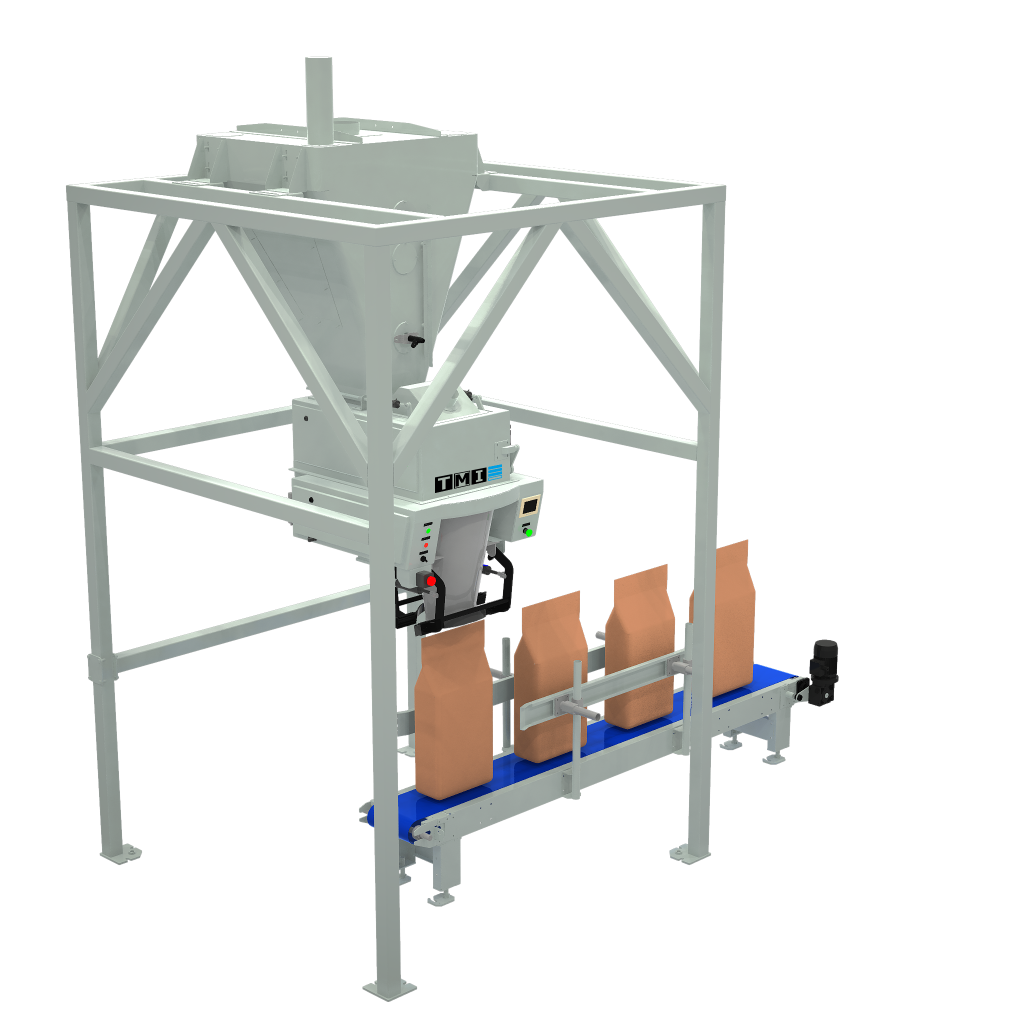
1. Understanding Versatile Semi-Automatic Bagging Machines for Optimal Packaging
In demanding manufacturing and logistics environments, optimizing packaging operations is critical for efficiency and cost control. Businesses continually seek methods to accelerate processes, enhance throughput, and ensure consistent product quality. The versatile semi-automatic bagging machine emerges as a pivotal technology in this pursuit. This guide explores the capabilities of these machines, detailing how they significantly improve packaging speed and accuracy, offering a competitive advantage for diverse industrial applications.
2. Defining Semi-Automatic Bagging Machines
A semi-automatic bagging machine automates key stages of the bagging process while incorporating necessary operator involvement. This configuration balances the efficiency gains of automation with the flexibility and oversight offered by manual control, making it distinct from fully manual or fully automated packaging lines.
2.1 Key Operational Features:
- Adjustable Parameters: Allows configuration for various bag sizes and types.
- Automated Bag Handling: Features mechanisms for automatic bag opening and positioning for filling.
- Controlled Filling: Integrates systems (e.g., weighers, augers, counters) for accurate product dosing.
- Semi-Automated Sealing: Incorporates heat sealers, stitchers, or other closing mechanisms activated by the operator or automatically after filling.
- Variable Fill Rates: Enables adjustment of filling speed based on product characteristics and desired throughput.
- Operator Interface: Typically includes intuitive controls (touchscreens or buttons) for setup and operation.
The "semi-automatic" designation signifies that an operator typically initiates each cycle, places the bag for filling, and manages the removal of filled bags, ensuring adaptability within the packaging workflow.
3. The Evolution from Manual to Semi-Automated Bagging
Understanding the progression of packaging technology highlights the value proposition of semi-automatic systems:
- Manual Bagging: Entirely reliant on human labor; slow, inconsistent, and ergonomically challenging.
- Basic Mechanical Aids: Simple funnels or scoops offering marginal improvement over purely manual methods.
- Semi-Automatic Bagging Machines: Integrate mechanical and control systems to automate filling and often sealing, significantly boosting output while retaining operator oversight. This represents a crucial step-up for many operations.
- Fully Automatic Bagging Lines: End-to-end automation requiring minimal human intervention; suited for high-volume, dedicated production lines.
Semi-automatic bagging machines occupy a critical middle ground, providing substantial efficiency gains over manual methods without the high capital investment and complexity associated with fully automated lines, making them ideal for small-to-medium enterprises (SMEs) or operations with diverse product lines.
4. Quantifying the Speed Advantage: Boosting Throughput
A primary benefit of adopting semi-automatic bagging technology is the significant increase in packaging speed. Comparative throughput rates illustrate this impact:
- Manual Bagging: Typically achieves 3-8 bags per minute (BPM), highly dependent on operator skill and product complexity.
- Semi-Automatic Bagging: Can consistently operate at 10-25+ BPM, influenced by the specific machine design, product flow characteristics, bag size, and operator efficiency.
- Potential Speed Increase: Often represents a 150% to 400% improvement over manual methods.
This acceleration allows businesses to meet tighter deadlines, handle larger order volumes, and improve overall operational responsiveness without necessarily scaling their workforce proportionally.
5. Enhancing Packaging Accuracy: Precision and Consistency
While speed is crucial, accuracy is paramount for quality control, cost management, and customer satisfaction. Semi-automatic baggers deliver superior precision through several mechanisms:
5.1 Precise Weight or Volume Control
Integrated weighing systems (like net weigh or gross weigh scales) or volumetric fillers ensure each bag contains the specified amount of product. This is vital for:
- Granular Products: Grains, seeds, pellets, plastic resins.
- Powders: Chemicals, food ingredients, additives.
- Small Parts: Hardware, fasteners, electronic components.
- Compliance: Meeting regulatory requirements for net weight labeling (e.g., NIST Handbook 133 in the U.S.).
Benefit: Minimizes product giveaway, ensures consistent value for the end-user, and meets legal standards. Typical accuracies can range from +/- 0.1% to 1% depending on the system and product.
5.2 Uniform Bag Filling and Presentation
Automated filling ensures consistent fill levels and product density within each bag. This uniformity is important for:
- Shelf Appeal: Consistent appearance for retail products.
- Secondary Packaging: Ensuring bags fit correctly into cartons or cases.
- Pallet Stability: Uniform bags stack more securely.
Benefit: Improves product presentation, simplifies downstream handling and logistics, and enhances brand perception.
5.3 Reduction of Human Error
Automating the filling and often the sealing process drastically reduces errors associated with manual fatigue or inconsistency, leading to:
- Fewer Under/Overfills: Direct cost savings on product.
- Reduced Product Waste: Less spillage during filling.
- Consistent Seal Quality: Prevents leaks and ensures product integrity.
Benefit: Significant cost reduction through waste minimization and improved overall product quality control.
6. Operational Versatility: Adapting to Diverse Needs
Modern semi-automatic bagging machines are engineered for flexibility, capable of handling a wide spectrum of products and packaging materials.
6.1 Broad Product Compatibility
These systems can be configured for various product types:
- Free-Flowing Granules: Rice, beans, plastic pellets, sand, salt.
- Powders & Fine Granules: Flour, cement mix, spices, chemical powders.
- Irregular Small Solids: Bolts, nuts, electrical connectors, candies, small hardware kits.
- Some Semi-Free-Flowing Products: Animal feed, certain snack foods, wood pellets. (May require specific feeder designs).
This adaptability allows a single machine to potentially service multiple product lines, enhancing asset utilization.
6.2 Packaging Material Flexibility
Semi-automatic baggers are compatible with common bag formats and materials:
- Open-Mouth Bags: Pre-made bags requiring filling and sealing.
- Bag Materials: Polyethylene (PE), polypropylene (PP), multi-wall paper, woven poly, laminated films.
- Bag Types: Pillow bags, gusseted bags, stand-up pouches (SUP), block-bottom bags.
7. Cost-Effectiveness: A Balanced Investment in Automation
Semi-automatic bagging machines provide a compelling return on investment (ROI) for many operations.
7.1 Lower Initial Capital Outlay
Compared to fully automated systems, the initial purchase price of a semi-automatic bagger is significantly lower, making automation accessible for businesses with moderate budgets or production volumes.
7.2 Reduced Labor Costs per Unit
While an operator is required, one person can manage the output equivalent of multiple manual packers. This drastically reduces the labor cost component per packaged unit and frees up personnel for higher-value tasks.
7.3 Minimized Product Waste and Rejects
The enhanced accuracy in filling and sealing directly translates to less product giveaway and fewer rejected packages due to defects, leading to tangible material cost savings.
7.4 Scalability and Integration Potential
Many semi-automatic systems are designed with future growth in mind. They can often be integrated with conveyors, checkweighers, metal detectors, or case packers as production needs increase, protecting the initial investment.
8. Improving Workplace Safety and Ergonomics
Beyond efficiency, semi-automatic bagging machines contribute positively to the work environment.
8.1 Reduced Risk of Repetitive Strain Injuries (RSIs)
Automating tasks like scooping, weighing, and often bag sealing alleviates the repetitive motions common in manual bagging, which are known causes of RSIs like carpal tunnel syndrome or back strain.
8.2 Enhanced Ergonomic Design
Manufacturers increasingly focus on ergonomics:
- Adjustable Machine Height: Accommodates different operator statures.
- Accessible Controls: User-friendly interfaces positioned for comfortable operation.
- Automated Bag Handling: Reduces awkward lifting and manipulation of empty bags.
- Integrated Bag Closing: Eliminates manual sealing motions.
Benefit: Less operator fatigue, improved morale, and potentially lower workers' compensation claims. Referencing ergonomic guidelines from bodies like [OSHA (Occupational Safety and Health Administration)] can be beneficial when selecting equipment.
8.3 Minimized Operator Exposure
For dusty, hazardous, or sensitive products, automating the filling process reduces direct operator contact, improving hygiene and safety. Dust collection ports are often standard or optional features.
9. Seamless Integration with Production Lines
Semi-automatic baggers are designed to fit into broader production workflows.
9.1 Upstream and Downstream Connectivity
- Infeed Systems: Easily connect to product supply lines via hoppers, conveyors, or elevators.
- Outfeed Conveyors: Facilitate smooth transfer of filled bags to checkweighing, sealing, palletizing, or case packing stations.
9.2 Ancillary Equipment Integration
- Printers/Coders: Integrate inkjet or thermal transfer printers for date/batch coding directly onto bags.
- Label Applicators: Apply pre-printed labels automatically.
- Checkweighers: Verify final package weight and reject out-of-tolerance bags.
- Metal Detectors: Ensure product safety, especially in food or pharmaceutical applications.
9.3 Data Communication Capabilities
Advanced models may offer communication protocols (e.g., Ethernet/IP, Modbus TCP) allowing integration with plant-level control systems (SCADA) or Manufacturing Execution Systems (MES) for:
- Production Monitoring: Real-time tracking of output, uptime, and efficiency.
- Recipe Management: Remotely download product parameters.
- Quality Data Logging: Record weight data for traceability.
10. Key Industries Leveraging Semi-Automatic Bagging
The adaptability of these machines makes them indispensable across numerous sectors:
- Food Processing: Coffee beans, snack foods, frozen vegetables, spices, bakery mixes.
- Pet Food: Dry kibble, birdseed, cat litter.
- Agriculture: Seeds, fertilizers, animal feed supplements, soil amendments.
- Chemicals: Resins, pigments, detergents, non-hazardous powders, masterbatch.
- Building Materials: Cement mix, grout, sand, aggregates, decorative stone.
- Hardware & Industrial Parts: Fasteners (nails, screws), small components, fittings.
- Horticulture: Potting soil, mulch, compost.
11. Maintenance and Longevity: Ensuring Peak Performance
Consistent performance and a long service life depend on proper maintenance practices.
11.1 Routine Cleaning
- Schedule: Daily or weekly, depending on product characteristics (dusty vs. clean).
- Focus Areas: Hoppers, feed mechanisms (augers, belts), weigh buckets, fill spouts, sealing jaws/bands.
- Benefit: Prevents cross-contamination, ensures accurate weighing, maintains seal integrity.
11.2 Preventive Maintenance (PM)
Follow the manufacturer's recommended PM schedule, typically including:
- Lubrication: Greasing bearings and lubricating moving parts.
- Inspection: Checking belts, chains, pneumatic lines, electrical connections.
- Wear Part Replacement: Regularly replacing items like sealing bands, cutter blades, gaskets based on usage.
- Calibration: Periodically verifying and calibrating weighing systems using certified weights.
11.3 Operator Training
Ensure operators are trained on:
- Proper Operation: Including startup, shutdown, bag changes, parameter adjustments.
- Basic Troubleshooting: Identifying common issues (e.g., poor seals, weight inaccuracies).
- Cleaning Procedures: Performing routine cleaning correctly.
- Safety Features: Understanding E-stops and guarding.
11.4 Software & Firmware Updates
For machines with programmable logic controllers (PLCs) or advanced interfaces, keep software/firmware updated as recommended by the manufacturer to benefit from performance improvements or bug fixes.
12. Future Outlook: The Evolution of Bagging Technology
Semi-automatic bagging technology continues to evolve, driven by broader industrial trends:
12.1 Increased Connectivity (IIoT)
- Remote Monitoring: Accessing machine status and performance data remotely.
- Predictive Maintenance: Using sensor data and analytics to anticipate failures before they occur.
- Cloud Integration: Storing production data for analysis and reporting.
12.2 Focus on Sustainability
- Material Compatibility: Enhanced capability to handle thinner films, recycled content, and compostable/biodegradable materials reliably.
- Energy Efficiency: Designs optimized for lower power consumption.
12.3 Enhanced Flexibility and Automation
- Robotic Integration: Potential for collaborative robots (cobots) to handle bag placement or removal, bridging the gap towards full automation.
- Automatic Changeovers: Faster, tool-less adjustments between different bag sizes or product types.
- Advanced Sensing: Vision systems for quality inspection or improved bag handling.
12.4 Intuitive Human-Machine Interfaces (HMIs)
- Larger Touchscreens: Easier navigation and data visualization.
- Guided Troubleshooting: On-screen diagnostics and step-by-step repair guidance.
- Mobile Device Integration: Potential for monitoring or control via tablets/smartphones.
13. Conclusion: Optimizing Packaging with Semi-Automatic Solutions
Semi-automatic bagging machines offer a powerful combination of increased speed, enhanced accuracy, operational flexibility, and cost-effectiveness. They represent a practical and scalable automation step for businesses aiming to improve packaging efficiency without committing to the higher cost and complexity of fully automated lines.
By significantly boosting throughput, ensuring consistent product weights and fills, accommodating diverse products and materials, and improving workplace ergonomics, these machines deliver tangible benefits. Their ability to integrate with other production equipment and potentially plant-wide data systems further enhances their value.
Investing in a suitable semi-automatic bagging machine is a strategic move to streamline operations, reduce costs associated with waste and labor, improve product quality, and gain a competitive edge. For operations currently relying on manual bagging or struggling with inefficient older equipment, evaluating the capabilities of modern semi-automatic baggers is a critical step towards optimizing the entire packaging process.