Essential Packaging Solutions for Steel Coil Service Centers: A Strategic Guide
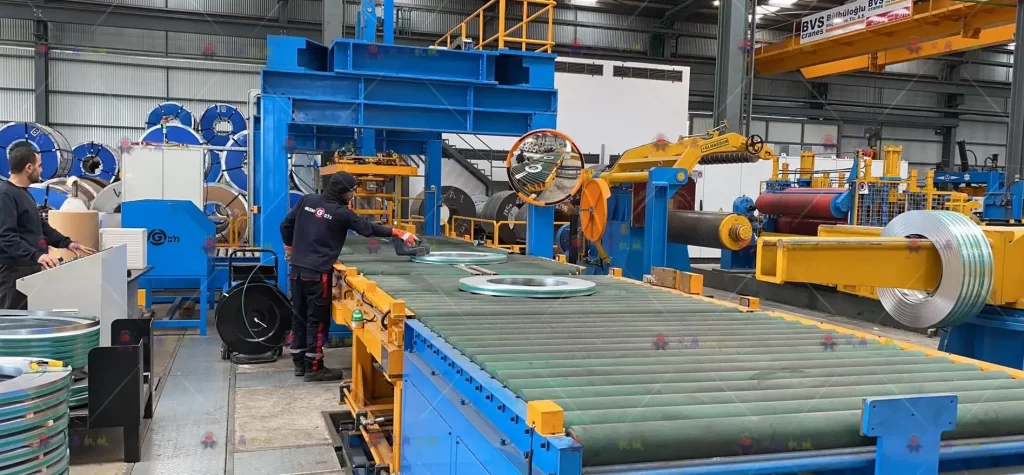
Introduction
Investing in a steel coil service center is a significant undertaking requiring careful planning across all operational aspects. A critical, yet sometimes underestimated, component is the packaging solution. The right packaging strategy directly impacts operational efficiency, cost-effectiveness, product quality, and safety. This guide provides essential insights into comprehensive steel coil packaging solutions, focusing on long-term planning and alignment with Industry 4.0 principles, crucial for making an informed investment decision.
1. Key Considerations for Future-Proofing Your Packaging Line
Successfully integrating a packaging line into a modern steel coil service center involves looking beyond immediate needs. Aligning with Industry 4.0 trends ensures longevity, efficiency, and competitiveness.
1.1. Data Integration (Datamation)
Implementing robust data management systems, such as an Enterprise Resource Planning (ERP) or Manufacturing Execution System (MES), is fundamental. These systems should track materials and processes from production through packaging to final logistics.
- Benefits: Provides comprehensive oversight, enabling identification of bottlenecks, data-driven decision-making for efficiency improvements, streamlined inventory management, reduced human error, and improved inter-departmental communication.
- Customer Insights: Leverages data to refine service offerings and maintain a competitive advantage.
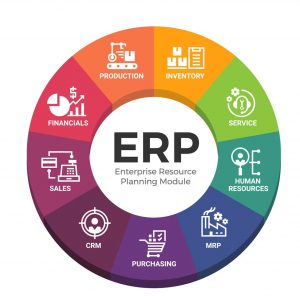
1.2. Automation Strategy
Investing in automated machinery for unmanned or semi-automated packaging is crucial for modern operations.
- Advantages: While initial investment can be substantial, long-term benefits include significantly reduced labor costs, increased throughput, consistent packaging quality, and enhanced workplace safety.
- Phased Approach: If budget constraints are a concern, select packaging solutions designed with modularity, allowing for future upgrades towards full automation as the business grows.
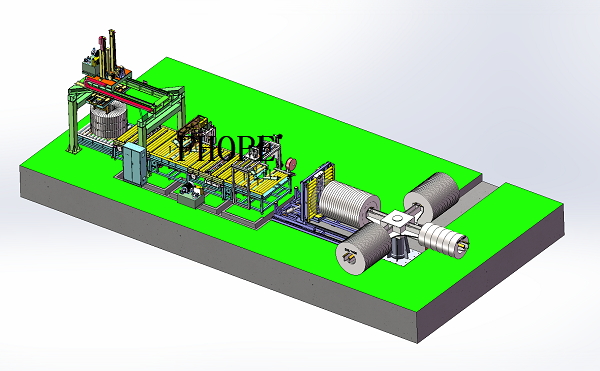
1.3. Scalability and Modularity
Your chosen packaging solution must accommodate business growth.
- Flexibility: Opt for modular equipment and systems that can be easily expanded, reconfigured, or upgraded as production volumes increase or market demands shift.
- Cost-Effectiveness: This foresight helps avoid expensive complete overhauls and ensures adaptability without significant downtime.

2. Components of a Comprehensive Automated Steel Coil Packaging Line
An effective automated line integrates several key stages to handle and package steel coils efficiently and safely.
2.1. Coil Transfer (Coil Car)
Automated coil cars are used to transfer slit coils safely from the slitting/rewinding machine exit point to the start of the packaging line.
- Function: Reduces manual handling, minimizes potential coil damage during transit, and improves overall line efficiency and operator safety.
- Configuration: Available in various load capacities and designs (e.g., floor-mounted, overhead) to suit different facility layouts and coil sizes.

2.2. Automated Coil Wrapping
Wrapping machines apply protective materials (like stretch film, VCI paper, or plastic sheets) around the coil.
- Purpose: Ensures consistent, secure packaging, enhances product presentation, and crucially protects coils from environmental factors like moisture, dust, and corrosion during storage and transport.
- Customization: Advanced machines offer programmable wrapping patterns, tension control, and compatibility with various materials to meet specific protection requirements.

2.3. Automated Coil Strapping
Strapping machines apply steel or plastic straps circumferentially (eye-to-sky) or radially (through the eye) to secure the coil.
- Function: Prevents coil unwinding and provides stability during handling, storage, and shipping, reducing the risk of damage and accidents. Increases efficiency by automating a physically demanding task.
- Technology: Modern systems handle various strap types, sizes, and tensions, often incorporating features like automatic strap feeding, cutting, and sealing for reliable operation.

2.4. Automated Coil Stacking
Automated systems stack packaged coils onto pallets or directly onto each other according to predefined patterns.
- Benefits: Optimizes storage space, significantly reduces manual lifting and associated injury risks, improves stacking consistency and stability, and speeds up the process compared to manual methods.
- Adaptability: Can be designed to handle various coil dimensions (ID, OD, width) and weights, integrating seamlessly with upstream and downstream automation.

2.5. Automated Weighing and Labeling
Integrated systems accurately weigh each coil and apply labels with essential information.
- Importance: Ensures precise data for shipping documents and inventory management, reducing billing errors. Streamlines product identification and traceability throughout the supply chain.
- Integration: Advanced systems print barcodes, QR codes, or RFID tags, often interfacing directly with ERP/WMS to update records automatically.

2.6. Automated Dispatch and Logistics Integration
This involves the automated transport of finished, packaged, and labeled coils (often stacked on pallets) from the packaging line exit to designated warehouse storage locations or shipping docks.
- Efficiency: Utilizes conveyors, AGVs (Automated Guided Vehicles), or other transfer systems to minimize manual transport, reduce transit time, and enhance overall logistics flow.
- Connectivity: Can be fully integrated with Warehouse Management Systems (WMS) for real-time inventory updates, optimized storage allocation, and efficient order fulfillment preparation.

Conclusion
Selecting the right packaging solution is a strategic decision pivotal to the success of a steel coil service center investment. By prioritizing data integration, embracing automation, ensuring scalability, and understanding the components of a comprehensive packaging line, businesses can enhance efficiency, reduce costs, improve product quality, and position themselves for long-term success in an increasingly competitive and technologically advancing industry. Careful consideration of these factors from the outset will yield substantial returns throughout the operational life of the service center.