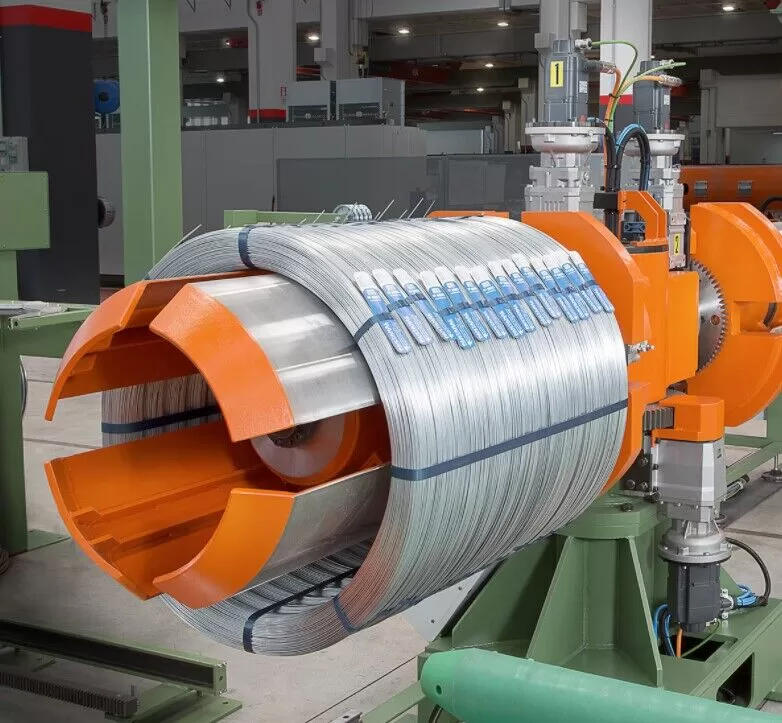
Steel wire coils are indispensable components across numerous sectors, including construction, automotive, and manufacturing. Ensuring their integrity during transport and storage is paramount. However, selecting the appropriate packing material involves navigating a complex web of considerations, including durability, environmental impact, cost-efficiency, and specific protection needs. This comprehensive guide delves into the critical factors and material options to help you choose the optimal packing solution for your steel wire coils, safeguarding your product and streamlining your operations.
The choice of packing material profoundly influences operational success by minimizing damage risks and optimizing logistics costs. For steel wire coils, packaging serves as more than just a covering; it's a vital protective barrier against physical damage, environmental hazards like moisture, and contamination, ensuring the coil's quality from production to end-use.
Selecting the ideal packing material is not a universal formula. It necessitates a thorough understanding of the steel wire coil's characteristics, the environmental conditions it will encounter during transit and storage, regulatory requirements, and alignment with overall business objectives, including sustainability goals. Let's explore the essential considerations and available material solutions.
1. Why is Choosing the Right Packing Material Crucial for Steel Wire Coils?
1.1 The Essential Role of Protection and Preservation
Steel wire coils are susceptible to various forms of damage during handling, transit, and storage. Physical impacts can cause deformation, while exposure to moisture is a primary cause of rust and corrosion. Effective packing materials act as the primary defense against these threats. For example:
- Waterproof Wraps (e.g., Polyethylene Film, Tarpaulins): Shield coils from rain, humidity, and condensation, preventing costly corrosion.
- Reinforced Outer Layers & Edge Protectors: Guard against abrasions, dents, and physical damage during handling and stacking.
- VCI (Volatile Corrosion Inhibitor) Materials: Provide chemical protection against rust, crucial for long-term storage or sea freight.
Furthermore, professional packaging enhances product presentation. Well-packaged steel wire coils reflect higher quality control standards, positively influencing customer perception, even in industrial contexts.
1.2 Minimizing Waste and Maximizing Logistical Efficiency
Strategic packaging choices contribute significantly to operational efficiency. Consider these aspects:
- Material Weight & Flexibility: Lightweight materials like stretch film can reduce transportation costs compared to heavier options. Flexible materials ensure a tight, secure wrap.
- Stacking & Storage: Robust packaging, including appropriate strapping and edge protection, facilitates safe and efficient stacking, optimizing warehouse space.
- Sustainability: Opting for recyclable or reusable packing materials aligns with environmental regulations and corporate sustainability goals, reducing waste disposal costs and enhancing brand image.
1.3 Learning from Industry Best Practices
Leading steel manufacturers continuously innovate their packaging strategies. Many have transitioned from traditional materials like burlap to advanced multi-layer polymer films or VCI-impregnated papers. These modern materials offer superior protection against moisture, UV radiation, and physical stress, ensuring coils arrive in optimal condition, even after long international journeys. Observing these industry shifts can provide valuable insights for refining your own packaging approach.
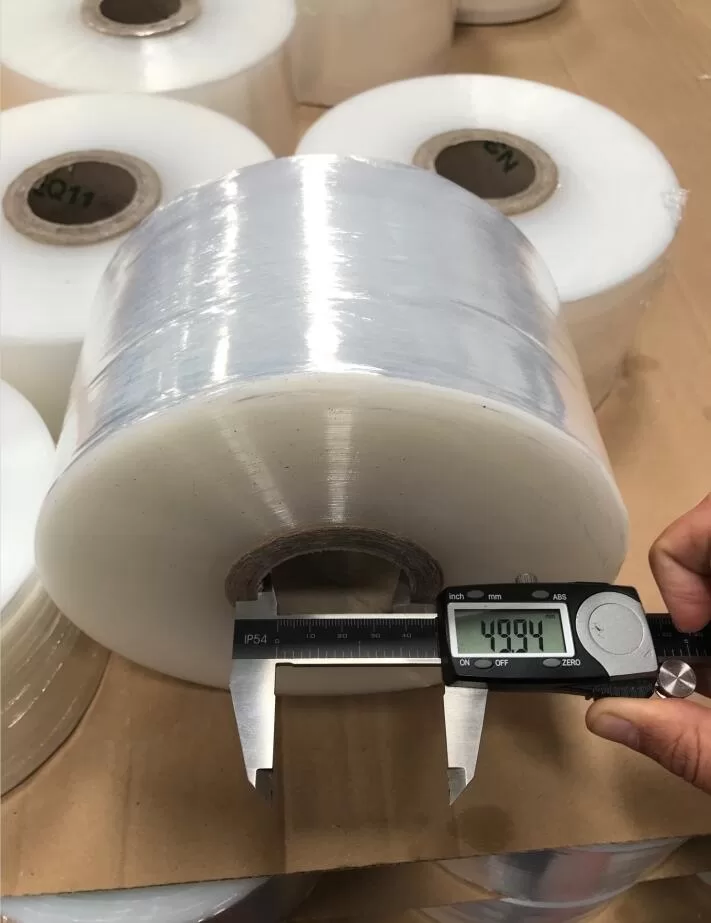
1.4 Understanding the Challenges of Transporting Steel Wire Coils
Transporting steel wire coils presents unique challenges due to their weight, shape, and sensitivity to environmental factors. Safe transit requires tailored packaging solutions that account for:
- Coil Dimensions and Weight: Heavier coils demand stronger strapping and more robust protective layers.
- Handling Methods: Packaging must withstand lifting, loading, and unloading procedures, often involving cranes or forklifts.
- Destination Climate: Coils shipped to humid or coastal areas require enhanced corrosion protection.
A common challenge lies in balancing durability with conformability. The packing material must be tough enough to resist punctures and tears yet flexible enough to wrap snugly around the coil's contours.
1.5 The Financial Impact of Inadequate Packaging
Attempting to save costs by using substandard packing materials often leads to significant financial repercussions. Damaged coils result in:
- Customer dissatisfaction and potential loss of business.
- Increased warranty claims and replacement costs.
- Reputational damage within the industry.
- Delays in delivery and potential contractual penalties.
Investing appropriately in high-quality packing materials, such as durable wraps, strong strapping, and necessary edge protection, is a proactive measure to mitigate these costly risks.
1.6 Key Types of Damage Prevented by Proper Packaging
Effective packaging safeguards steel wire coils from a range of detrimental issues:
- Corrosion (Rust): Caused by moisture, saltwater spray (sea freight), or high humidity. Prevented by waterproof barriers and VCI materials.
- Physical Deformation: Dents, flattening, or edge damage caused by impacts, improper handling, or excessive pressure during stacking. Prevented by cushioning, edge protectors, and secure strapping.
- Contamination: Dirt, dust, or chemical contaminants adhering to the wire surface. Prevented by fully sealed wraps.
- Telescoping or Unraveling: Prevented by proper tensioning and secure strapping around the coil circumference.
Studies and industry experience consistently show that multi-layered packaging systems significantly reduce transit-related damage claims for steel products. Combining appropriate wraps, VCI protection, strapping, and edge protectors is a proven best practice.
2. What Key Factors Influence Packing Material Selection?
2.1 Assessing Environmental Conditions During Transit and Storage
The journey your steel wire coils undertake dictates the level and type of protection needed. Key environmental factors include:
- Humidity and Moisture: Sea freight, transport through rainy regions, or storage in humid warehouses necessitates waterproof materials (e.g., PE films, tarps) and potentially VCI corrosion inhibitors.
- Temperature Fluctuations: Extreme heat or cold can affect material integrity. Ensure chosen materials can withstand the expected temperature range without becoming brittle or losing adhesion.
- UV Exposure: For outdoor storage or long transit times in sunny conditions, UV-resistant materials are advisable to prevent degradation of the packaging itself.
2.2 Adhering to Regulatory and Safety Requirements
Packaging choices are often governed by national and international regulations, industry standards, and specific customer requirements. Considerations include:
- Shipping Regulations: Certain transport modes (e.g., sea freight) may have specific packaging strength or securing requirements (e.g., ISPM 15 for wood pallets).
- Safety Standards: Packaging must ensure safe handling for workers throughout the supply chain.
- Environmental Legislation: Many regions have restrictions on certain plastics or mandate the use of recyclable/biodegradable materials. Non-compliance can lead to fines or shipment rejection. (Consider linking to relevant regulatory bodies or standards organizations here).
2.3 Ensuring Material Compatibility with Coil Specifications
The characteristics of the steel wire coil itself influence material selection:
- Coil Size and Weight: Larger, heavier coils require materials with higher tensile strength and puncture resistance (e.g., heavy-duty films, steel or high-strength polyester strapping).
- Surface Coating/Finish: Coated wires might require non-abrasive inner layers, while uncoated (bright) wire is highly susceptible to rust and benefits significantly from VCI protection.
- End Use Requirements: Some applications might have specific cleanliness standards, requiring packaging that prevents any contamination.

2.4 How Transportation Methods Shape Packaging Needs
The mode of transport significantly impacts packaging requirements:
- Sea Freight: High risk of moisture, salt spray, and longer transit times. Requires robust waterproof barriers, VCI protection, and secure container lashing.
- Road/Rail Freight: Higher risk of vibration and handling impacts. Demands secure strapping, edge protection, and potentially shock-absorbing materials.
- Air Freight: Weight and volume are key cost drivers. Lighter-weight, compact packaging solutions are preferred, though protection remains crucial.
Aligning material properties (e.g., water resistance, impact strength, weight) with the specific demands of the chosen transport method is essential for effective protection.
2.5 The Growing Importance of Sustainability in Material Selection
Sustainability is no longer optional but a core consideration in packaging decisions. Businesses are increasingly seeking eco-friendly options due to:
- Regulatory Pressure: Bans on single-use plastics, extended producer responsibility (EPR) schemes.
- Customer Demand: Environmentally conscious clients prefer suppliers with sustainable practices.
- Corporate Responsibility: Aligning with internal sustainability goals and improving brand image.
Options include recyclable materials (paperboard, specific plastics like PE/PP), materials with recycled content, biodegradable films, and reusable packaging systems (like durable tarps or containers where feasible). While sometimes having a higher initial cost, sustainable options can offer long-term benefits through reduced waste fees and enhanced market appeal. (Consider linking to resources on sustainable packaging standards).
2.6 Balancing Cost Considerations Without Sacrificing Quality
While cost control is vital, it must be balanced against the need for adequate protection. Achieving cost-effectiveness involves:
- Total Cost of Ownership Analysis: Consider not just the material price but the potential costs of damage, claims, and reputational harm resulting from inadequate packaging.
- Material Optimization: Use the right amount of the right material. Over-packaging is wasteful, while under-packaging is risky. Customization can help.
- Supplier Relationships: Build strong relationships with reliable suppliers for potential bulk discounts, consistent quality, and access to material innovations.
- Evaluating Alternatives: Compare different material combinations that offer similar protection levels to find the most economical solution that still meets performance requirements.
3. What Types of Packing Materials Are Best Suited for Steel Wire Coils?
3.1 Protective Wraps: The Primary Barrier
Wraps provide the main shield against environmental factors and contamination. Common choices include:
- Stretch Film (PE): Highly flexible, good cling, provides moderate protection against dust and moisture. Available in various thicknesses and strengths. Cost-effective for lighter coils or as part of a multi-layer system. Often applied using orbital stretch wrappers for efficiency.
- Shrink Film (PE/POF): Provides a tighter, more conforming seal when heat is applied. Offers excellent moisture barrier properties. Suitable for irregular shapes and long-term storage.
- Woven Fabric (PP/PE) / Tarpaulins: Highly durable, puncture and tear-resistant. Excellent water resistance. Often reusable. Suitable for heavy-duty applications and outdoor storage.
- Paper Wraps (Kraft, VCI-Treated): Kraft paper offers basic protection and interleaving. VCI paper actively prevents rust by releasing corrosion-inhibiting molecules. Essential for rust-sensitive coils.
Often, a combination is used, such as an inner VCI paper layer followed by an outer stretch film or woven fabric wrap.
3.2 Strapping and Edge Protection: Ensuring Stability and Integrity
Strapping secures the coil, prevents unwinding, and aids handling. Edge protectors prevent damage from strapping tension and impacts:
- Steel Strapping: Highest tensile strength, minimal elongation. Ideal for very heavy, stable loads. Requires specialized tools and careful handling. Can rust if not treated.
- Polyester (PET) Strapping: High strength, retains tension well, resistant to environmental factors. Often considered a safer alternative to steel. Suitable for medium to heavy loads.
- Polypropylene (PP) Strapping: Lower cost, good for light to medium loads. Higher elongation than PET.
- Composite Strapping: High strength, flexible, doesn't rust or damage surfaces easily. Good alternative to steel.
- Edge Protectors: Made from heavy-duty cardboard, plastic, or metal. Placed under straps at the coil edges to distribute pressure and prevent cuts or deformation. Crucial for maintaining coil shape.
3.3 Anti-Corrosion Solutions: Combating Rust
Corrosion is a major threat, especially for bare steel wire or during long transit/storage periods.
- VCI Film and Paper: Volatile Corrosion Inhibitors release vapors creating a protective molecular layer on the metal surface. Highly effective, especially within enclosed packaging. Available as films, papers, emitters, and bags.
- Desiccants: Absorb moisture within the package. Often used in conjunction with waterproof barriers and VCI materials, especially in high-humidity conditions. Must be calculated based on package volume and expected moisture ingress.
- Contact Corrosion Inhibitors/Oils: Applied directly to the wire, but may not be suitable for all applications due to potential contamination.
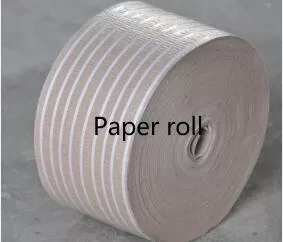
3.4 Selecting the Optimal Combination of Materials
Rarely does a single material suffice. Effective steel wire coil packaging typically involves a multi-layered approach tailored to the specific risks:
- Standard Duty (Domestic, Short Transit): Stretch film + PP/PET strapping + Cardboard edge protectors.
- Medium Duty (Longer Transit, Moderate Climate): VCI paper/film inner layer + Stretch film/Woven fabric outer layer + PET strapping + Plastic/Cardboard edge protectors.
- Heavy Duty (Sea Freight, High Humidity, Long Storage): VCI paper/film inner layer + Desiccants + Woven fabric/Heavy-duty shrink film outer layer + Steel/High-strength PET strapping + Metal/Heavy-duty plastic edge protectors + potentially palletizing/crating.
The optimal combination depends on a thorough risk assessment considering the coil type, transport mode, duration, destination, handling methods, and budget.
3.5 How Innovative Materials Are Advancing Coil Protection
The packaging industry continuously evolves, offering new solutions:
- High-Performance Films: Multi-layer co-extruded films offer enhanced strength, puncture resistance, and barrier properties in thinner gauges, reducing material usage.
- Bio-Based and Biodegradable Materials: Sustainable alternatives to conventional plastics are gaining traction, though performance and cost need careful evaluation for demanding applications like steel coil wrapping.
- Improved VCI Technology: Newer VCI formulations offer longer-lasting protection and compatibility with various metals and conditions.
- Smart Packaging Elements: While still niche, sensors for monitoring humidity, temperature, or shock inside packaging are emerging, offering enhanced supply chain visibility.
3.6 Balancing Practical Application and Environmental Responsibility
Achieving both effective protection and sustainability requires careful choices:
- Prioritize Recyclable Materials: Choose films (PE, PP), strapping (PET, PP), and paper-based materials that are widely recyclable. Ensure clear labeling for end-of-life disposal.
- Consider Recycled Content: Many packaging materials are available with significant recycled content without compromising performance.
- Optimize Material Usage: Use automated wrapping and strapping equipment for consistent application and minimal material waste. Ensure wraps are properly tensioned and straps are correctly sized.
- Explore Reusable Options: For closed-loop systems or regular routes, durable, reusable wraps or containers might offer long-term environmental and economic benefits.
4. How to Balance Cost-Effectiveness and Quality in Packing Materials?
4.1 Recognizing the Hidden Costs of Low-Quality Materials
Opting for the cheapest available packing materials can be a false economy. Potential consequences include:
- Material Failure: Wraps tearing, straps breaking, VCI failing – leading directly to product damage.
- Increased Labor: Flimsy materials may require more layers or slower application speeds.
- Damage Claims & Returns: The cost of replacing or reworking damaged coils often far exceeds the savings on packaging materials.
- Reputational Damage: Consistently delivering damaged goods harms customer trust and future business prospects.
A thorough cost analysis should factor in these risks, not just the purchase price per roll or strap.
4.2 Partnering with Reliable Suppliers for Value
Building strong relationships with reputable packaging suppliers offers several advantages:
- Consistent Quality: Assurance that materials meet specified performance standards batch after batch.
- Technical Expertise: Access to advice on the best materials and application techniques for your specific needs.
- Negotiating Power: Potential for better pricing through volume commitments or long-term agreements.
- Access to Innovation: Reputable suppliers often introduce new, potentially more cost-effective or higher-performing materials.
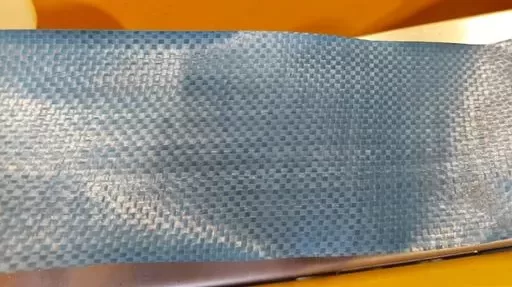
4.3 Evaluating the Return on Investment (ROI) of Premium Materials
While premium materials like high-strength PET strapping, multi-layer films, or VCI products have a higher initial cost, their ROI can be significant. Calculate ROI by considering:
- Reduced Damage Rates: Quantify the savings from fewer rejected coils, replacements, and associated administrative costs.
- Improved Efficiency: Stronger materials might allow faster wrapping or require less material per coil.
- Enhanced Customer Satisfaction: Protecting product quality strengthens relationships and can lead to repeat business.
- Lower Insurance Premiums: Demonstrating robust packaging practices might positively influence insurance costs.
Investing in quality often pays dividends by minimizing preventable losses.
4.4 Customizing Packaging Solutions to Optimize Costs
One-size-fits-all packaging is often inefficient. Customization can lead to cost savings:
- Right-Sizing Materials: Using film widths, strap strengths, and edge protector sizes specifically suited to your coil dimensions reduces material waste.
- Tailored Combinations: Develop specific packaging protocols for different coil types, destinations, or transport modes, using only the necessary protection levels for each scenario.
- Working with Suppliers: Collaborate with suppliers to develop custom material specifications or pre-cut components that streamline your packaging process.
4.5 Leveraging Automation for Efficiency and Cost Savings
Automated packaging equipment plays a crucial role in cost-effectiveness and quality control:
- Orbital Stretch Wrappers: Apply stretch film consistently and efficiently with optimal tension and overlap, reducing material consumption and labor time compared to manual wrapping.
- Automated Strapping Machines: Ensure consistent strap tension and placement, improving load security and reducing operator variability. Can use PET or steel strapping.
- Integrated Systems: Combining wrapping, strapping, and labeling into automated lines significantly boosts throughput and reduces manual handling costs.
Automation minimizes material waste, reduces labor costs, improves packaging consistency, and enhances overall operational efficiency, contributing significantly to cost savings in the long run.
Conclusion: Strategic Packaging for Steel Wire Coil Integrity
Choosing the right packing material for steel wire coils transcends mere logistics; it's a fundamental aspect of product quality assurance, operational efficiency, risk management, and customer satisfaction. A strategic approach requires a clear understanding of the coil's characteristics, the potential hazards during its journey, and the performance capabilities of available materials.
The optimal solution typically involves a carefully selected combination of materials – protective wraps, anti-corrosion agents like VCI, robust strapping, and essential edge protection – tailored to specific transport conditions and coil requirements. Balancing performance with cost-effectiveness requires looking beyond the initial material price to consider the total cost of ownership, including the significant financial impact of product damage.
By prioritizing quality materials, exploring sustainable options, leveraging automation, and partnering with knowledgeable suppliers, businesses can implement packaging strategies that effectively protect their steel wire coils, enhance their brand reputation, minimize waste, and contribute to long-term profitability.
Investing wisely in high-quality, appropriate packing materials for steel wire coils is an investment in your product's integrity, your operational efficiency, and your customer relationships. Making informed choices safeguards your assets and supports a more reliable and sustainable supply chain.

Get Your Best Solution !