also operating costs, maintenance requirements, lifespan, and potential savings in labor and materials over time.
- Damage Cost Analysis: Compare the cost of implementing enhanced packaging solutions against the potential costs associated with product damage, returns, customer dissatisfaction, and safety incidents. Often, investing slightly more in packaging can yield significant savings by reducing these negative outcomes.
- Sustainability Considerations: Evaluate the environmental impact and recyclability of packing materials. Sometimes, slightly more expensive but recyclable or reusable options can align with corporate sustainability goals and even offer long-term cost benefits (e.g., reusable steel pallets or coil supports for closed-loop logistics).
Striving for the optimal balance ensures that the steel wire is adequately protected in a way that supports the overall profitability and efficiency of the business.

Conclusion
Developing a successful steel wire packing strategy is a multi-faceted process that demands careful consideration of the product itself, the journey it will undertake, and the resources available. By systematically addressing these six key elements—understanding wire characteristics, choosing the right materials, selecting appropriate machinery, adapting to environmental factors, ensuring secure transport, and balancing cost with efficiency—manufacturers and suppliers can effectively protect their products. A well-executed packing strategy minimizes damage, prevents corrosion, enhances handling safety, reduces waste, and ultimately ensures that high-quality steel wire is delivered to the end-user, ready for its intended application. Implementing these principles contributes significantly to operational excellence and customer satisfaction in the competitive steel wire market.