Enhance Packaging Efficiency: A Guide to Automatic Pallet Wrappers with Auto Film Cut
Manual pallet wrapping can be time-consuming, inconsistent, and physically demanding. In today's fast-paced logistics and manufacturing environments, optimizing end-of-line packaging processes is crucial for maintaining competitiveness. Automatic pallet wrapping machines, particularly those equipped with an automatic film cutting system, offer a significant upgrade in efficiency, safety, and load security.
This guide explores the functionality, benefits, and key considerations of automatic pallet wrappers featuring the auto film cut capability.
1. What is an Automatic Pallet Wrapper with Auto Film Cut?
An automatic pallet wrapper with auto film cut is a sophisticated piece of packaging equipment designed to fully automate the stretch wrapping process for palletized goods. Unlike semi-automatic machines that require operator intervention to attach and cut the stretch film, these fully automatic systems handle the entire cycle from start to finish, including the final step of cleanly cutting the film and often securing the film tail to the load.
2. How Does It Work? The Automated Wrapping Cycle
The operation of an automatic pallet wrapper with film cut is seamless, typically involving these steps:
2.1. Pallet Placement & Cycle Start
The palletized load is placed onto the machine's turntable or conveyed into the wrapping zone (in the case of rotary arm models). Sensors detect the presence of the pallet. The wrapping cycle is initiated either automatically via upstream signals from a conveyor system or by an operator through a control panel.
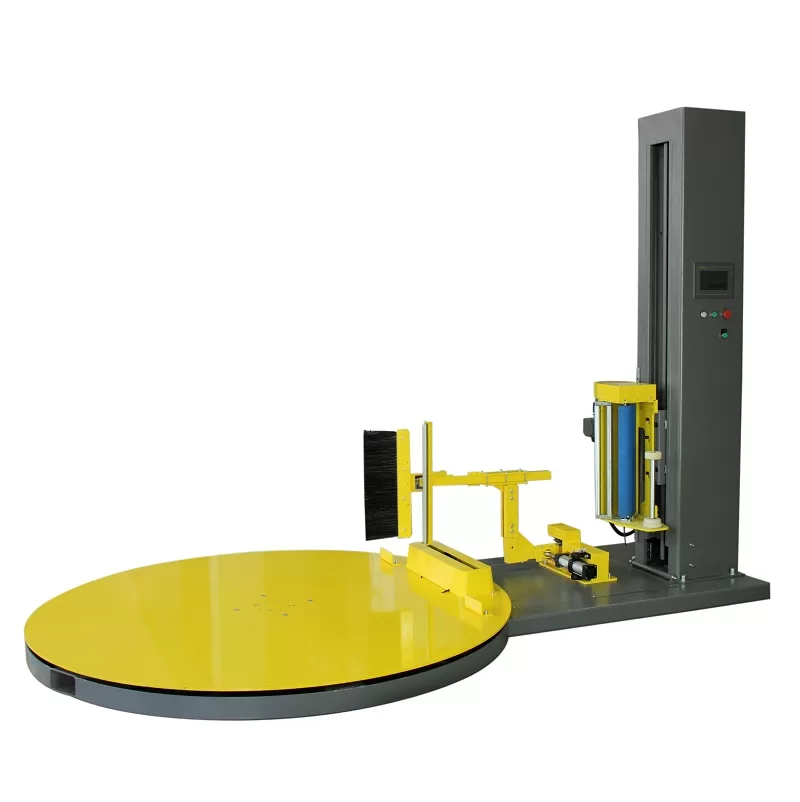
2.2. Automated Wrapping Cycle
The machine executes the pre-programmed wrapping sequence. This usually involves:
- Rotation: The turntable spins the load (or a rotary arm moves around a stationary load).
- Film Dispensing: A film carriage, holding the roll of stretch film, moves vertically up and down the mast.
- Pre-stretching: Most modern machines incorporate a powered pre-stretch system, stretching the film before application (often by 200-300%). This maximizes film yield and enhances load containment forces.
- Parameter Application: The machine precisely follows programmed parameters, including:
- Number of top and bottom wraps.
- Film tension/force-to-load control.
- Wrapping speed (rotation and carriage speed).
- Film overlap percentage.
2.3. Automatic Film Cutting & Securing
Once the wrapping pattern is complete, the machine automatically performs the critical final steps:
- Film Cutting: A mechanism (commonly a hot wire, impulse sealer, or cutting blade) extends to cleanly sever the stretch film near the load.
- Film Tail Securing: Simultaneously or immediately after cutting, a device (like a wipe-down brush, heat sealer, or pneumatic arm) presses the film tail against the wrapped load, ensuring it doesn't unravel during handling or transport.
2.4. Cycle Completion & Pallet Exit
The machine signals cycle completion. The wrapped pallet is then ready for removal by a forklift or automatically transferred downstream via conveyors in an integrated line.
3. Key Advantages of Automatic Film Cut Pallet Wrappers
Integrating an automatic pallet wrapper with film cut technology brings substantial benefits:
- Increased Throughput and Efficiency: Fully automating the process significantly reduces cycle times compared to manual or semi-automatic methods, allowing more pallets to be wrapped per hour.
- Reduced Labor Costs: Operators are freed from the tasks of manually attaching, cutting, and securing the film. They can be reassigned to other value-added activities, lowering direct labor costs per pallet.
- Improved Load Safety and Consistency: Automation ensures every pallet is wrapped according to precise specifications, leading to consistent load containment, reduced product damage during transit, and a lower risk of load failure. The secure film tail prevents snagging and unraveling.
- Optimized Stretch Film Consumption: Powered pre-stretch systems combined with precise control significantly reduce the amount of film used per pallet compared to manual wrapping, leading to material cost savings and reduced environmental impact. Explore film characteristics further at reliable sources.
- Enhanced Operator Safety: Eliminating the need for operators to manually cut film near moving machinery or bend down to secure tails reduces the risk of repetitive strain injuries and accidents.
- Professional Pallet Appearance: The clean cut and securely wiped-down film tail provide a more professional and tidy appearance for shipped goods.
4. Key Features to Consider When Selecting a System

When evaluating automatic pallet wrappers with auto film cut, consider these features:
- Cut and Secure Mechanism: Understand the technology used (hot wire, blade, heat seal, brush) and its suitability for your film type and operating environment.
- Pre-stretch Capability: Look for high-efficiency powered pre-stretch systems (e.g., 250% or higher) for maximum film savings.
- Control System & Programmability: User-friendly interfaces (like touch screens), the ability to store multiple wrap recipes for different load types, and diagnostic capabilities are important.
- Throughput Capacity: Ensure the machine's wrapping speed (pallets per hour) aligns with your production requirements.
- Load Handling: Consider maximum load weight capacity, turntable/wrapping zone dimensions, and suitability for unstable or variable loads.
- Safety Features: Look for comprehensive safety measures like interlocked access doors, safety fencing, light curtains, and emergency stops.
- Integration Options: Evaluate compatibility with existing or planned conveyor systems and plant communication networks if full integration is desired.
5. Conclusion: Streamlining Your End-of-Line Packaging
Automatic pallet wrappers with auto film cut represent a significant step forward in packaging automation. By eliminating manual intervention in the film application and finishing process, these machines deliver measurable improvements in efficiency, cost reduction, load integrity, and operator safety. Evaluating your specific throughput needs, load characteristics, and integration goals will help you select the right system to streamline your end-of-line packaging operations effectively. Investing in this technology can provide a rapid return on investment through labor savings, reduced film consumption, and minimized product damage.