Understanding the Unloading Pushing Type Coil Packing Line: Enhancing Efficiency and Protection
Efficiently handling and packaging metal coils is crucial in demanding industrial environments like steel mills, service centers, and fabrication shops. Proper packaging protects valuable coils from environmental damage (dust, moisture, corrosion) and handling mishaps during transit and storage. The coil packing line represents a key piece of automation in this process, and the unloading pushing type configuration offers specific advantages for streamlined workflows.
What is an Unloading Pushing Type Coil Packing Line?
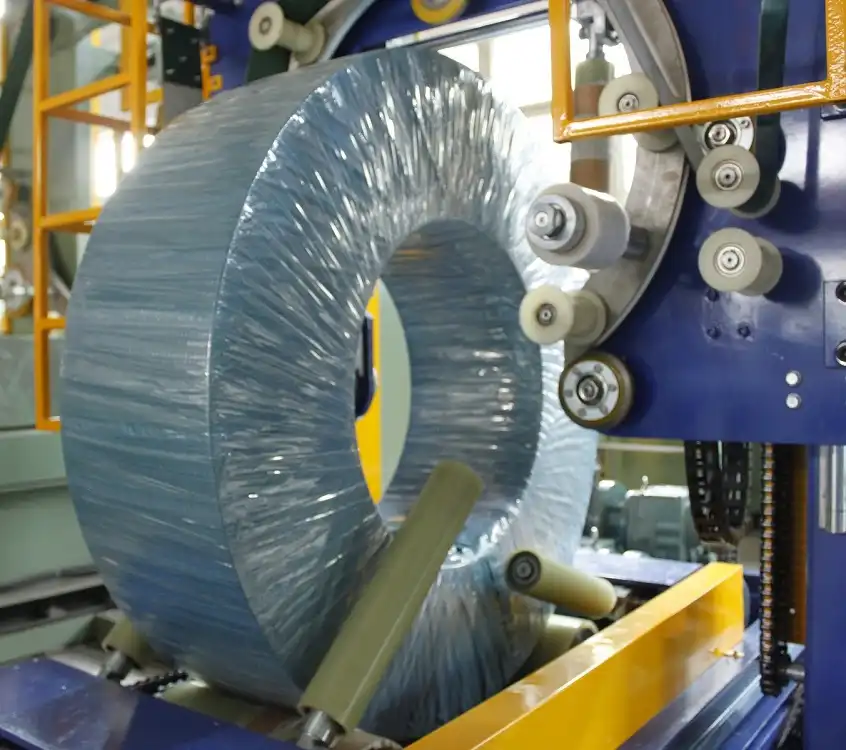
An unloading pushing type coil packing line is an automated system designed specifically to receive coils—typically from a production line, slitter, or turnstile—push them onto the packaging station, wrap them securely, and then discharge them for transport or storage. This configuration is commonly employed where floor space optimization and seamless integration with upstream processes are priorities.
Operational Workflow Explained
The typical operation sequence involves:
- Coil Reception: The line receives a coil, often via crane, C-hook, or coil car, onto an entry saddle or conveyor section.
- Automatic Transfer: A pusher mechanism gently but firmly transfers the coil from the receiving station onto the main packing line conveyor or rollers. This automated step eliminates manual handling risks and delays.
- Positioning: The coil moves to the wrapping station, where rollers may adjust its position for optimal packaging. Vibration dampening features ensure stability during this process.
- Automated Wrapping: The core of the line, where the coil is automatically wrapped using selected materials dispensed from integrated storage units. This often involves a wrapping shuttle that orbits the coil.
- Discharge: Once wrapped, the coil is moved off the packing station, ready for labeling, strapping (if required), and pickup by forklift or crane.
Key Features and Components Driving Performance
These lines incorporate several advanced features for reliable and efficient operation:
- Automated Control Systems: Programmable Logic Controllers (PLCs) and Human-Machine Interfaces (HMIs) provide centralized control over the entire process. They allow operators to set parameters, monitor operations, store different packing recipes, and troubleshoot issues quickly. Alarms automatically indicate malfunctions.
- Integrated Material Handling: Dedicated storage for various packing materials (stretch film, VCI paper, woven fabric) ensures continuous operation. Automated dispensing and cutting systems minimize waste and manual intervention.
- Precise Tension Control: The ability to adjust the tension of wrapping materials like stretch film is critical. Proper tension ensures a secure wrap without damaging the coil edges, providing consistent package integrity.
- Safety Mechanisms: Safety is paramount. Features include overload protection, power and mechanical interlocks, emergency stops, and often light curtains or safety fencing to protect personnel during operation. Soft start and stop functions prevent abrupt movements, enhancing both safety and equipment longevity. ([See OSHA guidelines for machine guarding] for general safety principles).
- Flexible Operation Modes: Most lines offer both fully automatic and manual modes, facilitating setup, maintenance, and handling of non-standard coils or situations.
Common Packaging Materials Utilized
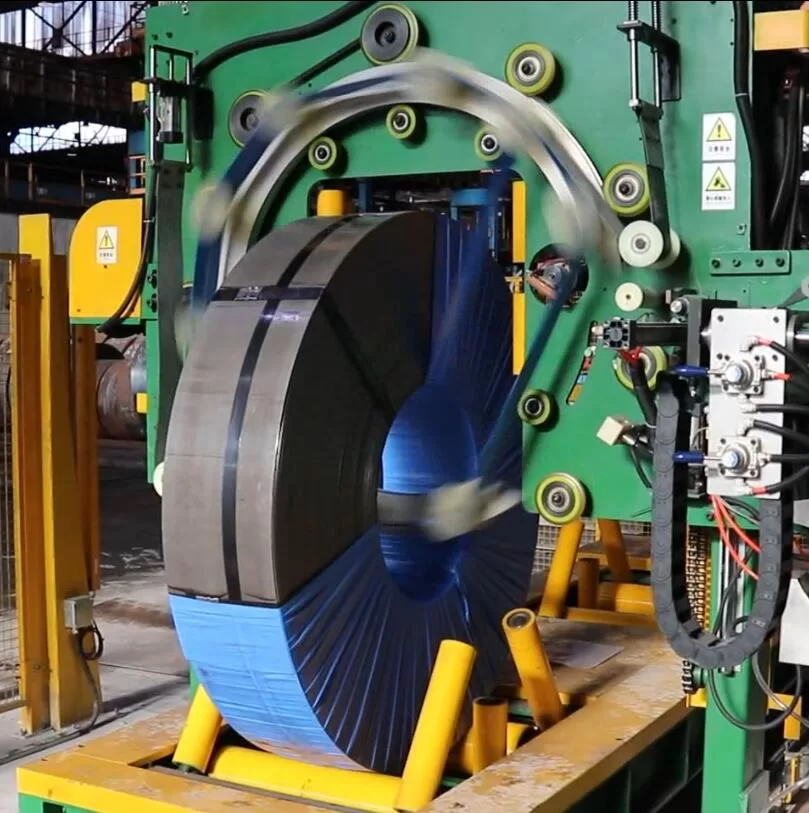
The choice of packaging material depends on the coil type, storage duration, transit conditions, and customer requirements:
- Stretch Film: Provides containment, stability, and protection against dust and moisture.
- VCI (Volatile Corrosion Inhibitor) Paper/Film: Releases chemicals that create a protective atmosphere around the metal surface, preventing rust, especially crucial for steel coils.
- Woven Fabric (PP/HDPE): Offers robust protection against tears, punctures, and environmental factors.
- Wrapping Paper (Kraft Paper): Provides a basic layer of protection and surface separation.
Benefits of Implementing an Unloading Pushing Type System
Automating coil packaging with this type of line delivers significant operational advantages:
- Enhanced Productivity: Continuous, automated operation drastically reduces cycle times compared to manual or semi-automatic methods.
- Reduced Labor Costs: Minimizes the need for manual handling and wrapping, freeing up personnel for other tasks.
- Improved Safety: Eliminates strenuous and potentially hazardous manual coil manipulation and wrapping tasks.
- Consistent Packaging Quality: Automated control ensures every coil is wrapped to the same specifications, improving load integrity and protection.
- Better Coil Protection: Secure, uniform wrapping minimizes damage from handling, transit vibrations, and environmental factors like moisture and dust.
- Streamlined Workflow Integration: The pushing mechanism facilitates smooth integration with upstream equipment like slitters or downenders.
Industries Served
Unloading pushing type coil packing lines are essential equipment in various sectors, including:
- Steel Mills
- Aluminum Mills
- Metal Service Centers
- Automotive Stamping Plants
- Tube and Pipe Mills
- Wire and Cable Manufacturing
Conclusion
The unloading pushing type coil packing line is a sophisticated automation solution that addresses the critical need for safe, efficient, and protective packaging of metal coils. By integrating automated handling, wrapping, and control systems, these lines enhance productivity, improve worker safety, ensure consistent package quality, and protect valuable metal products throughout the supply chain. For facilities handling significant volumes of coils, implementing such a system represents a strategic investment in operational excellence.