Understanding Semi-Automatic Pipe Coiling Machines for Efficient Handling
Managing long lengths of flexible pipe and hose efficiently is a common challenge in manufacturing and distribution. Coiling provides a practical solution for storage, transport, and installation. While manual coiling can be labor-intensive and inconsistent, fully automated systems represent a significant investment. Bridging this gap are semi-automatic pipe coiling machines, offering a balance of mechanization and operator control. This guide explores the function, benefits, and considerations surrounding these essential pieces of equipment. For fully automated solutions, explore options in automatic coiling machines.
What is a Semi-Automatic Pipe Coiling Machine?
A semi-automatic pipe or hose coiler is a machine designed to wind flexible products like plastic pipes, conduits, tubes, or hoses into neat coils. The "semi-automatic" designation means that while the machine performs the core winding action, human operators are typically involved in processes such as:
- Loading the pipe or hose end onto the winding core.
- Initiating and monitoring the winding cycle.
- Cutting the pipe/hose once the desired length is reached.
- Securing the coil (manually or with integrated assistance).
- Unloading the finished coil.
Key features often include:
- Variable Speed Control: Allows adjustment of winding speed based on product type and line speed.
- Adjustable Tension Control: Crucial for creating tight, stable coils without damaging the product. Tension can often be adjusted to suit different materials and requirements.
- Traverse System: Guides the pipe or hose back and forth across the coiler drum or core to ensure an even, level wind.
- Configurable Core: The central drum or tooling can often be adjusted to produce coils of different inner diameters and widths.
- Single or Dual Winders: Some setups feature two winding heads (dual winders) allowing for nearly continuous operation – while one coil is being finished and unloaded, the other head can begin winding.
automatic pipe coiling machine, automatic hose coiling machine3 The Semi-Automatic Coiling Process Explained
While specific operations vary by machine design, a typical workflow involves:
- Setup: The operator configures the machine for the specific pipe/hose diameter and desired coil dimensions (inner diameter, width, length). Winding speed and tension are set.
- Loading: The leading end of the pipe or hose (often coming directly from an extruder or payoff stand) is manually fed and secured to the coiler's core or grippers.
- Winding: The operator initiates the winding cycle. The machine rotates the core, pulling the product and winding it layer by layer. The traverse system guides the product for an even lay. The operator monitors the process and the length counter.
- Cutting & Securing: Once the target length is reached, the machine stops (or the operator stops it). The operator cuts the pipe/hose. The tail end of the coil is then secured, typically using tape, straps, or stretch film applied manually or with simple tools.
- Unloading: The finished coil is removed from the machine. If using a collapsible core, it's retracted to allow easy removal. The machine is then ready for the next cycle.
Advantages of Semi-Automatic Pipe Winders
Compared to manual methods and fully automatic systems, semi-automatic coilers offer distinct advantages:
- Improved Consistency: Produces uniform coils compared to manual winding.
- Increased Efficiency: Significantly faster than coiling by hand, boosting throughput.
- Reduced Labor Strain: Minimizes the physical effort and repetitive motions required for manual coiling, improving ergonomics.
- Better Coil Quality: Controlled tension and level winding result in stable, neat coils suitable for packaging and transport.
- Moderate Investment: Offers mechanization benefits at a lower capital cost than fully automatic systems.
- Flexibility: Can often handle a range of product sizes and materials with reasonable changeover times.
Key Considerations When Selecting a Machine
Choosing the right semi-automatic coiler depends on specific operational needs:
- Product Range: Ensure the machine accommodates your minimum and maximum pipe/hose diameters and material types (e.g., PEX, PVC, PE, rubber).
- Coil Specifications: Verify the machine can produce the required coil inner/outer diameters, widths, and maximum weight.
- Winding Speed: Must be compatible with your production line speed (e.g., extruder output).
- Tension Control: The precision and range of tension adjustment needed for your products.
- Footprint and Layout: Ensure sufficient space for the machine and operator access.
- Integration: Consider how the coiler will interface with upstream (extrusion) and downstream (packaging/handling) processes.
Semi-Automatic vs. Fully Automatic Coiling Systems
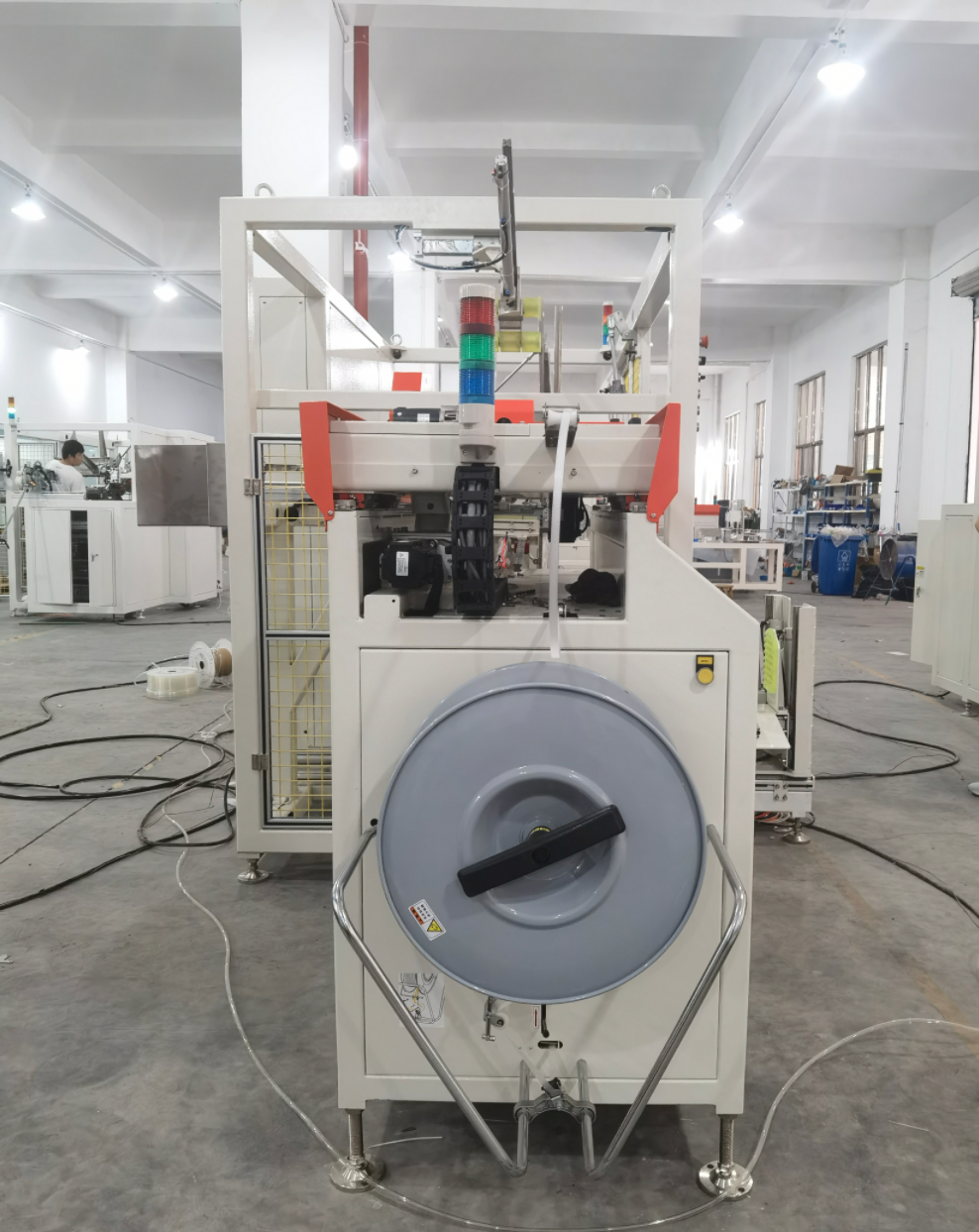
While semi-automatic machines require operator intervention for loading, unloading, and securing, fully automatic pipe coiling and strapping machines automate these steps. These advanced systems typically include:
- Automatic Pipe Accumulation & Feeding: Manages the incoming product flow.
- Automatic Cutting: Cuts the pipe/hose to length without operator input.
- Integrated Strapping/Wrapping: Automatically applies securing straps or stretch film to the finished coil.
- Automatic Coil Ejection: Discharges the finished coil onto a conveyor or holding area.
Fully automatic systems are ideal for high-volume production lines where minimizing labor and maximizing throughput are primary goals. However, they come with a higher initial investment and may require more specialized maintenance. Semi-automatic systems strike a balance, suitable for moderate production volumes or operations where flexibility and cost-effectiveness are key priorities. For insights into different equipment capacities, refer to industry examples of pipe handling solutions. You can find relevant information on plastic pipe standards and manufacturing practices from organizations like the Plastics Pipe Institute (PPI).
Examples of Coiler Configurations and Capacities
Coiling machines are available in various sizes and configurations to handle different product dimensions and production needs. Below are examples illustrating different capacity ranges:

Example: Small Diameter Pipe Coiler (FCL100 Type)
Suitable for smaller diameter pipes, often seen in pneumatic or fluid transfer applications.

Example: Integrated Coiling & Strapping (FCL200 Type)
Illustrates machines combining coiling and automatic strapping for enhanced automation.

Example: Medium Capacity Hose Coiler (FCL400 Type)
Designed for handling medium-sized industrial hoses or pipes.

Example: High-Speed Hose Coiler (FCL600 Type)
Represents configurations focused on higher throughput speeds.

Example: Large Diameter Pipe Coiler (FCL-800 Type)
Built to handle larger, often heavier pipes used in construction or infrastructure.

Example: Heavy-Duty Pipe Coiler (FCL1200 Type)
Machines designed for the largest and heaviest flexible pipe products.
Note: The links above point to examples of different machine types and capacities for illustrative purposes.
Conclusion
Semi-automatic pipe coiling machines represent a valuable tool for manufacturers and processors dealing with flexible pipe and hose. By mechanizing the winding process while retaining operator control for specific tasks, these machines offer significant improvements in efficiency, consistency, and ergonomics compared to manual methods, without the full investment required for complete automation. Selecting the appropriate coiler based on product specifications, production volume, and integration needs can greatly enhance pipe handling operations.