XPS Foam Board Large Product Sealing and Shrink Wrap Machine: A Comprehensive Guide
Extruded Polystyrene (XPS) foam boards are widely used in construction and insulation due to their excellent thermal resistance, rigidity, and moisture resistance. However, packaging these large, sometimes bulky boards presents unique challenges. Ensuring they reach their destination undamaged requires robust and efficient packaging solutions. This guide explores the specialized machinery designed for this purpose: the XPS foam board large product sealing and shrink wrap machine.
1. Understanding the Need: Properties of XPS Foam Board
Before diving into the machinery, it's crucial to understand why specialized packaging is necessary for XPS foam boards. Key properties include:
- Size: Often manufactured in large sheets or panels.
- Rigidity: While strong, edges and corners can be susceptible to impact damage.
- Surface: Can be scratched or dented during handling and transport.
- Sensitivity: Requires protection from prolonged UV exposure and certain chemicals.
These characteristics necessitate a packaging method that secures the boards, protects them from physical damage, and shields them from environmental factors like moisture and dust.
2. The Challenge of Packaging Large Format Boards
Manually packaging large XPS foam boards is often inefficient and inconsistent. Key challenges include:
- Handling large, unwieldy items.
- Ensuring a tight, uniform seal.
- Applying protective wrapping evenly.
- Maintaining high throughput in production environments.
- Risk of damage during the packaging process itself.
Automated or semi-automated machinery specifically designed for these large dimensions overcomes these hurdles effectively.
3. Introducing the XPS Foam Board Sealing and Shrink Wrap Machine
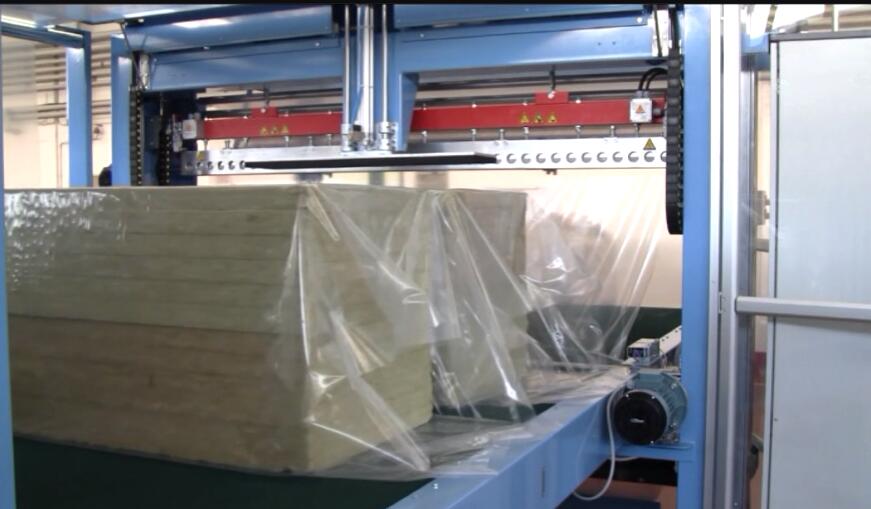
An XPS foam board large product sealing and shrink wrap machine is purpose-built equipment designed to automate or semi-automate the packaging process for large-format foam insulation boards and similar products. It typically combines two primary functions: sealing the packaging material and shrinking it for a tight fit.
4. Key Processes Explained
4.1 Sealing
The sealing component creates a secure closure around the XPS foam board (or stack of boards) using a protective film.
- Mechanism: Often utilizes an L-bar sealer or a side-sealing system. Heat and pressure are applied to fuse the edges of the packaging film (commonly Polyolefin or Polyethylene).
- Purpose: To create a fully enclosed bag or sleeve around the product.
- Benefit: This initial seal provides a contained environment, protecting the foam board from contaminants like dust, dirt, and moisture ingress during storage and transit. It ensures the product remains clean and dry.
4.2 Shrink Wrapping
Following the sealing stage, the enclosed product moves into the shrink wrapping section, typically a heat tunnel.
- Mechanism: Controlled hot air circulates within the shrink tunnel. This heat causes the specialized shrink film to contract uniformly.
- Purpose: The film shrinks tightly around the contours of the XPS foam board(s).
- Benefit: This process provides several advantages:
- Stability: Bundles multiple boards securely together, preventing shifting.
- Protection: Adds a durable, conforming layer of protection against scratches, abrasions, and minor impacts.
- Tamper Evidence: A tight, intact shrink wrap indicates the product hasn't been tampered with.
- Presentation: Creates a clean, professional look for the packaged product.
5. Core Features and Technical Parameters
While specific models vary, common features and parameters of these machines include:
- Large Sealing Area: Designed to accommodate the dimensions of standard and oversized XPS foam boards. Specify maximum length, width, and height capacity.
- Sealing System: Type of sealer (e.g., L-Bar, side seal, continuous motion) impacting speed and sealing quality.
- Shrink Tunnel: Size of the tunnel aperture, heating element type, temperature control range, and conveyor speed adjustment are crucial for handling different product sizes and film types.
- Conveyor System: Belt type (e.g., roller, mesh), speed control, and load capacity suitable for heavy foam boards.
- Film Compatibility: Designed to work with specific types and gauges of shrink film (e.g., [Polyolefin shrink film] Polyethylene).
- Control System: Often PLC-based with user interfaces (touch screens) for setting parameters like sealing time, temperature, and conveyor speed.
- Construction: Robust frame and components built for industrial environments.
6. Benefits of Using a Specialized Machine
Investing in a dedicated XPS foam board packaging machine offers significant advantages:
- Enhanced Product Protection: Minimizes damage from handling, moisture, and contaminants.
- Improved Packaging Efficiency: Increases throughput compared to manual methods, reducing bottlenecks.
- Consistent Packaging Quality: Ensures every board or bundle is sealed and wrapped uniformly.
- Professional Product Presentation: Enhances the perceived value and protects brand image.
- Reduced Labor Costs: Automation decreases the need for manual labor in the packaging process.
- Optimized Material Usage: Precise control can lead to more efficient use of shrink film.
7. Applications Across Industries
These machines are vital in sectors that handle large XPS foam boards, including:
- Building Material Manufacturing: Packaging insulation panels directly off the production line.
- Construction Supply Distribution: Protecting boards during storage and transit to job sites.
- Wholesale and Retail: Ensuring products are presented professionally and protected in warehouses and showrooms.
- Related Industries: Packaging similar large, flat products like Expanded Polystyrene (EPS) panels, composite boards, or large signage materials.
door shrinking machine with motion sealer4 8. Considerations for Implementation
Before integrating such a machine, consider:
- Footprint: Ensure sufficient floor space for the machine, including infeed and outfeed areas.
- Power Requirements: Verify electrical supply compatibility.
- Air Supply: Some sealing systems may require compressed air.
- Operator Training: Personnel need training for safe operation and basic maintenance.
- Maintenance Schedule: Regular upkeep is essential for longevity and optimal performance.
- Integration: How the machine fits into the existing production or packaging line.
Conclusion
Properly packaging large XPS foam boards is essential for preserving their quality and integrity from the factory to the end-user. Specialized sealing and shrink wrap machines offer an efficient, reliable, and protective solution tailored to the unique challenges these materials present. By automating the sealing and shrink-wrapping process, manufacturers and distributors can enhance product protection, improve operational efficiency, and ensure their products arrive in optimal condition.